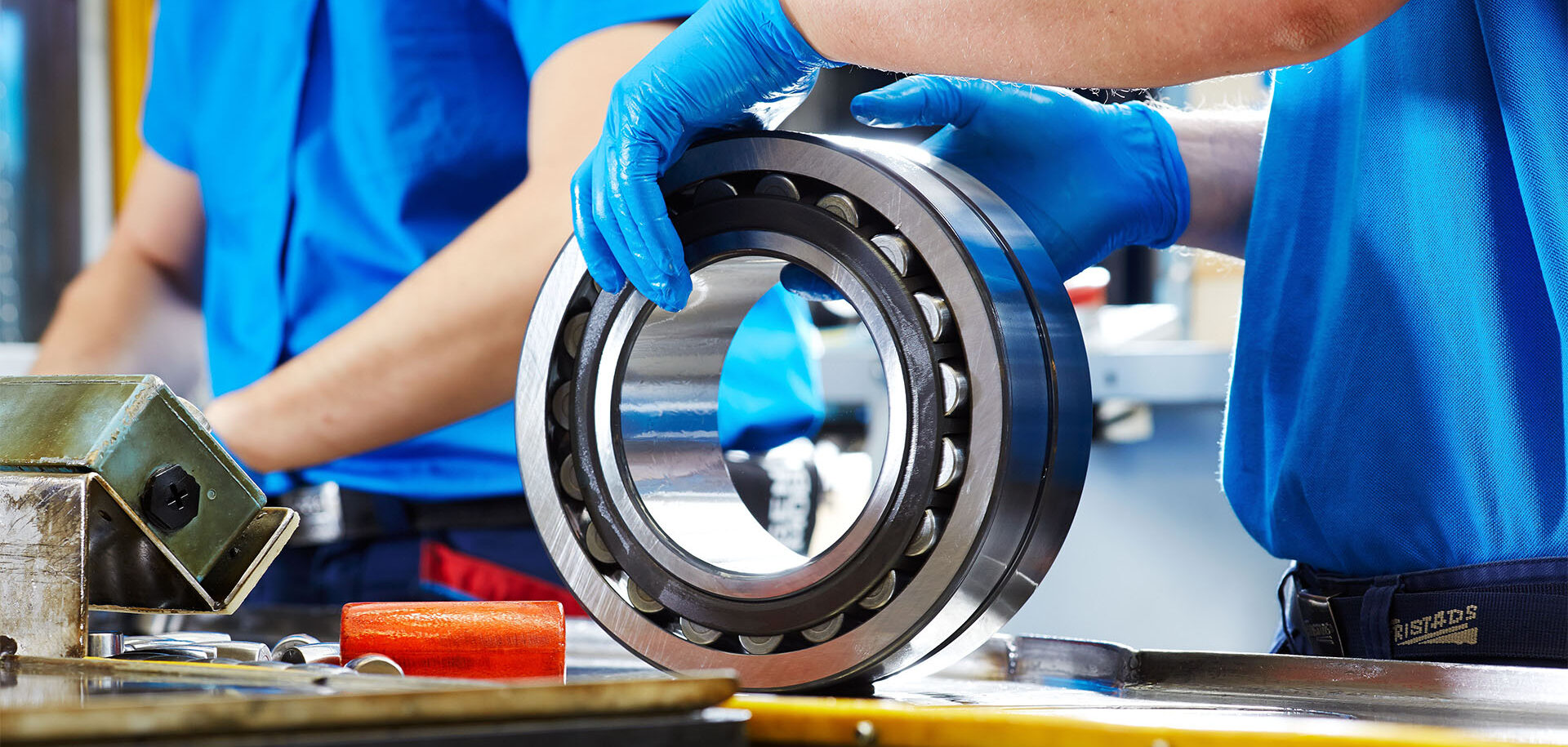
Die Zukunft für SKF: Schlanke und digitalisierte Produktion
Als Ajay Naik 2017 von Indien nach Schweden zog, um die Leitung der SKF Fabrik in Göteborg zu übernehmen, stand das Werk in vieler Hinsicht vor Problemen. Mit seinem Team verwandelte er diese Probleme in Erfolge.
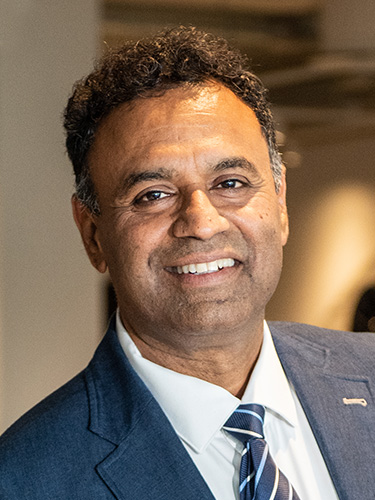
Die SKF Fabrik in Göteborg erlebte 2017 eine nie da gewesene globale Nachfragewelle, gleichzeitig war das Unternehmen gerade mit einer umfassenden Überarbeitung der IT-Systeme beschäftigt. Im Sommer stapelten sich die Aufträge, und wegen akuten Personalmangels suchte man dringend nach Aushilfen.
