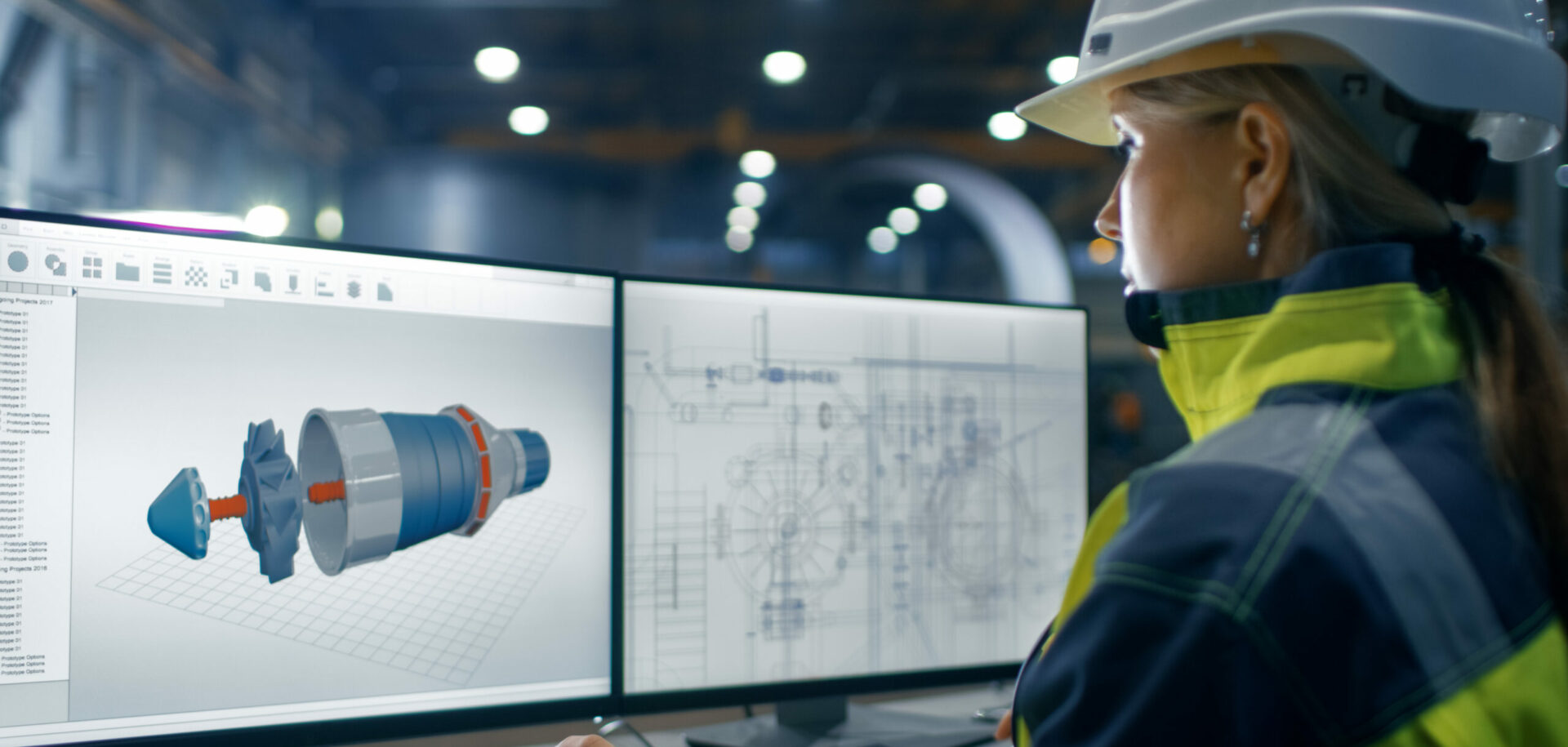
Entwicklung von keramischen Wälzlagerkugeln
Eine maßgeblich treibende Kraft für die Entwicklung keramischer Wälzkörper in Wälzlagern war die Suche nach Lösungen für moderne Gasturbinen mit hohem Wirkungsgrad. Erste Anwendungen wie in Werkzeugmaschinenspindeln, Elektromotoren und Generatoren haben den Einsatz keramischer Wälzkörper auf eine breitere Basis gestellt.
Zusammenfassung
Vor mehr als 400 Jahren bestanden die ersten industriell gefertigten Keramikkugeln aus Marmor und wurden als Kanonenkugeln, Schiffballast oder Kinderspielzeug verwendet. Als die neuen Werkstoffe der Ingenieurkeramik in den 1960er und 1970er Jahren entstanden, wurden daraus Wälzlagerkugeln aus Hochleistungskeramik, die heute in Düsentriebwerken getestet und in Werkzeugmaschinenspindeln, Elektromotoren, Formel-1-Rennwagen und Pumpen erfolgreich eingesetzt werden.
