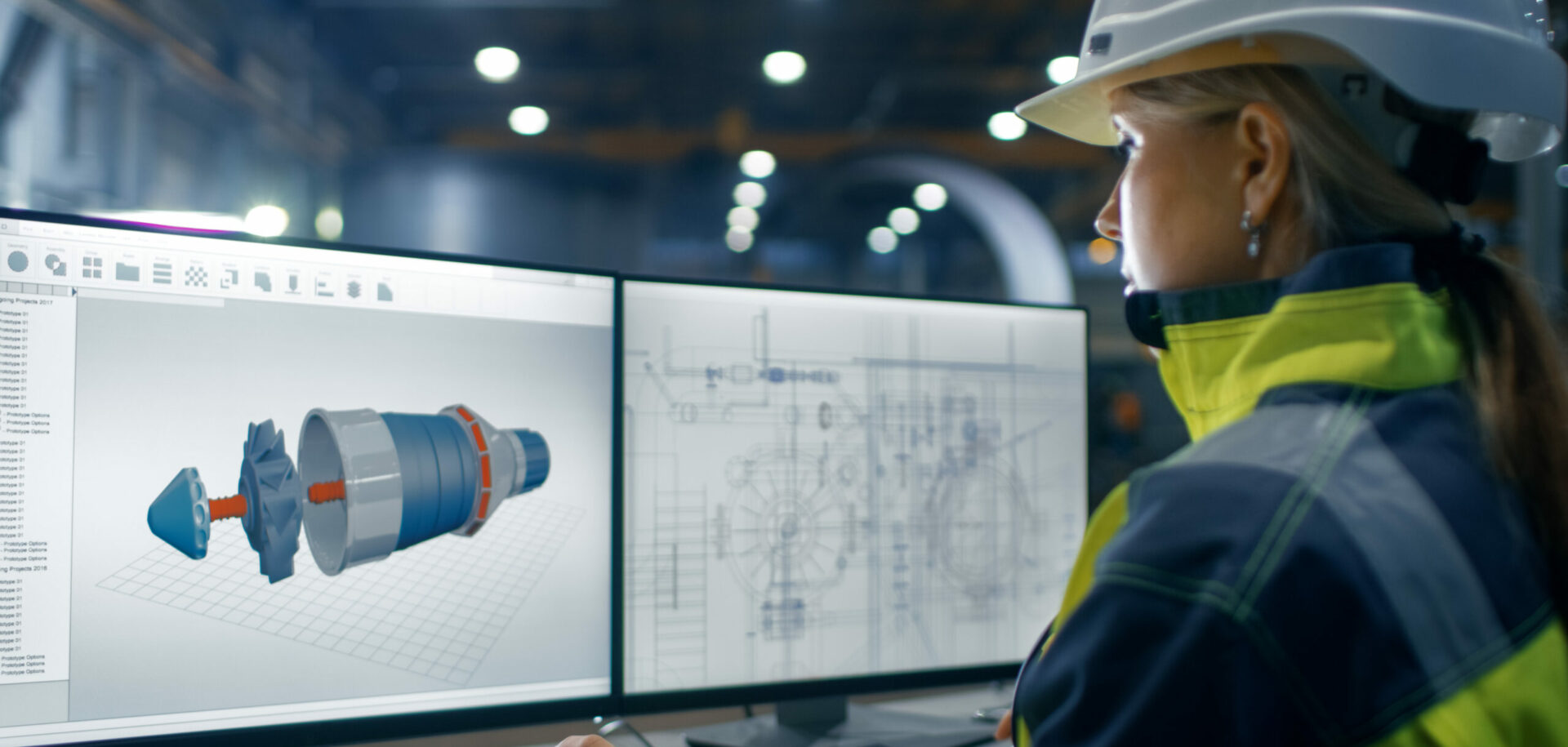
Energieeffiziente Minimalmengenschmierung von Hochgeschwindigkeitsspindeln
Die Versorgung mit präzise dosierten Minimalmengen eines geeigneten Schmierstoffs ist eine der wichtigsten Grundvoraussetzungen für den optimalen Betrieb und die lange Lebensdauer von Hochgenauigkeitslagern. Dies veranlasste SKF dazu, ein innovatives Öl-Mikrodosiersystem zu entwickeln.
Zusammenfassung
Das SKF Mikrodosiersystem stellt eine eindeutige Verbesserung gegenüber der Öl-Luft-Schmierung dar und erfüllt die gestiegenen Anforderungen der Hersteller von Werkzeugmaschinen nach höherer Effizienz, längerer Lebensdauer und geringerem Energieverbrauch. Bis zu vier Schmierstellen können von diesem System individuell mit Öl versorgt werden. Dabei kann der fast kontinuierliche Volumenstrom bei konstanter Qualitätsüberwachung für jede Schmierstelle einzeln im Bereich von 0,5 bis 5 mm³/min hochpräzise eingestellt werden.
