
Die Schmierqualität in Lagern von Kältemittelverdichtern unter Berücksichtigung des verwendeten Kältemittels
Die Maschineneffizienz und die Umweltbelastung von Kältemittelverdichtern haben zur Folge, dass neue Kältemittel und Kältemaschinenöle entwickelt werden. Die Industrie muss sich schnell auf diese Veränderungen einstellen, indem sie die Voraussetzungen für eine zuverlässige Lagerauswahl schafft, die für eine robuste Maschinenkonstruktion unerlässlich sind. All dies setzt die Fähigkeit voraus, die Schmierfilmdicke und den Schmierqualitätsparameter (Kappa-Wert) exakt vorausbestimmen zu können. In diesem Artikel wird ein Modellierungsverfahren beschrieben, das genau dies ermöglicht.
Die Bestimmung der Schmierqualität in Wälzlagern von Kältemittelverdichtern war schon immer schwierig, da es viele Unbekannte gibt, wie zum Beispiel die Verdünnung des Schmierstoffs durch das Kältemittel, die Lagertemperatur, die Piezoviskosität und die Viskositätsveränderung des Kältemittels in Abhängigkeit von Druck und Temperatur sowie die chemischen Einflüsse des Kältemittels auf die Lagerlaufbahnen. Bei Wälzlagern wird der κ-Wert zur Bestimmung der Schmierqualität herangezogen. Doch selbst wenn die tatsächliche Viskosität des Öl-Kältemittel-Gemischs einer Anwendung bekannt ist, kann die klassische Methode zur Berechnung des Schmierqualitätsparameters κ eines Lagers gemäß ISO 281:2007 [1] nicht angewendet werden, da bei diesem Verfahren von einer Schmierfilmdicke im Lager ausgegangen wird, wie sie für ein Schmieröl berechnet wird. Die Abnahme der Piezoviskosität im Gemisch und die Zunahme der Kompressibilität bei vorhandenem Kältemittel werden nicht berücksichtigt. Daher haben in der Vergangenheit verschiedene Wissenschaftler Änderungen am ursprünglichen Modell vorgeschlagen.
Meyers [2, 3] führte Änderungen bei der Berechnung des Schmierqualitätsparameters κ bei Wälzlagern ein, um die verdünnten Kältemittel im Schmieröl zu berücksichtigen. Dann hat er diesen Parameter bei der Berechnung der Lebensdauer L10 von Wälzlagern angewendet. Es wurden jedoch keine Lebensdauertests zur Validierung dieser Vorgehensweise durchgeführt. In einer internen Mitteilung schreibt er auch, dass B.O. Jacobson festgestellt hatte, dass der reduzierte Chlorgehalt des HFCFC-22-Kältemittels und das Fehlen von Chlor im HFC-134a-Kältemittel die Viskositätsanforderungen an die Schmierung von Wälzlagern deutlich erhöht. Er errechnete, dass für ein Lager, das mit einem Gemisch aus HFCKW-22 und Mineralöl geschmiert wird, eine doppelt so hohe Betriebsviskosität erforderlich ist; bei einem Lager, das mit einem Gemisch aus HFC-134a und Polyolesteröl (POE) geschmiert wird, muss die Betriebsviskosität dreimal so hoch sein wie bei einem mineralölgeschmierten Lager. Zum ersten Mal wurde damit bei der Berechnung der erforderlichen Viskosität des Lagers ein „technischer“ Sicherheitsfaktor aufgrund der Kältemittelchemie eingeführt, der über die einfache Berechnung der Schmierfilmdicke hinausgeht. Dieses Modell wird in Meyers [2] zusammenfassend beschrieben.
