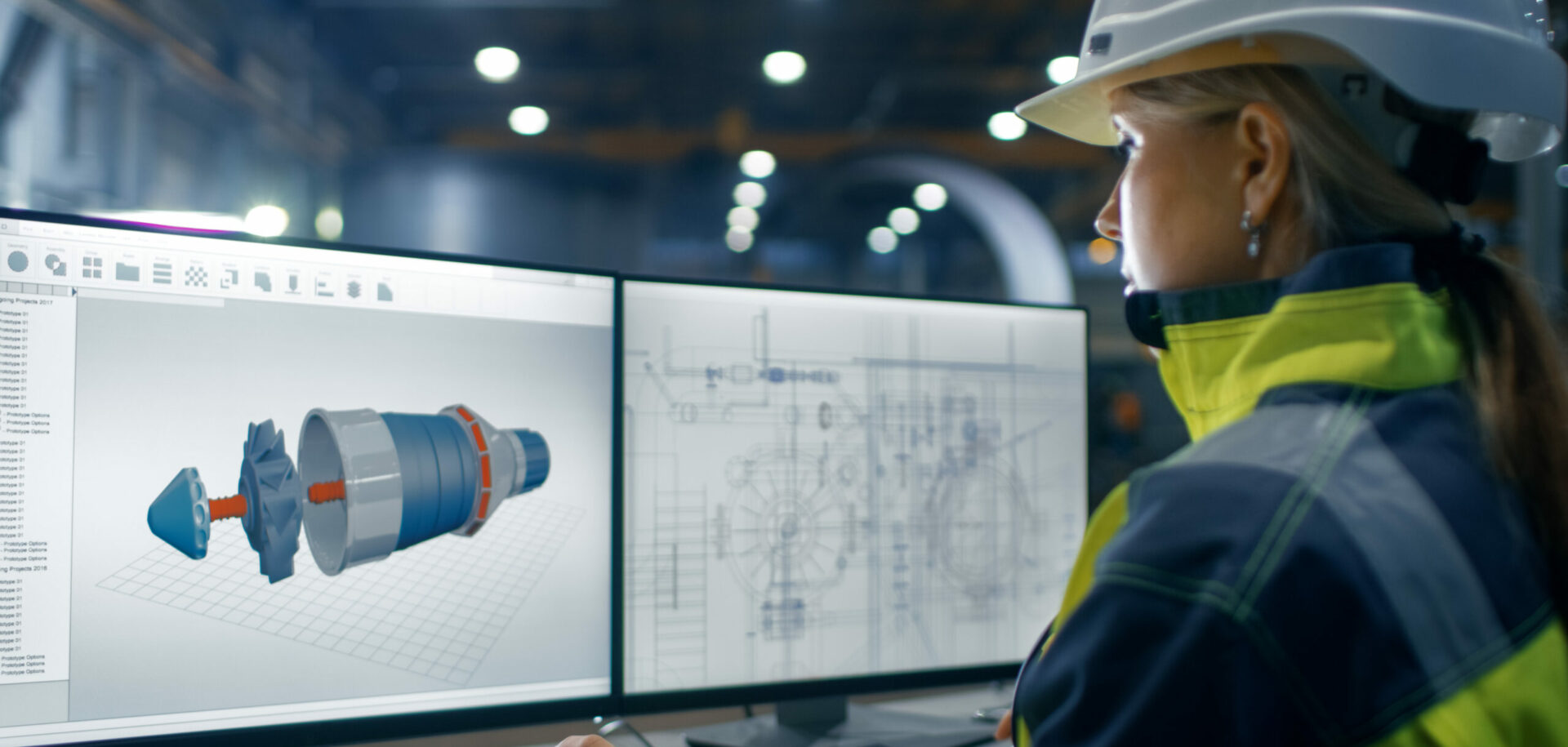
Bearings for vibrating machinery
SKF bearings for vibrating applications are able to cope with all these phenomena in a superior way. Because of the hardened cage, hammering of the roller on the cage bars is almost eliminated. For a non-hardened cage material, hammering could be catastrophic.
Vibrating machines represent some of the most challenging applications for bearings. Spherical roller bearings for vibrating applications offer reliable operation across a broad range of applications.In applications inducing vibrations, such as shaking screens, road rollers, exciters, vibrating engines and planetary gearboxes, acceleration levels and speeds are generally high and lubrication of the bearing is difficult. One of the best solutions currently available for such applications is the SKF spherical roller bearing for vibrating applications.
