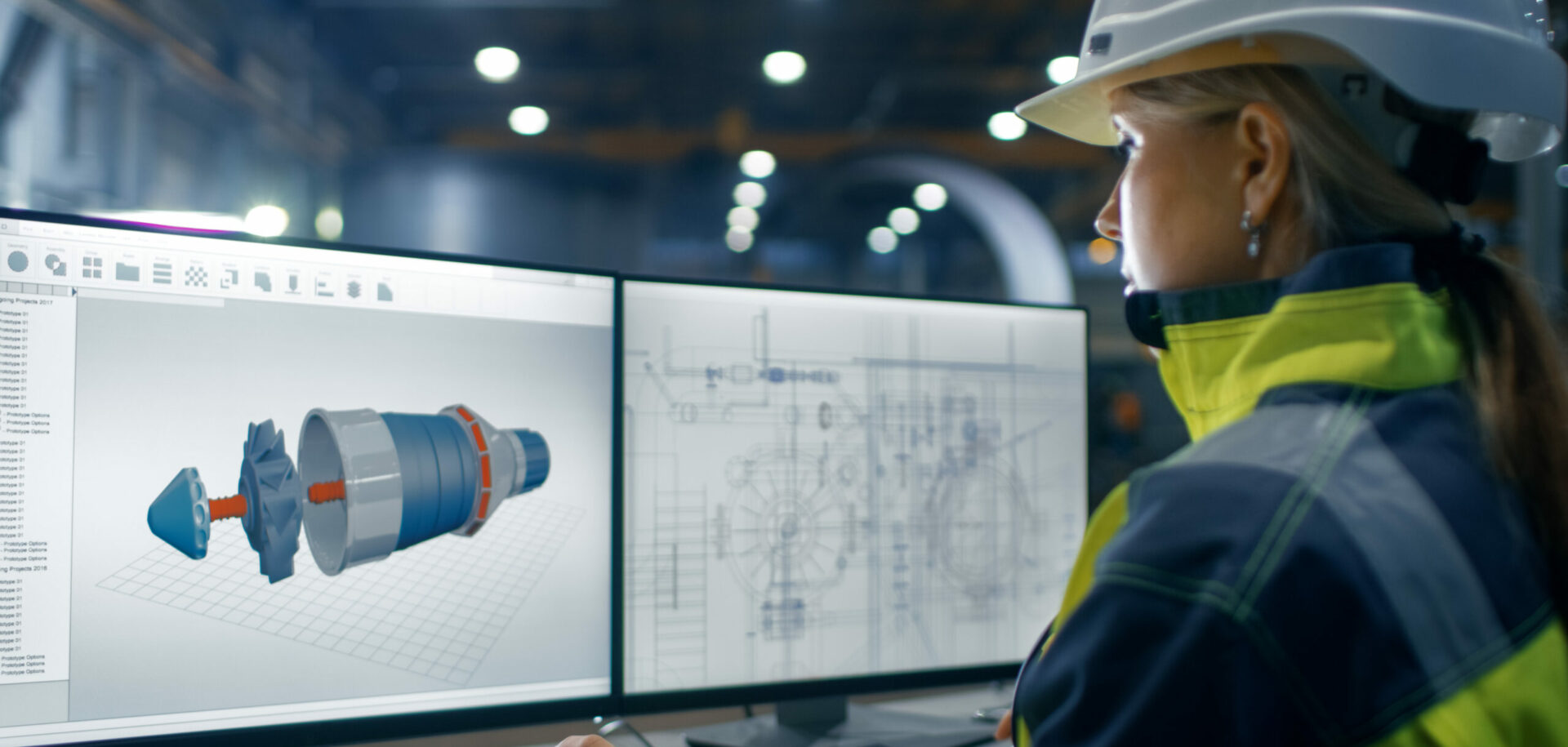
Die Vorteile der Rekonditionierung von Wälzlagern
Kosten-Nutzen-Analysen haben gezeigt, dass durch die Rekonditionierung von Wälzlagern im Vergleich zum Neukauf Einsparungspotentiale von 50 bis 80 Prozent erzielt werden können – je nach Größe, Komplexität, Zustand, Preis etc. des jeweiligen Lagers. Darüber hinaus kann durch das Rekonditionieren gebrauchter Wälzlager der CO2-Ausstoß gesenkt werden. So ergeben 100 kg rekonditionierte Wälzlager eine Verringerung von etwa 350 kg CO2.