„Wir waren einfach unvorbereitet“, erinnert sich Ajay Naik, Geschäftsleiter und Country Manager SKF Schweden. „Unter normalen Umständen konnten wir einen schrittweisen Nachfrageanstieg bewältigen, aber ausgerechnet als wir mit internen Problemen beschäftigt waren, schoss die Nachfrage in die Höhe. Die Lage war katastrophal.“
Naik war vorher 30 Jahre lang für SKF in Indien tätig gewesen und hatte Erfahrung mit Herausforderungen im Fertigungsprozess. In Schweden griff er darauf zurück: Er setzte einen Krisenmanager ein, benannte einen Lieferkettenexperten und richtete ein Krisenzimmer ein, um die Situation zuentschärfen. Bis Ende 2017 war das Schlimmste überstanden. Ein Transformationsprozess hatte begonnen, der das SKF Werk in Göteborg zu einer der weltweit leistungsfähigsten Produktionsstätten machen sollte. 2021 erhielt Naik für seine Errungenschaften den European Quality Leader (EQL) Award von der Europäischen Organisation für Qualität (European Organization for Quality).
„Wir waren einfach unvorbereitet“, erinnert sich Ajay Naik, Geschäftsleiter und Country Manager SKF Schweden. „Unter normalen Umständen konnten wir einen schrittweisen Nachfrageanstieg bewältigen, aber ausgerechnet als wir mit internen Problemen beschäftigt waren, schoss die Nachfrage in die Höhe. Die Lage war katastrophal.“
Naik war vorher 30 Jahre lang für SKF in Indien tätig gewesen und hatte Erfahrung mit Herausforderungen im Fertigungsprozess. In Schweden griff er darauf zurück: Er setzte einen Krisenmanager ein, benannte einen Lieferkettenexperten und richtete ein Krisenzimmer ein, um die Situation zuentschärfen. Bis Ende 2017 war das Schlimmste überstanden. Ein Transformationsprozess hatte begonnen, der das SKF Werk in Göteborg zu einer der weltweit leistungsfähigsten Produktionsstätten machen sollte. 2021 erhielt Naik für seine Errungenschaften den European Quality Leader (EQL) Award von der Europäischen Organisation für Qualität (European Organization for Quality).
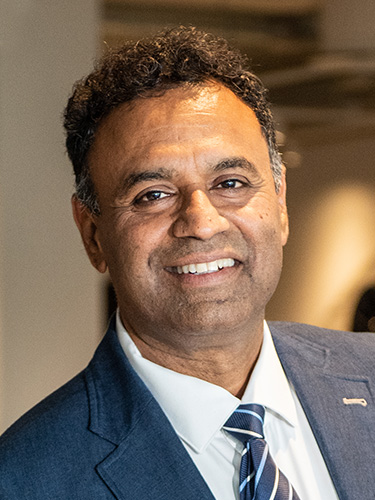
Erste Veränderungen
Die erste Etappe der Transformation begann im Januar 2018 und dauerte bis zum Sommer 2019. Naik nennt sie die „Normalisierung“. Während die Fehler im IT-System ausgemerzt wurden, führte die Fabrik ein manuelles Lieferkettensystem ein. Initiativen der Mitarbeiter sollten Stress abbauen. Als die Führungskräfte häufiger in die Produktionshallen kamen, wurde auch die Kommunikation besser. Hinzu kam ein Plan zur deutlichen Reduzierung von Ausschuss.
Wir haben gesagt, wir wollen unsere Wände nicht mit Farbe anstreichen, sondern mit Verbesserungsvorschlägen tapezieren.
Ajay Naik, Geschäftsleiter und Country Manager SKF Schweden
„Wir wollten berechenbar und wirklich zuverlässig werden“, sagt Naik. „Klar war auch, dass wir gewaltige Kosten hatten und deswegen nicht wettbewerbsfähig sein konnten. Die Krise konnten wir meistern, aber mit unseren geringen Gewinnmargen würden wir nie rentabel sein.“
Im Juni 2019 begann die Etappe der Leistungssteigerung. Naik organisierte Workshops, in denen die Mitarbeiter darin geschult wurden, unnötige Kosten zu vermeiden. Die Werksleitung schloss sich mit den Gewerkschaftsvertretungen zusammen, um das Schichtsystem in wirtschaftlichen Hoch- und Tiefphasen flexibler zu gestalten. Mitarbeiter, die aufgrund von automatisierten Prozessen nicht mehr gebraucht wurden, erhielten eine Umschulung oder Fortbildung.
