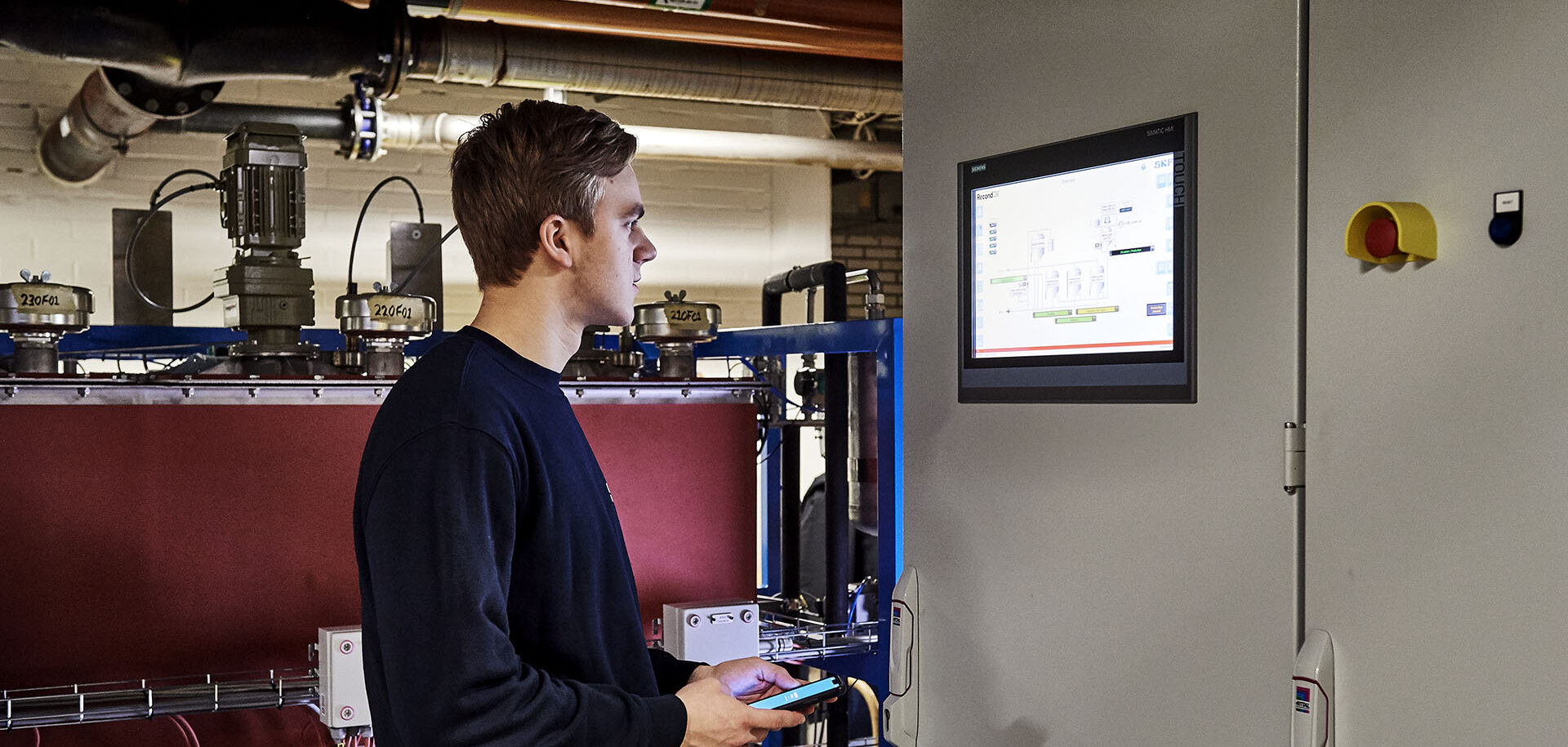
Beyond filtering – new approaches for oil cleanliness
Dirty oil is a drain on industrial productivity. For equipment that requires higher levels of oil cleanliness, in-line filtering might not be enough to achieve the necessary performance. New technology from SKF RecondOil transforms lubrication oil from a contamination problem to an ally in reliability.
These contaminants affect the performance of the oil. Hard particles can damage machines and the products they make. In the presence of heat, dirty oil can coalesce into varnish – an accumulation of sticky particles that blocks pipes and coats surfaces, adding friction and accelerating wear. Water and metal contaminants cause oxidation reactions, eventually destroying the oil.