Neue Geschäftsfelder für Hybridlager sind Anwendungen in der Schienenfahrzeugindustrie und im Bereich der erneuerbaren Energien, wie beispielsweise Windkraftanlagen. SKF steht nach wie vor an vorderster Front in der Entwicklung, Industrialisierung, Anwendung und Standardisierung von Wälzlagerkugeln aus Keramik. Die Entwicklungsarbeit geht immer noch weiter, insbesondere bei Keramikkugeln mit größeren Durchmessern. Wälzlagerkugeln aus Siliciumnitrid mit einem Durchmesser von bis zu 47,625 mm sind bereits kommerziell erhältlich. Auf der Werkstoffseite gibt es durchaus noch Möglichkeiten, um die Keramik besser für spezielle Anwendungen auszulegen. Dies spart nicht nur Kosten, sondern schont auch die Umwelt, da weniger energieintensive Prozesse zum Einsatz kommen, um die wachsende Nachfrage nach diesen neuen Werkstoffen zu decken.
Ansprechpartner Verkauf
Oscar Schöppl, Oscar.Schoeppl@skf.com
Hybridlager mit keramischen Wälzkörpern werden heute in vielen anspruchsvollen Anwendungen eingesetzt. Einige aktuelle Anwendungsbeispiele sind in der Schienenfahrzeugindustrie und im Bereich der erneuerbaren Energien, wie beispielsweise Windkraftanlagen, zu finden.
Siliciumnitrid (Si3N4) hat sich als der keramische Standardwerkstoff für Wälzkörper etabliert und in der internationalen Normung Einzug gefunden. Die speziell dafür entwickelten Prüfverfahren (Bild 1) folgen dem Trend hin zu immer größeren Keramikkugeln. Mittlerweile sind qualitativ hochwertige Siliciumnitrid-Wälzlagerkugeln mit einem Durchmesser von bis zu 47,625 mm (1 7/8”) (Bild 1, rechts) kommerziell erhältlich.
Die Entwicklung der neuen Synthesekeramik Siliciumnitrid in den 1960er und 1970er Jahren führte dazu, dass Wälzlagerkugeln aus dieser Hochleistungskeramik Stand der Technik wurden, und zwar für unterschiedliche Produkte wie Düsentriebwerke, Werkzeugmaschinenspindeln, Elektromotoren, Formel-1-Rennwagen, Pumpen etc. Die Entwicklungsarbeit geht aber immer noch weiter, insbesondere im Bereich der größeren Kugeln.
Die Entwicklung von Wälzlagerkugeln aus Keramik und ihre Anwendungen
Der Traum, Gasturbinen mit sehr hohem thermischen Wirkungsgrad zu bauen, war eine wichtige treibende Kraft für die Entwicklung moderner Ingenieurkeramiken. Bei Drehzahlen von mehr als 30.000 Umdrehungen pro Minute und prognostizierten Lagertemperaturen über 650 °C sind die Betriebsbedingungen für die Hauptwellenlager solcher Gasmotoren extrem hart [1]. Bei Gastemperaturen über 1.100 °C haben nur Hochleistungskeramiken eine höhere Härte als Wälzlagerstähle oder Kobaltbasislegierungen wie Stellite oder auch hoch legierte wolframhaltige Werkzeugstähle, die bei diesen hohen Temperaturen angedacht wurden. Der primäre Einsatzbereich solcher Turbinen war in Triebwerken. Diese Anwendung verlangt nach Werkstoffen, die leicht (geringe Dichte), hochfest und hochtemperaturbeständig sind und eine Reihe zusätzlicher Anforderungen, wie beispielsweise Steifigkeit, Verarbeitbarkeit und Verfügbarkeit, erfüllen.
Keramiken konnten die ersten beiden Anforderungen wie hohe Temperaturstabilität und geringe Dichte erfüllen. Aber sie waren dafür bekannt, eine geringe Festigkeit und hohe Sprödigkeit aufzuweisen. Die Forschungsergebnisse von Luft und Raumfahrt wurden verwendet, um zu verstehen, warum Keramiken eine geringe Festigkeit hatten und wie diese Eigenschaft verbessert werden konnte. Die Theorien, Methoden und Prozesse, die aus diesen Erkenntnissen hervorgingen, führten zu verbesserten Keramiken wie die damals neue Synthesekeramik Siliciumnitrid. Das SKF Engineering and Research Centre (ERC) in den Niederlanden hat hier bereits sehr früh die Entwicklung keramischer Werkstoffe intensiv begleitet.
