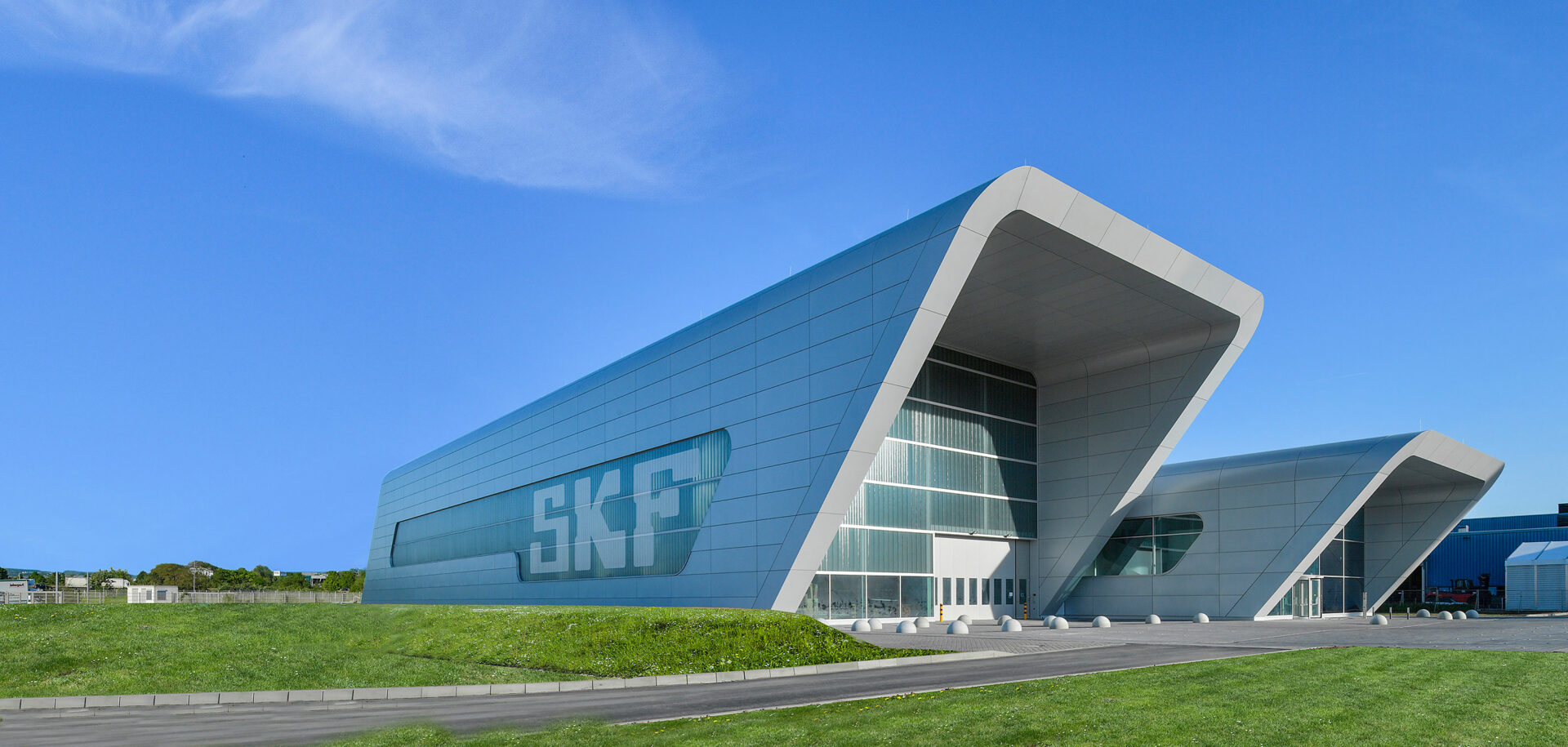
Grenze der Belastbarkeit
Im Sommer hat SKF in Schweinfurt das „Sven Wingquist Test Center“ offiziell eingeweiht. Es ist das leistungsfähigste Großlager-Prüfzentrum der Welt. Die technologische Pionierleistung wird dazu beitragen, künftige Großlager-Generationen weiter zu verbessern – und sie zugleich viel effizienter und ressourcenschonender zu produzieren als bislang möglich. Unter dem Strich sollen die Kunden von optimierten Lösungen profitieren. Zu diesem Zweck werden zwei gigantische neue Teststände die Prüflinge ordentlich „in den Schwitzkasten“ nehmen.
