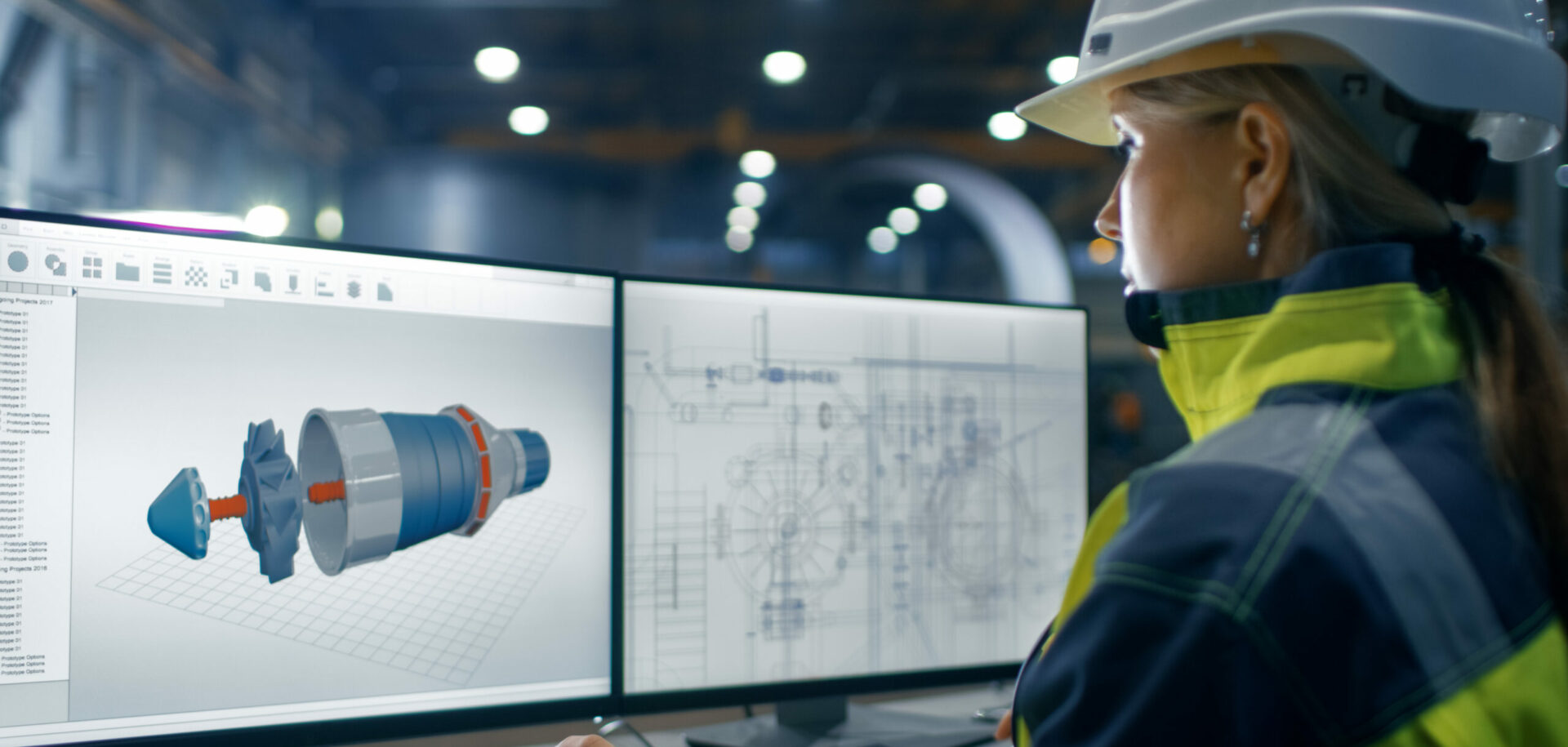
Condition-based maintenance goes maritime
Maintenance programs driven by condition monitoring processes can offer significant benefits to the marine industry. SKF has developed specific offerings for the maritime market that have already proven their worth with leading shipping lines.
Maintenance programs driven by condition monitoring processes can offer significant benefits to the marine industry. SKF has developed specific offerings for the maritime market that have already proven their worth with leading shipping lines.
Condition monitoring, when combined with maintenance processes, has clearly demonstrated significant benefits throughout industry in terms of reducing mainten-ance activities and costs, helping to avoid unplanned stoppages and more. Recently the maritime industry has realized that similar advantages are to be gained by adopting condition-based maintenance (CBM) strategies tailored to their particular needs. SKF has had many years of experience in this field and has developed programs that meet the unique requirements of shipping operators.
