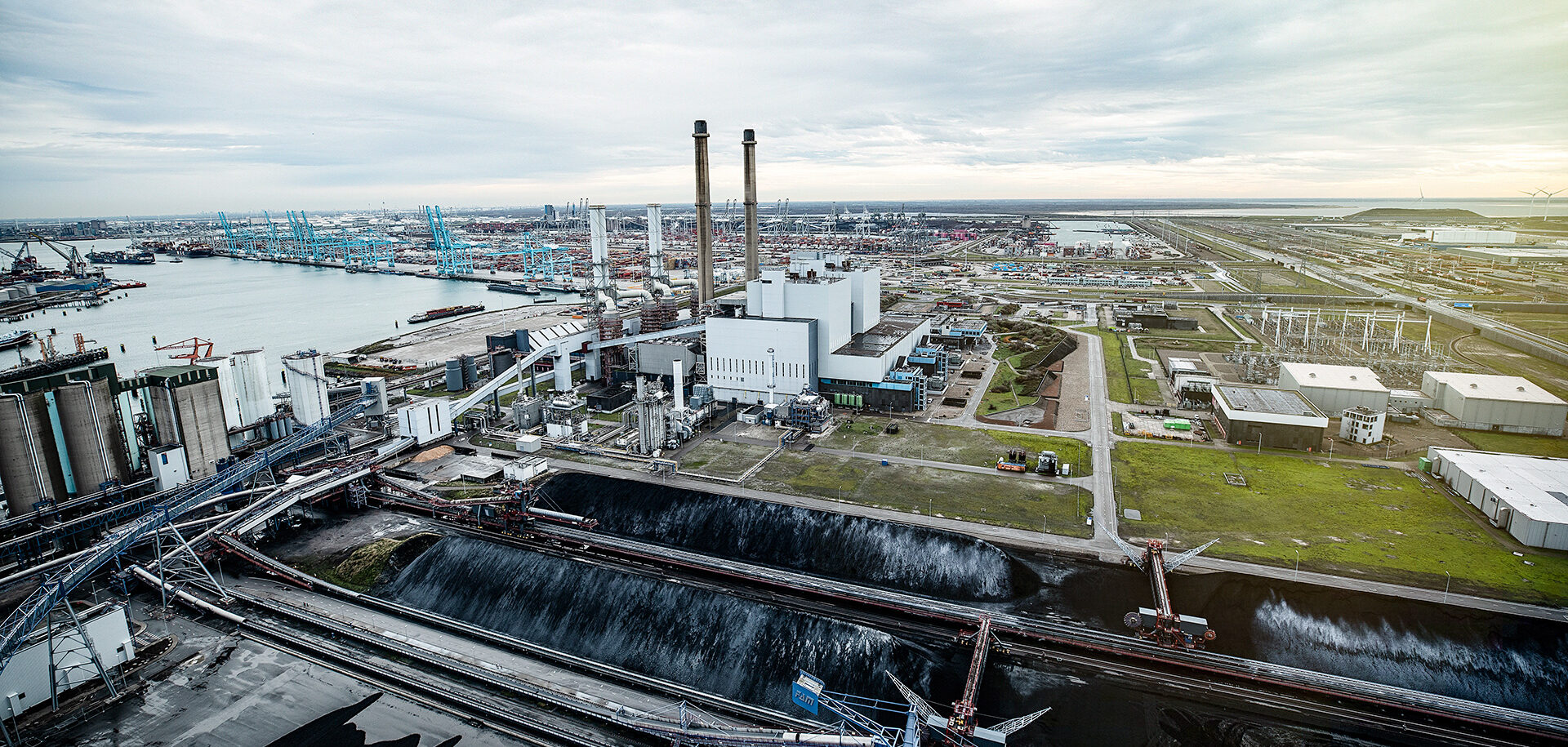
Colossal power by the sea
The Maasvlakte Power Plant 3 in the Netherlands burns 100 kilograms of coal per second and is designed to run for six years without shutting down for maintenance. SKF plays a key role in keeping the electric current flowing.
MPP3 key data
- Gross capacity: 1,100 MW
- Efficiency: ~ 47 percent
- Steam conditions: 620 degrees Celsius, 285 bar
- Start of construction: April 2008
- In operation: 2014/ 2015
- Workers on site: > 2,500
- Record safe days: 1,337
MPP3 is 80 percent coal-fired, but it also burns biomass, meat and bone meal, bio-propane and some waste from neighbouring companies on the Maasvlakte.
“Some 100 kilograms of coal burned per second produce 1,100 megawatts of electricity,” Boere says. “But the plant also produces fly ash and gypsum for use in the construction industries, and it supplies steam to its neighbours for their industrial processes.”
Optimizing rotating equipment performance
- Condition monitoring through vibration measurements
- Condition monitoring through a pump, electrical motor and gearbox inspection programme
- Lubrication management
- Maintenance engineering consultancy
- Bearing damage analysis
- Continuous improvement
“UCML is inextricably linked to predecessors of MPP3,” Boere says. “The MPP2 has been converted into a synchronous condenser that delivers reactive power and manages energy to stabilize the grid. It’s the only synchronous condenser in Europe converted in this particular way, and it took us just 15 months to convert. It’s great to be able to turn something old and obsolete into a key element supporting energy transmission across the continent.
“MPP3 is right at the top of the merit order for European power suppliers, and we run at almost full load, day and night, 24/7,” Boere says. “It’s a dynamic, volatile and complex system. Power is hedged and traded daily in blocks of 15 minutes.” The volatility is due to the unpredictability of solar and wind and is difficult to predict, he explains.
The Maasvlakte plant is connected not only to its industrial neighbours but also to the European grid, so maintenance is a tricky ballet to choreograph. “Our agreed outage interval for essential maintenance on UCML is six years, which means we have to keep all our systems running continuously for that period of time until we can shut down for essential maintenance,” Boere says. “And when we shut down, all our neighbours shut down too. Our outages are all aligned.”
This is a 1.6 billion-euro plant that uses the latest technology, and SKF is up to that challenge.
Rutger Boere
maintenance manager
Previously, Uniper had three different independent contractors providing maintenance services, but the lack of interaction between them meant more work for Uniper. “SKF brings extensive technical knowledge along with state-of-the-art equipment and engineering power, with qualified people who can support us in our business,” Boere says. “This is a 1.6 billion-euro plant that uses the latest technology, and SKF is up to that challenge. That said, we thought we’d be further along the optimization process by now, but perhaps we overestimated our progress in terms of taking back the technology from our previous contractors. And we’re not making life any easier for SKF, as we are currently introducing biomass combustion to our portfolio, which has added a whole raft of new rotating tech to maintain!”