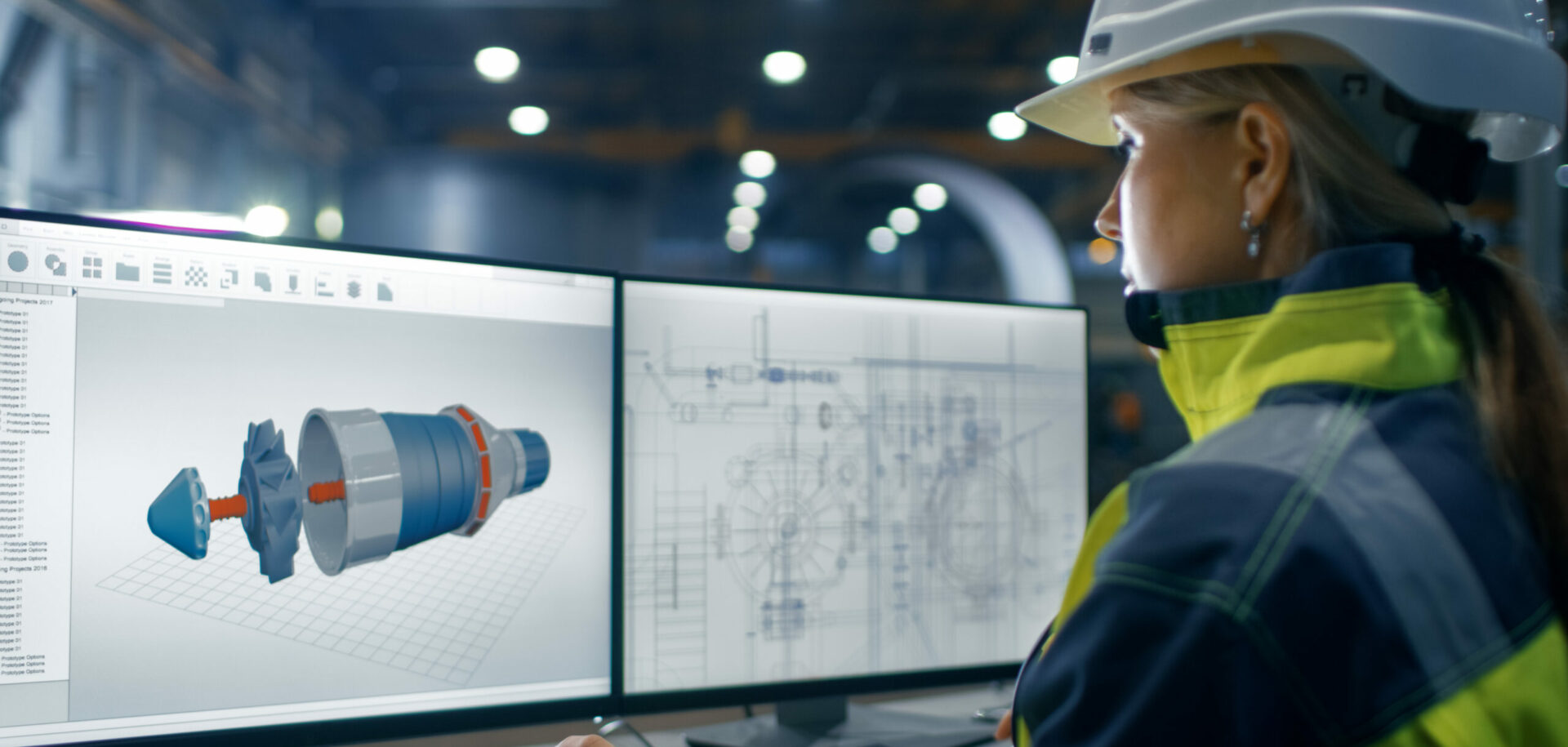
Erweiterte numerische Simulationen für optimierte Dichtungsausführungen
Numerische Simulationen sind heute aus der Entwicklung neuer Produkte und Verbesserung bereits vorhandener Produkte nicht mehr wegzudenken. Im Hinblick auf eine Optimierung des allgemeinen Produktdesigns und eine bessere Unterstützung der Kunden stattet die SKF Gruppe ihre Produktingenieure derzeit mit Finite-Elemente-Tools aus, die im SKF Forschungszentrum ERC entwickelt wurden.
Zusammenfassung
Die SKF Produktingenieure verwenden jetzt ein leistungsfähiges Analyse- und Berechnungstool, um neue Dichtungsausführungen zu entwerfen und deren Verhalten zu prognostizieren. Der SKF Seal Designer verkürzt die Produktentwicklungszeit und unterstützt die Produktingenieure dabei, die Dichtungsleistung besser an die jeweiligen anwendungsspezifischen Erfordernisse anzupassen.
Numerische Simulationen spielen in den verschiedenen Lebenszyklusstadien von immer mehr Produkten eine wichtige Rolle. Sie tragen zur Kostensenkung in der Konzeptentwicklung und in den Prototypphasen bei und sorgen dafür, dass optimierte Prototypausführungen zum Test gelangen.