One way to minimize these undesirable effects is to replace the oil at regular intervals. But that comes with its own problems. New oil is expensive, and so is safe disposal of contaminated oil. Frequent oil changes mean extra maintenance labour and lost production time. And high oil consumption is undesirable at a time when organizations are striving to reduce their overall environmental impact.
Conventional filtration systems
To extend the working life of oils and reduce the frequency of replacement, most larger machines and production facilities incorporate some type of cleaning and filtration equipment. Industrial users can choose from a wide range of technologies to suit the needs of their processes and operating environments. Oil can be pumped through filters that trap particles, for example, and specialist filter materials can be used to absorb water from the oil.
Such systems act as a user’s first line of defence against contaminated oil. Positioned in-line between the oil reservoir and machine, they are effective at removing particles as small as a few μm across.
However, in-line filtering comes with significant limitations, especially for users who strive for higher levels of oil cleanliness. Filters inevitably restrict the flow of oil. The finer the filter, the higher the losses and the greater the expense. To maintain the flow of oil as the pore size in the filter diminishes, users must install larger filters and run their systems at higher pressures. This leads to greater energy consumption and higher filter replacement costs. In addition, there’s the cost of environmentally benign disposal of the hazardous waste of used filters.
One way to sidestep such filtration issues is by using an offline system. These work by extracting oil from the storage reservoir and passing it through a dedicated cleaning loop. Because they are decoupled from the machine that uses the oil, offline filtration systems can work at their own pace, continually treating and re-treating the oil to gradually reduce contamination.
The offline approach also enables the use of a range of alternative filtration technologies. Centrifugal systems spin the oil at high speeds to eject heavier molecules such as water. Electrostatic separators use a high-voltage electric field that attracts polar wear or varnish particles and pulls them out of the oil.
In today’s critical production applications, owners often install a complex mix of on-line and offline filtration systems, aiming to catch all the contamination they can, to maintain oil performance and extend the period between oil changes. Yet however much they invest in conventional filtration technology, some contaminants still slip through the net.
In a typical oil sample, 80 % of the contaminant surface area is found on nano-sized particles.
Thomas Persson
Process development manager, SKF RecondOil.
The small particle conundrum
The very smallest particles are the biggest weakness for conventional filtration technologies. High-efficiency mechanical filtration systems can be very effective at removing particles down to a few μm across. But the smallest nano-sized particles present a very different challenge. These particles are much too small to see with the naked eye and are even difficult to detect with standard oil analysis equipment. They are also small enough to pass through the finest conventional filters. Left unchecked, nano-sized particles accumulate in ever-greater numbers in the oil supply.
Despite their tiny size, nano particles play a decisive role in oil degradation. This is generally because they make up a significant part of the overall contamination load in most industrial oils. In a typical oil sample, 80 % of the contaminant surface area is found on nano-sized particles. The interface between the oil and the contaminant surface is where oxidation takes place. And since oxidation is the primary cause of oil ageing, reducing that surface area really matters.
Nano-sized particles also contribute to wear. The lubricant film between the moving surfaces of a ball bearing is around 500 nm, for example. So even a particle much smaller than 1 μm is large enough to disrupt the film, potentially leading to surface damage.
Until recently, equipment owners could do very little to eliminate nano-sized particles from their oils. Extremely fine mechanical filter elements that can catch particles smaller than 1 μm are available, but these filters may also damage the oil, stripping out additives that are vital for performance and longevity.
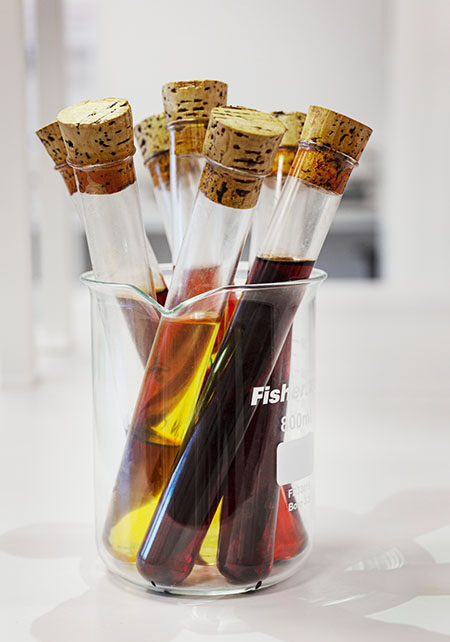
Double Separation Technology
Today, industrial users can take advantage of a new, different approach in the quest for cleaner oil – SKF RecondOil’s Double Separation Technology (DST). Based on principles originally developed in the world of biochemistry, the technology has now been adapted for industrial application. The patented two-stage combination of chemical and mechanical separation removes nano-sized particles and water molecules without damaging the oil or its vital additives.
