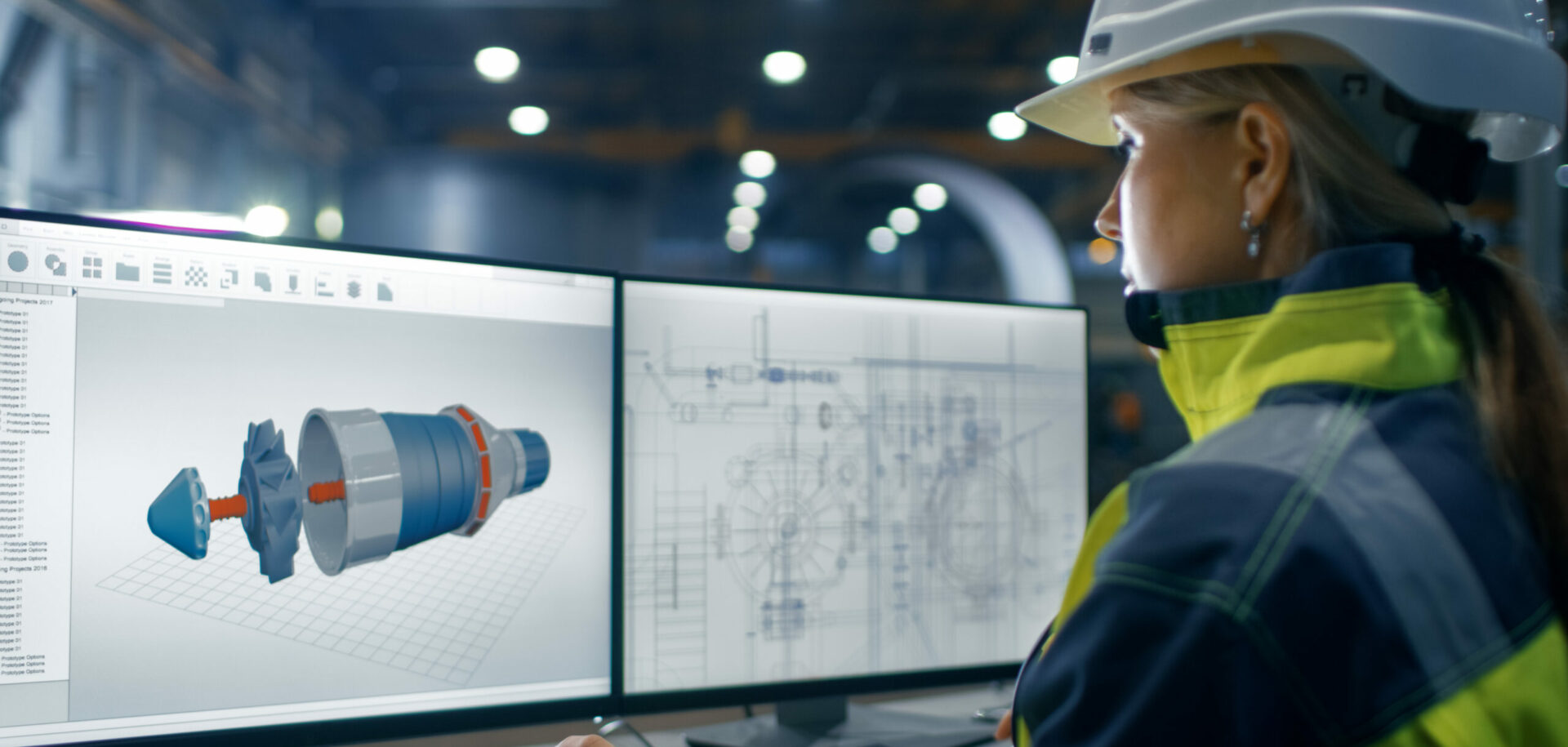
Oberflächenzerrüttung verstehen und vermeiden
In vielen Industrieanwendungen mit geschmiertem Roll-/Gleitkontakt, wie Wälzlager, hat sich mit der Zeit die Leistungsdichte aufgrund der Nachfrage nach höherer Effizienz, Gewichts- und Kostenreduzierung (d. h. Downsizing) ständig erhöht. Daneben hat die Schwere der Anwendungsbedingungen durch höhere Belastung in Verbindung mit höheren Temperaturen, dünneren Schmierfilmdicken und/oder Grenzschmierbedingungen zugenommen. Dies kann zu einer Zerrüttung der Oberflächen in den betreffenden Maschinenkomponenten führen [1].
In vielen Industrieanwendungen mit geschmiertem Roll-/Gleitkontakt, wie Wälzlager, hat sich mit der Zeit die Leistungsdichte aufgrund der Nachfrage nach höherer Effizienz, Gewichts- und Kostenreduzierung (d. h. Downsizing) ständig erhöht. Daneben hat die Schwere der Anwendungsbedingungen durch höhere Belastung in Verbindung mit höheren Temperaturen, dünneren Schmierfilmdicken und/oder Grenzschmierbedingungen zugenommen. Dies kann zu einer Zerrüttung der Oberflächen in den betreffenden Maschinenkomponenten führen [1].