Es sind verschiedene kommerzielle Berechnungstools am Markt erhältlich, die sich als sehr zuverlässig und universell anwendbar erwiesen haben. Allerdings braucht man sehr gut ausgebildete Anwender, die mit diesen Systemen nicht nur umgehen können, sondern auch deren Ergebnisse zu interpretieren und sie in sinnvolle Lösungen umzuwandeln verstehen.
SKF verfügt über langjährige Erfahrung auf dem Gebiet numerischer Simulationen, und zwar nicht nur in der Nutzung dieser kommerziellen Simulationssoftwarepakete, sondern auch in der Entwicklung eigener Berechnungsprogramme. SKF Ingenieure nutzen die Orpheus und BEAST Plattformen täglich, um Anfragen zu beantworten und Kunden zu unterstützen. Mit diesen selbst entwickelten Werkzeugen können Wälzlageranwendungen von SKF in vielfältiger Weise und unterschiedlicher Komplexität simuliert werden. Diese Erfahrung und diese Werkzeuge werden kontinuierlich verbessert und mit neuen Funktionen und Leistungsmerkmalen ausgestattet, um den Vorstellungen von SKF, bei denen sämtliche Komponenten – Lager, Wellen, Dichtungen, Getriebe und Gehäuse – als Gesamtsystem simuliert werden, zu entsprechen (Bild 1).
Dichtungen und numerische Simulationen
Der erste Schritt hin zur Simulation von Gesamtsystemen ist die Simulation von Dichtungen als Einzelkomponenten (Bild 2). Diese zunächst detaillierte Betrachtung eines einzigen Bauteils führt dazu, dass die SKF Ingenieure umfassendere Kenntnisse über das Verhalten einer Dichtung im eingebauten Zustand erlangen.
Bei numerischen Simulationen von Dichtungen sind verschiedene mechanische Aspekte zu berücksichtigen. Im Folgenden werden diese Aspekte kurz beschrieben, und es wird ein Überblick über die Komplexität von Dichtungssimulationen gegeben. Ferner wird die Technologie vorgestellt, die SKF entwickelt, um ihre Produktingenieure mit leistungsfähiger und zuverlässiger Software auszustatten.
Simulationen von Elastomer: ein hochgradig nichtlineares Material
Viele der heutigen technischen Berechnungen basieren auf der Annahme, dass sich ein Werkstoff linear und elastisch verhält. Im Allgemeinen verhalten sich Elastomerwerkstoffe nichtlinear. Es reicht nicht aus, eine Konstante zu definieren, um Kraft und Verschiebungen oder Spannung und Dehnung zueinander in Beziehung zu setzen. Stattdessen braucht man hier komplexere Werkstoffmodelle, die eine mehrachsige Nichtlinearität handhaben können.
Unter anderem werden oft hyperelastische Modelle zur Simulation des Verhaltens von Elastomerwerkstoffen eingesetzt. Diese Werkstoffmodelle sind zwar elastisch, aber außerhalb eines bestimmten Bereichs weicht die Nichtlinearität des Spannungs-Dehnungszusammenhangs, wie in Bild 3 ersichtlich, erheblich vom linearen Verhalten ab. Darüber hinaus ist das Werkstoffverhalten stark von der Ausrichtung der Verformung abhängig.
Elastomer ist der am häufigsten verwendete Dichtungswerkstoff, da er den Dichtungen ermöglicht, den Bewegungen der Gegenlaufflächen zu folgen (z. B. Wellen, Stangen oder Lager). Bei der Simulation von Dichtungen wird daher eine zuverlässige Methode zur Simulierung hyperelastischer Werkstoffmodelle benötigt, die große Verformungen in multiplen Ausrichtungen nachvollziehen kann.
Simulationen von Elastomer: ein nahezu inkompressibles Material
Elastomer ist auch ein nahezu inkompressibles Material, das heißt, die Volumenänderung eines zusammengedrückten oder gedehnten Elastomermusters vor und nach der Verformung ist nahezu null. Dies ist ein Werkstoffverhalten, das die numerischen Verfahren der herkömmlichen Simulationssoftware vor Probleme stellt. Die Inkompressibilität des Materials bewirkt numerische Instabilitäten, die im Allgemeinen als Volumenblockieren („Volumetric Locking“) bezeichnet werden. Um diesen Blockiereffekt zu unterdrücken, wurde eine spezielle Implementierung des Integrationsschemas vorgenommen, die für genaue und stabile Ergebnisse sorgt [1].
Im Rahmen einer Literaturrecherche hat sich zur Lösung des Volumenblockierens die F-Bar-Methode [1] angeboten, bei der eine Änderung der in der Literatur [2] dargestellten traditionellen Integrationsverfahren erforderlich ist. In Bezug auf diesen Aspekt hat die Zusammenarbeit mit Universitäten, insbesondere mit der Universität Twente in den Niederlanden, den Nachweis für die Richtigkeit und Genauigkeit der implementierten Algorithmen erbracht. Dadurch wird die Qualität der Berechnung vergleichbar mit der Lastberechnung, die mit einem der handelsüblichen FE-Programme wie ABAQUS, Marc oder ANSYS durchgeführt wird.
