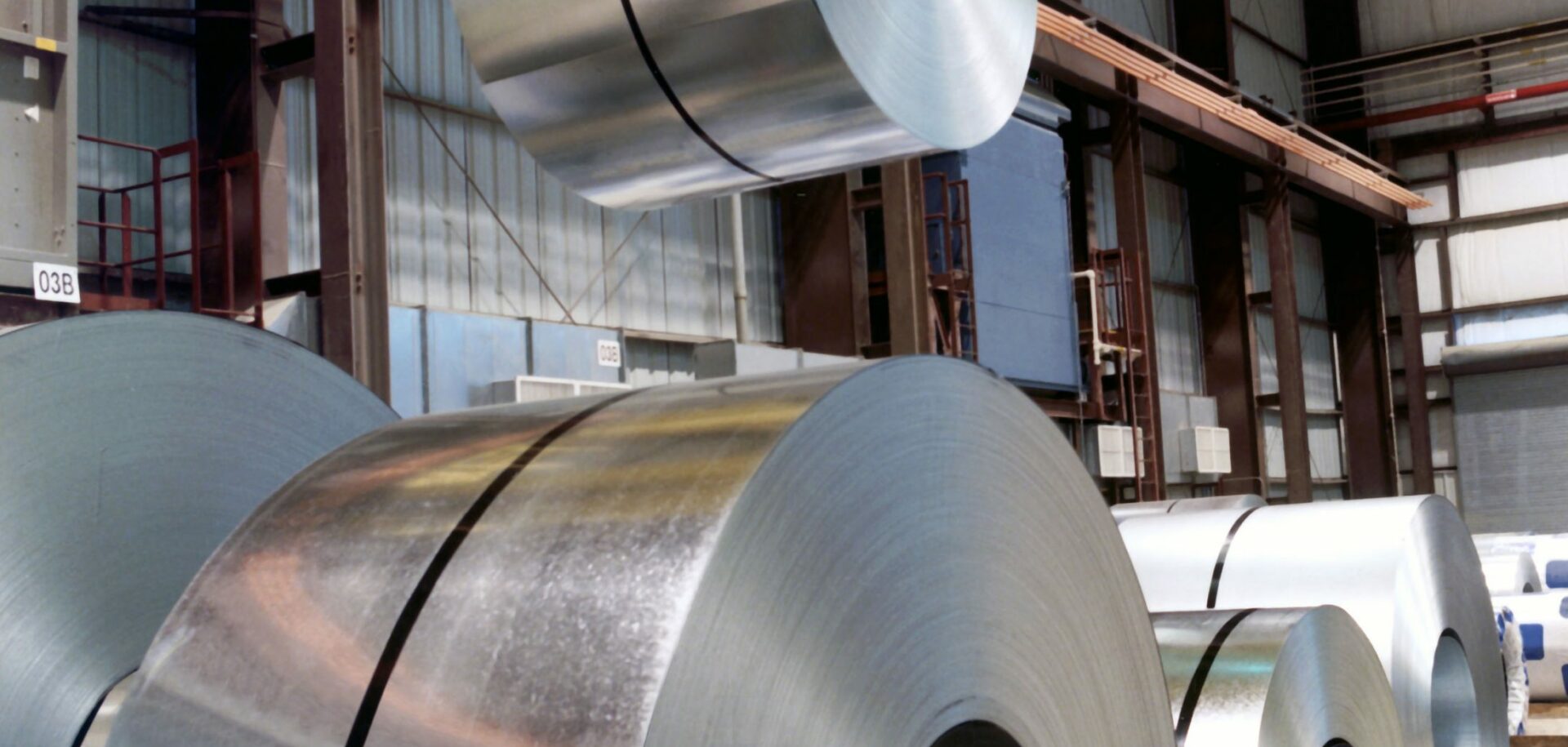
Konsequente Problemlösung
Immer wieder kam es in einem US-Stahlwerk zu Lagerausfällen. Dank systematischer Vorgehensweise konnte schließlich die Ursache festgestellt werden. Was zunächst wie ein Schmierungsproblem aussah, erwies sich als Dichtungsfrage. Eine neue verbesserte Lösung musste her.
U.S. Steel
Die U.S. Steel Corp. gehört mit Umsatzerlösen von 10,2 Milliarden US-Dollar zu den Fortune-500-Unternehmen.
Der integrierte Stahlproduzent mit Sitz in Pittsburgh im US-Bundesstaat Pennsylvania betreibt große Stahlwerke in Nordamerika und Europa.
U.S. Steel verfügt über eine Produktionskapazität von circa 24,4 Millionen Nettotonnen Stahl pro Jahr und bietet Mehrwert-Stahlprodukte für den Automobil- und Anlagenbau, für das Baugewerbe und andere Branchen.
Immer wieder sorgten Verunreinigungen durch Schmierfett bei den Granite City Works der U.S. Steel Corp. in St. Louis im US-Bundesstaat Illinois für Probleme. Vorzeitige Lagerausfälle in den Rollgängen der Warmbreitbandstraße und damit Schädigungen an den Förderrollen waren die Folge.
