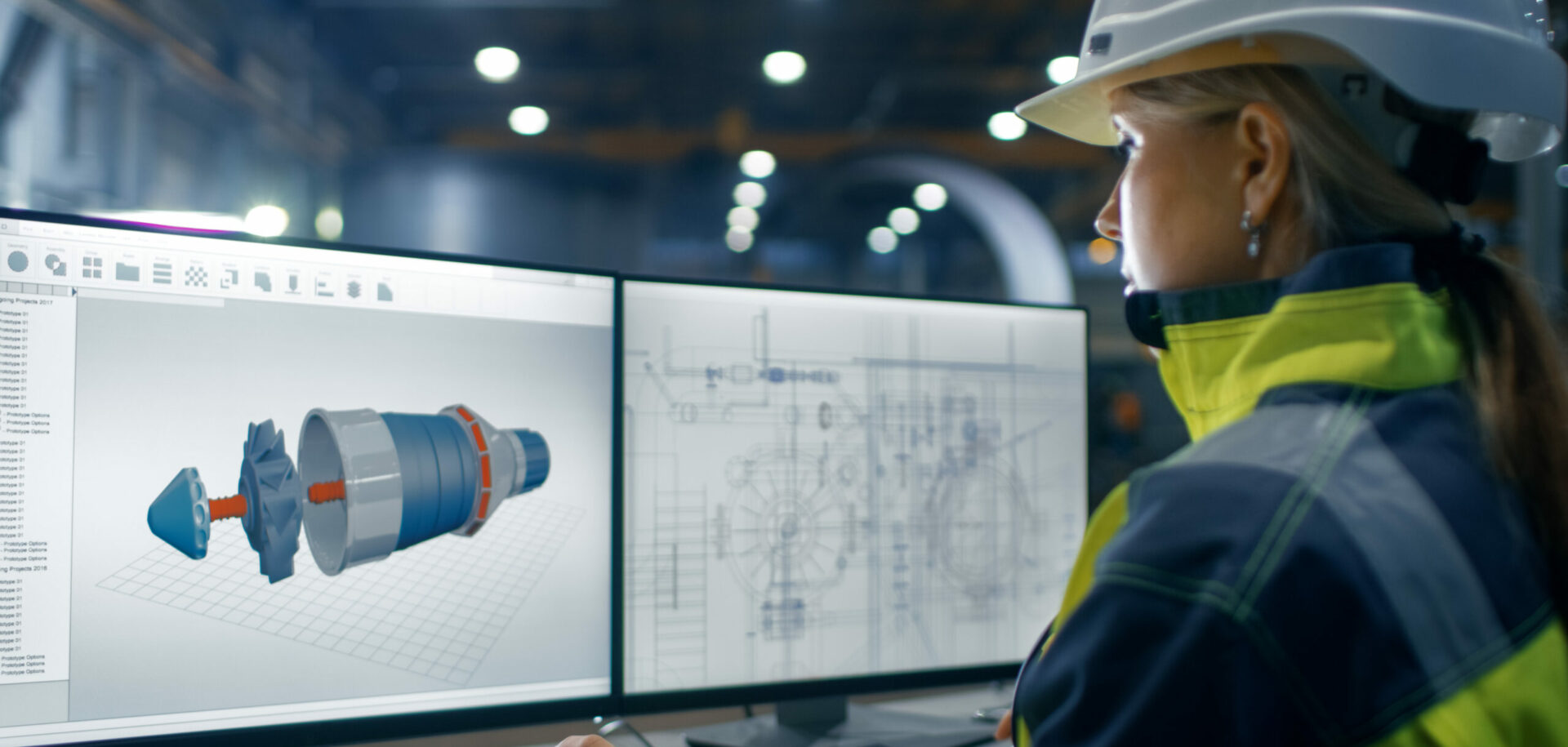
Customer approach to housing design
Design approach
A new generation of standard housings, the SNL range, will shortly enter the market – offering considerable flexibility in bearing choice, lubrication features and improved overall performance. Key to the development process has been a closer working relationship between
SKF and its customers.The split plummer block housing has been designed on a modular principle. This allows a wide choice of bearings including spherical roller bearings, self-aligning ball bearings or CARBTM. Overall bearing performance is also increased through improved bearing housing quality and enhanced heat transfer characteristics. Attention has also been paid to the improvement of grease and oil lubrication methods and facilitating bearing condition monitoring.
Design approach
Creating the SNL range has involved a design methodology called Quality Function Deployment (QFD). The design team at SKF Mekan AB in Sweden were initially trained by Ben Bles from the SKF Engineering & Research Centre (ERC) in the Netherlands.
