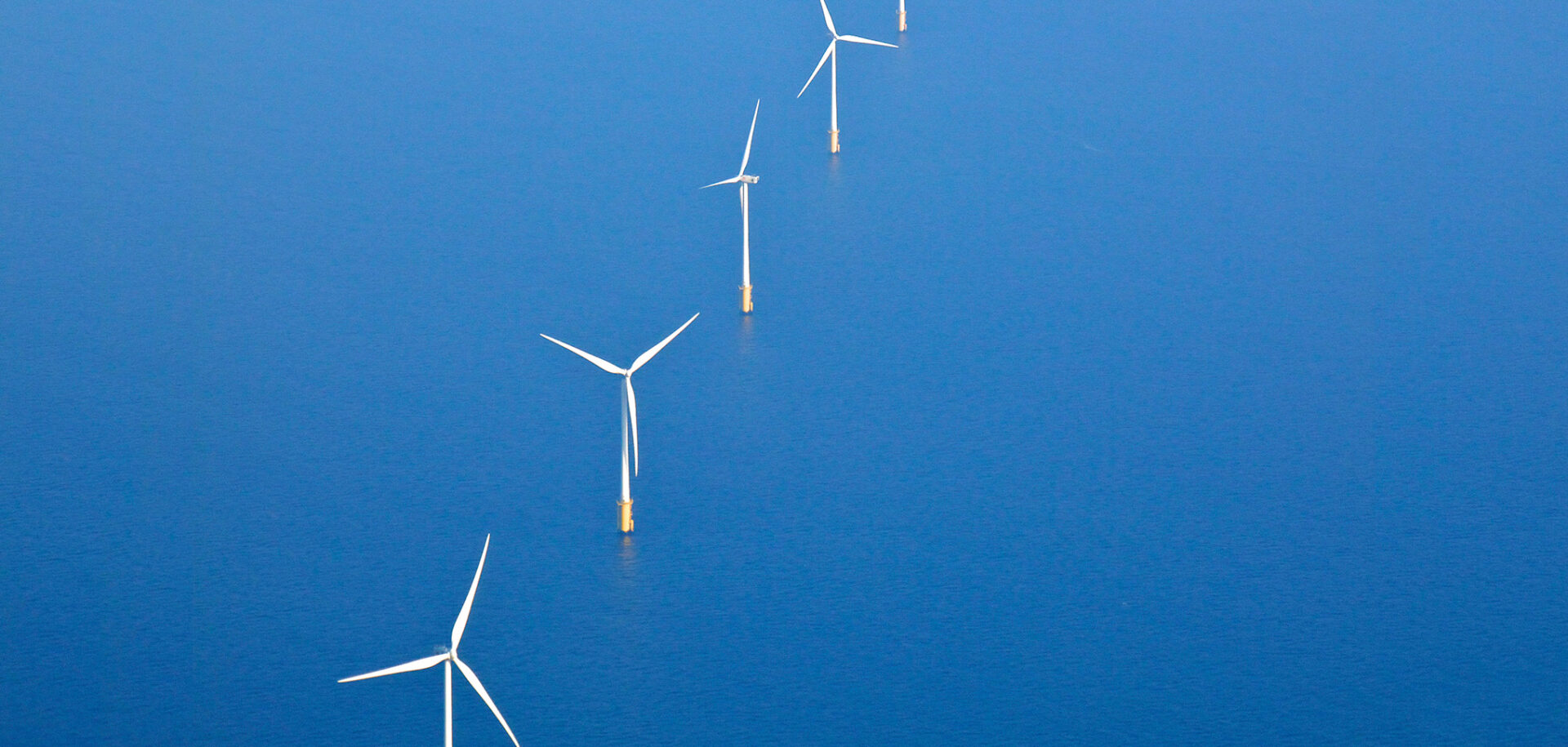
Neue Herausforderung
für Rotorlagerungen
in der 8-MW-Offshore-Klasse
Die „Round 3“, ein 33-GW-Offshore-Windparkprojekt in Großbritannien, gehört zu einer völlig neuen Offshore-Turbinengeneration.