Links
Ansprechpartner Verkauf
Dietmar Seidel, Dietmar.Seidel@skf.com
Für den optimalen Betrieb von Lagern von Präzisionsspindeln, die mit hohen Drehzahlkennwerten von mehr als 2 Mio. n×dm laufen (dies entspricht mehr als 30.000 min-1 bei herkömmlichen Werkzeugspindeln), ist eine zuverlässige und äußerst gleichmäßige Versorgung mit präzise dosierten Schmierstoffmengen unerlässlich. Innerhalb des optimalen Mengenbereichs ist das Reibungsmoment in den Lagern so gering wie möglich, ohne dass es zu einer Mischreibung mit nachfolgendem erhöhtem Verschleiß kommt (Bild 1).
Insbesondere bei hohen Drehzahlkennwerten werden neben den mit lebensdauergeschmierten Lagern ausgerüsteten Spindelsystemen normalerweise Nachschmiereinrichtungen verwendet. Bei diesen Systemen wird den Lagern eine nach Lagerungsart, Lagertyp, Lasten und Betriebsbedingungen angemessene Schmierstoffmenge in bestimmten Zeitabständen zugeführt. Kürzere Schmierintervalle und kleinere Schmierstoffmengen sorgen für einen kontinuierlicheren und zuverlässigeren Schmierzyklus.
Aktuelles Problem
Die Öl-Luft-Schmierung ist bei Spindeln weitverbreitet. Dabei werden den Lagern bestimmte Ölmengen über kontinuierlich mit Druckluft beaufschlagte Zuleitungen zugeführt. Der Luftstrom transportiert den Schmierstoff und verteilt auch die geringen Ölmengen in einem Ölstrahl, wodurch sich eine gleichmäßigere Schmierstoffzuführung ergibt (Bild 2). Der Luftdurchsatz und die Zeiteinstellung zur Erzeugung der Ölmenge können an die jeweilige Schmieraufgabe und Anwendung angepasst werden, weshalb solche Systeme sehr flexibel einsetzbar sind.
Allerdings haben sie auch verschiedene Nachteile. Dazu zählen lange Reaktionszeiten auf geänderte Dosiermengen und Zeiteinstellungen, eine unzureichende Dosiergenauigkeit und ein (unabhängig von der Zeiteinstellung) kontinuierlich höherer Druckluftverbrauch, wobei die Überwachung des Schmierstoff-Volumenstroms normalerweise lediglich auf Vergleichsbasis erfolgt.
Die Lösung
SKF hat ein neues Schmiersystem – das SKF Mikrodosiersystem – entwickelt, um die Unzulänglichkeiten der Öl-Luft-Schmierung auszugleichen und den gestiegenen Anforderungen der Hersteller von Werkzeugmaschinen nach größerer Effizienz, längerer Lebensdauer und niedrigerem Energieverbrauch gerecht zu werden. Das System erzeugt unter ständiger Qualitätsüberwachung vier hochpräzise dosierte, fast kontinuierliche Volumenströme im Bereich von 0,5 bis 5 mm3/min. Dies entspricht einem Hundertstel bis zu einem Zehntel eines Tropfen Öls – gestreckt über eine Minute. Zu den Kernkomponenten des Systems gehören Mikroventile, die mit einem Strömungssensor und Steuerelementen Schmierstoffmengen im niedrigen Nanoliterbereich zuführen können (Bild 3).
Die Mikroventile werden für eine Zeitdauer im Mikrosekundenbereich geöffnet, wodurch ein Dosierimpuls für eine bestimmte Schmierstoffmenge ausgelöst wird. Diese wird in die angeschlossene Kapillarleitung gedrückt. So werden in sehr schneller Folge (Millisekunden) viele Dosierimpulse generiert, wobei ein fast kontinuierlicher Volumenstrom zur Schmierstelle entsteht (Bild 4).
Da die Mikroventile selbst keinen Druck erzeugen können, sorgt ein Vorratsbehälter für den erforderlichen Vordruck. Bei der ersten Produktausführung wird der Vordruck quasi statisch und linear mit Druckluft im Vorratsbehälter aufgebaut. Zusammen mit einem vorgeschalteten Drosselventil wirkt die Druckluft wie eine ideale lineare Feder. Damit besteht das Mikrodosiersystem aus einer Dosiereinheit und einem Vorratsbehälter. Beide Komponenten sind an die Maschinensteuerung angeschlossen, über die sie gesteuert und überwacht werden können (Bild 5). So kann u. a. die Schmierstoffmenge fast in Echtzeit (über ein Maschinenprogramm) angepasst werden.
Die modulare Ausführung ermöglicht auch einen dezentralen Einbau der einzelnen Module. Die Dosiereinheit in Schutzart IP67 wird unmittelbar an oder in der Nähe der Spindel montiert, während der Vorratsbehälter auch weiter entfernt, beispielsweise im Fluidteil, untergebracht werden kann (Bild 6).