Zusammenfassung
Seit Jahrzehnten ist es in kommerziellen und industriellen Anwendungen üblich, dass Wälzlager bei Wartungsarbeiten oder Revisionen ausgebaut, rekonditioniert und dann wieder eingebaut werden. Der bei der Rekonditionierung von Wälzlagern oder Lagerelementen erzielte Nutzen kann bewertet werden. So ergeben sich durch das Rekonditionieren von Wälzlagern viele Kostenvorteile. Die dabei erzielten Einsparungen können je nach Zustand, Größe etc. des jeweiligen Lagers bei 50 bis 80 Prozent liegen. Darüber hinaus wird durch die Rekonditionierung eine starke nachhaltige Wirkung erreicht: 100 kg rekonditionierte Wälzlager senken den CO2-Ausstoß um etwa 350 kg. Über eine algebraische Beziehung kann die Lebensdauer L10 von Lagerlaufbahnen durch den partiellen Abtrag des beanspruchten oberflächennahen Materials bestimmt werden, und zwar als Funktion der Tiefe z bei der Überarbeitung und Instandsetzung. Der Lebensdauerfaktor LF eines rekonditionierten Wälzlagers kann je nach Rekonditionierungsumfang im Bereich von 0,87 bis 0,99 der Lebensdauer eines neuen Wälzlagers liegen.
Ansprechpartner Verkauf
Heike Sengstschmid, heike.sengstschmid@skf.com
Durch das Rekonditionieren von Wälzlagern können Unternehmen Stillstandszeiten verkürzen, Kosten einsparen, Verschrottung vermeiden und die Nachhaltigkeit verbessern.
Wälzlager gehören zu den wichtigsten Bauteilen von Anlagen und müssen großen Belastungen standhalten. Normalerweise werden sie bei planmäßigen Wartungsarbeiten, kurz vor Ende ihrer Lebenszeit oder nach ungeplanten Ausfällen ersetzt. Je nach Lagerart kann ein solcher Austausch kostspielig sein und lange Vorlaufzeiten bedeuten. Außerdem kann sich die Verschrottung ausgedienter Lager negativ auf das Nachhaltigkeitsprofil eines Unternehmens auswirken; dieser Aspekt gewinnt für Investoren und Kunden immer mehr an Bedeutung. Wie gelingt es nun die Lebensdauer von Wälzlagern zu verlängern, um Stillstandszeiten zu verkürzen, Kosten einzusparen und Verschrottung zu vermeiden? Die Antwort hierauf lautet: Rekonditionierung (Bild 1 und 2).
Kosten-Nutzen-Analysen haben gezeigt, dass durch die Rekonditionierung von Wälzlagern im Vergleich zum Neukauf Einsparungspotentiale von 50 bis 80 Prozent erzielt werden können – je nach Größe, Komplexität, Zustand, Preis etc. des jeweiligen Lagers. Darüber hinaus kann durch das Rekonditionieren gebrauchter Wälzlager der CO2-Ausstoß gesenkt werden. So ergeben 100 kg rekonditionierte Wälzlager eine Verringerung von etwa 350 kg CO2.
In der Luftfahrtindustrie beispielsweise ist es üblich, dass Wälzlager, die bei der Wartung oder Revision ausgebaut werden, rekonditioniert werden. Danach kommen diese Lager wieder zum Einsatz [1], [2], [3].
Es wird die Notwendigkeit für die Herausgabe einer internationalen Norm (ISO) gesehen, um sicherzustellen, dass es festgelegte Verfahren und Vorgaben für die Rekonditionierung von Wälzlagern gibt. Zurzeit liegt nur eine nationale österreichische Norm vor [4], die 2011 veröffentlicht wurde.
Für die Rekonditionierung gebrauchter Wälzlager wurden fünf Klassen eingeführt.
Es ist möglich die Lebensdauer von rekonditionierten Wälzlagern zu beschreiben, und zwar unter Berücksichtigung der veränderten Geometrie und der Schubspannung τ (τ0, τu) durch den Abtrag von beanspruchtem Material bzw. den Austausch der Wälzkörper.
Lagerlebensdauer und Zuverlässigkeit
Im Allgemeinen ist ein Wälzlager nicht unbegrenzt einsatzbereit und funktionstüchtig, außer die Betriebsbedingungen sind ideal und die Ermüdungsgrenzbelastung ist noch nicht erreicht; allerdings tritt früher oder später eine Werkstoffermüdung ein [5].
