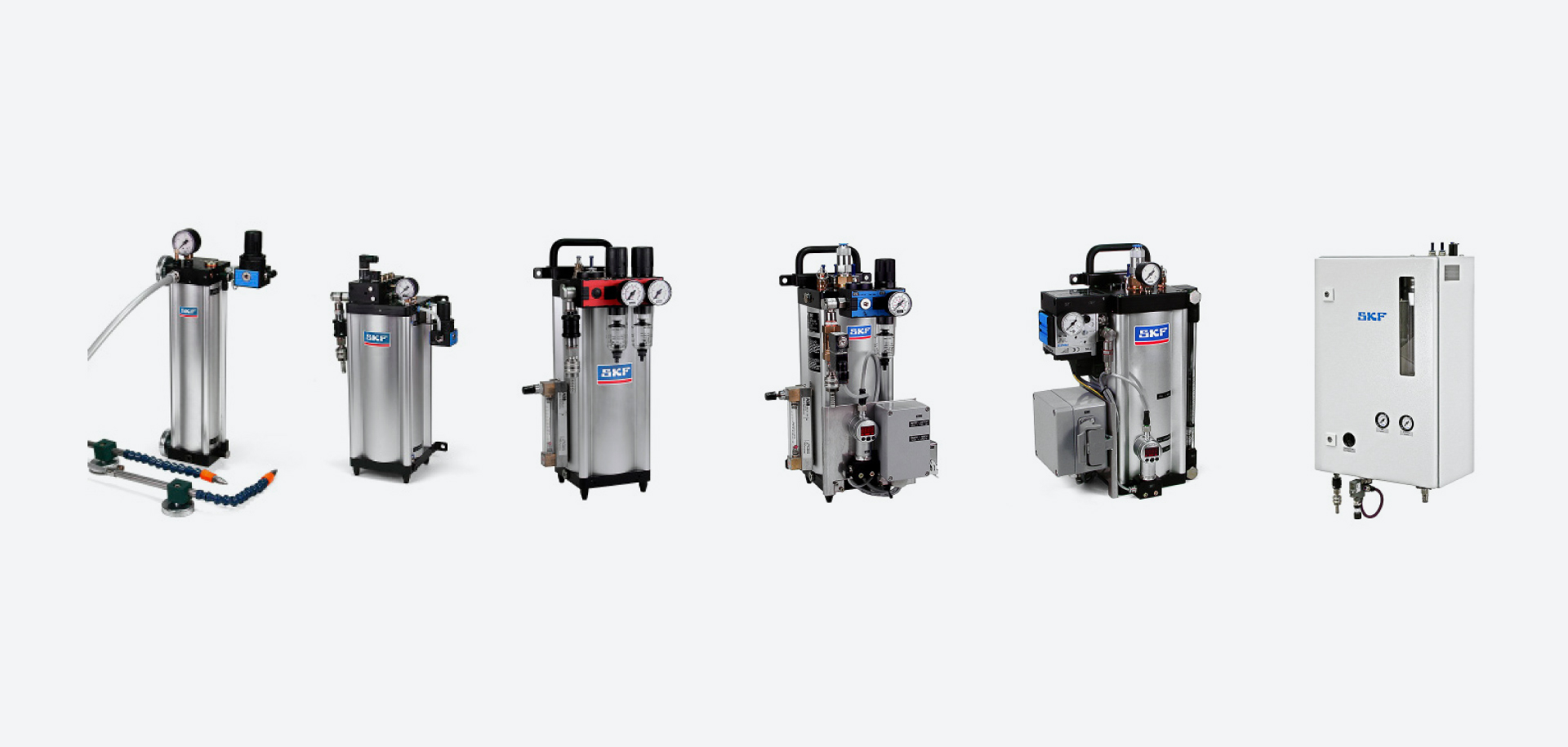
Genug ist genug
Die Minimalmengenschmierung (MMS) ist nachhaltig, steigert die Produktivität und reduziert die Zerspanungskosten. Deshalb wird sie in Bearbeitungsprozessen immer beliebter.