Arbeiten nach dem Kaizen-Konzept
Naik führte eine Strategie nach dem Kaizen-Konzept ein. Bei dieser japanischen Arbeitsphilosophie kooperieren Mitarbeiter aller Ebenen, um den Produktionsprozess schrittweise zu verbessern. Jeden Monat wählen die Gewerkschaftsvertretungen und das Personal von SKF Göteborg den besten „Kaizer” aus. An den Wänden der Fabrik hängen inzwischen mehr als 5.000 Verbesserungsvorschläge, die seit der Einführung des Konzepts umgesetzt worden sind.
„Wir haben gesagt, wir wollen unsere Wände nicht mit Farbe anstreichen, sondern sie mit Verbesserungsvorschlägen tapezieren“, erklärt Naik. „Jede Wand ist wie diese. So kann jeder die Beiträge unserer Mitarbeiter sehen und anerkennen.“
Erste Ergebnisse
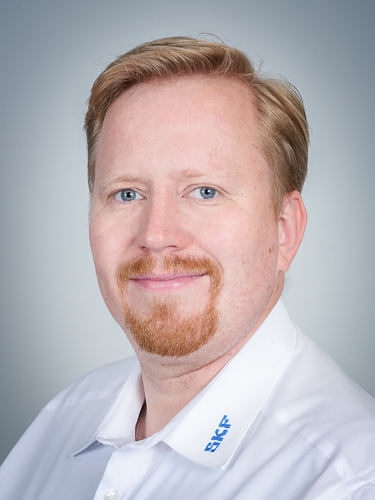
Bis Dezember 2020 waren alle unnötigen Kosten beseitigt und die Umsatzrendite des Werks deutlich verbessert. Als Naik die EQL-Auszeichnung erhielt, begründete die Europäische Organisation für Qualität ihre Wahl mit Naiks „außerordentlichem Einsatz“ bei der Umwandlung von SKF Göteborg zu einer der drei effizientesten Fabriken Europas durch seine „konsequente und engagierte Führung, unterstützt durch ein hoch motiviertes Personal und Team“.
Naiks Erfolg in Göteborg war umso bemerkenswerter, als die SKF Fabrik eine der ersten war, die eine Reihe neuer Technologien eingeführten“, analysiert Nikki Homes, Leiter der Future Factory von SKF.
„Naik hat einige Investitionen in erstklassige Fertigungskanäle getätigt und muss gleichzeitig die Herausforderungen der Umsetzung neuer Technologien im IT-Bereich und bei der Automation meistern“, erklärt Homes. „Das Göteborger Werk hat diese neuen Technologien sehr schnell angenommen und ist trotz gelegentlicher Schwierigkeiten offen für weitere Entwicklungen.“
Erste Ergebnisse
Bis Dezember 2020 waren alle unnötigen Kosten beseitigt und die Umsatzrendite des Werks deutlich verbessert. Als Naik die EQL-Auszeichnung erhielt, begründete die Europäische Organisation für Qualität ihre Wahl mit Naiks „außerordentlichem Einsatz“ bei der Umwandlung von SKF Göteborg zu einer der drei effizientesten Fabriken Europas durch seine „konsequente und engagierte Führung, unterstützt durch ein hoch motiviertes Personal und Team“.
Naiks Erfolg in Göteborg war umso bemerkenswerter, als die SKF Fabrik eine der ersten war, die eine Reihe neuer Technologien eingeführten“, analysiert Nikki Homes, Leiter der Future Factory von SKF.
„Naik hat einige Investitionen in erstklassige Fertigungskanäle getätigt und muss gleichzeitig die Herausforderungen der Umsetzung neuer Technologien im IT-Bereich und bei der Automation meistern“, erklärt Homes. „Das Göteborger Werk hat diese neuen Technologien sehr schnell angenommen und ist trotz gelegentlicher Schwierigkeiten offen für weitere Entwicklungen.“
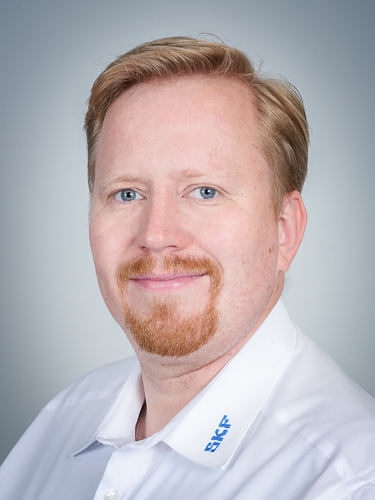
Digitale Transformation bei SKF weltweit
Homes ist für die Lean Transformation und Digitalisierung der nahezu 100 SKF Werke weltweit verantwortlich. Die anstehenden Veränderungen umfassen viele neue Technologien und Prozesse, für die das Göteborger Werk und andere führende Fabriken in verschiedenen Teilen der Welt Vorreiter waren. Ziel ist es, ähnliche Ergebnisse zu erzielen.