Unter der Oberfläche beginnende Ermüdung
Die Lebensdauer eines Wälzlagers wird als ein Zeitraum betrachtet, der andauert, bis sich die ersten Anzeichen von Ermüdung zeigen. Die Lagerlebensdauer ist abhängig von der durchgeführten Anzahl Lagerumdrehungen und der Größe der Belastung [6 bis 9]. Ermüdung resultiert aus der Schubspannung, die zyklisch direkt unter der belasteten Oberfläche der Ringe und Wälzkörper auftritt (Bild 3 und Gleichung 1).
S Erlebenswahrscheinlichkeit [%]
N Anzahl der Lastzyklen
τ0 max. Orthogonal-Schubspannung [Pa]
τᵤ Ermüdungsgrenzspannung [Pa]
z0 Tiefe der maximalen Orthogonal-Schubspannung [m]
a Kontakt Halbachse in Querrichtung [m]
l Länge des Laufbahnkontakts [m]
e Weibull-Exponent
c, h Exponenten der Belastungs-Lebensdauer-Gleichung
Nach einer gewissen Zeit verursachen diese Belastungen Risse unter der Oberfläche, die sich nach und nach bis zur Oberfläche ausbreiten. Wenn die Wälzkörper über diese Risse rollen, lösen sich Werkstofffragmente. Dieser Vorgang ist als Schälung bekannt.
Weitere Ausfallarten
Durch den langfristigen Einsatz von Wälzlagern unter mangelhaften Bedingungen und bei nicht optimaler Montage sind viele andere Ausfallmodelle bekannt. Die Norm ISO 15243 [5] gibt einen guten Überblick über diese Ausfallarten, allerdings sollte diese Norm über Wälzlagerschäden und -ausfälle aufgrund jüngster Erkenntnisse rekonditioniert werden.
Mitte der 1950er Jahre schlug Arvid Palmgren, ein führender Theoretiker auf dem Gebiet Wälzlager, vor, Wälzlager nicht länger zu ersetzen, sondern zu reparieren. Er sagte: „Die mittlere Lebensdauer ist viel länger als die berechnete Lebensdauer, und bei Wälzlagern mit einer kürzeren Lebensdauer ist eigentlich nur das Teil zu reparieren, das zuerst beschädigt wurde.“
Das soll nicht heißen, dass ein Wälzlager, sobald Schälungen oder andere Schäden eintreten, nicht mehr verwendbar ist (Bild 4). Das Vorliegen eines Schadens kann mit einer Geräusch- und Schwingungsprüfung festgestellt werden. So wurden über Jahrzehnte Reparaturverfahren bei Wälzlagern durchgeführt, die eine Wiederherstellung der erwarteten Lebensdauer und Zuverlässigkeit der Lager ermöglichten.
Konsequenzen
Analysen und die bei der modernen Rekonditionierung gemachten Erfahrungen zeigen, dass rekonditionierte Wälzlager nahezu die Lebensdauer und Zuverlässigkeit von neuen Wälzlagern erreichen können. Die Berücksichtigung des Ausmaßes der Rekonditionierung, der Ergebnisse von Spannungsmessverfahren, wie XRD [10] (Bild 5), und der Ergebnisse von zerstörungsfreien Prüfverfahren, wie der Barkhausenrauschen-Analyse [11], dem mikromagnetischen Prüfverfahren (3M), der NEWS- [12] und RUSSAW-Spektroskopie sowie der Ultraschallprüfung mit Phased-Array-Technik ergibt die repräsentativen Lebensdauerfaktoren LF. Diese können im Bereich von 0,87 bis 0,99 der Lebensdauer eines neuen Wälzlagers liegen (Bild 6).
Klassifizierung der Rekonditionierungsarten von Wälzlagern
Die bei der Rekonditionierung von gebrauchten Wälzlagern verwendeten Begriffe und Definitionen werden wie folgt erläutert.
Je nach Grad der Vorbenutzung bzw. Abnutzung kann die Rekonditionierung von Wälzlagern in fünf Klassen eingeteilt werden (Bild 7).
Während die einzelnen Tätigkeiten in den jeweiligen Klassen nummeriert sind, ist die tatsächliche Abfolge der Tätigkeiten nicht an diese Nummerierung gebunden. Dabei müssen besondere Vereinbarungen zwischen dem Instandhaltungsbetrieb und dem Betreiber berücksichtigt werden.
Zwischen den einzelnen Tätigkeiten können werterhaltende Maßnahmen erforderlich sein. Beispielsweise, wenn eine Lagerlaufbahn durch eine unter der Oberfläche beginnende Ermüdung – siehe [5] – beschädigt ist, kommt sie für eine Überarbeitung nach Klasse III nicht in Frage. Wenn jedoch ein durch Verunreinigungen oder Schmutzteilchen entstandener Oberflächenschaden (an der Oberfläche beginnende Ermüdung) der Lagerlaufbahnen vorliegt, dann können diese oft durch Honen oder Schleifen wiederhergestellt werden.
