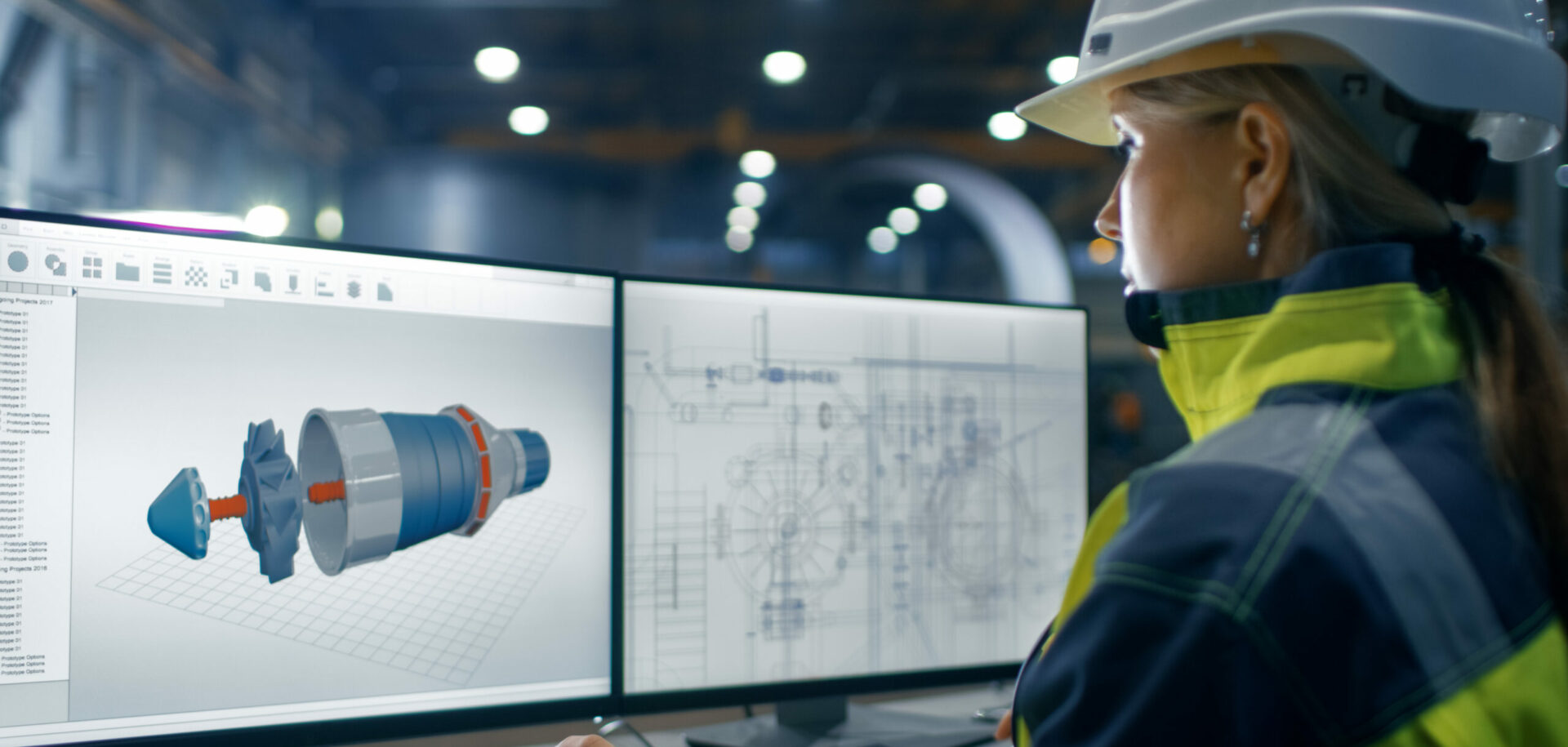
Creating the right environment for compressor bearings
L10aah = aSKFL10h
The refrigeration compressor industry is in a state of change. The thrust of this change is to develop more environmentally friendly, cost-effective compressors that consume less energy than current designsChanges in compressor technology to meet environmental and other customer-driven demands are being achieved through the adoption of alternative refrigerants and the development of smaller, more efficient compressors. These rely on compact, reliable bearing arrangements. Rolling bearings are being considered as an alternative to hydrodynamic bearings in higher speed machines to reduce frictional power losses. Higher efficiencies reduce the compressor’s electrical power consumption, thus contributing to the conservation of the earth’s resources.