SKF verfügt über ein breites Portfolio an extrem leistungsfähiger Software zur Berechnung und Simulation von Wälzlagerungen aller Art. Darunter befinden sich auch hochkomplexe Systeme, die das Lagerverhalten in einer virtuellen Umgebung eingehend untersuchen können: Mit einem Tool wie „SimPro Expert“ bspw. lässt sich das Verhalten des gesamten Welle-Lager-Gehäuse-Systems unter Berücksichtigung der exakten inneren Geometrie der Lager betrachten. Unter anderem gibt das Programm die Verkippung der Lager und die daraus resultierenden Kontaktspannungen sowie die berechnete Lagerlebensdauer anhand verschiedener Methoden aus. Darin stecken nicht nur viele Jahre an Forschungs- und Entwicklungsarbeit, sondern auch Dekaden an Praxis-Erfahrung. Ähnliches gilt für ein noch mächtigeres Instrument wie BEAST, das die SKF Ingenieure nutzen, um die dynamischen Verhältnisse innerhalb eines Lagers detailliert nachzubilden. Im Grunde ist BEAST sogar eine Art „virtueller Prüfstand“, der eingehende Untersuchungen von Kräften und Momenten in einem Lager unter beliebigen Belastungen erlaubt.
Software zu soft
So ausgeklügelt die entsprechende Software auch sein mag, bislang ist kein Simulationsprogramm der Welt imstande, sämtliche Prozesse in Großlagern wirklichkeitsgetreu abzubilden. Eindeutiges Indiz: Noch immer kommt es in der harten Realität vereinzelt zu vorzeitigen Ausfällen von Großlagern, obwohl diese nicht nur mit äußerster Akribie berechnet worden waren, sondern oft sogar über „konstruktive Sicherheitsreserven“ verfügten. In der Praxis treten demnach gewisse Phänomene auf, die von den „Ursache-Wirkung-Algorithmen“ aktueller Simulationsmodelle nicht ausreichend berücksichtigt werden.
Zusammenfassung
Gegenwärtig ist kein Simulationsprogramm der Welt im Stande, sämtliche dynamischen Prozesse im praktischen Betrieb von Großlagern realitätsgetreu abzubilden. Zwei neuartige Prüfstände im hochmodernen Sven Wingquist Test Center von SKF werden Erkenntnisse ans Tageslicht fördern, mit denen sich die derzeit verfügbaren Simulationsmodelle im Hinblick auf eine größere Realitätsnähe vervollkommnen lassen. Das gewonnene Know-how wird in die Produktentwicklung einfließen und dazu beitragen, dass Großlager-Generationen bei möglichst geringem Gewicht und minimaler Reibung in ihrer jeweiligen Anwendung ein Maximum an Haltbarkeit erzielen. Alles zusammen schont Ressourcen – nicht nur während der Tests sowie in der Herstellung, sondern auch beim Einsatz künftiger SKF Großlager. Davon werden Umwelt und Anwender gleichermaßen profitieren.
Unter anderem um solchen bislang rätselhaften Schadensursachen auf die Schliche zu kommen, hat SKF am Standort Schweinfurt rund 40 Millionen Euro in das leistungsfähigste Großlager-Prüfzentrum der Welt investiert. In dem futuristisch anmutenden Zwillingsgebäude werden zwei riesige Prüfstände die zu testenden Lager an ihre absoluten Belastungsgrenzen treiben.
Wind-Kraft-Protz
Der „Superman“ unter den beiden neuen Prüfständen ist der weltweit erste, der nicht nur ein einzelnes Windenergielager mit bis zu sechs Metern Außendurchmesser, sondern gleich die komplette Lagerungseinheit testen kann – also mitsamt Umbauteilen des jeweiligen Kunden. Der rund neun Meter breite, 11 Meter hohe und acht Meter tiefe Gigant wiegt etwa 700 Tonnen. Er verfügt über 64 radial und axial angeordnete Zylinder, die enorme dynamische Kräfte im Bereich von mehreren Meganewton entwickeln können.
Die Hydraulikzylinder wirken zunächst auf einen überdimensionalen „Stahl-Diskus“ ein, der im Inneren des Prüfstandes rotiert (Bild 3). Diese massive Scheibe hat einen Durchmesser von ca. sieben Metern und bringt allein 125 Tonnen auf die Waage. Sie überträgt die Kräfte aus den Hydraulikzylindern auf das zu prüfende Lager, indem der Prüfling per Adapter an der Scheibe befestigt wird.