Weitere Tätigkeiten
Bei der Instandsetzung (Klasse II) oder (Grund-)Überholung (Klasse III) werden reparierbare Lager zerlegt, die Komponenten optisch begutachtet und die Härte der Ringe wird gemessen. Bei den Komponenten, die als überarbeitbar beurteilt wurden, werden die Maße kontrolliert. Falls erforderlich, werden die Lagerstirnseiten, der Bohrungsdurchmesser und der äußere Durchmesser nachgeschliffen oder poliert, soweit die Toleranzen dies zulassen. Das Beschichten mit Nickel oder Chrom ist zulässig, um das Nachschleifen bzw. Nachpolieren der Oberflächen zu ermöglichen, damit die ursprünglich geplanten Maße wieder erreicht werden können.
Bei der Instandsetzung (Klasse II) erfolgt ein nennenswerter Materialabtrag, wobei Oberflächenschäden entfernt und die Spannungen des oberflächennahen Materials verändert werden. Die Oberflächengüte wird bis zu ihrer ursprünglich geplanten Spezifikation wiederhergestellt oder verbessert. Das Lager wird dann mit neuen Wälzkörpern, deren Durchmesser dem der ursprünglichen Wälzkörper plus der zweifachen Bearbeitungstiefe entspricht, ausgestattet, wenn dies aufgrund der Lagerluftbedingungen erforderlich sein sollte. Die neuen Wälzkörper müssen dieselbe Nenngröße aufweisen, aber ihre Größe muss ausreichend Lagerluft zulassen.
Käfige werden visuell auf Risse untersucht und ggf. neu beschichtet. Falls erforderlich, wird der Käfig durch einen neuen ersetzt. Normalerweise werden neue Wälzkörper in den Käfig eingesetzt, und das Lager wird wieder zusammengebaut.
Bei der (Grund-)Überholung (Klasse III) sind bei den Außenringlaufflächen größerer Wälzlager auch größere Schleiftiefen zulässig. Darüber hinaus können auch andere zerspanende Bearbeitungsverfahren (z. B. Hartdrehen) angewendet werden. Dabei werden Oberflächenschäden entfernt und die Spannungen des oberflächennahen Materials werden verändert. Die Oberflächengüte wird bis zu ihrer ursprünglich geplanten Spezifikation wiederhergestellt oder verbessert. Das Lager wird dann mit neuen Wälzkörpern, deren Durchmesser dem der ursprünglichen Wälzkörper plus der zweifachen Bearbeitungstiefe (je Ring) entspricht, ausgestattet. Bei Zylinderrollenlager wird sowohl die Rollenlänge als auch der Rollendurchmesser vergrößert. Gewöhnlich haben die neuen Wälzkörper dann einen größeren Nenndurchmesser als die ursprünglichen Wälzkörper. Diese starke Vergrößerung der Wälzkörper erfordert eventuell eine Überarbeitung der Käfigtaschen oder einen Austausch des Käfigs.
Aufgrund der genau festgelegten Verfahren und vorhandenen Einstufungen kann gewährleistet werden, dass bei der Rekonditionierung von Wälzlagern vorgeschriebene Normen erfüllt und Vergleiche zwischen den Servicebetrieben ermöglicht werden.
Klasse 0 – Befundung
Die Befundung von Wälzlagern beinhaltet die Inspektion bzw. Begutachtung gebrauchter (oder länger bevorrateter) Wälzlager und deren Vergleich mit Anforderungen gemäß Zeichnungen oder Spezifikationen.
Anmerkung: Üblicherweise wird eine Empfehlung zur weiteren Behandlung in der entsprechenden Rekonditionierungsklasse gegeben.