Higher efficiency also reduces the compressor’s lifetime investment costs and improves product competitiveness. One constant within this industry sector is the demand for high reliability, whether it is for scroll, reciprocating, single, twin screw or centrifugal type compressors. SKF has worked intensively to develop the products and knowledge to apply bearings reliably in refrigerant applications.
Banned substances
For environmental reasons, the use of chlorofluorocarbons (CFCs) such as CFC-12 is now banned in new systems and its use in existing compressors is heavily restricted. The chlorine in the refrigerant, if released into the atmosphere, is known to contribute to global warming and the depletion of the earth’s ozone layer.
The common replacements for CFCs are the hydrochlorofluorocarbons HCFC-22, and the hydrofluorocarbons HFC-134a and HFC-401a, though a number of other chemicals are being considered. All these alternatives are less damaging to the environment as they either have low chlorine content or are chlorine-free.
These alternative refrigerants are not necessarily simple substitutes for CFCs, however. The HFC-134a refrigerant, for example, is incompatible with the natural mineral oils normally used with CFCs.
An important property of any refrigerant and oil combination is the ability to dissolve with one another. HFC-134a does not dissolve in mineral oils because of differences in molecular polarity. Polyol ester (POE) or polyalkene glycol (PAG) synthetic lubricants are necessary with this particular refrigerant.
As part of its programme in supporting the changes in the compressor industry, SKF has been active in a number of areas. At the forefront of these activities has been the SKF Life Theory, research at the group’s Engineering & Research Centre (ERC) in the Netherlands, coupled with design and manufacturing efforts related to the EC-design cylindrical roller and BE-design angular contact ball bearings. The CARBTM bearing, a compact aligning roller bearing developed by SKF, also has potential in high-pressure refrigerant applications and testing is currently underway.
Evaluating life
Refinements in evaluating bearing rating life through the SKF Life Theory are valuable in studying new refrigeration and oil combinations. The method considers that bearing steels have an endurance or fatigue load limit like other steels below which fatigue will not occur in the bearing raceways or rolling elements, provided that they are adequately lubricated and not disturbed by foreign debris. Too low a lubricating film thickness or contamination passing through the rolling contact can result in damage and dents in the surfaces, producing increased stresses in the materials. Subsequent over-rolling of the damaged surfaces by continued operation of the bearing results in the initiation of fatigue damage and failure.
Bearings that are satisfactorily lubricated, cleaned and protected from contamination have a much longer service life than predicted by previous rating life evaluation techniques.
In the refrigerant compressor, where lubrication cleanliness is important to a number of compressor components, the SKF Life Theory is a useful tool for the selection of bearings. Its validity has been verified through extensive laboratory and field testing and is under review by the International Organization for Standardization, ISO.
The theory is able to explain the relationship between bearing load capacity, lubrication conditions and cleanliness levels. Using this in compressor applications has resulted in smaller and more compact bearing arrangements using fewer bearings. Applying the theory in selection is achieved by the application engineering service of SKF, and the compressor engineer can have direct access to the CADalog and Electronic handbook computer programs available through SKF.
The computer programs allow the engineer to consider easily the operating viscosity and cleanliness in the compressor when the bearing selection is made. The SKF Life Theory is expressed by the following formula:
L10aah = aSKFL10h
where
L10aah=rating life according to SKF Life Theory, operating hours,
aSKF =life adjustment factor based on SKF Life Theory and,
L10h=basic rating life, operating hours
The factor aSKF takes into account the bearing fatigue load limit, Pu, lubrication condition, κ, and contamination condition, hc , in the bearing. The lubrication condition, K, is the ratio of the actual viscosity, n, of the lubricant in the bearing and the minimum required viscosity of the bearing, n1, at the operating temperature.
Research has been carried out at ERC on bearings with the two oil and refrigerant combinations. Tests were made on the HCFC-22 refrigerant/mineral oil and HFC-134a /polyol ester synthetic oil. It was found that the oxygen and chlorine-free environments with the new refrigerant and oil combinations do not produce the same protective oxide layer on the steel or have the same anti-wear and run-in behaviour on the bearing’s rolling contacts as in an air atmosphere or as in the CFC refrigerants.