Essentially this approach requires that quality aspects are considered on all design, development and production activities to provide the user with an appropriate product. Consequently, the customer has to be involved at the initial design concept stage to ascertain user needs and wishes.
In practice, Quality Function Deployment uses a matrix to correlate a list of customer needs with a number of design characteristics. This is in the form of basic “what” questions linked to “how” responses to the way in which these needs can be met. In this way, customer requirements can be translated into the design parameters, process and production details to outline the appropriate product features.
SKF has its own technical language that is often at odds to the customer’s own. The customer may be interested in low wear or easy mounting, while SKF engineers work with surface hardness and chamfer details. The QFD method, with its linked responses and triangular correlation matrix, called the House of Quality, can provide the bridge between these very different worlds.
Building the matrix
As the new housing has applications in a variety of industrial applications, leading customers from key segments were contacted. These included companies involved in fan applications, materials handling equipment, paper machines, and steel production, as well as general industrial applications.
In addition, a number of distributors with a broad knowledge of industry were also involved in the “brain-storming” sessions to create input to the product design.
Within each customer location, representatives from a minimum of three different departments with an interest in the product were interviewed. This included the quality, design, purchase, maintenance and mounting departments, for example.
Such meetings were carried out in an informal atmosphere that yielded results in the form of a number of customer requirements. These requirements were assigned an order of importance to guide the use of the Quality Function Deployment method.
It became apparent that within each customer location, different departments had diverging opinions on their specific needs. Five factors, however, proved to be of recurring importance to customers.
These were:
- simplified mounting
- housing ready for re-lubrication
- housing prepared for sensors for condition monitoring
- improved heat transfer characteristics
- components to build a bearing unit supplied from one source
Internal data
As crucial to the design process was the collection of information within SKF itself. Sources approached for views included the sales force, application and bearing design engineers. Their input provided the design specification to fulfil customer’s stated requirements.
Subsequently, a project team was formed to implement the new plummer block design based on the QFD “House of Quality” exercise. A prerequisite was that the SNL housing range should be interchangeable with the existing SNH models which involves following the appropriate international standards.
Additional design goals were to ensure that all existing accessories such as seals, are compatible with the new design, retain current designation systems and use environmentally friendly materials and manufacturing processes.
The bearing seating diameter and roundness tolerances have been tightened to improve bearing running performance. Equally important are close tolerances for the seal groove and shaft bore to ensure good sealing.
Grease relubrication for the SNL range has been achieved through the provision of an inlet hole and a grease nipple as standard.
A standard variant of this is also equipped with an outlet hole. Oil lubrication requires running at a lower temperature when compared to the prevailing SNH design. This has been achieved for example, through improved heat transfer between the plummer block and the support surface.
The potential to mix housing caps is a problem that has been identified when mounting more than one split housing at a time. The consequence of such an error is premature bearing failure because of damage to the all-important bearing seating tolerance when the incorrect housing cap and base are used. Such an eventuality can be avoided with a new marking system that pairs the cap and base together.
Mounting procedures have been further improved through the provision of clear instructions along with the seal package.
Investment
The SNL housing has a complex geometry that requires the use of a three dimensional design and manufacturing system. SKF Mekan now uses the Pro/ENGINEERÒ software system linked to a four axis Computer Numerically Controlled (CNC) milling machine. This system provides a solid prototype from which a manufacturing pattern can be created.
Using such equipment, the appropriate machining and cutting steps can be chosen from the computer’s menu and the computer program automatically selects the optimal machining sequences. When this has been completed, a further check is carried out to ensure that the CNC machine can successfully run the program on the factory floor.
In December 1996, operation started of a new castings facility in order to produce the first SNL units, built into a 48 m long production line. This produces 200 casts per hour and, depending on the casting size, each mould can hold from one to 12 pieces.
These casts are then machined to their final tolerances. As accurate machining is vital, SKF Mekan has also made a substantial investment in CNC machining equipment. The CNC round table units have internal measuring devices for automatic inspection and statistical evaluation of performance. Machining to the bearing seating, shaft bore and seal grooves is carried out by this equipment. The machined tolerance of the bearing seating has a great impact on the performance and life expectancy of a roller bearing while the precision of the seal groove determines seal wear and efficiency.
This year the SNL will be launched on the market. Several sizes of the new housing are being exhibited at the Hannover Fair between 14-19 April 1997. Most of these are available from stock and the range will be complete shortly.
Birgitta Hammar, Henrik Olsson,
Stig Persson and Jan-Ake Pettersson,
SKF Mekan AB
Katrineholm, Sweden