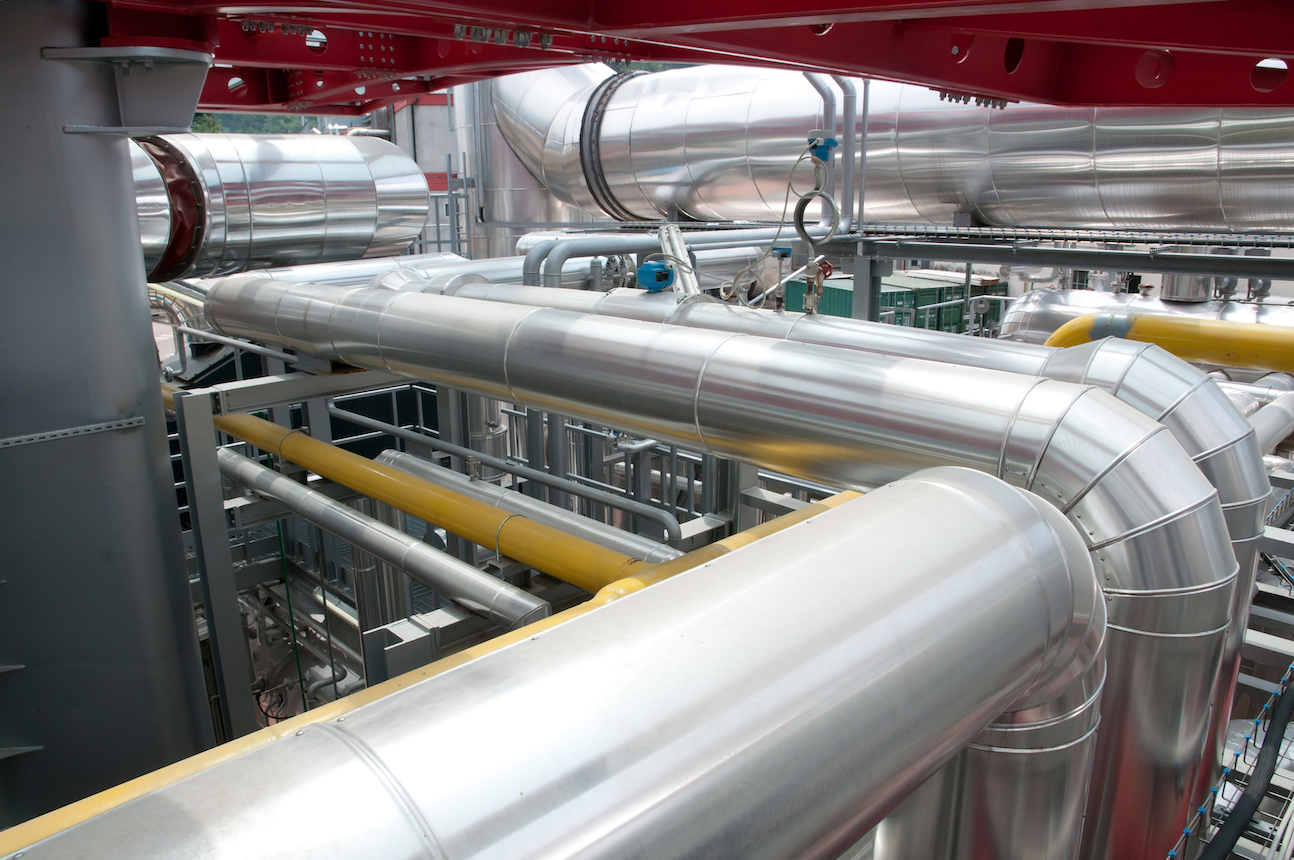
Clearing the air
Each year charcoal fires, and the toxic smoke they generate, cause the deaths of millions of people worldwide and have a disastrous impact on the environment. The Swedish-Zambian company Emerging Cooking Solutions has found an effective solution to address this problem.