This research indicates that greater minimum viscosity, n1 , is required in bearings operating in these refrigerants compared to operation in air or with the CFC refrigerants. Preliminary ERC results show that the minimum required viscosity must be doubled for HCFC-22 and tripled for HFC-134a with polyol ester oil when compared with an air atmosphere. It is recommended that the following adjustments be made for the refrigerant and lubrication in line with these findings:
- n1adj = 2n1, with HCFC-22 and mineral oil
- n1adj = 3n1, with HFC-134a and polyol ester oil
The lubricant in the compressor is diluted and its viscosity reduced by the refrigerant. The property of the lubricant to increase in viscosity under the pressure of the Hertzian rolling contact is reduced by the dissolved refrigerant.
Exacerbating the situation with HFC-134a is the fact that the polyol ester oil has a naturally lower increase in viscosity with pressure than mineral oil. These factors contribute to a reduction in the actual viscosity of the oil lubricating the bearing. The actual viscosity, nadj, can be adjusted for the effects of the refrigerant dilution.
This information is used with the SKF Life Theory by applying an adjusted lubrication condition, kadj, for the refrigerant condition:
- Kadj = nadj /n1adj
The SKF Life Theory coupled with the ERC research results help in the reliable selection and evaluation of operating bearings under refrigerant conditions. It can also help in the selection of the compressor lubricant and filtration.
Bearing advantage
EC-design cylindrical roller and BE-design angular contact ball bearings represent the state-of-the-art in bearing design, manufacture and applications technology. The cylindrical roller bearing has a high load-carrying capacity, logarithmic crowned rollers, optimised raceway finishes and optional cage designs to suit the particular compressor application. The logarithmic crowned rollers of the EC design significantly reduce the effects of bearing misalignment which is a critical manufacturing issue for the compressor manufacturer.
These EC-design cylindrical roller bearings are made with high running accuracy as standard, so that more costly special, higher precision bearings are not needed. There is little variation in bearing internal clearance when mounted although there is interchangeability between the bearing rings. Such features allow the compressor manufacturer to design for high efficiencies through smaller rotor clearances and easier compressor assembly.
The BE-design angular contact ball bearings also have a high load-carrying capacity and a 40– contact angle for high axial loads. Bearings for paired arrangements have high dimensional and running accuracy. The paired bearing is available with small axial clearances or preloads to suit the requirements of small compressor rotor running clearances. The BE-design single row angular contact bearing is available with glass fibre reinforced polyamide 6,6 cages or with machined brass or pressed steel cages.
The expertise of SKF in this area has led to a patented design for high speed compressor bearing arrangements for high speed dry air screw and gear driven centrifugal refrigeration compressors. In this, the bearings have high speed cages and high running accuracy coupled with a level of precision that makes them suitable for rotational speeds up to 1.2 million ndm. The angular contact ball bearings have special contact angles for optimum support of the applied compressor loads and the internal centrifugal forces. This high speed compressor arrangement significantly reduces the frictional losses in the compressor, so increasing efficiency, particularly during part load operation.
Potential for CARBTM The compact size, high load capacity and internal axial adjustment capability of the CARBTM bearing make it a strong candidate for use in high pressure compressors. Tests of the caged version of this bearing are currently underway in ammonia, NH3 and HFC-134a refrigerants. The CARBTM bearing is already used in high pressure air and natural gas screw compressors. It is also available with non-metallic cages and reduced internal clearances. These features make it attractive for compressor applications. The CARBTM bearing can replace cylindrical or needle roller bearings where space is limited in the compressor.
Evaluation
Extensive testing has also been carried out to evaluate the compatibility of bearing cage materials and bearing preservation methods with refrigerants. These tests show, for example, that the SKF machined brass cages used in cylindrical roller and angular contact ball bearings perform satisfactorily in ammonia refrigeration compressors. It was previously believed that the copper based alloy would react negatively with the ammonia gas and that the cage would be damaged by the interaction. The tests show that as long as the cage has low residual stresses from manufacture, its performance is satisfactory. However, a pressed brass cage is not recommended as it can be subject to stress related cracking due to the induced residual stresses in the material from the forming operation. The moulded polyamide 6,6 cage is satisfactory in ammonia and the new types of refrigerants and is widely used in compressors. Polyamide cages are now standard on the EC cylindrical and BE angular contact ball bearings.
Additional research and development is still needed to understand more fully the influences of refrigerant conditions on the rolling bearing. In particular, studies of all the alternative refrigerants are desirable to verify their compatibility with bearing cages and preservation materials. SKF is aiming to gain complete knowledge of the requirements and application parameters of bearings operating in these conditions with the goal of tailoring products closely to customer needs.
Keith Meyers,
SKF Industrial Division, King of Prussia,
Pennsylvania