Permanente Anpassung
Die hohe, konstante Präzision der Minimalmengendosierung wird unter Berücksichtigung einer Vielzahl von Parametern erzielt. Die zugeführte Schmierstoffmenge wird nämlich nicht nur durch die Ventilöffnungszeiten, sondern auch durch die Viskosität des Öls, die Umgebungstemperatur und andere Faktoren beeinflusst. Dabei können auch Vordruckschwankungen im Druckluftsystem und mögliche Fertigungstoleranzen (z.B. bei den Ventilen) eine Rolle spielen. Damit sich das System auf all diese Faktoren einstellen kann, führt es eine ständige Überwachung und Selbstkalibrierung durch. Der integrierte Strömungssensor erfasst die über die einzelnen Ventile zugeführten Schmierstoffmengen und vergleicht diese Messungen mit den gespeicherten Soll- und Referenzwerten. Sobald die vorgegebenen Toleranzen über- oder unterschritten werden, passt das System die Ventilöffnungszeiten pro Impuls an. Die Kalibrierung wird für jeden aktiven Auslass (Ventil) separat und sequentiell durchgeführt (Bild 7).
Dabei ergibt sich letztlich für jedes Ventil ein eigener Parametersatz, z.B., eine spezielle Öffnungszeit pro Impuls. Die am Strömungssensor oder den Auslässen gemessenen Ausbringungsmengen entsprechen dann dem jeweiligen Sollwert (Bild 8).
Darüber hinaus wird der Kalibriervorgang auch von Ereignissen wie dem Einschalten des Systems nach einer Stillstandzeit oder bei Temperaturänderungen von ± 5 Kelvin, die vom integrierten Temperatursensor festgestellt werden, ausgelöst. In der Firmware der Dosiereinheit werden solche Ereignisse gespeichert. Alle vier Betriebsstunden kalibriert sich das System automatisch selbst.
Erste Erfahrungen
Um die Wirkung der Öl-Mikrodosierung bei Spindellagern über den gesamten Drehzahlbereich zu demonstrieren, hat SKF Vergleichstests an einem vereinfachten, riemengetriebenen Spindellager ohne Temperaturregelung durchgeführt. Die Lagertemperatur am Außenring wurde als Vergleichswert gewählt, da sie relativ einfach zu messen ist und einen ersten Hinweis auf den Zustand der Schmierung gibt. Der Schmierstoff wurde durch den Lageraußenring zugeführt. Der Drehzahlbereich von 0 bis 2,4 Mio. n×dm wurde in Schritten von 3.000 min-1 durchlaufen. Jede Drehzahlstufe wurde 30 Minuten lang gehalten, um sicherzustellen, dass das System einen stabilen Zustand erreicht hatte. Die daraus resultierende Drehzahl des Lagers mit einem mittleren Durchmesser von 54 mm betrug zwischen 0 und 45.000 min-1. Dabei wurden für das Mikrodosiersystem unterschiedliche Mengeneinstellungen gewählt als für ein herkömmliches Öl-Luft-Schmiersystem.
Ergebnisse: Bei niedrigen Drehzahlkennwerten zwischen 0,5 und 1,0 Mio. n×dm (mit einer minimalen Schmierstoffmenge von 30 mm3/h) wurde eine um rund 2 bis 3 Kelvin niedrigere Lagertemperatur festgestellt. Bei höheren Drehzahlkennwerten zwischen 1,8 und 2,4 Mio. n×dm (mit entsprechend nachgeregelten Dosiermengen) blieben die Lager dank des Mikrodosiersystems bis zu 8 Kelvin kühler (Bild 9).
Mögliche Einsparungen
Das SKF Mikrodosiersystem kann viel mehr als nur die zugeführte Schmierstoffmenge minimieren. Vor allem entfällt hier die bei herkömmlichen Öl-Luft-Schmiersystemen erforderliche energieintensive Erzeugung von Druckluft. Für die Verdichtung, Filtration und Trocknung von Druckluft werden rund 0,1 kWh pro Nm³ benötigt. So kann das SKF Mikrodosiersystems beispielsweise bei den Strompreisen in Mitteleuropa eine Einsparung von bis zu 130 Euro pro Jahr und Schmierstelle erbringen. Da Werkzeugspindeln normalerweise mit drei oder vier Lagern ausgestattet sind, können sich die Einsparungen auf jährlich 390 oder 520 Euro summieren.
Zudem bedeutet die nicht vorhandene Druckluft auch deutlich reduzierte Geräuschemissionen. Bei Drehzahlkennwerten von bis zu rund 2 Mio. n×dm wurde bei den Prüfstandsmessungen im Vergleich zu herkömmlichen Öl-Luft-Schmiersystemen eine Verringerung der Geräuschemissionen um bis zu 10 dB(A) verzeichnet.
Das neue SKF Mikrodosiersystem leistet daher einen erheblichen Beitrag zur energieeffizienten, emissionsarmen und hochpräzisen Schmierung von Hochgeschwindigkeitslagern. Dieses Potenzial wird am besten ausgeschöpft, wenn das neue SKF Mikrodosiersystem und die Spindellagerung aufeinander abgestimmt sind.