Siliciumnitrid ist eine spezielle Art von Keramik, die sich durch selbstverstärkende Eigenschaften auszeichnet. Die beiden keramischen Phasen, Alpha-Siliciumnitrid und Beta-Siliciumnitrid, haben unterschiedliche Kristallformen; eine davon bildet sehr lange Nadeln (Bild 2). Während der Prozessführung kann die Ausbildung des richtigen Verhältnisses beider Phasen so gesteuert werden, dass sich ein Werkstoff mit für Keramiken relativ hoher Zähigkeit bildet. Der erste Siliciumnitrid-Werkstoff, der eine ausreichend hohe Festigkeit und Zähigkeit für Wälzlageranwendungen hatte, war heißgepresstes oder heißisostatisch gepresstes (HIP) Siliciumnitrid.
In den 1960er und 1970er Jahren hat das zur SKF Gruppe gehörende Unternehmen Marlin Rockwell Corp. (MRC) die ersten Keramiklager konstruiert. Das Hybridlager mit geteiltem Innenring wurde von MRC für ein von der US-Regierung finanziertes Testprogramm gefertigt. Der Langzeiteinsatz des Siliciumnitrid-Werkstoffs in einem Wälzlager unter Verwendung von Festschmierstoffen bei Temperaturen über 500 °C wurde von SKF im Jahr 1984 [1] nachgewiesen.
Um das Jahr 1990 begann neben der Luft- und Raumfahrt auch die Werkzeugmaschinenindustrie, die Vorteile des geringen spezifischen Gewichts bei hohen Drehzahlen zu nutzen. Mitte der 1990er Jahre wurden Frequenzumwandler in Elektromotoren verstärkt eingesetzt, die Stromschäden in Wälzlagern verursachten. Hier boten sich Hybridlager als sehr robuste Alternative zu anderen Lösungen der Stromisolierung an. Ungefähr zur gleichen Zeit wurden Hybridlagerlösungen auch in Formel-1-Rennwagen eingebaut, um ihre Robustheit unter extremen Anwendungsbedingungen (Mangelschmierung, hohe Last, hohe Drehzahlen) zu nutzen. Die Anwendung von Hybridlagern in Pumpen und Kompressoren kam verstärkt um das Jahr 2000, wo selbst Mangelschmierung in der Anwendung kein Problem darstellte. Andere Medien geringerer Viskosität als Schmieröl, wie etwa Kühlschmierstoffe, zeigten sich ausreichend für eine Schmierung der Lagerung. Darüber hinaus begünstigte die hervorragende Korrosionsbeständigkeit von Keramiken im Vergleich zu anderen Werkstoffen ihren Einsatz bei Sauergaskompressoren. In den letzten Jahren hat die Keramik im Bereich der erneuerbaren Energien bei Windkraftanlagen ein Einsatzfeld gefunden. Hier werden bereits große Keramikkugeln mit einem Durchmesser von 47,625 mm benötigt (Bild 1, rechts). Ein weiteres Anwendungsgebiet mit steigender Nachfrage ist die Schienenfahrzeugindustrie, wo Wälzkörper aus Keramik in Fahrmotoren Verwendung finden (Bild 3). Die Stromisolierung und bessere Performance von keramischen Wälzkörpern unter relativ geringer Lagerlast, die sich in geringerer Reibungswärme niederschlagen, erhöhen die Fettgebrauchsdauer in dieser Anwendung.
Prüfung und Qualifizierung von Wälzlagerkugeln aus Hochleistungskeramik
Ein breites Spektrum von Wälzlageranwendungen kann von der Einführung von Keramikkugeln profitieren. Um sicherzustellen, dass die Keramik ihre Vorteile im Produkt zeigt, ist eine sorgfältige Prüfung der Werkstoffe, die in Wälzlagern eingesetzt werden, notwendig. Zu diesem Zweck wurden im Laufe der Zeit entsprechende Prüfverfahren eingeführt.
Eine erste Beurteilung des Werkstoffs kann im Allgemeinen durch Bewertung der Homogenität des Makrogefüges (Bild 4, oben) und des Mikrogefüges (Bild 4, Mitte) anhand von Probenquerschnitten aus Kugelrohlingen oder gefinishten Kugeln durch Anfertigung eines Gefügeschliffes erfolgen. Auf diese Art können auch relativ rasch die Härte (Bild 4, unten) und der Eindruckrisswiderstand eines möglichen Wälzlagerwerkstoffes bestimmt werden.
