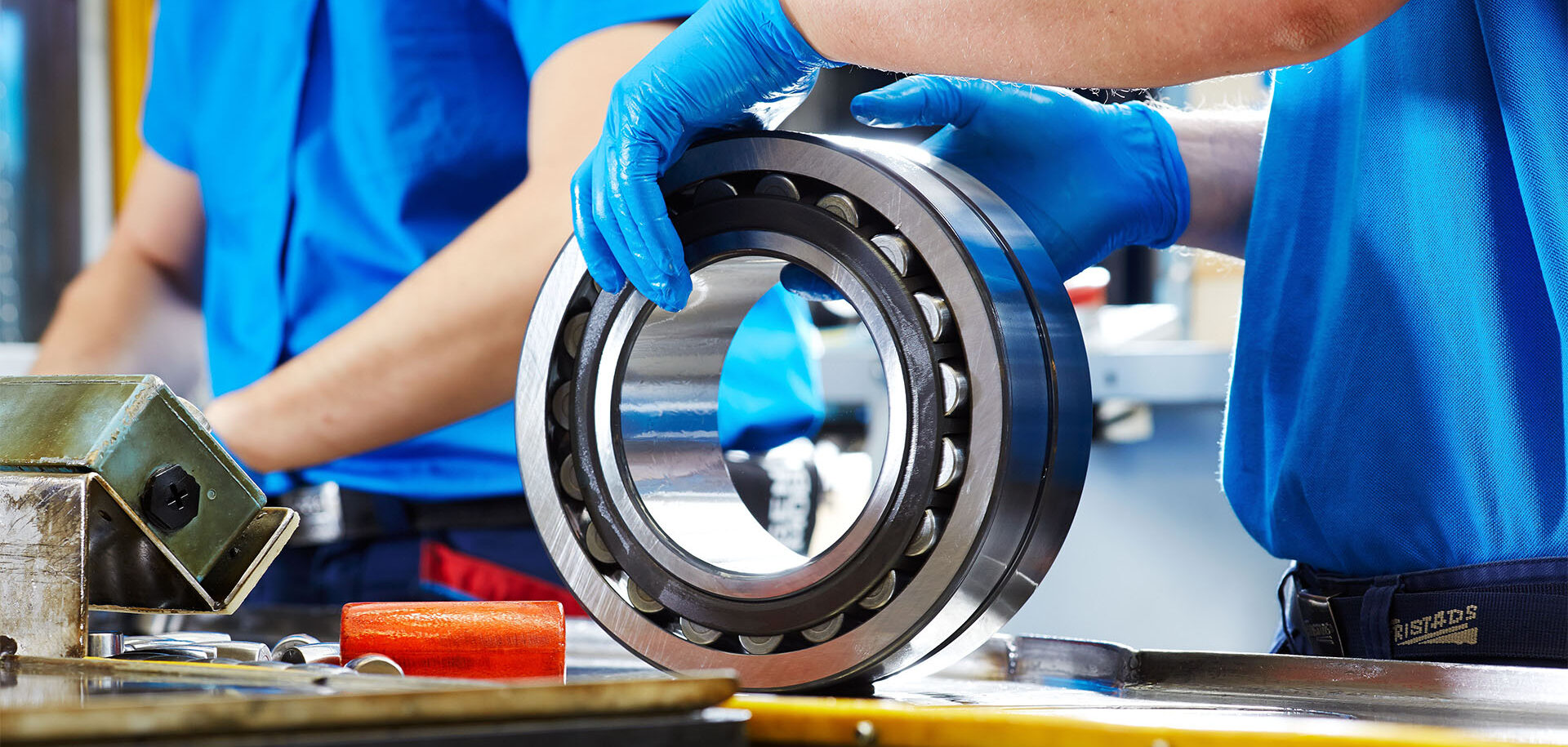
El futuro lean y digital de la fabricación en SKF
Cuando Ajay Naik se trasladó a Suecia desde la India en 2017 para dirigir la fábrica de SKF en Gotemburgo, la planta se enfrentaba a múltiples desafíos. Aquí explicamos cómo él y su equipo transformaron los problemas en éxitos.
