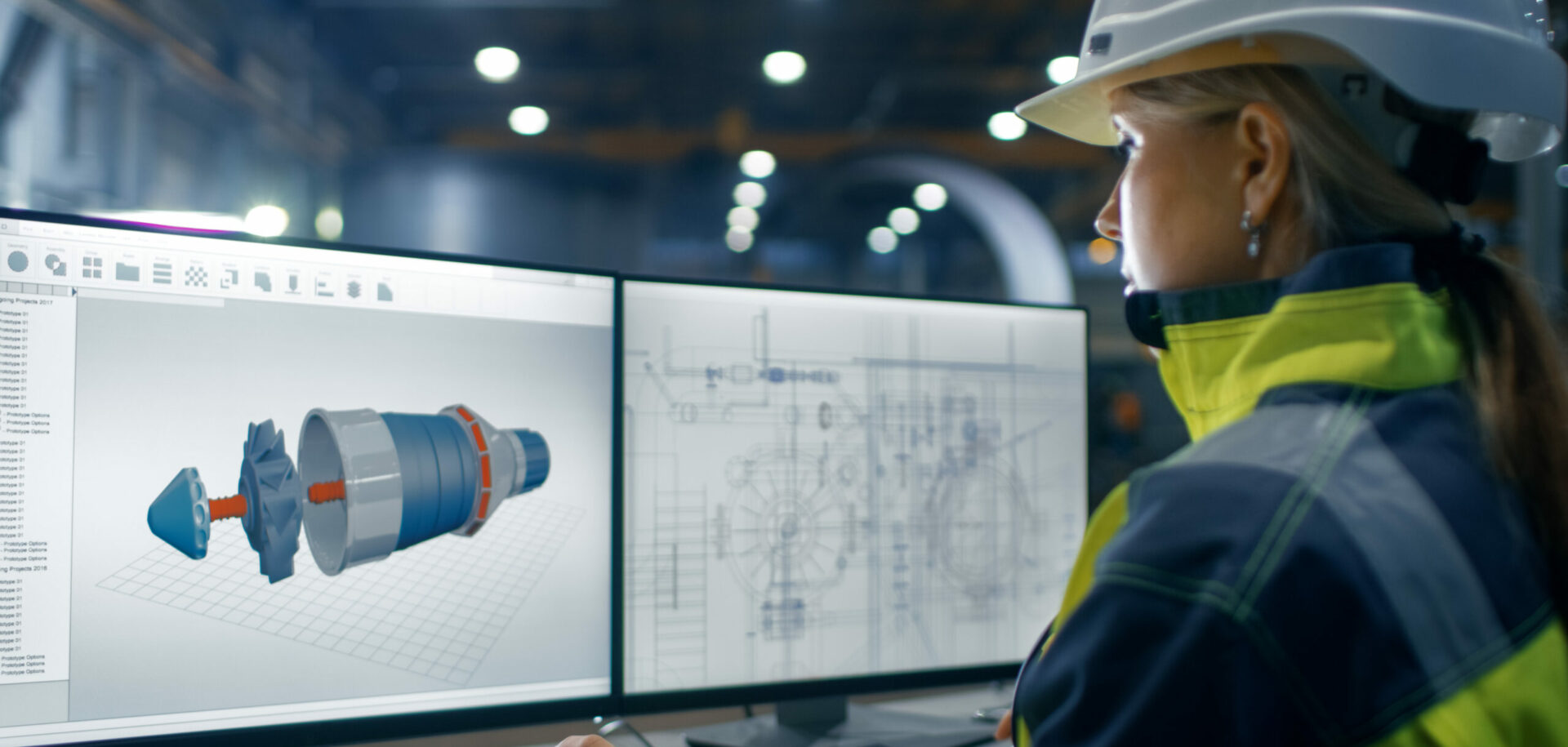
CARB cuts fan vibrations
Engineers from SKF and ABB Fläkt Industri AB have solved the problem of excessive vibration in large fans by using CARBTM as the non-locating bearing in standard housing arrangements.Medium and heavy industrial fan shafts are often supported by two spherical roller bearings that are frequently mounted in standard bearing housings, type SNH or SOFN.
Summary
Large fans such as those found in power stations or heavy industrial plants represent a considerable challenge to the bearing designer. Sometimes operating conditions give rise to excessive vibration in fan systems that can lead to failure and, consequently, plant shutdown.