SKF hat die Minimalmengenschmierung (MMS) in eigenen Fertigungsprozessen eingesetzt und mit den SKF LubriLean Minimalmengenschmiersystemen ein umfangreiches Angebot an MMS-Lösungen entwickelt. Während SKF erhebliche Vorteile aufgrund der MMS-Einführung verzeichnete, darunter einen drastischen Rückgang des Ölverbrauchs und eine höhere Bearbeitungsproduktivität, hat HRE Hydraulic S.L., ein spanischer SKF Vertragshändler für Schmierungslösungen, eine Untersuchung zur Quantifizierung der Einsparungen bei den Gesamtbetriebskosten in Auftrag gegeben. Tecnalia, ein führendes Forschungs- und Entwicklungsunternehmen in der Nähe von Bilbao in Spanien, führte die Tests durch.
Prüfparameter
Die Tests waren so konzipiert, dass ein Vergleich der Bearbeitungsleistung, der Schnittkrafteinwirkung, des Werkzeugverschleißes und der Werkzeugtemperaturen unter verschiedenen Schmierbedingungen sowie der Gesamtkosten bei Trockenbearbeitung (ohne Schmierung), Nassbearbeitung mit einem Kühlsystem und innerer und äußerer MMS durchgeführt werden konnte.
Zusammenfassung
Wenn es um die Produktivität, Kosteneffizienz und Umweltverträglichkeit von Zerspanungsprozessen geht, nimmt die Bedeutung der Minimalmengenschmierung (MMS) ständig zu. In Versuchen wurde jetzt nachgewiesen, dass die Gesamtbetriebskosten durch den Einsatz eines SKF LubriLean Systems für die innere MMS im Vergleich zur Nassbearbeitung um die Hälfte gesenkt werden können.
Das Bearbeitungszentrum IBARMIA ZV 25 (Bild 1) diente als Basisprüfstand. Diese Werkzeugmaschine wurde für die Nassbearbeitung (Kühlsystem) und die Trockenbearbeitung ausgelegt und mit einem SKF LubriLean VarioSuper System für die innere und äußere MMS ausgerüstet.
Als Prüfwerkstoff wurde Duplex-Edelstahl 1.4462 eingesetzt. Als Werkstücke dienten 400 mm x 90 mm große Rohlinge, als Zerspanungswerkzeuge 4-schneidige Fräser Kendu 3203.57(Z4). Die Tests wurden mit äußerer Schmierung oder bei Trockenbearbeitung durchgeführt, wobei jeweils der gleiche Fräsertyp – wegen der inneren Kanäle jedoch in abgewandelter Form – verwendet wurde.
Es wurden zwei Schmierstoffarten ausgewählt. Im Nassbearbeitungsprozess wurde der Kühlschmierstoff Houghton HOCUT B-750 verwendet; dieses lösliche Öl mit einer Konzentration von 7 % wurde der Werkzeugmaschine von außen unter einem Druck von 2,3 MPa (23 bar) zugeführt. Bei der inneren und äußeren MMS wurde das eigene SKF Produkt LubriOil benutzt. Folgende Einstellungen wurden vorgenommen:
Parameter:
Drehzahl 2.228 min-1
Schnittgeschwindigkeit 70 m/min
Vorschub pro Schneide 0,05 mm/Zahn
Schnitttiefe 8 mm
Schnittbreite 4 mm
Die Tests wurden jeweils mit zwei Werkzeugen wiederholt, und es wurden Messwerte für den Stromverbrauch und die Werkzeugstandzeit ermittelt.
Ergebnisse
Der Stromverbrauch wurde mit einem an die Stromquelle angeschlossenen Leistungsmesser FlukeView 435 gemessen. Dieses Messgerät zeichnete die Leistungsaufnahme der Werkzeugmaschine, die in jeder Phase verbrauchte Strommenge sowie den Gesamtstromverbrauch auf (Bild 2).
Es wurde eine Vergleichsanalyse der Werkzeugstandzeit für die verschiedenen Schmiertechniken durchgeführt. Als Kriterium für das Ende der Standzeit galt, dass sich beim Werkzeug ein Schadenseintritt in Form eines Verschleißes der Werkzeugschneide zeigte (VB <0,3 mm); Messungen der Flankenverschleißwerte (VB) wurden mit einem Stereomikroskop in der Flanke (VB) nach jeweils 10 Fräsbahnen vorgenommen.
In den Trockenbearbeitungsversuchen kam es nach kurzer Zeit zu einem Bruch der Werkzeuge.
