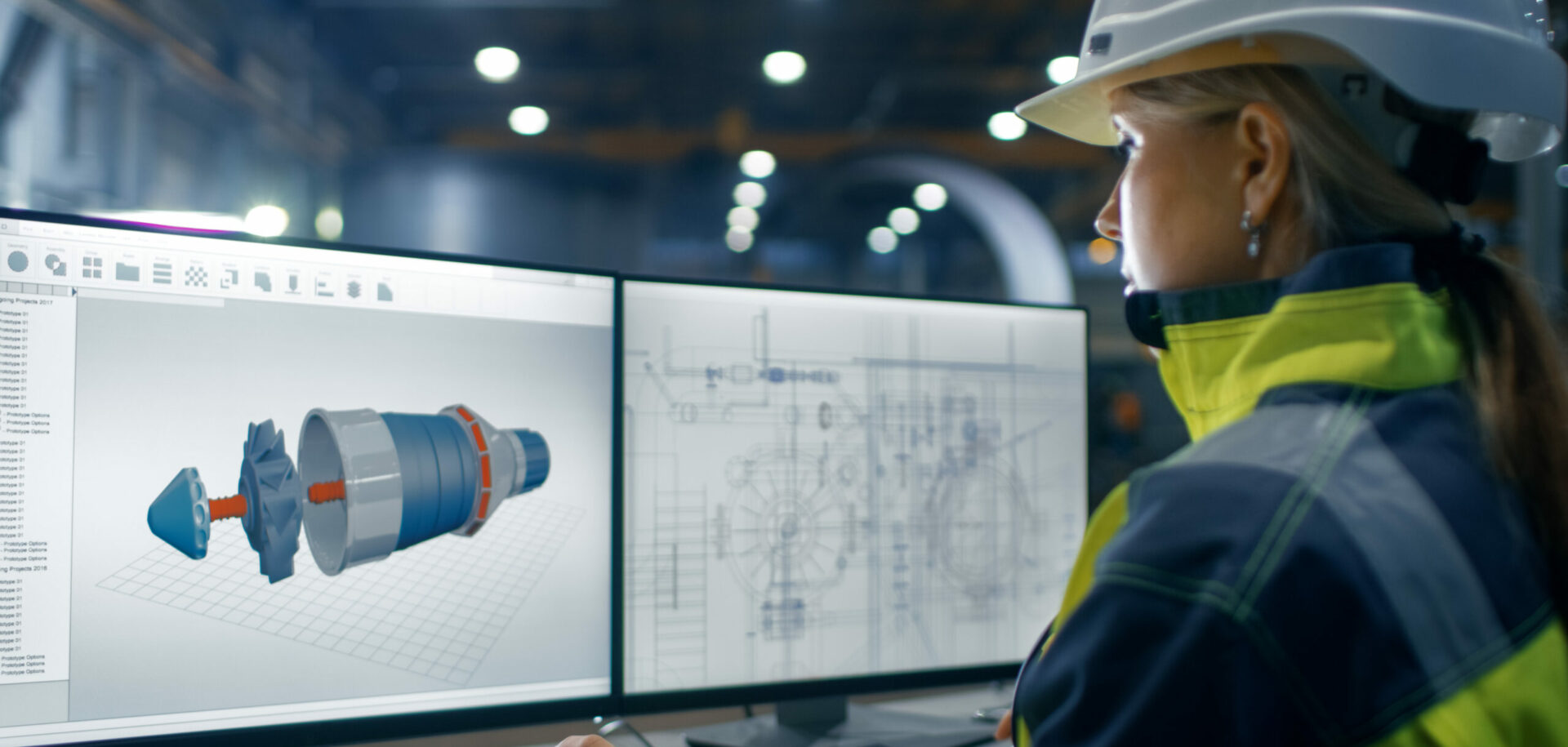
Compact hydraulic unit for high-tech fine paper machine
Specialists within SKF Lubrication Systems AG have developed a unique lubrication system to meet the needs of Voith’s latest and largest paper machines.
Summary
On China’s Hainan Island a novel lubrication system has been installed as part of the world’s largest, fastest and most productive paper machine. To meet the stringent requirements of this impressive new paper production facility, the 45-tonne lubrication unit was built, tested and packed in Germany and then shipped by sea to its final destination for assembly on site. It stands as a testament to SKF engineers’ expertise in lubrication systems design.
Modern paper machines are becoming increasingly bigger, faster and more efficient. On Hainan Island in the southernmost province of the People’s Republic of China, the world’s most productive fine-paper machine is currently being installed and commissioned. This giant machine’s manufacturer is Voith Paper, based in Heidenheim, Germany, one of the largest suppliers of paper machinery worldwide.