Klasse I – Wartung (Pflege)
Die Wartung von Wälzlagern umfasst alle Tätigkeiten der Befundung (Klasse 0) und folgende zusätzliche Tätigkeiten:
Klasse II – Instandsetzung
Die Instandsetzung von Wälzlagern umfasst alle Tätigkeiten der Befundung (Klasse 0) und Wartung (Klasse 1) sowie eine oder mehrere der folgenden Tätigkeiten:
Klasse III – (Grund-)Überholung
Die (Grund-)Überholung von Wälzlagern umfasst alle Tätigkeiten der Befundung (Klasse 0) und Wartung (Klasse 1) und ggf. Instandsetzung (Klasse II) sowie eine oder mehrere der folgenden Tätigkeiten:
19) Einbau von größeren Wälzkörpern mit größerem Nenndurchmesser (siehe Tätigkeit 13)
20) Einbau des ursprünglichen, ggf. nachgearbeiteten Käfigs oder erforderlichenfalls eines neuen Käfigs (siehe Tätigkeit 14)
Klasse IV – Reparatur; Aufarbeitung
Die Reparatur bzw. Aufarbeitung von Wälzlagern umfasst die Tätigkeiten der Klassen I bis III und die folgende zusätzliche Tätigkeit:
Weltweite Verfügbarkeit
SKF unterhält ein globales Netzwerk von erstklassig ausgestatteten Servicezentren, in denen die gebrauchten Wälzlager ihrer Kunden auf höchstem technischem Niveau rekonditioniert werden. Als Geschäftsbereich von SKF, einem weltweit führenden Wälzlagerhersteller, blickt SKF Remanufacturing Services auf mehr als 100 Jahre Erfahrung und Kompetenz auf dem Gebiet rotierender Maschinen zurück.
SKF verwendet bei der Rekonditionierung gebrauchter Wälzlager die gleichen hochwertigen Werkstoffe, Verfahren und Maschinen, die auch bei der Erstfertigung zum Einsatz kommen. So kann ein Kunde, egal, wo in der Welt er seinen Standort hat, darauf vertrauen, dass seine Wälzlager und die dazugehörigen Komponenten, wie beispielsweise Gehäuse, in allen SKF Servicezentren mit den gleichen Qualitätsmaßstäben, Arbeitabläufen und dem gleichen Know-how bearbeitet werden. Folgende Vorteile können sich durch die Zusammenarbeit mit SKF Remanufacturing Services ergeben:
-
Verlängerung der Lagerlebensdauer
-
Senkung der Lebenszykluskosten
-
Reduzierung des Umwelteinflusses dank Wälzlager-Recycling
-
Längerfristiger Erhalt des Ersatzteillagers
-
Verbesserung der gesamten Anlagenzuverlässigkeit
-
Informationen über die Optimierung der Zuverlässigkeit der jeweiligen Anwendung
Bei gleichzeitiger Nutzung der SKF Programme zur vorausschauenden Wartung können Kunden sämtliche Vorteile ausschöpfen, die sich durch das Rekonditionierungsprogramm erzielen lassen.
Literatur
[1] Zaretsky, E.V.; Branzai, E.V.: NASA TM-2005-212966; Effect of rolling bearing refurbishment and restoration on bearing life and reliability. (2005)
[2] Zaretsky, E.V.; Branzai, E.V.: NASA TP-2007-214463, Model specification for rework of aircraft engine, poser transmission, and accessory/auxillary ball and roller bearings. (2007)
[3] Optimize your assets with SKF Remanufacturing Services. SKF Publication 6697 EN, July 2008
[4] ÖNORM M 6328 :2011 Wälzlager – Überarbeitung gebrauchter Wälzlager (Rolling bearings – Reworking of used rolling bearings).
[5] ISO 15243:2004, Rolling bearings – Damage and failures – Terms, characteristics and causes
[6] Lundberg, G.; Palmgren, A.: Dynamic capacity of rolling bearings. Acta Politecnica. Mechanical Engineering Series. Royal Swedish Academy of Engineering Sciences, Vol.1, No3, 7, (1947)
[7] Lundberg, G.; Palmgren A.: Dynamic capacity of roller bearings. Acta Politecnica. Mechanical Engineering Series. Royal Swedish Academy of Engineering Sciences, Vol.2, No4, 96, (1952)
[8] Ioannides, E.; Bergling, G.; Gabelli, A.: An analytical formulation for the life of rolling bearings.
Acta Polytechnica Scandinavica. Mechanical Engineering Series No. 137. Espoo 1999
[9] ISO 281:2007, Rolling bearings – Dynamic load ratings and rating life
[10] Voskamp, A.P.: Material response to rolling contact loading. Trans. Am. Soc. Mech. Engineers, J.Tribology 107 (1985) 359
[11] Zika, T.; Schimpelsberger, B.; Kern, A.: Barkhausen-Noise – A possibility for non-destructive grinding burns (TROOSTITE) and residual stress testing. Science Report 2006-2007, SKF Österreich AG, AT 0802 EN. (2008)
[12] Andersson, B.E.; Griffa, M.; Le Bas, P-Y.; Ulrich, T.J.; Johnson, P.A.: Experimental implementation of reverse time