Bild 3 zeigt den Zustand der Schneidwerkzeuge in den beiden Versuchen, die mit dem Kühlschmierstoff durchgeführt wurden.
Bei Versuch 1 (Bild 3a) zeigt das rechte Bild den Bruch des Werkzeugs nach 36 m zerspanender Bearbeitung. Im linken Bild ist der Bruch einer der Schneidkanten wohl die Ursache für den kompletten Werkzeugausfall.
Bei Versuch 2 (Bild 3b) zeigen die Bilder, dass der Bruch der Schneidkanten weniger dramatisch war. Allerdings weist der Ausbruch an der Werkzeugspitze darauf hin, dass das Werkzeug während des Zerspanvorgangs nicht richtig geschmiert wurde, was zu lokalen Spannungen und dem Ablösen des Schneidkantenmaterials des Fräswerkzeugs führte.
Bild 4 zeigt den Zustand der Schneidwerkzeuge in den beiden Versuchen, die mit äußerer MMS durchgeführt wurden. Für diese Tests war die Schneidkante des Werkzeugs progressiver als bei der Bearbeitung mit dem Kühlschmierstoff.
Bei Versuch 1 (Bild 4a) ist auf den Bildern ein Verschleiß auf der Spanfläche des Werkzeugs zu sehen.
Bei Versuch 2 (Bild 4b) zeigen die Bilder, dass das Fräswerkzeug an der Spitze bricht und dabei einen Bruch am Ende der Schneidkante verursacht.
Bei den Fräsversuchen mit innerer MMS zeigten die Ergebnisse schließlich einen eher gleichmäßig zunehmenden Verschleiß der Schneidkante im Vergleich zur Bearbeitung mit einem Kühlschmierstoff und bei der Bearbeitung mit äußerer MMS. Es gab überhaupt keine Schneidausfälle bei den beiden Bearbeitungsversuchen mit innerer MMS.
Bei Versuch 1 (Bild 5a) ist Verschleiß an der Schneidkante in Höhe der Zustelltiefe zu erkennen.
Dagegen zeigt sich bei Versuch 2 (Bild 5b) ein Mikrobruch an der Werkzeugspitze.
In Bild 6 ist der Standweg dargestellt, der von jedem der Schneidwerkzeuge mit der jeweiligen Schmiertechnik erreicht wurde. Es ist auch der mit den verschiedenen Wiederholungen erzielte Durchschnittswert für jedes Schmierverfahren angegeben.
Schlussfolgerungen aus den Tests
Es wurde demonstriert, dass die Werkzeugstandzeit unter Verwendung der inneren MMS erheblich gesteigert wird. Sie ist bedeutend länger als bei den beiden anderen Schmiertechniken.
Die Gesamtbetriebskosten (gemessen an der Bearbeitung von 1.000 cm3 Metall) sind in Tabelle 1 zusammengefasst.
Diese Tabelle zeigt deutlich, dass sich die Gesamtbetriebskosten aufgrund der LubriLean Minimalmengenschmierung verringern und bei der inneren MMS unter 54 Prozent der Gesamtkosten der Nassbearbeitung liegen.
Die Weiterentwicklung der MMS
Beim Tieflochbohren mit kleinen Werkzeugdurchmessern besteht die Herausforderung bei der MMS darin, dass sich der Gegendruck in den Kühlmittelkanälen bei zunehmender Bohrtiefe erhöht. Die Folge davon ist, dass das Aerosol aufgrund der geringen Druckdifferenz zwischen dem Lufteinlass und dem Aerosolauslass des MMS Gerätes nicht mehr so leicht erzeugt werden kann und sich dadurch das Risiko erhöht, dass das Werkzeug bricht und Ausschuss produziert wird.
Die SKF Ingenieure hatten es sich zum Ziel gesetzt, die Aerosolzuführung beim Tieflochbohren mit Werkzeugdurchmessern (D) unter 5 mm und Bohrtiefen über 25 x D zu verbessern. Sie integrierten ein Bypass-System in das SKF DigitalSuper Gerät, das die Druckdifferenz zwischen dem Lufteinlass und dem Aerosolauslass laufend überwacht. Sobald die Druckdifferenz unter den erforderlichen Wert absinkt, wird die Bypass-Regelung zur Druckentlastung der Aerosolleitung aktiviert. Sie sorgt dafür, dass das MMS-System genug Aerosol erzeugt, um die Schmierung von langen Werkzeugen mit kleinen Durchmessern bis zur Werkzeugspitze zu gewährleisten.