When Per Löfberg, co-founder of the Swedish-Zambian company Emerging Cooking Solutions, recently visited SKF in Gothenburg, he carried with him one of the portable wood gas stoves his company has begun selling in Zambia as a way to curb the use of charcoal cooking fires. It is the fuel, not the stove itself, that is the most important part of Löfberg’s initiative. In Zambia, as in several other African countries, the search for cooking fuel has resulted in massive deforestation. In some countries, more than 95 percent of forests have disappeared. Meanwhile, millions of tonnes of biomass are going to waste as piles of peanut shells, sugar cane scraps and sawdust rot away or are burned unnecessarily. Emerging Cooking Solutions now wants to utilize this bio waste and convert it into fuel. “In its pulverized form, biomass cannot be used to cook food,” says Löfberg. “But this becomes possible if you compress it into briquettes or pellets – and that’s exactly what we have done.” He carries the small stove onto the balcony, fills it with pellets and lights it. After a couple of minutes, the pellets begin to gasify, and Löfberg places a pot of water on the stove, which quickly comes to a boil. “By using pellets instead of charcoal, you can save at least an hour a day, which can be used for more productive work,” Löfberg explains. Even more important, the smoke produced by the pellets is nontoxic. A study conducted by the World Bank Group shows that 4 million people die prematurely each year due to toxic smoke from cooking. At the same time, open fires are responsible for as much as 18 percent of the greenhouse effect. “One result that we hadn’t anticipated, and that many women see as one of the main advantages, is that they don’t get dirty while cooking, since the pellet stove doesn’t leave a covering of soot in the same way as a charcoal stove,” Löfberg says. Löfberg founded Emerging Cooking Solutions two years ago with partner Mattias Ohlson. At the time, the two ran a consulting company specializing in helping companies work in accordance with the “cradle-to-cradle” principle – an approach that focuses on manufacturing products in a way that generates no unutilized waste. Instead, all of the input materials are to be reused as nutrients for the soil or recycled and converted into new raw materials. “When we looked at various material flows, we realized just how problematic things are in Africa,” says Löfberg. “Taking an old-growth forest and converting it into charcoal is an immensely unproductive process. It takes six tonnes of wood to produce one tonne of charcoal – and on top of that, charcoal is toxic, and the trees are not replanted.” Although the idea of replacing charcoal stoves with pellet stoves had been around for years, pellets were not actually being produced in Africa. Löfberg and Ohlson decided to initiate a test operation. The only question was where to begin. It was at this time that Löfberg was invited to visit the Swedish embassy in Zambia, where he learned of the mountains of sawdust being generated in Zambia’s Copperbelt mining region. “Suddenly, it all became clear,” he recalls. “This area had an enormous amount of unused biomass.” The next step was to procure a used pellet machine and install it at a sawmill located in the city of Kitwe. However, it quickly became clear that the bearings and other wear parts were old and in poor condition. And frequent power outages in Zambia, which regularly caused the machine to come to a sudden halt, did not make matters easier. “That’s when SKF in Zambia stepped up and supplied us with new bearings, which was incredibly helpful,” Löfberg says. Production has been under way since June 2013 and has attracted considerable attention. In addition to household stoves, the company also sells stoves for professional use, which are used in restaurants, orphanages, schools and other types of food service establishments. Since pellets are significantly cheaper than charcoal, the cost of the stove can be recovered in very little time. This is more difficult when it comes to household stoves, which cost about 32 euros. Even if the full price can be recovered quickly, many people simply cannot afford to pay it all at once. “We buy the stoves ourselves and sell them at cost, but the company is too small to subsidize them to any great extent,” Löfberg explains. “That’s why we started an online campaign called Give Cooking, which enables sponsors to help people in Zambia buy stoves. We also work together with a number of companies whose employees have the option to set aside a portion of their salaries for three or four months in order to buy a stove.” In recent months, the company’s sales have increased 30 percent per month. The goal for 2015 is for 15,000 households to be using pellet stoves instead of charcoal stoves. The Emerging Cooking Solutions pellet machine is equipped with two presses. If both are operational at the same time, the machine has an annual capacity of about 3,000 tonnes. The machine’s gearbox, engine and pressing wheel contain about 10 bearings, which are exposed to considerable forces and powerful vibrations in a hot, dusty environment. It is therefore important that the bearings are of an extremely high quality. The process begins with the raw material – in this case, coarse sawdust – being blown into a hammer mill. From there, the sawdust is reduced into smaller particles measuring a maximum of 5 millimetres. The hammer mill is also equipped with a screen to remove any stones. The sawdust is then blown into a large container equipped with agitators. Here, two screw conveyors push the sawdust through a steel mould with a number of small holes. The dimension of the holes varies depending on the type of raw material, but 8 millimetres is the most common. After the sawdust has been compressed, the pellets drop onto a conveyor and pass into a cooling tower. Once the pellets are cool, they are fed onto another conveyor and finally dropped into bags.
“During the year, we also plan to start testing new markets in Africa,” Löfberg says. “Our long-term vision is to eliminate the use of charcoal for cooking in Africa. If we can help make this happen, we are more than happy to do so – if only by inspiring others.”The pellet machine