Während die Berechnung von L10 in dieser Anwendung nach wie vor schwierig ist, eignet sie sich vielleicht in idealer Weise für ein Lagerlebensdauermodell, das explizit die Bereiche an und unterhalb der Oberfläche trennt, wie bei Morales-Espejel et al. [4]. Die in [4] vorgeschlagene Methodik erfordert jedoch eine genaue Berechnung der Filmdicke im Kontakt, was nur möglich ist, wenn die Viskosität, die Piezoviskosität und die Kompressibilität des Gemischs bestimmt werden können. Einige Wissenschaftler haben versucht, hierfür entsprechende Verfahrensweisen zu entwickeln. Auch wenn Fortschritte erzielt wurden, gibt es nur sehr wenige Veröffentlichungen, die eine technische Methodik für die Berechnung der Viskosität von Öl-Kältemittel-Gemischen, der Piezoviskosität, der Filmdicke und der erforderlichen Viskosität behandeln. Im vorliegenden Artikel wird beschrieben, wie dies durch die Änderung der Viskosität unter dem Einfluss von Druck und Temperatur des Schmieröls und des Kältemittels unabhängig voneinander erreicht werden kann. Anschließend werden die Schmiereigenschaften des Gemischs anhand von modifizierten Gleichungen der Mischungsgesetze berechnet. Auf dieser Basis können Daniel-Plots erstellt werden, die eine Berechnung der für das Lager erforderlichen Viskosität und des Schmierqualitätsparameters ermöglichen.
Mischungsgesetze
Literature models
In der Vergangenheit wurden Studien zur Messung und Bestimmung der Filmdicke in mit Öl-Kältemittel-Gemischen geschmierten EHD-Kontakten durchgeführt. Bei der Berechnung der Filmdicke in solchen Kontakten ist die Bestimmung der Mischungseigenschaften ein wichtiger Zwischenschritt. Es wurden verschiedene Gleichungen zur Berechnung der Viskosität und Piezoviskosität von Öl-Kältemittel-Gemischen vorgeschlagen. Akei und Mizuhara [5] verwenden beispielsweise die Eyring-Theorie, um Gleichungen für den piezoviskosen Koeffizienten und die Viskosität abzuleiten: Bei m=Moil / Mref ist M die Molekularmasse des Bestandteils. Hier steht α für den piezoviskosen Koeffizienten, η für die dynamische Viskosität, s für den Anteil der Verdünnung des Bestandteils, oil für Öl und ref bezieht sich auf das Kühlmittel. Die vorstehenden Gleichungen können, wie in Bild 1 dargestellt, für verschiedene Kältemittelanteile und Molekularmassenverhältnisse verwendet werden.
Adaptiertes Modell
Die ursprünglichen Mischungsgleichungen werden dahingehend geändert, dass zwei Funktionen (kal, ket) das Molekularmassenverhältnis wie folgt multiplizieren:
Diese Funktionen werden mithilfe von Viskositätsmessungen verschiedener Öl-Kältemittel-Gemische kalibriert; sie sind also abhängig von der Ölviskosität und der Betriebstemperatur. Hieraus folgt:
η0 steht für die dynamische Viskosität des Öls unter atmosphärischem Druck und T für die Temperatur.
In [6] wurde nachgewiesen, dass mit dem verbesserten Modell basierend auf der Mischungsviskosität eine wesentlich bessere Übereinstimmung mit den Messungen eines Gemischs aus dem Kältemittel HFC-134a und dem Öl POE 100 erzielt werden konnte. Das Modell wurde mit verschiedenen anderen Kombinationen von Ölen und Kältemitteln bei unterschiedlichen Temperaturen und Verdünnungsgraden getestet, und die Übereinstimmung mit den Messungen war immer wesentlich besser als beim ursprünglichen Modell.
Im vorliegenden Artikel wird der beschriebene Ansatz auf ein Gemisch aus dem Kältemittel HFC-134a und dem Öl POE 170 angewendet; hierbei handelt es sich um eine typische Gemischzusammensetzung wie sie in Kältemittel-Schraubenkompressoren gemäß Fuchs Schmierstoffe GmbH [7] verwendet wird. Die jeweiligen Fluideigenschaften sind in Tabelle 1 zusammengefasst dargestellt. Der Daniel-Plot für dieses Gemisch ist in Bild 2 dargestellt und wurde in der Publikation der Fuchs Schmierstoffe GmbH [8] veröffentlicht.
