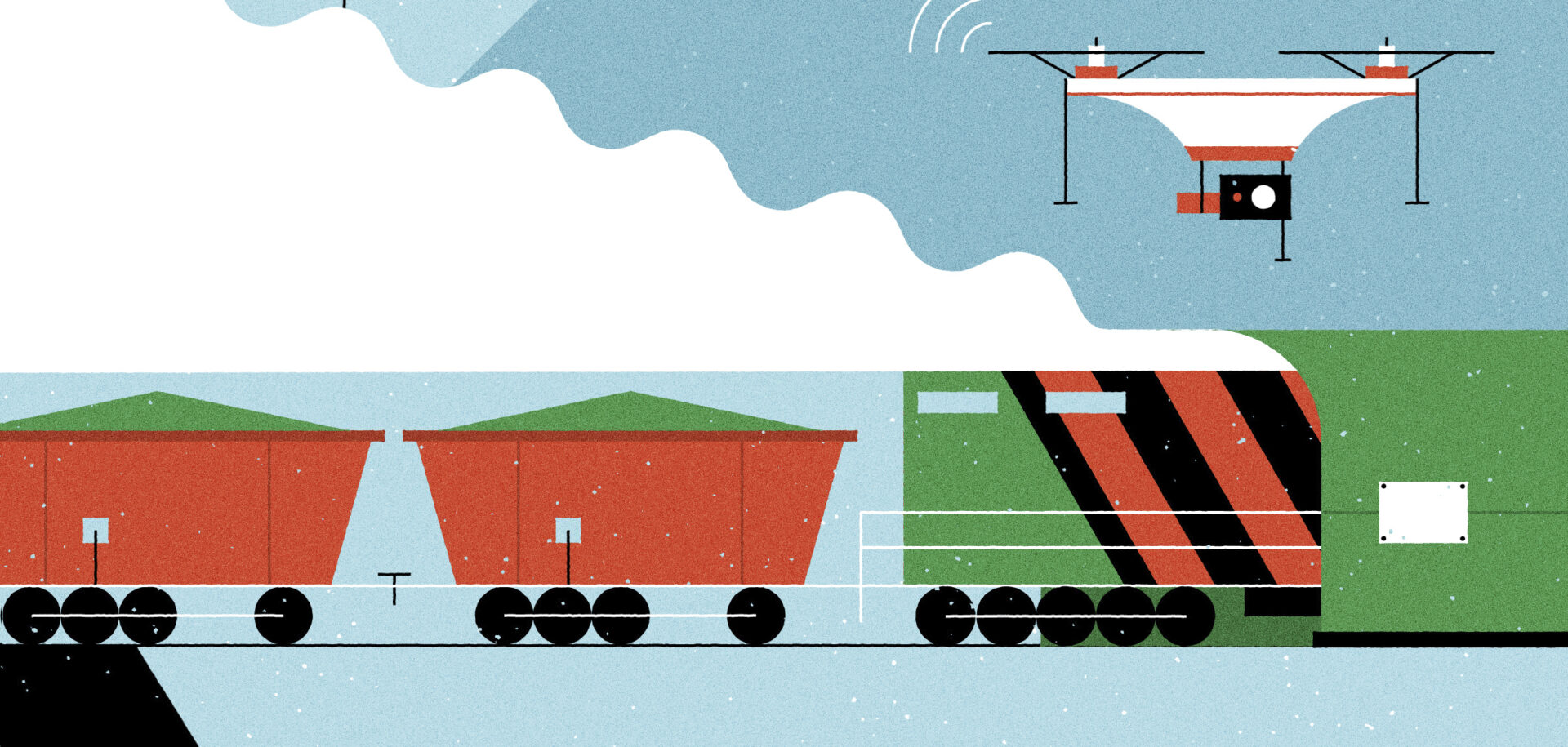
Die vierte Industrielle Revolution
Die vierte Industrielle Revolution, das Industrielle Internet der Dinge, ist auf dem Vormarsch. Es soll die Industrie effizienter und produktiver machen und bis 2030 zwölf Billionen Euro zur Weltwirtschaft beisteuern.
Eines Tages Ende 2017 verließ ein Güterzug, schwer beladen mit Eisenerz, die Stadt Tom Price in der westaustralischen Bergbauregion Pilbara und fuhr zu dem 100 Kilometer entfernten Ort Paraburdoo.
Die Fahrt auf der staubigen Wüstenstrecke verlief ereignislos und war recht unspektakulär – abgesehen von einer Sache: An Bord des Zuges befand sich nicht ein einziger Mensch. Stattdessen steuerte eine Reihe von Sensoren, die mit Computerprozessoren und einer Fernsteuerungszentrale vernetzt waren, den vom Bergbauunternehmen Rio Tinto betriebenen Zug. Der erfolgreiche Probelauf sollte zeigen, dass die weltweit erste Fernbahnstrecke für voll autonomen Schwerlastverkehr 2018 in Betrieb genommen werden kann. Die Probefahrt demonstrierte auch das enorme Potenzial des Industriellen Internets der Dinge (Industrial Internet of Things, IIoT), also jener Vernetzung von Maschinen, die die Arbeitsweise der Industrie grundlegend verändern wird.