Zusammenfassung
Zur Bewältigung der genannten Herausforderungen ist SKF im Bereich Rotorlager für Windkraftanlagen der 8-MW-Klasse sehr gut aufgestellt. Die heutige Vielfalt an unterschiedlichen Antriebssträngen wird in Zukunft noch größer werden. SKF versteht sich als Partner der Konstrukteure, Hersteller und Betreiber von Windkraftanlagen und verfügt über Fertigungsstätten in der ganzen Welt. Dort arbeiten Experten, die neue Antriebsstränge von der Idee bis zur Serienreife entwickeln.
Die Windkraftanlagen eines neuen 33-GW-Offshore-Projekts in Großbritannien haben sehr große Rotorblätter mit bis zu 90 Metern Länge sowie ein Naben- und Blattgewicht von rund 220 Tonnen. Der Überhang von der Nabe zur Turmmitte ist relativ groß, um die Freigängigkeit der durchbiegenden Blattspitzen zu ermöglichen. Ein Entwicklungsziel besteht darin, möglichst leichte und kompakte Antriebsstränge zu entwickeln, um die Gesamtkosten von Maschinen und Installation zu senken.
Um in derartigen Dimensionen möglichst hohe Leistungen bei möglichst geringen Betriebskosten erzielen zu können, bietet SKF für die unterschiedlichen Triebstrangkonzepte eine Vielzahl von Rotorlagerlösungen an.
Sphärische Lagerungen bei Turbinen mit Hauptgetriebe
In der 5-MW-Klasse hat sich vor allem die 2-Punkt-Lagerung mit einem Toroidalrollenlager (CARB) und einem Pendelrollenlager in getrennten Rotorlagergehäusen durchgesetzt (Bild 1). Das CARB Lager dient als reines Loslager, dessen axiale Verschiebefunktion durch die bordlosen Lagerringe realisiert wird. Im geeigneten Lagerabstand befindet sich generatorseitig das kleinere Pendelrollenlager, das die Funktion eines Festlagers übernimmt. Die spielbehaftete Lagerung in dieser Größenordnung erfordert künftig eine ganzheitlichere, dynamische Betrachtung des kompletten Antriebsstrangs und ist beispielweise für die Planetenträgerlagerung des Hauptgetriebes und der Getriebeaufhängung relevant.
Die winkelbeweglichen Lager gleichen hohe Wellendurchbiegungen, Winkelfehler und Versatz der beiden Lagergehäuse sehr gut aus. Die Rollen des Lagers haben selbsteinstellende Eigenschaften. Damit nehmen sie selbsttätig immer die Stellung ein, in der die Last über die Rollenlänge gleichmäßig verteilt ist (Bild 2). Selbst wenn Schiefstellungen oder Axialverschiebungen auszugleichen sind, ist die Tragfähigkeit der Lager sehr hoch.
Aufgrund der bisherigen positiven Erfahrungen ist die 2-Punkt-Lagerung, bestehend aus einem CARB Lager und einem Pendelrollenlager, prädestiniert, auch für eine neue modulare 8-MW-Maschine mit Hauptgetriebe angewandt zu werden. Auf Basis einer Hohlwelle ist ein CARB Lager mit einer Bohrung von 1.700 bis 1.800 mm und ein Pendelrollenlager mit einer Bohrung von 1.200 bis 1.300 mm einsetzbar. Auch in dieser Größe bietet SKF CARB Lager und Pendelrollenlager der nächsten Generation an. Diese haben deutlich verbesserte Leistungsparameter hinsichtlich Ausdauer, Drehvermögen und dynamischer Belastbarkeit. Ihre gesteigerte Leistungsfähigkeit beruht im Wesentlichen auf verbessertem Wälzlagerstahl für höhere Ermüdungsfestigkeit, optimierter Wärmebehandlung mit dem X-Bite-Verfahren (spezielles bainitisches Durchhärten) und einer gleichmäßigen Lastverteilung innerhalb des Lagers.
SKF ist aufgefordert, auch für diese Lagergrößen individuell konstruierte Gehäuse anzubieten. Diese sind auf der Basis von Betriebslasten und mit Berücksichtigung der Gehäuseverformung optimal auf die Lastverteilung konstruiert (Bild 3). Außerdem können schleifende SKF Kontaktdichtungen oder Labyrinthdichtungen integriert werden, und zwar je nachdem, ob als Schmiermedium Fett oder zukünftig Öl verwendet wird.