Im Mittelpunkt der digitalen Transformation steht die Verpflichtung, das richtige Gleichgewicht zwischen Technologie, Prozess und Menschen zu finden. Nur wenn das gelingt, wird SKF in der Lage sein, die potenzielle Kraft von Daten für die Verbesserung seiner Prozesse auszuschöpfen, betont Homes. Dafür sei eine Sensibilisierung in sämtlichen Bereichen des Unternehmens erforderlich, damit alle Beteiligten offen für Veränderungen sind, die Prozesse optimieren und standardisieren und die für SKF richtige Technologie zum Einsatz bringen.
„Nachdem die geschäftlichen Erfordernisse definiert sind, besteht der erste Schritt darin, die Technologie zu ermitteln, die für uns am besten geeignet ist“, fährt Homes fort. „Anschließend geht es darum, diese Technologie so umzusetzen, dass sie unsere Prozesse und unsere Mitarbeiter, die diese Prozesse durchführen, unterstützt.“
Eine Technologie, die SKF Prozesse rasch verbessert, ist die hyperkonvergente Infrastruktur (hyper-converged Infrastructure) oder HCI. Sie ermöglicht es, die Vorteile der Cloud-Technologie und der werksinternen Rechnerleistung zu nutzen. Berechnungen, die in der Fabrik in Echtzeit benötigt werden, können sofort intern vorgenommen werden. Komplexere Aufgaben hingegen werden über die Cloud abgewickelt, wo bei Bedarf mehr Rechenkapazität zur Verfügung steht.
Verbesserter Schleifprozess
Homes nennt das Präzisionsschleifen als Beispiel. Ein Messgerät berechnet die Ergebnisse des Schleifprozesses mithilfe eines Algorithmus, verdeutlicht er. Es erkennt ein Verbesserungspotenzial und liefert dieses Feedback an die Schleifmaschine, damit Anpassungen zur weiteren Erhöhung der Produktqualität vorgenommen werden können.
„Wir haben schon seit vielen Jahren die Möglichkeit, mit statischen Algorithmen zu messen und zu reagieren“, so Homes. „Mit HCI sind wir heute in der Lage, kontinuierlich Daten vom aktuellen Fertigungsprozess in die Cloud einzuspeisen und unsere maschinellen Lernverfahren immer wieder dynamisch zu trainieren, um noch genauere Einstellungen zu ermöglichen.“
Die Digitalisierung ist ein Wegbereiter für eine optimierte Fertigung. Homes bezeichnet die Lean Transformation in den SKF Fabriken jedoch als die Grundlage der gesamten digitalen Transformation. Sein Team berät und unterstützt die Fabriken, bis die richtigen Bedingungen für eine Zertifizierung erreicht sind.
„Zuerst müssen wir unsere Prozesse verbessern und standardisieren“, so Homes. „Dann können wir die Digitalisierung in Angriff nehmen. Ansonsten besteht die Gefahr, dass wir einen Prozess digitalisieren, der immer noch überflüssige Elemente enthält. Das würde Lösungen komplizierter und weniger effizient machen.
Transformation ist ein laufender Prozess
„Ajay und sein Team in Göteborg gingen nach dieser strukturierten Methode vor. Alle Bereiche der Fabrik wurden nach dem SKF Produktionssystem zertifiziert. Die Veränderungen wurden in enger Zusammenarbeit mit dem gesamten Fertigungspersonal durchgeführt. All dies hat zu den großartigen Errungenschaften der letzten Jahre in Göteborg beigetragen.“
Naik will sich jedoch nicht auf seinen Lorbeeren ausruhen, er sucht nach neuen Verbesserungsmöglichkeiten, mit denen er seine Kaizen-Wand dekorieren kann. Eine Fabrik auf Veränderungen vorzubereiten, insbesondere in digitaler Hinsicht, sei ein fortlaufender Prozess, der mit der technologischen Entwicklung fortschreite, betont er.
„Wir streben eine wirklich kundenorientierte Organisation an. Deshalb müssen wir laut Plan nicht nur Kosten senken, sondern auch Mehrwert schaffen“, erklärt Naik. „Das bedeutet für die Zukunft mehr Fokus auf das Beschaffungsmanagement und die Weiterentwicklung unserer Digitalisierungskompetenz. Das heißt auch noch mehr Change Agents und eine weitere Stärkung unserer Kultur der Rechenschaftspflicht. Das ist unser Weg.“