Schmierqualität in Wälzlagern
Für Wälzlager, die mit einem Öl-Kältemittel-Gemisch geschmiert werden, wird in [6] eine Modifikation des Schmierqualitätsparameters κ vorgeschlagen. Die endgültige angepasste tatsächliche Viskosität eines Öl-Kältemittel-Gemischs zur Kappa-Berechnung (κ=νadj ⁄ ν1) wird wie folgt bestimmt:
und
Zu beachten ist, dass der Anpassungsfaktor fadj = fpiezo / fs mathematisch gesehen unbegrenzt ist und zu Mischungsanteilen von 100 % Kältemittel führen kann, aber natürlich werden Stahllager dies, wie in [10] dargestellt, nicht unbeschadet überstehen. Es wird deshalb vorgeschlagen, dieses Kompensationsverfahren aus praktischen Gründen auf eine maximale Verdünnung von 30 % des Kältemittels zu beschränken (sref <0.3).
Nachfolgend wird anhand eines praktischen Anwendungsbeispiels das Potenzial der beschriebenen Verfahrensweise und der Einfluss des Viskositätsverhaltens des Schmierstoffs auf die Systemberechnungen aufgezeigt. Die Schmierqualität von Lagern eines Schraubenverdichters einer Klimaanlage wird analysiert. In Tabelle 2 sind die Betriebsbedingungen zusammengefasst dargestellt.
Einfluss von Temperatur und Verdünnung
Die Kennlinien der Verdünnung in Abhängigkeit von Druck und Temperatur sind für jedes Öl-Kältemittel-Gemisch spezifisch, und diese Angaben sind in den Daniel-Plots enthalten. Bei diesem Beispiel wird davon ausgegangen, dass die Schmiermittelbedingungen durch den Förderdruck des Verdichters bestimmt werden. Das hieraus resultierende Mischungsverhältnis von Öl und Kältemittel wird im Daniel-Plot durch den Schnittpunkt der Linien für Druck (Isobaren) und Temperatur definiert. In Bild 3 (a) werden diese Angaben für zwei Drücke aus dem Daniel-Plot in Bild 2 (a) entnommen. Beim Gemisch aus POE 170 und HFC-134a nimmt die Verdünnung des Öls durch das Kältemittel bei 6 und 8 bar und höheren Temperaturen ab. Im untersuchten Temperaturbereich und bei 8 bar enthält das Gemisch zwischen 8 % und 22 % Kältemittel.
Die Verdünnung bei einem bestimmten Druck und einer bestimmten Temperatur ist ein wichtiger Faktor, der die Schmierqualität des Lagers beeinflusst und von der tatsächlichen Öl-Kältemittel-Kombination abhängig ist. Die Kältemittel mit einem niedrigen Treibhauspotenzial (GWP) und einem Ozonabbaupotenzial (ODP) von null führen häufig zu einer höheren Verdünnung als die vorherige Kältemittelgeneration, wie beispielsweise HFC-134a.
Da die Mischungsviskosität (ebenso wie die Piezoviskosität) bei zunehmender Verdünnung abnimmt (siehe Bild 1) und sich die Viskosität bei höherer Temperatur reduziert (siehe Bild 2 (a)), führt die Betrachtung der Kennlinie von Verdünnung und Temperatur in Bild 3 (a) zu einer Überlagerung dieser beiden gegenläufigen Trends. Dies führt zu einer interessanten Kennlinie, die einen maximalen Viskositätswert innerhalb des betrachteten Temperaturbereichs und einen Abfall der Viskosität sowohl bei niedrigeren als auch bei höheren Temperaturen aufweist. Dieser Effekt zeigt sich auch im Daniel-Plot, wenn man der Isobarenlinie folgt. Bild 3 (b) zeigt die Nachbildung der Mischungsviskosität νmix bei 8 bar nach der angepassten Gleichung für die Viskositätsmischung sowie die angepasste (Mischungs-)Viskosität νadj einschließlich der Viskositätsminderung durch den Piezoviskositätseffekt und den vorgeschlagenen Sicherheitsfaktor. Im gesamten Beispiel wird ein Jacobson-Sicherheitsfaktor f von 1,5 verwendet.