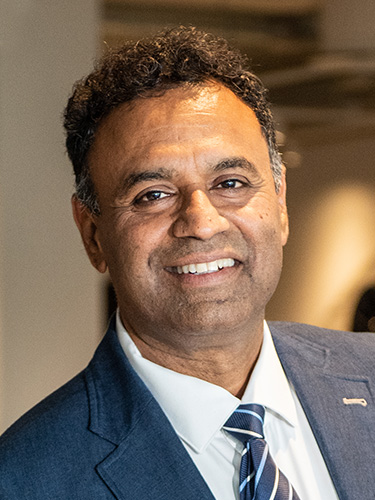
En 2017, cuando todavía estaba inmersa en una revisión exhaustiva de sus sistemas informáticos, la fábrica de SKF en Gotemburgo debía responder a un auge sin precedentes de la demanda mundial. En verano, los pedidos se acumulaban y la falta de personal había precipitado una búsqueda urgente de personal temporal.
“No estábamos preparados”, admite Ajay Naik, director general y director nacional de SKF Suecia. “Nuestros recursos eran suficientes para trabajar en condiciones normales, con incrementos progresivos de la demanda. Pero la explosiva expansión del mercado nos encontró todavía trabajando en la resolución de problemas internos”.
Con 30 años en SKF en la India, Naik aportaba experiencia en la superación de problemas en los procesos de fabricación. Y fruto de esta experiencia, cuando llegó a Suecia en 2017, contrató a un gestor de crisis, nombró a un experto en cadenas de suministro y creó una sala de crisis en un intento de estabilizar la situación. A finales de 2017, lo peor había pasado, y se dio paso a un período de transformación que consolidaría la fábrica de SKF en Gotemburgo como líder mundial en rentabilidad. En 2021, en reconocimiento a sus logros, la Organización Europea para la Calidad concedió a Naik el premio European Quality Leader (EQL).
“No estábamos preparados”, admite Ajay Naik, director general y director nacional de SKF Suecia. “Nuestros recursos eran suficientes para trabajar en condiciones normales, con incrementos progresivos de la demanda. Pero la explosiva expansión del mercado nos encontró todavía trabajando en la resolución de problemas internos”.
Con 30 años en SKF en la India, Naik aportaba experiencia en la superación de problemas en los procesos de fabricación. Y fruto de esta experiencia, cuando llegó a Suecia en 2017, contrató a un gestor de crisis, nombró a un experto en cadenas de suministro y creó una sala de crisis en un intento de estabilizar la situación. A finales de 2017, lo peor había pasado, y se dio paso a un período de transformación que consolidaría la fábrica de SKF en Gotemburgo como líder mundial en rentabilidad. En 2021, en reconocimiento a sus logros, la Organización Europea para la Calidad concedió a Naik el premio European Quality Leader (EQL).
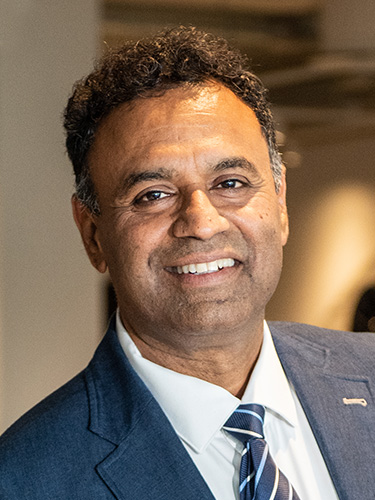
Varias medidas como primer paso de la transformación
La primera fase de la transformación comenzó en enero de 2018 y continuó hasta el verano de 2019, un período que Naik califica de “normalización”. Mientras depuraba las fallas del sistema informático, la fábrica introdujo un sistema de cadena de suministro manual. Se implementaron iniciativas propuestas por los propios empleados para mitigar el estrés. Los directivos dedicaron más tiempo a apoyar a los trabajadores en la zona de producción. Mejoró la comunicación y se puso en marcha un plan para reducir significativamente el desaprovechamiento de material.
Dijimos que no pintaríamos nuestras paredes con colores, sino que pintaríamos nuestro mundo con mejoras
Ajay Naik, director general y director nacional de SKF Suecia
“Queríamos ser previsibles y confiables de verdad”, explica Naik. “También sabíamos que nuestros costos estaban desorbitados y que así era imposible ser competitivos. Podríamos salir de la crisis, pero nunca seríamos rentables con unos márgenes tan estrechos”.