Condition-based maintenance processes, properly applied, can help to identify and rectify problems at an early stage and can improve marine machinery reliability and reduce maintenance costs significantly. This has been confirmed by the major classification agencies. Keeping machinery running in optimum condition reduces the likelihood that it will fail in service, leading to improved reliability and increased efficiencies.
Overall, properly implemented condition maintenance strategies for marine applications can also contribute to maximized machine and vessel availability, simplified and streamlined classification procedures and a safer onboard environment for staff while reducing the environmental impact of the vessel’s operations.
Challenges of condition monitoring in marine environments
When it comes to running a condition monitoring program, the shipping industry faces a major challenge – being able to maintain a consistently high standard of condition monitoring expertise on every ship with a workforce that tends to move frequently between ships. Without the introduction of a common standard and the skill of an experienced condition monitoring specialist, the collected diagnostic data may be difficult to interpret to carry out optimized maintenance, and too often this results in the anticipated gains failing to materialize.
The best way to make sure that full bene-fits are reaped is to develop a program where the timing, sharing, storage, interpretation and use of the collected data are optimized.
The appropriate application of a CBM program varies from ship to ship and depends on the operator’s goals and experience with maintenance procedures. An in-depth discussion of maintenance and operation needs and objectives between the ship operator and SKF lays the groundwork for a recommended program. Depending on the type of ship, the number of onboard auxiliary machines ranges from 75 to 150 per vessel. Auxiliary machines typically covered under a CBM program include:
-
engine lubrication machine systems
-
cargo pumps
-
engine room fans and blowers
-
engine room purifiers
-
main engine blowers
-
turbochargers
-
refrigeration units
-
centrifugal pumps
To solve the common problem of attaining and sustaining condition monitoring expert-ise on board, SKF Remote Diagnostic Center’s support services reduce, and in some cases eliminate, the need for extensive condition monitoring training or knowledge required of onboard personnel.
Steps in implementing a program
A CBM is customized to each ship operator’s requirements. Assessing and mapping the ship’s critical machinery and establishing measuring points and trend values is the starting point for the development of the program. Data are collected through the application of portable data collectors. These collectors are specifically designed to be easy to use while still allowing sophisticated analysis of machine vibration data. SKF’s portable condition monitoring tools set the standard for the industry, and ATEX-approved models are available where required.
SKF online and fixed condition monitoring systems provide the optimum approach to safety and reliability of a ship’s critical machinery by automatically collecting data on a continual basis. This enables analysis or interpretation of data at any time, either on the ship or by remote diagnosis via the ship’s communication system. Collected data relating to machine reliability are transmitted via the ship’s communication system to an SKF remote diagnosis center, where it is monitored and interpreted by certified machine reliability experts. Customized reports identify potential problems, recommend appropriate actions and facilitate the scheduling of maintenance procedures. Based on these reports, fleet maintenance programs can be developed and the necessary actions implemented. SKF can provide specialist services for advanced maintenance and alignment of machinery and equipment.
Case study
Using condition monitoring as part of a predictive maintenance strategy to improve fleet availability and efficiency is where BP Shipping has significant experience. Coming from a predictive maintenance strategy, the challenge was to take the maintenance strategy to the next level, heading towards a proactive approach. With a proactive maintenance strategy, the deterioration of machine condition triggers a short-term corrective solution as well as a longer-term in-depth investigation to understand the root cause of failures. The objective is to further improve machinery and ship reliability, as repetitive problems are identified and prevented. With this in mind, the company sought a partner who specialized in both precise and timely data analysis as well as machinery expertise and application engineering. Thus, SKF was selected as a partner to enhance the existing fleet machinery condition monitoring system and support the fleet maintenance strategy.
Standardized work procedures are used to collect data on vessels. The data are then transmitted through the ship’s communication system and analyzed onshore by certified SKF specialists. The results are put into simple-to-use customized reports that help vessel engineers focus on the specific machines that are in most need of maintenance. For significant failures and repetitive issues, SKF application engineers also participate in Root Cause Failure Analysis to help eliminate ongoing reliability issues.
Finally, the retention of good quality data on historical in-service machinery conditions also reduces the need for compulsory intrusive visual examination, which saves considerable time and cost during mandatory in-port continuous survey machinery inspection cycles.
Another benefit of the CBM solution is an improved environment with regards to health, safety and security. With fixed sensors enabling data collection outside hazardous areas and away from hazardous machines, ship engineers and other personnel do not have to enter these areas or approach these machines to evaluate machine conditions, thus reducing safety risks to operators.
SKF provides predictive and proactive maintenance for auxiliary machinery, applying condition monitoring supported by a broad range of services and products. With SKF “on board,” the goal of maintaining the highest levels of CBM can be achieved.