Da die Ergebnisse für die Schmierqualitätsparameter beim Schrägkugellager (ACBB) und beim Zylinderrollenlager (CRB) unter den gewählten Betriebsbedingungen sehr ähnlich sind, werden in den folgenden Diagrammen nur die Ergebnisse für das Schrägkugellager dargestellt.
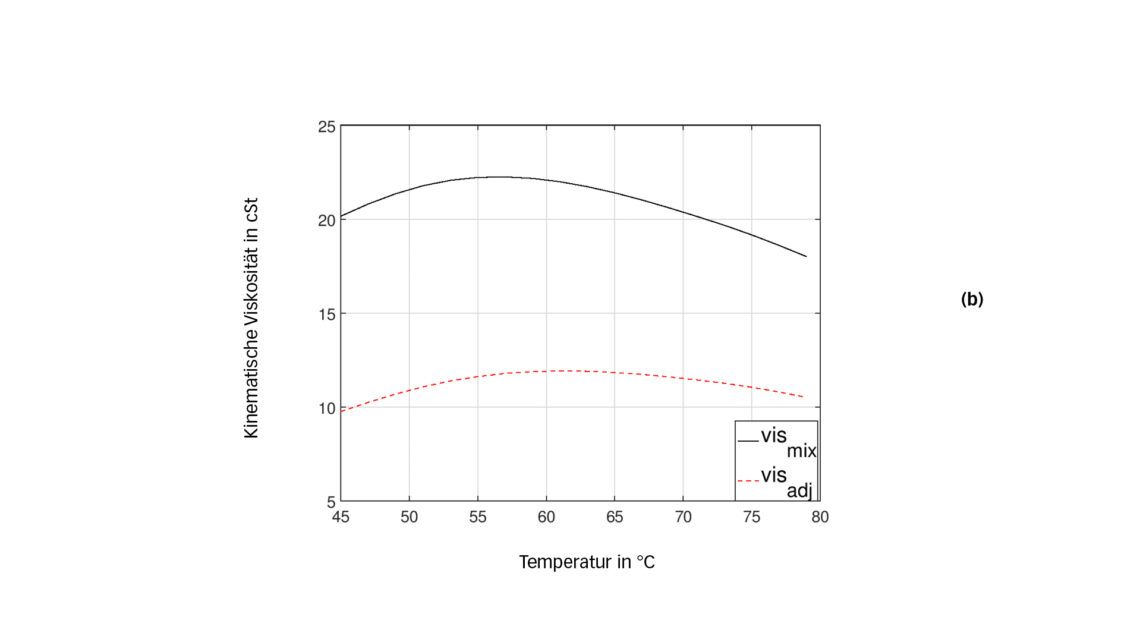
Einfluss des Förderdrucks
Als Nächstes wird die gleiche Auswertung wiederholt, wobei ein Förderdruck von 6 bar anstelle von 8 bar angenommen wird (bei gleicher Drehzahl wie zuvor). Bild 3 (a) zeigt eine Verminderung der Verdünnung aufgrund des niedrigeren Drucks. Im betrachteten Temperaturbereich liegt der Kältemittelgehalt zwischen 6 % und 15 % bei 6 bar.
In Bild 4 (b) wird die Schmierqualität bei 6 bar dargestellt. Wie das Daniel-Plot zeigt, führt der geringere Druck zu einer geringeren Verdünnung bei gleicher Temperatur und somit zu einem Anstieg der Mischungsviskosität und des Kappa-Wertes im Vergleich zum Beispiel bei 8 bar.