DST does not render conventional oil filters obsolete. They are still needed to filter out the larger contaminants in the oil. But DST is capable of capturing the minuscule particles that escape through a filter’s cut-off size, among them the nano-sized particles that cause the irreversible oxidation and ageing of the oil.
At the heart of DST is the separation booster, a specialized chemical that is added in precisely metered amounts into a reaction chamber with contaminated oil. It’s a delicate process. The oil needs to be at a specific temperature, and the correct amount of booster must be mixed into the oil at just the right speed and allowed to settle for the right amount of time.
The booster attracts dirt – even nano-sized particles – while leaving the additives intact. The dirt coalesces and can be separated from the oil, leaving clean oil that can be used and regenerated again and again. During testing in real operating conditions, measurements show as much as 90–99 % reduction in very small (less than <0.2 micron) particles.
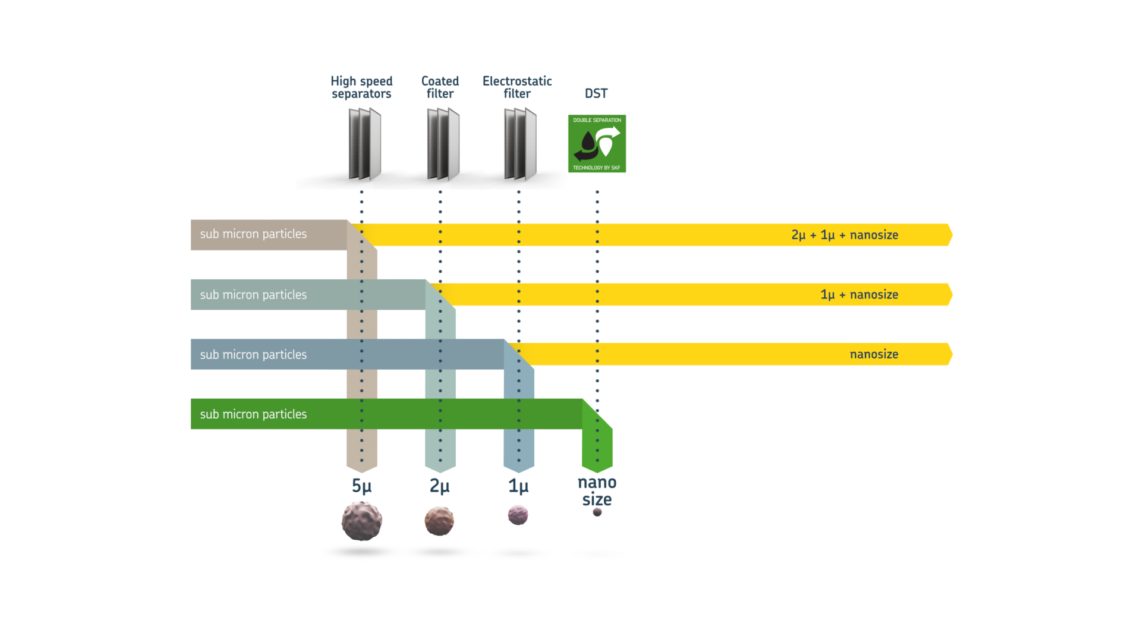
A circular use of oil
DST can eliminate a host of problems associated with contamination. With nano-clean oil, wear and damage to equipment is reduced. Machines last longer and need less maintenance, and processes become much more predictable and stable, since they are no longer affected by the gradual degradation of oil performance over time.
Indeed, since even virgin oils contain a small amount of contamination from their production and transport, the DST-treated, nano-clean oil can perform better than brand new oils in some applications. With DST, oil can become an ally in reliability rather than a recurring contamination problem that must be solved.
Over time, the impact of the process can be even more profound. Since it removes nano-sized particles from the oil, DST stops oxidation, the primary cause of oil ageing. This means the oil can be reused virtually indefinitely. And when the same oil is reused, the need for extracting, refining, shipping and modifying crude oil and disposing of it once it’s contaminated decreases. As a result, industrial oil can transform from a costly consumable into a financially and environmentally sustainable, circular resource.
Oil as a service
With SKF’s performance-based contracts, customers are charged on their operations’ performance measured against predetermined KPIs – productivity, amount of downtime, energy use and other relevant parameters. Rather than paying for equipment and oil in a traditional, transactional model, both customers and SKF benefit from maximizing machine productivity, reliability and efficiency.