Es wurde eine neue Methode entwickelt, um die Festigkeit an gefinishten Kugeln zu bestimmen. Man hat bei hochfesten Werkstoffen festgestellt, dass die Oberflächengüte einen erheblichen Einfluss auf die Bauteilfestigkeit hat. Es ist weiters ein Faktum, dass die Oberfläche von Wälzlagerkugeln von besserer Qualität ist, als jene von Biegebruchstäbchen. Der sogenannte „Kerbkugelversuch“ (Bild 5) hat daher den Vorteil, dass die Festigkeit an den Wälzlagerkugeln direkt ermittelt werden kann und die aufwendige Herstellung von Biegebruchstäbchen, wie in der ISO26602:2009 festgelegt wurde, wegfällt. Die Kugeln werden mit einer Kerbe versehen und senkrecht zur Kerbe belastet. Man erhält somit eine Biegeprobe in Kugelform. Nähere Angaben zu diesem Prüfverfahren wurden bereits veröffentlicht [2, 3]. Es wurde nachgewiesen [4], dass Oberflächenfehler wie Hertz’sche „C“-Risse einen beträchtlichen Einfluss auf die Festigkeit der Kugeln haben. Eine erste Idee über Ermüdung im Wälzkontakt kann mittels der Polymet-Prüfmaschine (Bild 6) erhalten werden. Ein Stab aus der zu prüfenden Keramik wird zwischen zwei rotierende Stahlscheiben gespannt. Typischerweise werden 40×106 Lastzyklen bei Kontaktpressungen von 3 oder 4,8 GPa als Prüfkriterium für eine Wälzlagerkeramik herangezogen. Die zyklische Ermüdung im Wälzkontakt an gefinishten Kugeln kann mit Hilfe eines modifizierten Vierkugelapparates geprüft werden. Eine in die Antriebswelle eingespannte Keramikkugel treibt drei Stahlkugeln in einem Stahltiegel an; dabei wird ein ganz einfaches Lager nachgebildet (Bild 7). Ein ähnlicher Test kann auch mit fünf Kugeln durchgeführt werden, wobei vier Kugeln unten verwendet werden. Eine weitere Möglichkeit zur Beurteilung der Ermüdung im Wälzkontakt an gefinishten Keramikkugeln ist der sogenannte „V-Groove-Test“ (Bild 8). Eine Kugel zwischen Ringen mit V-förmigen Rillen wird dabei Kontaktdrücken zwischen 1,5 und 5,5 GPa ausgesetzt. Mit der Standarddrehzahl des Prüfstands können bei Verwendung von Kugeln mit einem Durchmesser von 28,575 mm ungefähr 6 Mio. Lastwechsel pro Stunde gefahren werden.
Die Ermüdungslebensdauer von Hybridlagern wird unter verschiedenen Schmierbedingungen getestet. Die typische Lagerart für Lebensdauerversuche ist ein 7209 Schrägkugellager, in dem ein Kugeldurchmesser von 12,7 mm verwendet wird. Ein weiterer Hybridlager-Lebensdauerversuch mit Fettschmierung am Beispiel eines größeren Schrägkugellagers 7318, in dem der Kugeldurchmesser 31,7 mm beträgt, wird in Bild 9 gezeigt.
Schlussfolgerung
Mit diesen formalen Methoden zur Bewertung keramischer Wälzkörper in Hybridlagern können die Anwender sicher sein, dass diese Werkstoffe ihre Leistung in modernen Anwendungen erbringen. Im Zuge der weiteren gezielten Entwicklung keramischer Werkstoffe für Hochleistungsanwendungen kann für die Zukunft angenommen werden, dass Hybridlager ihren erfolgreichen Weg bei Anwendungen in neuen Industrien mit oftmals hohen Anforderungen fortsetzen werden.
Literatur
[1]Pallini, R.A.: Turbine engine bearings for ultra-high temperatures, SKF Ball Bearing Journal 234, September 1989
[2]P. Supancic, R. Danzer, S. Witschnig, E. Polaczek, R. Morrell: A new test to determine the tensile strength of brittle balls — The notched ball test, Journal of the European Ceramic Society 29 2447–2459 (2009)
[3]P. Supancic, R. Danzer, W. Harrer, Z. Wang, S. Witschnig, O. Schöppl: Strength Tests on Silicon Nitride Balls, Key Engineering Materials, Vol. 409, pp. 193-200 (2009)
[4]P. Supancic, R. Danzer, Z. Wang, S. Witschnig, O. Schöppl: The Notched Ball Test – A New Strength Test for Ceramic Spheres, 9th Symposium on Ceramic Materials, Shanghai (2008)