„Das Industrielle Internet der Dinge wurde vor wenigen Jahren noch als Spinnerei abgetan“, sagt Brian Buntz, Content Director beim IOT Institute, der führenden News-Site und Community für das Internet der Dinge. „Heute wird überall auf der Welt massiv in diesen Bereich investiert. Hersteller aus China versuchen so, sich weitere Wettbewerbsvorteile zu sichern, die Amerikaner wollen auf diese Weise Produktion aus China ins eigene Land zurückholen und in ganz Europa unterstützen Regierungen Smart Factories (intelligente Fabriken).“
Wenn Sie in 15 Jahren eine Fabrik betreten, erkennen Sie möglicherweise überhaupt nichts mehr wieder.
Erik Walenza, CEO, IoT ONE
Die Definitionen variieren zwar, aber generell gilt das Industrielle Internet der Dinge als Teil von Industrie 4.0, der vierten Industriellen Revolution seit der Mechanisierung von industriellen Prozessen im 18. Jahrhundert. Während sich die zweite Industrielle Revolution auf Fließbandfertigung und Globalisierung, die dritte auf das Internet und die Robotertechnik konzentrierte, geht es bei der vierten um die Nutzung von Big Data, vernetzten Sensoren, autonomen Maschinen und künstlicher Intelligenz. Dabei wird das Internet der Dinge – das Ökosystem von vernetzten Geräten, das zum Beispiel Ihre Google Home Assistants oder Fitbit-Aktivitätstracker steuert – auf das industrielle Umfeld übertragen.
Unternehmen hoffen, dass sie sich durch die Ausrüstung von industriellen Komponenten mit Sensoren, die Vernetzung von Systemen, das Sammeln von Daten und den Einsatz von hochentwickelter Computertechnik bei einfachen Tätigkeiten von menschlicher Arbeitskraft unabhängiger machen können. Gleichzeitig wollen sie dadurch ihre Produktivität und Effizienz steigern. Obwohl das volle Potenzial des IIoT zurzeit noch erforscht wird, nennt der Computer-Riese IBM in seinem 2017 veröffentlichten Bericht schon einige unmittelbare Vorteile für die Industrie: vorausschauende Wartung, intelligente Verbrauchsmessungen, Asset Tracking, vernetzte Fahrzeuge und verbessertes Fuhrparkmanagement.
Nach Schätzungen der Analysten von Industry ARC soll der IIoT-Markt bis 2021 weltweit einen Wert von über 105 Milliarden Euro erreichen. Das Beratungsunternehmen Accenture geht in seinem Bericht Winning with the Industrial Internet of Things sogar davon aus, dass diese Technologie bis 2030 ganze zwölf Billionen Euro zur Weltwirtschaft beisteuern könnte.
Victoria Van Camp, CTO und President, Innovation & Business Development, SKF:
„Wir leben in einer Zeit, in der neue Technologien wieder einmal die Geschäftsmöglichkeiten für Hersteller und Dienstleister verbessern können. Ein Beispiel: Man zahlt für die Leistung, die man bekommt, nicht nur für die Produkte an sich. Warum hat man das nicht immer so gemacht? Nun, vor allem, weil die Informationen zur Messung und Verbesserung der ‘Leistung’ nicht zur Verfügung standen. Für mich geht es bei IIoT um die Nutzung und Analyse von Echtzeit-Daten aus vielen Quellen, also um die Umwandlung von Daten in Informationen. Dadurch können – automatisch – Maßnahmen ergriffen werden, bevor etwas passiert. ‘Maßnahmen ergreifen’ kann bedeuten, Prozessparameter in Echtzeit zu korrigieren, das Schmiersystem zu justieren, Teile im Voraus zu bestellen …. und vieles mehr. Lernfähige Maschinen und Künstliche Intelligenz sind eine wesentliche Voraussetzung für IIoT, damit wir nicht von Signalen, Daten und Informationen überflutet werden.“
Das IIoT steht noch am Anfang, aber Buntz zufolge gibt es jede Menge Beispiele von Unternehmen, die diese Technologie für Veränderungsprozesse nutzen.
Rio Tinto betreibt nicht nur den nahezu komplett autonomen Güterzug, sondern setzt in seinen Bergwerken auch miteinander vernetzte autonome Muldenkipper, Bohrer und Drohnen ein. Dadurch erhöht Rio Tinto die Effizienz und kann in einem gefährlichen Arbeitsumfeld auf menschliche Arbeitskraft verzichten.
Sensoren an Industrierobotern der Firma ABB informieren die Bediener über erforderliche Instandhaltungsmaßnahmen. Dadurch entfallen standardisierte, intervallgetriebene Wartungsroutinen, und die Zahl der Störfälle nimmt ab. Das globale Versandunternehmen Amazon lässt bei der Kommissionierung von Kundenaufträgen die Produkte durch WLAN-vernetzte Roboter im Lager lokalisieren und aus dem Regal holen.
