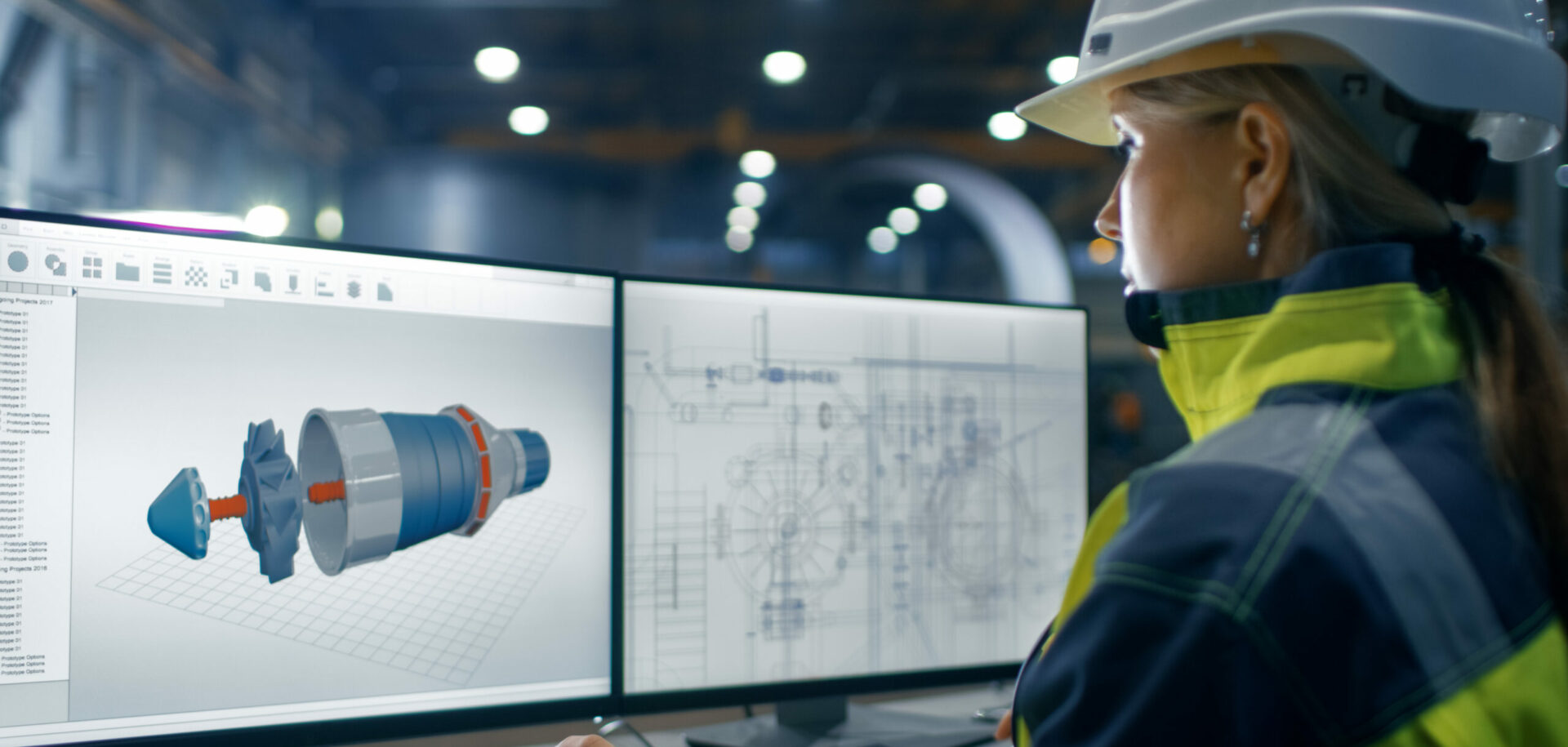
Centralized lubrication system for wind turbines offers improved efficiency
A successful cooperation of companies within the SKF Group has led to the development of an improved pump unit for centralized lubrication systems for wind turbine applications.
Summary
SKF has developed a special pump unit that supplies the centralized lubrication system in wind turbines. The main component of the system consists of the KFG pump, an electric filling pump and a pressure switch. Unlike in earlier pump versions, the lubricant can be fed into the modified KFG pump unit from the top, avoiding an accumulation of grease in the upper part of the pump. The modular concept of the new KFG pump is suitable for use in a wide temperature range, enables larger pump designs and is easy to install.
The KFG pump unit also contains a new machined sealing concept for the grease follower piston. This new K01-R ECOVAR sealing concept was developed by SKF Economos Deutschland GmbH in cooperation with SKF Lubrication Systems Germany. The KFG pump can be refilled with a specially designed portable electric filling pump, thus significantly improving service and maintenance operations.
Lubrication requirements for bearings in wind turbines have triggered a series of developments that further enhance the operation of SKF centralized lubrication systems. This has culminated in SKF developing a lubrication package for wind farms worldwide that increases the lifetime and reliability of these systems.