Was nach unnötigem Umweg klingt, hat in Wirklichkeit einen entscheidenden Vorteil: Dank dieses innovativen Konzepts werden die auf den Prüfling einwirkenden Kräfte nicht durch die „Eigen-Stabilität“ eines lastausübenden Lagers beschränkt. So können die 64 Zylinder in Kooperation mit der Scheibe über alle Achsen hinweg Kräfte entfesseln, die in ihrer Kombination um ein Mehrfaches höher liegen als bei der bislang stärksten Großlager-Prüfanlage. Außerdem erreicht der neue Prüfstand von SKF – gemessen an den Dimensionen der Prüflinge – auch noch sehr hohe Umdrehungsgeschwindigkeiten.
Zeitraffer-Tests
Die einzigartige Kombination aus Dynamik, maximalen Kräften, Biegemomenten und Drehzahlen hat einen kundenorientierten Grund: Damit sich Windenergieanlagen für ihre Betreiber rentieren, sollen die darin verbauten Großlager möglichst 20 Jahre und länger zuverlässig laufen.
Diese 20 Jahre – und alle in dieser Zeit denkbaren Belastungen – wird der neue Prüfstand dank eines beschleunigten Verfahrens innerhalb weniger Wochen sehr realitätsgetreu abbilden können. Das spart nicht nur viel Zeit und Geld, sondern auch Energie; zumal die Abwärme der Testanlage per Wärmerückgewinnung für das Prüfzentrum selbst sowie die angrenzende Großlager-Fabrik genutzt wird. Unter anderem deshalb hat das Bayerische Staatsministerium für Wirtschaft und Medien, Energie und Technologie den Bau dieses hocheffizienten „Stresstesters“ mit rund 1,9 Mio. Euro gefördert.
Kräfte unter Kontrolle
Damit der mächtige Prüfstand seine gewaltigen Kräfte kontrolliert auf die Prüflinge aufbringen kann, sind seine unteren Gehäusesegmente mit rund zweihundert M80-Gewindebolzen und einer Vorspannkraft von mehreren Meganewton auf ihren Sockeln fixiert worden. Die Sockel, in denen die Schrauben stecken, sind Bestandteil eines 3.000 Tonnen schweren Fundaments, das vom leicht anmutenden Gebäude entkoppelt ist, um keine störende Wechselwirkung mit dem Gebäude zu erzeugen.
Angesichts des massiven Unterbaus ist die Präzisionsarbeit an der Schnittstelle zwischen den Sockeln und den Gehäuse-Unterteilen umso erstaunlicher: Die Auflageflächen weisen über eine Distanz von rund zehn Metern nur wenige Zehntel Millimeter Abweichung bei der Ebenheit auf (Bild 4).
Kleiner, flexibler, schneller
Im direkten Vergleich mit seinem „großen Bruder“ wirkt der kleinere der beiden neuen SKF Prüfstände zwar weniger monumental, aber auch er hat es in sich: In seinem Prüfkopf stecken vier Axial- und zwei Radialzylinder, die mit Hilfe von Außen- und Innenringadaptern auf unterschiedliche Großlager-Designs einwirken können. Seine Prüflinge können beispielsweise aus Anwendungsbereichen wie dem Schiffbau, dem Bergbau oder auch der Zement- und Stahlindustrie stammen. Das macht ihn außerordentlich vielseitig einsetzbar. Seiner „Flexibilität“ zum Trotz ist natürlich auch dieser Teststand ein äußerst stabiles Ungetüm: Sein Eigengewicht liegt bei rund 300 Tonnen.
Diese Anlage entwickelt Kräfte von gut einem halben Dutzend Meganewton (etwa so viel wie ein einzelnes Triebwerk der Saturn V-Mondrakete) und erreicht Rotationsgeschwindigkeiten von über 200 min-1. Durch die Kombination derartiger Lasten und Drehzahlen ist selbst der kleinere der beiden neuen SKF Prüfstände weltweit konkurrenzlos. Mit seinen einzigartigen Fähigkeiten wird auch er maßgebliche Potenziale zur Energie- und Materialeinsparung bei der Herstellung künftiger Großlager aufzeigen. Das ist einer der Gründe dafür, dass dieser Prüfstand in das Umweltinnovationsprogramm des Bundesministeriums für Umwelt, Naturschutz, Bau und Reaktorsicherheit aufgenommen und mit ca. 1,6 Mio. Euro gefördert wurde.