Simulationen von Dichtungen: Kontaktmechanik für den Umgang mit Übermaßen
Radialwellendichtringe müssen prinzipiell mit einem bestimmten vorgegebenen Übermaß zwischen Bohrung und Welle eingebaut sein. Eine Simulation des Kontakts zwischen den Dichtungen und den umgebenden Oberflächen (z. B. Gehäuse, Wellen, Schleuderscheiben oder Lager) ist daher sehr wichtig (Bild 4 und 5).
Um das Übermaß zwischen Dichtungen und Umbauteilen der Anwendung richtig simulieren zu können, war die Kontaktmechanik eine der Hauptanforderungen bei der Entwicklung des Softwaretools. Für den Kontakt gibt es verschiedene Lösungen in numerischen Codes. In Anbetracht der Art des Werkstoffs, der sich normalerweise in Kontakt befindet (meist Elastomer und Stahl), wird angenommen, dass es keine Kopenetration zwischen den kontaktierenden Bauteilen gibt. Diese Annahme führte zur Anwendung der Lagrange-Multiplikator-Methode (die Dichtungsverformung wird gezwungen mathematisch gleich der Restriktionen zu sein, die von den umgebenden Gegenlaufflächen vorgegeben werden) anstelle der sogenannten „Penalty-Methode“ (die Dichtungsverformung wird zwangsweise Penalty-Funktionen unterworfen, die bei Verletzung der Restriktionen aktiviert werden).
Simulationen eines Dichtungssystems: FE-Solver
Die beste Möglichkeit zur Kombination aller oben genannten Anwendungen in numerischen Simulationen ist die Nutzung der Finiten-Elemente-Methode (FEM). Mit dieser Methode lassen sich die zusammenwirkenden Aspekte von hyperelastischen Werkstoffmodellen, großen Verformungen und Kontaktmechanik mit der Lagrange-Multiplikator-Methode und spezieller Implementierung leicht handhaben, und das numerische Blockierproblem aufgrund der Werkstoffinkompressibilität wird vermieden.
SKF Seal Designer
Die SKF Gruppe hat mit Unterstützung des SKF Forschungszentrums ERC ihre Produktingenieure mit einem modernen, auf der Orpheus Plattform basierten Berechnungstool ausgestattet, dem SKF Seal Designer.
Die Hauptmerkmale der Software decken die beiden Bereiche Fertigungsprognosen (Schwund vom Werkzeug bis zur fertigen Geometrie) und Verhaltensprognosen (Einbau auf einer Welle und/oder in ein Gehäuse) ab.
Die SKF Produktingenieure nutzen die Möglichkeiten der Fertigungssimulation, um die Entwurfsstudie vor Festlegung der endgültigen Dichtungsform zu verbessern. Dieses Vorgehen dient ebenfalls der Verbesserung der Werkzeuggeometrie, die aufgrund ihres Kostenbeitrags eine der wichtigsten Phasen des gesamten Entwurfsprozesses darstellt, aber auch weil die Werkzeuggeometrie für andere Entwürfe wiederverwendet werden kann.
Ein weiteres Funktionsmerkmal stellt die Berechnungsmöglichkeit einer auf der Welle montierten Dichtung dar. Die Dichtlippe einer eingebauten Dichtung übt auf die Gegenlauffläche eine Anpresskraft aus (Bild 6). Diese ist einer der wichtigsten Parameter im Hinblick auf statische und dynamische Betriebsbedingungen. Die Anpresskraft der Dichtlippe sorgt für die gewünschte Dichtigkeit, aber ist auch für die Reibung unter der Dichtlippe verantwortlich. Zusätzlich kann eine Zugfeder eingesetzt werden, um die für die Abdichtung erforderliche Anpresskraft bei Alterung des Dichtungswerkstoffs aufrechtzuerhalten (Bild 7). Die genaue Vorhersage der Anpresskraft der Dichtlippe unter unterschiedlichen Betriebsbedingungen ist daher eine entscheidende Anforderung an ein Simulationswerkzeug, mit dem die Anzahl der Entwurfsiterationen reduziert und folglich die Markteinführung neuer Produkte beschleunigt werden kann (Bild 8 und 9).
Fazit
Mit dem SKF Seal Designer können die SKF Produktingenieure die gesamte Leistungspalette der FE-Simulationen nutzen. Dieses Softwaretool verkürzt die Produkteinführungszeit und ermöglicht den Produktingenieuren eine virtuelle Beurteilung der Art und Weise, wie sich Dichtungsparameter, kundenseitige Designanforderungen und anwendungsspezifische Erfordernisse auf die Dichtungsleistung auswirken.
Literatur
[1]: “Computational Methods for Plasticity: Theory and Applications”, by EA de Souza Neto, D Peric and DRJ Owen (30.Dez., 2008)
[2] “The Finite Element Method”, Sixth Edition, by OC Zienkiewicz and RL Taylor (20.Sept., 2005)