SKF Lubrication Systems AG has built an extremely powerful supply unit to deliver the right amount of hydraulic and lubricating oil to this extraordinarily large piece of equipment. Dubbed Hainan paper machine No. 2, it is owned by Asia Pulp & Paper, one of the world’s top 10 papermakers.
The performance data of this fine-paper machine, the most productive in the world, are really impressive, boasting a design speed of 2,000 m/min for a total length of 430 m. The press section is the biggest ever built: 11 m in width, 20 m in length and 10.5 m in height. It weighs in at 500 tonnes, the weight equivalent of 500 compact cars.
The heart of the machine is the Tandem NipcoFlex shoe press. Its function is the mechanical dewatering of the paper before it enters the dryer section. Hydraulic pressure is built up to press the “shoe” against a rotating roll. The paper loses a significant amount of its water content as it runs through the extended nip formed by the shoe and the counter roll. The shoe itself is covered by a polymer liner that floats on an oil film. This way, the effective area for the application of pressure to the paper is increased enormously and results in a high dry content of the paper.
Vitally important: the hydraulic system
Paper quality is mainly determined by a paper machine’s press section. The press has a big impact on the future saleability of the final product. This is why the exact alignment of the equipment used for such a critical machine section is of vital importance. Just as the muscles of our body provide support and stability and also make us sensitive to external impulses and changes of balance, the hydraulic system must be capable of transmitting heavy forces while at the same time apportioning pressure equally across the paper web in order to achieve a uniform density and surface quality. Moreover, the hydraulic unit also covers the function of a circulating oil lubrication system. The circulating oil acts as the paper machine’s blood, removing contaminants and lubricating the machine’s articulations. Contaminants are particles that must be flushed out of the bearings and sliding surfaces, and the circulating oil keeps these components in good operating condition and extends their service life. Besides acting as the equivalent of a human kidney function, the oil must also cope with the high temperatures that result from hydraulic pressure. The hydraulic oil must be kept absolutely free from entrapped air. All these properties were implemented by engineers of SKF Lubrication Systems AG in close cooperation with the customer.
Innovative hydraulic unit
The specified performance data as well as the sheer dimensions of the paper machine presented a tremendous challenge. The hydraulic unit is top-performance design, and its technical development was virgin territory to the Hockenheim-based engin-eers from SKF Lubrication Systems AG.
One of the customer’s specifications required the supply of two NipcoFlex presses in a row – a tandem solution that traditionally requires two separate hydraulic units. In addition, because of the shipping requirements, the lubrication system design had to be capable of being containerized for the sea transport to China. This problem, like many others, could only be solved by close cooperation between SKF and Voith to develop an intelligent solution.
“Our task became more complicated because of the project dimensions,” notes Pulp & Paper team manager Hans-Georg Weber. “We had to implement components that were not readily available on the market. Therefore, SKF had to design them on their own. The press section’s hydraulic oil supply is provided by several hydraulic circuits. The return oil from the presses gets rested, cooled and filtered.”
The design concept is distinguished by the combination of features that traditionally have required two independent hydraulic units. In this design the number of components could be halved, eliminating the need for two tanks and reducing the number of spare pumps.
Meeting customer expectations
The SKF project team can take pride in its achievement – not only in creating a novel design approach but also in meeting the short time frame for the project. Jürgen Kreutzkämper, head of the R&D department, explains, “The customer’s specifications implied that this hydraulic unit had to be designed using as little space as possible. For optimum accessibility, the design was based on 3D CAD from the start. The 3D design made it possible to discuss solutions with the customer using a model that enabled immediate changes and optimization. The actual result is a layout that sets standards in respect of accessibility, efficient use of space and functional design.”
Even loading the system for transport following the customer acceptance test required extraordinary planning and effort. The whole unit had to be split into transportable units. The hydraulic unit’s gross weight is 45 tonnes, and each individual heat exchanger weighs six tonnes. The separate units that made up the total system were loaded on four trucks with the help of heavy-duty cranes to start their journey to the operation site.
The hydraulic unit at a glance:
-
Nominal tank volume: 28,000 litres
-
Dimensions (LxWxH): 10.0×10.6×3.1 m
-
Gross weight: 45 tonnes
-
Assembly time: eight weeks.
About SKF Lubrication Systems
The application engineers at SKF Lubrication Systems’ Hockenheim plant are specialized in the design and project management for large-size centralized lubrication systems for paper machines, steel mills, wind turbines and similar applications. SKF’s cooperation with Voith Paper has a history going back four decades.
SKF expertise in lubrication systems was enhanced by the acquisition in 2004 of Willy Vogel AG, the market leader in the area of lubrication systems. Since July 2009, all VOGEL lubrication systems, products and services have been sold under the SKF brand.
This acquisition has further strengthened the group’s five areas of competence (bearings and bearing units, lubrication systems, seals, mechatronics, and services) by combining synergies to develop superior lubrication solutions for customers around the world.