CARBTM bearings have been tested in this application, and results have shown significantly reduced vibration problems. The use of CARBTM bearings has been coupled with the use of a different type of housing that allows easier access during service. As the CARBTM bearing remains part of a solution that uses standard components, customers can still benefit from an economical answer to excessive vibration.
Engineers from SKF and ABB Fläkt Industri AB have solved the problem of excessive vibration in large fans by using CARBTM as the non-locating bearing in standard housing arrangements.Medium and heavy industrial fan shafts are often supported by two spherical roller bearings that are frequently mounted in standard bearing housings, type SNH or SOFN.
The use of standard components offers an economical bearing arrangement and, because of its reliability, has almost come to be regarded as a standard solution within the fan market.
The arrangement is based on the principle of one locating bearing position and a floating (non-locating) bearing that compensates for the thermal expansion of the fan shaft. One assumption made for this arrangement to function properly is that the outer ring of the non-locating bearing is truly floating in the housing. Theoretically, this should not present a problem. In practice, there are some difficulties.
Weighty problem
The shaft of a large industrial fan often represents a considerable weight. This is a consequence of rotor dynamic considerations leading to the choice of large shaft diameters. This means that the force needed to move the outer ring of the non-locating bearing must also overcome part of the shaft weight. In turn, this implies that quite heavy thrust loads are required to move the outer ring.
After a while in service, fretting corrosion may build up between the outer ring and the housing. Even under ideal conditions, fretting corrosion occurs and is almost impossible to avoid. It causes an increase in the coefficient of friction, and extensive axial loads must be transmitted over the non-locating bearing before the outer ring is repositioned in the housing.
There is a risk that the outer ring may be tilted in the housing, obstructing any repositioning. To provide acceptable operating conditions, there are certain relationships that must be fulfilled between the bearing width (B), bearing outside diameter (D) and the coefficient of friction (m), m£ B/D.
For example for the bearing SKF 22220 ECC/W33, m £ 46/180. The calculation indicates that the coefficient of friction should be less than 0.25. This simple formula shows that the margin is very small for successful repositioning of the outer ring, and that any obstacles in the housing will have a detrimental effect on the floating
performance of the bearing.
Practical experience
The opportunity to try out a new bearing arrangement stemmed from problems that arose in a fan located at an energy plant in Sweden. Severe problems were experienced because of the non-locating bearing. The fan, used during the winter, failed after eight years of operation. It was an axial fan with an adjustable impeller that transported exhaust gases of varying temperatures.
The fan was supported by two SKF 22244 CCK/C3 bearings; the rotational speed was 950 r/min. The bearings were lubricated by circulating oil.
High levels of vibration, particularly axial vibration, occurred sometimes while the fan was in use. During short periods, velocities of 10 mm/s and above had been recorded.
Vibrations of such magnitude were unacceptable to the user, so the fan was taken out of service. On checking the record of vibration measurements, it turned out that the vibrations emanated from the non-locating bearing; the locating bearing behaved normally with low levels of vibration during running. Careful study revealed that the peaks in vibration occurred during short periods (a matter of seconds) and coincided with an adjustment of the fan blade angle and/or a change in gas temperature.
These high peaks were caused by an interaction between the locating and the non-locating bearings, which resulted in a momentary change in rotor dynamics. Each time the thrust load changed, there was a corresponding deformation in the locating bearing and, consequently, a change in the fan’s axial position plus an alteration in the non-locating bearing’s internal loading.
Bearing solution
After promising test results with a corresponding cylindrical roller bearing, NU 240 ECM/C3, on the non-locating side, SKF and the customer decided to test a CARBTM in this position. Following comprehensive laboratory tests at the customer site, it was decided to mount CARBTM bearings in two large fans at two different sites in Sweden.
Vibration measurements have been carried out with this configuration and the results have been very encouraging. The vibration level has been considerably reduced, and both the fan manufacturer and the end user are very pleased with the performance of their fans.
As a direct consequence of these results, the fan manufacturer has decided to introduce CARBTM as a standard solution for the non-locating position in their large fans; the manufacturer will continue to use a spherical roller bearing for the locating position.
An additional improvement has been to mount the bearings in bearing housing type SBP which provides easier access to the side face of the bearing. This eliminates the need to lift the fan shaft from the lower half of the bearing housing during service. With SBP housings, the shaft need only be lifted a small distance to unload the bearings.
Ove Andersson,
SKF, Global Segment Fluid Machinery,
Gothenburg, Sweden