SKF hat das eigene MMS-System umfangreichen Tests unterzogen, um die erzielten Ergebnisse zu überprüfen und mit dem technisch komplizierteren Wettbewerbsgerät in Zweikanalbauweise zu vergleichen. Der Präzisionswerkzeughersteller Gühring stellte modernste Messgeräte zur Durchführung und Beurteilung dieser Tests zur Verfügung. Es wurden Sprühtests und quantitative Prüfungen auf einem speziellen MMS-Prüfstand von Gühring durchgeführt und die Sprüheigenschaften mit einer Kamera aufgezeichnet.
Außerdem wurden Tests mit AlSi7Mg, einem schwer zerspanbaren Werkstoff, und einem Bohrer mit einem Durchmesser von 4,5 mm und einer Länge von 200 mm bei Kühlmittelkanaldurchmessern von 0,6 mm gefahren.Anschließend wurde ein AlSi7Mg-Block mit einer Schnittgeschwindigkeit von 130 m/min und einem Vorschub von 0,2 mm pro Umdrehung bearbeitet. Das Ziel war es, die Bohrleistung und den Werkzeugverschleiß auf einer Gesamtstrecke von 100 m zu untersuchen. Mit dem SKF System wurden 18 ml Schmierstoff pro Stunde verbraucht. Nach einer Gesamtbohrstrecke von 100 m befand sich das Werkzeug immer noch in einem hervorragenden Zustand.
Nachgewiesene Vorteile
Beim Einsatz des SKF DigitalSuper Systems mit Bypass-Regelung und einem Eingangsdruck von 1 MPa (10 bar) zeigte sich, dass die Aerosolverteilung für das Tieflochbohren viel vorteilhafter ist als die bisher verwendeten Lösungsvarianten und als das Wettbewerbsprodukt. Die Videoaufnahmen belegten eine feine, gleichmäßige Aerosolzuführung zum Werkzeug, die erforderlich ist, um eine hohe Bearbeitungsqualität zu erzielen (Bild 7). Dies begünstigt eine gute Benetzung der Bearbeitungszone und führt zu einer Steigerung der Werkzeugstandzeit und der Werkstückqualität.
Die Zukunft von SKF LubriLean
Seit 2014 gehört SKF LubriLean zum SKF BeyondZero Produktportfolio. Werkzeugmaschinen mit SKF LubriLean Systemen werden bei führenden Automobilherstellern und in der Luft- und Raumfahrt erfolgreich eingesetzt. Bisher wurden MMS-Systeme hauptsächlich von europäischen und US-amerikanischen Werkzeugmaschinenherstellern eingebaut. Aufgrund des Erfolgs von MMS weltweit können SKF LubriLean Systeme nun auch in anderen Industrien und Ländern eingesetzt werden. MMS trägt auch zur Schonung der Umwelt bei und ermöglicht gleichzeitig wirtschaftliche und qualitativ hochwertige Bearbeitungsprozesse.
Die Entwicklung der MMS-Technologie und der MMS-Produktanwendungen schreitet rasant voran. Allerdings ist die Bearbeitungsleistung nicht nur vom MMS-System abhängig, sondern auch von der Werkzeugmaschine, dem Schneidwerkzeug, dem Werkstoff, den Bearbeitungsparametern usw. Alle Faktoren müssen aufeinander abgestimmt sein und zusammen optimiert werden. Daher ist für erfolgreiche Anwendungen eine starke technische Unterstützung und Zusammenarbeit mit anderen Technologiepartnern erforderlich. Dies ist der Ausgangspunkt für die nächste Phase in der Entwicklung und Verbreitung der MMS.
Was ist MMS?
Die Minimalmengenschmierung (MMS) wurde im Hinblick auf eine möglichst präzise Schmierung der Werkzeugschneide entwickelt, wobei nur so viel Schmierstoff zum Einsatz kommt, wie vom Bearbeitungsprozess unbedingt benötigt. Beim MMS-System (Bild 8) wird Bioöl in Form homogener Mikrotröpfchen zur Erzeugung eines Aerosols verwendet, das dann zur Wirkstelle der Werkzeugschneide transportiert wird. So erfolgt die Schmierung des Werkzeugs, des Werkstücks und des Spans über eine auf die Wirkstelle des Werkzeugs gerichtete Sprühdüse (äußere MMS) oder durch die Werkzeugmaschinenspindel und bis zur Werkzeugspitze reichende Kühlmittelkanäle (innere MMS). Der kleine Tröpfchendurchmesser sorgt dafür, dass die meisten Tröpfchen nicht durch Zentrifugalkräfte aus der Luft entfernt werden, wenn das Aerosol durch die rotierende Spindel strömt.