„Steife“ Lagerungen bei Turbinen mit Hauptgetriebe
Die Lagerung besteht aus einem Zylinderrollenlager und einem zweireihigen Kegelrollenlager (Bild 4) und hat sich seit Jahren in getriebelosen Anlagen bewährt. Diese Lagerkonstruktion bietet interessante Möglichkeiten für Hauptlagerungen – auch für eine modular aufgebaute 8-MW-Getriebemaschine.
Anspruchsvoller gegenüber sphärischen Lagerungen sind die Fertigungsgenauigkeit sowie die Form- und Positionstoleranzen beider Lagersitze zueinander. Diese Lagerung erfordert ein langes gemeinsames Rotorlagergehäuse, bei dem beide Lagersitze in einer Aufspannung gefertigt werden und damit radialen Versatz ausschließen (Bild 5).
Mithilfe der Berechnungssoftware „SKF SimPro Expert“ kann die Verformung der Rotorwelle sowie das Lagergehäuse inklusive Maschinenträger auf schädlichen Einfluss für die Lastzone und Lagerschiefstellung untersucht werden.
Erfahrungsgemäß müssen die Gehäusekonstruktion optimiert und die Lagerlaufbahnen profiliert werden, um die Kantenspannungen auf ein vertretbares Niveau zu bringen. Zur Auswahl für eine 8-MW-Turbine stehen grundsätzlich ein- und zweireihige Zylinderrollenlager mit schlanken Rollensätzen und formoptimierten Käfigen mit Lagerbohrungen größer 1.700 mm.
Als generatorseitiges Festlager bietet sich ein zweireihiges Kegelrollenlager in X-Anordnung an. Für große Bohrungsdurchmesser (> 1.000 mm) ergibt sich somit der Bedarf, den Einsatz von Einheiten im TDI-Design (einteiliger Innenring) als mögliche Alternative zu zwei einreihigen Kegelrollenlagern konstruktiv zu untersuchen.
Im Vergleich zu den „flexiblen“ CARB und Pendelrollenlagerungen können die „steifen“ Zylinder- und Kegelrollenlagerungen etwas kompakter, das heißt kürzer, ausgeführt werden.
Ebenfalls als „steife“ 2-Punkt-Lagerung bei Turbinen mit und ohne Hauptgetriebe gilt eine in O-Anordnung angestellte Lagerung mit zwei einzelnen Kegelrollenlagern. Auf Basis von zwei individuell ausgearbeiteten Kegelrollenlagern mit Bohrungsdurchmessern von rund 2.200 mm, unterschiedlichen Druckwinkeln und Tragzahlen lässt sich eine relativ kompakte Rotorlagereinheit im XXL-Format mit gegossener Rotorhohlwelle und einteiligem Gehäuse für eine 8-MW-Turbine realisieren (Bild 6).
Kompaktheit und Gewichtsreduzierung sind auch hier zentrale Punkte. Daher ist es erforderlich, die komplette Lageranordnung auf Montagemöglichkeiten, Steifigkeiten, Verformung und Einfluss auf die Vorspannung beider Kegelrollenlager frühzeitig zu untersuchen. Durch den relativ geringen Lagerabstand in der O-Anordnung und den großen Ringdurchmesser muss mit einem Vorspannungsverlust und einem damit verbundenen Einfluss auf die Lagerlebensdauer gerechnet werden. Das ist eine Herausforderung. Ein Wechsel hin zur Ölschmierung könnte bei dieser Lagerung eine geeignete Maßnahme sein, um das Temperaturniveau (Wärmeausdehnung) des vorgespannten Rotorlagersystems kontrolliert zu steuern.
SKF Nautilus Lager in Turbinen mit Hauptgetriebe
In den vergangenen Jahren wurden sehr kompakte Antriebsstränge mit einem teilintegrierten SKF Nautilus Lager in den Leistungsklassen von 2 bis 6 MW bei einem Rotordurchmesser von etwa 125 m realisiert. Der Maschinenträger umschließt dabei rotorseitig das Momentenlager (Bild 7). Alle Kräfte und Biegemomente werden bestenfalls von der Rotorwelle über das Hauptlager auf den Maschinenträger abgeleitet. Das Momentenlager sitzt auf einer kurzen Rotorwelle zwischen Nabe und Getriebe.