Some bearings in wind turbines require lubrication at predetermined intervals (fig. 1). To achieve this effectively, automatic centralized lubrication systems are required (fig. 2). A centralized lubrication system contains an KFG series pump unit from SKF, an electric filling pump, a pressure switch and a pump for the used lubricant (fig. 3).
The KFG pump unit
The KFG pump unit (fig. 4) is a key component of the centralized lubrication system. Many aspects of the pump have been specifically optimized to meet the demands of the wind industry.
A significant improvement in the design is the option to fill the pump from the top. This feature enables a homogenous exchange of the lubricant, based on the “first in, first out” principle. The lubricant is fed into the system from the top and pumped out at the bottom. In earlier versions, the grease entered the system from the bottom, which meant that unused grease was able to accumulate in the upper part of the pump. A patent application for this top-filling design has been filed by SKF Lubrication Systems, Germany.
The new top-filling design also required a new concept for the grease follower piston (fig. 5), necessary for the correct operation of the rotary pump. The piston feeds highly viscous grease continuously to the pump contained in the pump housing. This new grease follower piston design, in turn, demanded a new concept for a customized, machined sealing solution . This was developed together with SKF Economos Deutschland GmbH, part of the SKF seals platform.
In order to implement this innovative filling method, both a new grease follower piston and the new K01-R ECOVAR sealing system were developed. The piston was designed so that the lubricant is fed through a distributor duct into the system with precise centricity from the top into the grease reservoir. This new design and the customized K01-R ECOVAR sealing system enable the grease follower piston to operate using various viscous lubricants suitable for different temperature ranges.
The new concept was the result of a unique SKF programme “Innovation in a Day”, in which components can be designed and produced within one day. This made it possible to quickly and effectively respond to challenges encountered during the trial phase.
Benefits of the new design
The modular concept of the new KFG pump allows easy pump installation, as does the new reservoir concept, which enhances reliability, even when used in extreme conditions. Forcibly actuated pistons supply adequate volumes with substantial lubricants also at extremely low temperatures. This reduces maintenance requirements and increases reliability.
The exterior pump design was upgraded with aluminium profiles, which considerably improve the pump’s stability and permit larger pump designs without problems. Currently, versions with reservoir sizes from 4 to 15 kg are available for rotary applications and in sizes up to 20 kg (fig. 6) for stationary operations.
Demand-driven developments
The development of the pump was necessary to meet the increasing requirements of the wind industry. This new pump design meets corrosion requirements according to C5M, requested by offshore wind farm operators.
Design, material conformance and respective standards in compliance with C5M requirements have been confirmed by the issuance of the “Germanischer Lloyd Certification”, DAA-GL-426-2010, on 14 September 2010 (fig. 7).
During the development of the pump, a large number of experiments were carried out to test the new functions. Various NLGI class 1 and 2 lubricants were tested for their continuous transport properties in temperature ranges between –30 °C and +70 °C. For example, it confirmed the constant functionality of the grease follower piston with the K01-R ECOVAR customized seal, irrespective of whether the pump rotates, is upside down or is in a horizontal position. After various prototypes were found to function without any problems, the pump was presented at the 2010 HUSUM WindEnergy trade fair in Germany. Almost concurrently, for a pilot project in China, a first run of 40 KFG pumps was delivered to Sinovel, China’s largest wind turbine manufacturer.
As a supplement to the KFG pump, an electric filling pump has been developed that makes refilling the KFG pump from the top quick and easy (fig. 8). The electric filling pump requires an electric power supply, is mobile and can be transported easily by service teams from one wind turbine to the next. It significantly improves service and maintenance operations.
In conjunction with the other previously mentioned innovative SKF WindLub products, the development of the new KFG pump marks an important milestone in the development of centralized lubrication systems for wind power.
Special considerations for wind power applications include:
- C5 – corrosion protection
- Special approval for offshore use
- Convenient refilling with an electric pump
- Patented top-filling design
- Extensive temperature range from –30 °C to +70 °C
- Highly stable design.
Conclusion
An efficient and successful cooperation between SKF Sealing Solutions and SKF Lubrication Systems has resulted in a new pump unit with outstanding and reliable lubrication capabilities for bearing applications in wind turbines, thus providing long service life and reducing maintenance requirements.
Key improvements made to the new KFG pump:
- Top-filling design of the pump units
- Grease follower piston featuring the K01-R ECOVAR customized sealing solution with integrated magnetic tape and receptacle for the filling tube
- Sturdy design using aluminium profiles also for very large pumps
- New reservoir concept with inserted pump elements enable an operating range from –30 °C to +70 °C and resistance up to –40°C
- Special flanges support the modular concept and allow easy pump installation
- The fluid level in the lubrication reservoir can be monitored using up to three external magnetic switches.