Daten aus 16 Jahren zeigten, dass 30 Prozent aller Förderrollenschäden auf Lagerausfälle zurückzuführen waren. In den letzten drei Jahren hatten die Ausfälle so zugenommen, dass sie sogar für 50 Prozent der Probleme mit Förderrollen verantwortlich waren.
U.S. Steel entschied, dass die richtige Lösung nur durch eine konsequente und strukturierte Vorgehensweise gefunden werden konnte. Der erste Schritt bestand darin, mehr Schmierfett in die Lagergehäuse zu pumpen. Doch dadurch verschlimmerte sich das Problem nur noch. Als strategischer Partner von U.S. Steel wurde SKF gebeten, die Möglichkeiten für eine höhere Zuverlässigkeit zu eruieren. Im Mittelpunkt sollten Effizienzsteigerungen stehen mit dem Ziel, den Ausschuss zu verringern und Kosten einzusparen.
Ein spezielles Team aus Experten von SKF und U.S. Steel verbrachte rund 18 Monate damit, detaillierte Informationen zu sammeln, um die Ursache der Lagerausfälle zu identifizieren. Dabei schaute man sich jede einzelne Rollenkomponente – Welle, Lager, Lagergehäuse, Dichtungen und Schmiersystem – näher an und stellte Wartungsdaten beispielsweise zu den Schmierverfahren und der Wirksamkeit des Dichtungssystems zusammen. Das Team kam zu der Erkenntnis, dass starke Verunreinigungen und eine Schiefstellung der Lager beim Einbau ein wesentlicher Grund für das Problem waren, aber auch eine veraltete Dichtungstechnik, die immer noch verwendet wurde. Um all dies zu beheben, machten sich Installationstechniker von U.S. Steel und SKF gemeinsam daran, die Instandhaltungs- und Einbauverfahren zu verbessern.
Mike Bekeske, Leiter RCM (Zuverlässigkeitsorientierte Instandhaltung) im Stahlwerk, hatte sich mit einer möglichen Schmierungslösung von SKF befasst. Wie sich herausstellte, war allerdings die Schmierung gar nicht das Problem. „Was zunächst wie eine Frage der Schmierung aussah, wurde zu einer Dichtungsfrage“, sagt Paul Conley, Cheftechniker im Geschäftsbereich Schmiersysteme von SKF in USA. „Das Schmierfett im Lagergehäuse dient der Schmierung und dem Schutz vor Verunreinigungen, die Dichtung wiederum soll Wasser und Feuchtigkeit abhalten.“
Beobachtungen, Tests und Analysen ergaben, dass die Dichtungen in den Rollgängen der Warmbreitbandstraße nicht ordnungsgemäß funktionierten. Wasser und Dampf drangen in die Lagerhohlräume ein. Wenn Lager ausfielen und die Förderrollen sich nicht mehr drehten, musste die Produktion gestoppt werden, bis die beschädigten Rollen ausgetauscht waren. Durch das Gleiten der heißen Brammen auf dem Rollgang kam es zu Einschlüssen im Material. Dann konnten die schadhaften Brammen nur noch verschrottet werden.
Zur Verbesserung des Dichtungssystems installierte SKF ECOPUR-Doppellippendichtungen, wodurch sich der Wassergehalt in den Lagern beträchtlich verringerte. Lag er zuvor bei 30 bis 35 Prozent, betrug er jetzt mit den neuen Dichtungen nur noch fünf Prozent – eine drastische Reduzierung. Ein weiteres Plus war die 50-prozentige Einsparung beim Schmierfettverbrauch.
Als zweiter Teil der Lösung wurde SKF SPEEDI-SLEEVE eingebaut, eine dünnwandige Schutzhülse aus Metall, die über dem verschlissenen Bereich von Wellen in Position gebracht wird und eine ausgezeichnete Dichtungsoberfläche bietet.
Wir konnten die Ursachen des Problems beheben.
Mike Bekeske, Granite City Works, Leiter RCM
Feldversuche bestätigten die Ergebnisse. „Wir konnten die Ursachen des Problems beheben“, erklärt Bekeske. „Ausgehend von diesen Versuchen waren wir zudem in der Lage, die Intervalle zwischen Förderrollenausfällen von durchschnittlich sechs auf geschätzte 60 Monate zu erhöhen. Weniger Ausfälle heißt mehr Betriebszeit und weniger Kosten für den Austausch von Förderrollen.“
Die strukturierte Vorgehensweise bei der Lösung von Problemen ist inzwischen ein etabliertes Konzept. In Zukunft werden die Rollenbaugruppen der Rollgänge kontinuierlich überwacht, um Schäden frühzeitig zu erkennen und die Zuverlässigkeit zu verbessern. Das Pilotprogramm von Granite City wird zunehmend auch von anderen amerikanischen Stahlwerken der U.S. Steel Corp. übernommen.