En junio de 2019, se inició el período de racionalización. Naik creó talleres para enseñar a los equipos cómo reducir costos innecesarios. La gerencia dialogó con los sindicatos para flexibilizar la programación de turnos durante los altibajos del ciclo económico. En el caso de aquellas funciones que desaparecerían con la automatización, se ofreció a los empleados cursos de capacitación para poder desempeñar funciones nuevas.
Implementación del método Kaizen
Naik introdujo una estrategia Kaizen, un método desarrollado primero en Japón en el que los empleados colaboran en la mejora progresiva de un proceso de fabricación. Cada mes, los sindicatos y los empleados eligen la mejor iniciativa y se exponen, en las paredes de SKF en Gotemburgo, más de 5000 mejoras ejecutadas desde la puesta en marcha de la estrategia.
“Dijimos que no pintaríamos nuestras paredes con colores, sino que pintaríamos nuestro mundo con mejoras”, afirma Naik. “En todas las paredes, se pueden ver logros conseguidos gracias a los aportes de nuestros empleados”.
Los resultados comienzan a verse
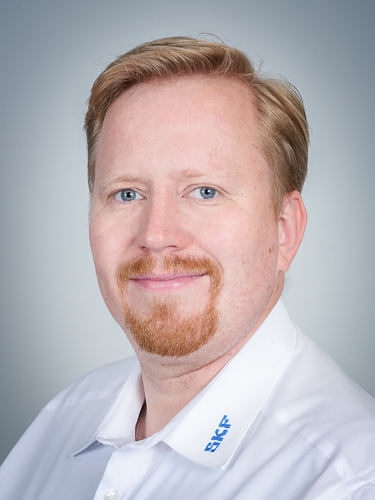
En diciembre de 2020, los costos innecesarios se habían reducido al mínimo y los márgenes operativos de la planta habían mejorado considerablemente. Al entregar el premio EQL a Naik, la Organización Europea para la Calidad destacó sus “logros sobresalientes” en la transformación de la planta de SKF en Gotemburgo, hasta convertirla en una de las tres fábricas más productivas de Europa, gracias a su “liderazgo consecuente y comprometido, al que se suma una fuerza laboral comprometida”.
El éxito de Naik en Gotemburgo fue aún más notable por el hecho de que la fábrica de SKF fue una de las primeras en incorporar varias tecnologías nuevas, afirma Niki Homes, gerente de la Fábrica del Futuro de SKF.
“Naik tiene en marcha una serie de inversiones en canales de fabricación de primera clase. Al mismo tiempo, afronta el desafío de gestionar tecnologías nuevas tanto de datos como de automatización”, continúa. “La fábrica de Gotemburgo asimiló estas tecnologías nuevas en muy poco tiempo y está abierta a seguir desarrollándolas, a pesar de los obstáculos que pueda haber en el camino”.
Los resultados comienzan a verse
En diciembre de 2020, los costos innecesarios se habían reducido al mínimo y los márgenes operativos de la planta habían mejorado considerablemente. Al entregar el premio EQL a Naik, la Organización Europea para la Calidad destacó sus “logros sobresalientes” en la transformación de la planta de SKF en Gotemburgo, hasta convertirla en una de las tres fábricas más productivas de Europa, gracias a su “liderazgo consecuente y comprometido, al que se suma una fuerza laboral comprometida”.
El éxito de Naik en Gotemburgo fue aún más notable por el hecho de que la fábrica de SKF fue una de las primeras en incorporar varias tecnologías nuevas, afirma Niki Homes, gerente de la Fábrica del Futuro de SKF.
“Naik tiene en marcha una serie de inversiones en canales de fabricación de primera clase. Al mismo tiempo, afronta el desafío de gestionar tecnologías nuevas tanto de datos como de automatización”, continúa. “La fábrica de Gotemburgo asimiló estas tecnologías nuevas en muy poco tiempo y está abierta a seguir desarrollándolas, a pesar de los obstáculos que pueda haber en el camino”.