Even standard SKF spherical roller bearings are able to cope quite well with vibrations. This is because of their rugged basic design and the type of material used in the standard rings, cages and rollers, which are resistant to contaminants and wear.
However, to cope reliably with the extra stresses that vibrating applications entail, the SKF spherical roller bearing for vibrating applications has additional refinements. The most notable of these is the hardened steel cage, which is guided by the outer ring via a hardened guide ring. In addition, SKF knowledge of lubrication, lubricants and applications contributes to a reliable performance in all conceivable vibrating machinery.
Tough conditions
Vibration problems in bearings can have different causes. The eccentric movement in a road roller is one example – another is the linear acceleration, which occurs when a wheel of a railway train passes a rail joint. As regards the bearing, vibrations could induce lubrication problems or serious mechanical damage if the bearing has not been designed properly. Typical examples of mechanical bearing damage in vibrating installations are:
- Hammering of the cage bars
- Fatigue in the cage
- Cage wear
- Roller wear
SKF bearings for vibrating applications are able to cope with all these phenomena in a superior way. Because of the hardened cage, hammering of the roller on the cage bars is almost eliminated. For a non-hardened cage material, hammering could be catastrophic.
High accelerations
The use of a hardened steel cage also eliminates fatigue in the cage bars. A non-hardened cage sometimes cannot tolerate the load levels because the material intrinsically has a lower fatigue limit. The pockets of the SKF hardened cages are of the closed window type. Cages made of softer material, with U-shaped pockets, can be subjected to damages due to excessive flexural stresses.
The wear in the cage is also reduced to negligible levels if the cage is hardened. The wear from a soft cage is of a completely different order of magnitude than that from a hardened steel cage. In a soft cage, hard particles may get embedded in the roller pockets, subsequently causing wear on the raceway of the rollers. With a hardened cage, the wear on the rollers is negligible. The reason for this is that it is almost impossible to press hard particles into hardened steel. Wear on the rollers caused by the cage is therefore eliminated. The guide ring, which guides the rollers and the cage, is a key component in SKF spherical roller bearing. This is particularly true for vibrating applications.
The roller end-guide ring contact is designed so that the guide ring produces a minimum of friction. This is a prerequisite for the reliability and expected service life of the bearing.
In eccentric movement, it is vital that the guide ring is guided by the outer ring. The lubrication of the guide ring contact in eccentric movement is actually considerably more effective against the outer ring of the bearing than against its inner ring. This function is so important and unique that it has been patented by SKF. The result is that SKF spherical roller bearings for vibrating applications can tolerate vibration levels of up to 125g (shaft diameter 40 mm) and up to 54g (shaft diameter 300 mm) when subjected to rotating acceleration. With linear acceleration, the equivalent values are around 31g or 15g respectively.
Less maintenance
This performance means that the bearings easily cope with the operational conditions in modern vibrating applications. Typical levels are 5g to 10g for shaking screens, 6g to 30g for road rollers and 70g to 100g for planetary gearboxes.
For bearings in a vibrating application, the lubricant may actually be the limiting factor. With grease lubrication in particular, permissible vibration levels are limited by the consistency and vibration tolerance of the lubricant. Broad application experience and comprehensive lubricant testing have made it possible for SKF to establish a range of greases to perfectly match different levels of acceleration.
There are many examples that confirm the superiority of the SKF spherical roller bearings for vibrating applications. The operating temperature is a measure of how well a bearing performs. In vibrating screens, SKF bearings for vibrating applications run cooler than other spherical roller bearings – more than 50° F cooler.
In road rollers, for example, the temperature difference may be as much as 85° F.
The operating temperature affects a bearing in several ways. For example, the lower the operating temperature, the longer the lubricant will last, and the thicker the oil film in the rolling contact, the better the separation of the surfaces will be.
The other parts of the bearings have also been adapted to the operating conditions in vibrating machinery. The tolerances of the bearing outside diameter and bore diameter have been adapted to make the contact fit between the bearing housing and outer ring and the inner ring and shaft as favourable as possible. For bearings that accommodate axial movement between the inner ring and the shaft, the bore of the inner ring can be provided with a low-friction PTFE coating. This eliminates axial loading and also fretting corrosion. It also permits the shaft to be made without costly special features. The bearing radial internal clearance is C4 in order to accommodate the large temperature differences that can arise in vibrating applications.
The superior design, the abrasion-resistant material in the rings, rollers and cage – heat-treated for optimum performance – and other refinements for increased vibration resistance give the SKF bearings for vibrating applications long service life, unmatched by other bearing designs.
Håkan Lindgren
SKF Sverige AB, Göteborg, Sweden