Schmierung im Grenzbereich
Der kleinere „Kraftprotz“ im Sven Wingquist Test Center weist noch eine weitere Besonderheit auf: Er verfügt über ein spezielles Schmiersystem der SKF Lubrication Systems Germany GmbH. Normalerweise sorgen deren Geräte automatisch dafür, dass Wälzlager in verschiedensten Anwendungen zum richtigen Zeitpunkt mit der richtigen Menge an Schmierstoff optimal versorgt werden. Die Sonderanfertigung für das Prüfzentrum kann aber auch das genaue Gegenteil: Sie kann den Prüfling in puncto „Mangelschmierung“ bis an die äußersten Grenzen treiben. Daraus lassen sich wichtige Erkenntnisse gewinnen, um kommende Großlager viel robuster auszuführen.
Das rund 6 Meter breite und etwa 1,6 Meter tiefe Aggregat fasst 3.000 Liter Schmieröl und bringt damit ein Gesamtgewicht von 7,2 Tonnen auf die Waage. Im Grunde handelt es sich dabei um einen Technologietransfer aus der Papierindustrie. Für die speziellen Anforderungen im Prüfzentrum haben die Schmiersystem-Experten von SKF jedoch diverse Modifikationen vorgenommen. Sie betrafen nicht nur die optische Gestaltung des Geräts oder die vergleichsweise ungewohnten Lärmschutz-Maßnahmen.
Knackpunkt Temperatur
Um das zu testende Lager nicht nur extremen Lasten, sondern auch extremen Schmierbedingungen auszusetzen, hat SKF das System auf Öltemperaturen ausgelegt, die um den Faktor Zwei über den normal üblichen liegen. Aus diesem Temperaturspektrum können enorme tribologische Strapazen für den Prüfling resultieren: Laut Faustregel halbiert sich die Viskosität des Schmieröls bei jeder Steigerung der Temperatur um 10 °C. Damit die Schmieranlage selbst während einer solchen „Hitzeschlacht“ keinen Schaden nimmt, ist sie mit einem Kühlsystem auf Basis von Plattenwärmetauschern ausgestattet worden.
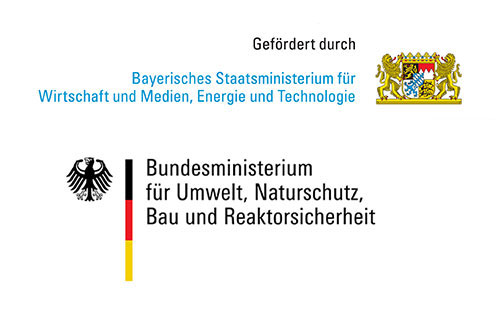
Gefördert durch
Der größere Prüfstand wurde vom Bayerischen Staatsministerium für Wirtschaft und Medien, Energie und Technologie mit rund 1,9 Mio. Euro gefördert, während der neue Prüfstand für andere Schwerindustrie-Anwendungen durch das Umweltinnovationsprogramm des Bundesministeriums für Umwelt, Naturschutz, Bau und Reaktorsicherheit mit ca. 1,6 Mio. Euro gefördert wurde.
Präzise Messungen am Prüfling
Von der Versorgungsstation aus gelangt das Schmieröl über ein Dutzend Leitungen zum Prüfling. An der zwischengeschalteten Verteilkonsole lässt sich sehr präzise dosieren, wie viel Öl pro Leitung zu welchem Schmierpunkt befördert wird. Dadurch können die Tester auch in punkto „Schmiermittel-Menge“ die schwierigsten Bedingungen bei verschiedensten Lasten hervorrufen. Darüber hinaus erlaubt es die variable Dosierung in Kombination mit der Vielzahl der Schmierpunkte, die Ölverteilung bzw. den internen Fluss im Prüfling extrem „lokal“ zu untersuchen. Zu diesem Zweck verfügt die Vorrichtung zur Aufnahme des Prüflings über ein ganzes Arsenal an weiteren Sensoren. Diese Sensoren erfassen nicht nur lokale Temperaturen und deren Trends, sondern bspw. auch Schwingungen und Kräfte sowie die Position kritischer Komponenten. Letztlich erfahren die SKF Experten dadurch, wo genau unter welchen Bedingungen welche dynamischen Effekte im Lager auftreten.
In den kommenden Monaten werden die SKF Ingenieure alles daran setzen, dass die prüftechnische Pionierleistung die extrem hohen Erwartungen an die Entdeckung bislang noch verborgener „Großlager-Geheimnisse“ auch Schritt für Schritt erfüllt. Derzeit arbeiten sie beispielsweise an der Validierung der massiven Hardware und der Kalibrierung der sensiblen Messtechnik.