Je nach Zerspanungsverfahren, zu bearbeitendem Werkstoff und Maschineneinstellung wird normalerweise eine Schmierstoffmenge unter 50 ml/h benötigt. Die geringe Schmierstoffmenge hält Werkstücke und Späne trocken. Dadurch ergeben sich beachtliche Kosteneinsparungen, da weder die Werkstücke gereinigt noch die Späne aufbereitet werden müssen.
Selbst bei Drehzahlen über 20.000 Umdrehungen pro Minute sorgt die MMS-Technologie für eine zuverlässige Schmierung der Werkzeugschneide.
MMS wird in primären Bearbeitungsprozessen wie Drehen, Fräsen, Bohren und Formen eingesetzt. Eine Fertigungszelle kann dank der MMS Technologie mit einer kompakten Schmierungslösung statt einem komplizierten Kühlsystem geliefert werden.
SKF MMS-Systeme
SKF hat eine komplette Produktpalette an MMS-Systemen entwickelt. Das Angebot reicht von Systemen für die innere oder äußere Schmierung von kleineren oder größeren Werkzeugdurchmessern bis hin zu Geräten mit automatischer Steuerung oder manuell einstellbarer Regelung mit oder ohne automatische Überwachung des Aerosolzustands. In Bild 9 ist das gesamte Produktprogramm abgebildet.
Die neueste MMS-Geräteserie DigitalSuper besitzt ein eigenes Steuersystem und ist mit der modernen Feldbusanbindung ProfiBus oder ProfiNet für ein- oder doppelspindlige Bearbeitungs- und Drehzentren erhältlich.
Die Vario Baureihe ist für die innere und äußere Schmierung konzipiert und kann über die Werkzeugmaschinensteuerung gesteuert werden. Das VarioSuper System eignet sich für Bearbeitungs- und Drehzentren sowie für Spezialmaschinen. Das VarioPlus System ist manuell einstellbar und für Dreh-, Fräs- und Bohranwendungen geeignet; Dreh- und Bearbeitungszentren können mit diesem System nachgerüstet werden. Vario ist ein manuelles, einfach einsetzbares Gerät für allgemeine und spezielle Anwendungen (beispielsweise bei Mehrspindlern) und lässt sich an Drehmaschinen nachrüsten.
LubriLean Basic und Smart sind Einstiegsprodukte für die äußere MMS-Zuführung. LubriLean Basic eignet sich insbesondere für Werkzeugmaschinen, bei denen das Werkzeug von beiden Seiten benetzt werden soll (optional für bis zu acht Düsen), wie beispielsweise beim Fräsen. LubriLean Smart ist eine kosteneffiziente und einfach zu installierende Lösung. Mit diesem modularen System können Anwendungen, wie beispielsweise Transferstraßen und die zentrale Versorgung mehrerer Bearbeitungsstellen, flexibel und kostengünstig realisiert werden.
Die SKF LubriLean Systeme sind für Hersteller und Endkunden gleichermaßen interessant, da sie nicht nur bei neuen Werkzeugmaschinen, sondern auch für die Nachrüstung von Werkzeugmaschinen einsetzbar sind. Anstelle eines Hochdruckkühlschmiermittels kommt in den SKF LubriLean Systemen ein Aerosol zum Einsatz, das mit einem Pflanzenöl nach dem Venturiprinzip ohne Pumpe erzeugt wird. Dieses Verfahren führt zu einem niedrigeren Stromverbrauch, höheren Schnittgeschwindigkeiten und längeren Werkzeugstandzeiten. Ferner kommt es zu keinen Verschmutzungen im und um den Werkzeugmaschinenbereich, und bei den trockenen Werkstücken entfallen die Reinigungsarbeiten.
LubriLean und BeyondZero sind eingetragene Marken der SKF Gruppe