Erik Walenza betreibt die Website IoT ONE, die IIoT-Anbieter mit Unternehmen und Organisationen zusammenbringt, die nach IIoT-Lösungen suchen. Die Website stellt neben einer Liste von Anwendungsfällen und IIoT-Lösungen auch einen auf Community-Umfragen und Angebotsanalysen basierenden Top 100 IIoT-Index der besten Anbieter solcher Systeme bereit. Walenza zufolge liegen die Technologieunternehmen IBM und Intel, der Software-Entwickler SAP, der Vernetzungsspezialist Cisco und der Mischkonzern General Electric im IIoT-Bereich an der Spitze.
„Bei IBM liegt der Schwerpunkt auf Beratung, das heißt, auf IIOT-Anwendungen und Marktanpassungen. SAP ist dagegen führend, wenn es darum geht, eine offene IoT-Plattform zu schaffen, an die andere Unternehmen externe Apps als Plug-in anbinden können“, erklärt Walenza. „Cisco treibt technische Innovationen voran, um Einführungsengpässe in Bereichen wie Edge Computing und Cybersicherheit zu beseitigen, während Intel ebenso wie SAP aufgrund des horizontalen Charakters seiner Technologie extrem kooperativ ausgerichtet ist. GE setzt mit seiner cloudbasierten Plattform Predix Industrial neue Kapazitätsgrenzen.“
Vor diesem Hintergrund stellt sich die Frage: Wie sieht die Zukunft für den IIoT-Sektor aus? Sowohl Buntz als auch Walenza sehen Schwierigkeiten, aber auch immense Gewinne voraus.
Eine Herausforderung sind die riesigen Datenmengen, die die zahlreichen, in industriellen Prozessen und Maschinen integrierten Sensoren generieren werden. Hier bieten sich Möglichkeiten für Effizienzsteigerungen und eine breite Palette neuer Dienstleistungen. Allerdings besteht ohne adäquate Sicherheit die Gefahr, dass die Daten von Cyberkriminellen oder konkurrierenden Unternehmen gestohlen werden.
Eine weitere Herausforderung ist die Frage der Besitzrechte an Daten, die zum Beispiel von miteinander vernetzten Fahrzeugen gesammelt werden. Ist der Hersteller, der die Daten für die Bereitstellung einer Serviceleistung nutzt, oder der Besitzer der Ausrüstung der Eigentümer?
Ungeachtet davon, wie diese Probleme gelöst werden, gibt es kaum einen Zweifel daran, dass das Industrielle Internet der Dinge in den kommenden Jahren jeden Industriezweig verändern wird. „Bei weiterhin rückläufigen Preisen für IIoT-Technologie zeichnet sich das Bild deutlicher ab“, meint Walenza. „Wenn Sie in 15 Jahren eine Fabrik betreten, erkennen Sie möglicherweise überhaupt nichts mehr wieder.“
SKF und das IIoT
SKF weiß seit langem um die Bedeutung der Digitalisierung in der Industrie. Schon vor vielen Jahren leistete das Unternehmen Pionierarbeit. SKF hat seit 15 Jahren Fernüberwachungssysteme in Betrieb, an die via Cloud inzwischen rund eine Million Maschinenkomponenten „angeschlossen“ sind.
SKF Insight ist ein drahtloses zustandsbasiertes System zur Überwachung der Lagerleistung. Es misst Parameter wie Schwingungen und Temperatur, um Abweichungen in einem frühen Stadium zu erkennen und so ungeplante Ausfälle und Stillstände auf ein Minimum zu reduzieren.
In Zusammenarbeit mit ihren Partnern Siemens und Bombardier stellt SKF im Rahmen eines 6-Milliarden-Euro-Projekts der Deutschen Bahn Kegelrollenlager mit integrierten Sensoren für den neuen Hochgeschwindigkeitszug ICE 4 bereit. Die Lagersensoren überwachen Drehzahl und Drehrichtung, wobei die Daten vom Bremssystem des Zugs generiert und anschließend genutzt werden.
Bei fest installierten Anlagen hat SKF leistungsabhängige Verträge abgeschlossen, bei denen Prozess- und Maschinendaten für die Prozessoptimierung sowie für reibungslose Wartungsstopps und maximale Maschinenverfügbarkeit von ausschlaggebender Bedeutung sind.
Vor kurzem eröffnete das Unternehmen in Schweden ein Software-Center, das sich mit Zukunftstechnologien für die Datenerfassung und analyse sowie mit automatischen Diagnosesystemen der nächsten Generation befasst. Das Center arbeitet zudem an der Entwicklung von Mixed-Reality-Lösungen, bei denen Wartungstechniker während der Durchführung von Inspektionen ein Overlay mit technischen Daten, Anweisungen und Echtzeit-Informationen zur Maschinenleistung sehen.