Dieses in O-Anordnung angestellte, zweireihige Kegelrollenlager bildet zusammen mit dem großen Lagerdurchmesser die Basis für die große Stützweite zur Aufnahme und Übertragung der hohen Biegemomente. Der innere 45°-Druckwinkel und der relativ kleine Kegelrollenwinkel treffen sich im Apex-Punkt und sorgen für ein pures Abrollen im Wälzkontakt ohne schädliches Gleiten an den Rollenenden. Die Konstruktion mit SKF Segmentkäfigen sorgt für die erforderliche Flexibilität, damit die erheblichen Systemverformungen unter den hohen Lasten abgefangen werden können.
Bei Rotordurchmessern von bis zu 180 m in der zukünftigen 8-MW-Klasse wird der Überhang von der Nabenmitte zur Turmmitte sogar noch größer, um die Freigängigkeit der durchbiegenden Blattspitzen zu gewährleisten. Damit wird genügend Gondellänge zur Unterbringung eines modularen Antriebsstrangs mit zweifach gelagerter Rotorwelle und angeflanschtem Hauptgetriebe zur Verfügung stehen. Sollte ein SKF Nautilus Lager eingesetzt werden, ist es zielführend, den Nabenüberhang zu verkürzen, den Rotoranbindungspunkt zum Momentenlager möglichst klein zu halten und den Schwerpunkt des 80- bis 110-Tonnen-Getriebes möglichst in der Turmmitte oder darüber hinaus wirken zu lassen.
Ähnliches gilt für 8-MW-Hybridturbinen-Konzepte, bei denen der komplette Antriebsstrang (Hauptlager, Getriebe und Generator) in einer Gehäuseeinheit zusammengeführt ist. Bei der Integration eines Rotorlagers innerhalb des Getriebes gilt es auch weiterhin, das (Planeten-)Getriebe von den Verformungen des Rotorlagers und der Umgebungskonstruktion zu entkoppeln. Damit wird gewährleistet, dass die Eingangswelle ein reines Drehmoment (bis zu 10.000 kNm nominal) erfährt und der exakte Zahneingriff nicht gestört wird.
SKF Nautilus Lager in Direktantrieben
Die Auswahl der Lagertypen und deren Anordnung haben Einfluss auf die Gesamtverformung sowie die Steifigkeit des Antriebsstrangs und damit auch auf den vorzuhaltenden Luftspalt in der elektrischen Maschine, auf die Magnetstärken und die Magnetmasse. Eine Luftspaltreduzierung von nur einem Millimeter kann bereits eine gewaltige Kosteneinsparung bewirken und die Effizienz der Turbine in ihrer Gesamtlebensdauer maßgeblich steigern.
Neben den Rotorlagerkonzepten mit den beiden Kegelrollenlagern sowie dem zweireihigen Kegelrollenlager und Zylinderrollenlager, die vorrangig auf stillstehenden Achszapfen montiert werden, ist vor allem die Variante mit dem Momentenlager weltweit auf dem Vormarsch (Bild 8). Das Momentenlager dient dabei als zentrales Bindeglied zwischen Nabe und einem langsam laufenden Generator, der vor dem Turm platziert ist („Bug-Generator“).
Die Varianten eines SKF Nautilus Momentenlagers erfordern eine detaillierte Ausarbeitung der Lagerleistung und Luftspaltoptimierung (Exzentrizität, Einfederung, Winkelversatz) zur Verformung der Gesamtkonstruktion. Daneben stehen auch sehr pragmatische Überlegungen bezüglich der Zugänglichkeit zum Dichtungswechsel sowie zur Schmierstoffein- und Altfettausbringung. SKF bietet hierzu entsprechende Großdichtungen in einteiliger und geteilter Ausführung an.
Hohe statische und dynamische Tragzahlen sind erforderlich, um die SKF Standards und die externen DNV-GL-Zertifizierungsanforderungen für Windkraftanlagen zu erfüllen und eine 20-jährige Lagerleistung auch weiterhin gewährleisten zu können.
Für die 8-MW-Klasse werden noch höhere Tragzahlen benötigt, die mit größeren Rollen und Ringquerschnitt realisiert werden. Daher ist SKF aufgefordert, unter Berücksichtigung der physikalischen Grenzen weitere Verbesserungen an den Lagern vorzunehmen und neue Dichtungen für die Ölschmierung sowie neue Schmiersysteme zu entwickeln.