Einfluss der Drehzahl
Mit Einführung der Antriebe mit variabler Drehzahlregelung (VSD) ist die Verdichterdrehzahl eine zusätzliche Komponente im Betriebsbereich geworden. Die Drehzahl ist ein wichtiger Parameter für die Schmierfilmdicke im Wälzlager. Nun wird die vorherige Bedingung wieder aufgegriffen und mit der zusätzlichen Komponente Drehzahl dargestellt.
Fazit
Der vorliegende Artikel beschreibt eine vollständige Methodik zur Bestimmung des Schmierqualitätsparameters κ bei Wälzlagern. Zunächst werden genaue Gleichungen basierend auf den Mischungsgesetzen für die Viskosität und die Piezoviskosität aufgestellt. Anhand dieser Gleichungen können die entsprechenden Daniel-Diagramme abgeleitet werden, falls sie noch nicht vorliegen. Anschließend werden diese Gleichungen zur Berechnung der Mischungsviskosität verwendet. Bei dieser Vorgehensweise wird ein Anpassungsfaktor für die tatsächliche Viskosität im Lager abgeleitet, wenn ein Öl-Kältemittel-Gemisch vorliegt. Wenn dieser Anpassungsfaktor mit der nach dem beschriebenen Verfahren ermittelten Mischungsviskosität multipliziert wird, reduziert sich deren Wert auf ein unschädliches Maß.
Wie in diesem Artikel dargelegt, lässt der Jacobson-Sicherheitsfaktor f dem Konstrukteur einen gewissen Spielraum, um die Sicherheit des geplanten Designs anzupassen, da es immer noch einige unbekannte Effekte gibt. Einer dieser Effekte wurde bereits in [10] behandelt: Die chemische Aggressivität des Kältemittels gegenüber dem Lagerstahl, die dessen Dauerfestigkeit durch Korrosion oder schlechte Schmierfähigkeit verringert. So können beispielsweise Kältemittel mit einem sehr niedrigen Treibhauspotenzial (GWP) und einem Ozonabbaupotenzial (ODP) von null als hochreaktive/hochkorrosive Flüssigkeiten betrachtet werden, insbesondere in Gegenwart von Feuchtigkeit. In diesen Fällen wird den Konstrukteuren empfohlen f ≥ 2 zu verwenden, ansonsten wäre 1.5 ≤ f ≤ 2 ausreichend.
Bei einer realen Anwendung werden alle Parameter, die die Schmierqualität des Gemischs beeinflussen (z. B. Temperatur, Druck und Drehzahl), basierend auf dem Betriebszyklus der Klimaanlage aufeinander abgestimmt. Mit dem vorgeschlagenen Ansatz ist es möglich, die Schmierqualität der Lager für jeden Punkt im Betriebsdiagramm vorauszuberechnen.
Aus dieser Analyse lässt sich folgendes Fazit ziehen:
- Die in der Literatur vorhandenen Gleichungen, die auf den Mischungsgesetzen von Öl-Kühlmittel-Gemischen basieren, müssen hinsichtlich der Viskosität und Temperatur des Schmiermittels angepasst werden, um die Mischungsviskosität und die Piezoviskosität genau vorausberechnen zu können.
- Bei der nach dem beschriebenen Verfahren ermittelten Mischungsviskosität in einem Wälzlager müssen noch die Piezoviskosität und der Sicherheitsfaktor entsprechend angepasst werden, bevor die Mischungsviskosität zur Berechnung der Schmierqualität eines mit einem Öl-Kältemittel-Gemisch betriebenen Lagers verwendet werden kann.
- Der Jacobson-Sicherheitsfaktor ist eine anpassungsfähige Größe bei der Konstruktion einer Lageranwendung. Bei hochreaktiven Kältemitteln (insbesondere in Gegenwart von Feuchtigkeit) sind für diesen Sicherheitsfaktor höhere Werte erforderlich.