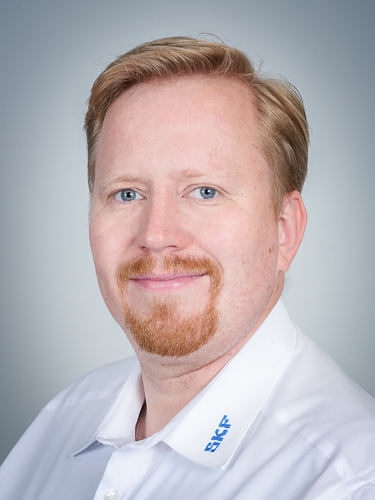
Transformación digital en SKF alrededor del mundo
Homes es responsable de dirigir la transformación de las casi 100 fábricas de SKF en todo el mundo hacia un entorno lean y digital. Para ello, será necesario incorporar muchas de las tecnologías y procesos nuevos implementados en Gotemburgo y en otras fábricas líderes de todo el mundo, con el objetivo de conseguir resultados similares.
Esta transformación digital se impulsa desde la voluntad de encontrar el equilibrio entre tecnología, procesos y personas. El equilibrio entre los tres pilares es fundamental para liberar el poder de los datos y así mejorar los procesos, afirma Homes. Implica un esfuerzo de concientización a todos los niveles de la empresa para que todos estén dispuestos a abrazar el cambio, optimizar y estandarizar los procesos, y seleccionar la tecnología que mejor se adapte a las necesidades de SKF.
“Una vez definidas las necesidades del negocio, el primer paso ha sido identificar la tecnología más adecuada”, continúa. “Después, se trata de decidir cómo incorporar las tecnologías que ofrezcan el mejor soporte para nuestros procesos y para la gente que los ejecute”.
Una tecnología clave que está mejorando rápidamente los procesos de SKF es la Infraestructura Hiperconvergente, o HCI, por sus siglas en inglés. La HCI permite a los equipos beneficiarse tanto de la tecnología en la nube como de la potencia de cálculo propia instalada. Los cálculos que deban ejecutarse en tiempo real dentro de la propia fábrica podrán realizarse inmediatamente. En cambio, las tareas más complejas se desarrollarán desde la nube, donde podrán aprovechar su mayor potencia de cálculo, si es necesario.
Mejorar el proceso de rectificación
Como ejemplo, Homes señala la rectificación de precisión. Una máquina de medir utiliza un algoritmo para calcular los resultados del proceso de rectificación. Detecta el potencial de mejora y envía la información a la máquina para que realice los ajustes necesarios a fin de mejorar la calidad del producto.
“Desde hace muchos años, tenemos la posibilidad de medir y reaccionar a través de algoritmos estáticos”, afirma. “Hoy, la HCI nos permite recopilar datos continuamente desde el proceso de fabricación en vivo y enviarlos a la nube. De este modo, nuestros algoritmos de aprendizaje automático evolucionan de manera continua y dinámica para realizar ajustes más precisos”.
La digitalización es uno de los elementos que facilitan el camino hacia la fabricación de primera clase. Sin embargo, continúa Homes, la base sobre la cual se construirá la transformación digital es la transformación lean de las fábricas de SKF. Su equipo orienta y apoya a las fábricas hasta que reciben la certificación cuando cumplen las condiciones exigidas.
“Primero debemos mejorar y estandarizar nuestros procesos”, afirma Homes. “Después empezaremos con la digitalización. De lo contrario, corremos el riesgo de digitalizar un proceso que aún contiene elementos redundantes, lo que haría que la solución fuera más compleja y menos eficaz”.
La transformación es un proceso continuo
“Ajay y su equipo en Gotemburgo aplicaron este método estructurado: todas las áreas de la fábrica han recibido la certificación conforme al sistema de producción de SKF y han colaborado estrechamente con todos los trabajadores de producción para hacer realidad esta transformación. Todo lo logrado por la fábrica de Gotemburgo en los últimos años debe mucho a este trabajo conjunto”.
Naik apenas se ha tomado un respiro en su búsqueda de nuevas mejoras para decorar su pared Kaizen. Preparar la fábrica para el cambio, sobre todo desde el punto de vista digital, es un proceso continuo que debe evolucionar paralelamente al desarrollo tecnológico, dice.
“Queremos construir una organización verdaderamente centrada en el cliente. Para ello, debemos continuar con nuestra hoja de ruta, no solo para eliminar costos sino también para aportar valor”, explica. “Implica un enfoque más intenso en la gestión del aprovisionamiento y en el desarrollo de competencias futuras en nuestro viaje digital. Potenciaremos la acción de nuestros agentes de cambio y nuestra cultura de transparencia. Es el camino que hemos elegido”.