Technik
Oberflächenzerrüttung zeigt sich anfangs in einer Farbveränderung bzw. in einem matten Erscheinungsbild der Oberfläche (sogenannte Graufleckigkeit). Symptome die sich mit zunehmendem Schaden verstärken. Unter dem Mikroskop weisen die betroffenen Oberflächenbereiche winzige Mikroschälungen, Mikrorisse oder Mikrogrübchen auf (Bild 1).
S. Way [2] war einer der ersten, der die Oberflächenzerrüttung im Schmierkontakt untersucht hat. Er stellte fest, dass polierte Kontaktscheiben das Risiko der Oberflächenzerrüttung verringerten. Später erkannte P.H. Dawson [3] die Bedeutung einer guten Schmierung und einer geringen Rauheit zur Vermeidung oder Verzögerung der Oberflächenzerrüttung.
Heute wird allgemein anerkannt, dass es sich bei der Oberflächenzerrüttung um das Phänomen eines Oberflächenschadens handelt, der mit schlechten Schmierbedingungen [4] einhergeht, also mit der Entstehung hoher lokaler Reibung und Spannungen im Oberflächenrauheitsbereich. Dieses Phänomen war Gegenstand zahlreicher experimenteller und numerischer Untersuchungen [5-7]. Andere Oberflächenphänomene wie leichter Materialabtrag (milder Verschleiß) [8, 9] stehen im Wettbewerb mit der Oberflächenzerrüttung während der Einlaufphase und in späteren Stadien, wobei die Oberfläche durch Abtragen der geschädigten Materialschichten für Mikrorisse weniger anfällig wird. Auf der Grundlage der Wechselwirkung zwischen der Entstehung von Oberflächenmikrorissen und leichtem Materialabtrag hat SKF kürzlich detaillierte Oberflächenzerrüttungsmodelle [10] entwickelt, um kritische Parameter zu untersuchen und Oberflächenschäden vorherzusagen.
In den folgenden Abschnitten werden die mechanischen Aspekte (Schmierung, Rauheit, Reibung und leichter Materialabtrag) beschrieben, die, wie man annimmt, eine bedeutende Rolle bei der Oberflächenzerrüttung spielen. Es werden darüber hinaus auch Empfehlungen zur Verbesserung der Kontaktbedingungen und zur Verringerung des Oberflächenzerrüttungsrisikos gegeben. Die Chemie, genauer gesagt die Tribochemie, spielt hier sicher eine Schlüsselrolle [8, 9] durch Beeinflussung des Materialabtrags und/oder des Grenzreibungskoeffizienten während der Einlaufphase und danach.
Oberflächenreibung
Da die Oberflächenzerrüttung stark vom Schmierregime, insbesondere Grenz- und/oder Mischreibungsbedingungen, beeinflusst wird, spielt die „Festkörper- oder Grenzreibung“ folglich eine sehr große Rolle. Beim vollgeschmierten Kontakt (Flüssigkeitsreibung) wird die Reibkraft durch Abscheren des Schmierfilms aufgrund von Gleiten eingeleitet. Die Schubspannungen (und folglich die Reibkraft) hängen von der Rheologie des Schmierstoffs ab und folgen dem schematischen Pfad wie in Bild 2a gezeigt. Wenn jedoch Rauheitsspitzen in Kontakt sind, dann verhält sich in diesen Bereichen die Reibung wie bei Festkörperreibung (oder Grenzreibung). D. h. in etwa wie bei Coulomb’scher Reibung (Bild 2b), wobei beim reinen Abrollen der Wert „Null“ ist und ein nahezu konstanter Wert erreicht wird sobald Gleiten eintritt. Zu beachten ist, dass in beiden Fällen ein höherer Gleitanteil nicht unbedingt eine höhere Reibung bedeutet. Bei (Grenz- oder) Mischreibung werden die sich kontaktierenden Rauheitsspitzen keine Reibkräfte erfahren, es sei denn, es tritt ein geringer Anteil von Gleiten, ungleich „Null“, wie in Bild 2b dargestellt, auf. „Reines Abrollen“ gibt es jedoch in der Praxis nicht. Reale Kontakte haben, selbst wenn sie unter „nominalen reinen“ Abwälzbedingungen laufen, immer einen gewissen Gleitanteil, der zu geringer Gleitreibung führt, und folglich ein mögliches Oberflächenzerrüttungsrisiko birgt. Die im SKF Engineering & Research Centre in Nieuwegein (Niederlande) durchgeführten Versuche zeigten, dass ein nominales reines Abrollen ebenfalls zur Oberflächenzerrüttung führen kann. Unter gleichen Bedingungen und mit der gleichen Anzahl Zyklen wurde bei einem Anstieg des Grenzreibungskoeffizienten auch eine Zunahme der Oberflächenzerrüttung festgestellt. Somit kann gesagt werden, dass die Grenzreibung ein sehr wichtiger Einflussparameter zur Begünstigung von Mikrorissen an der Oberfläche darstellt, wenn der Kontakt unter Grenz- oder Mischreibungsschmierbedingungen läuft.
Die Grenzreibung hängt stark vom verwendeten Schmierstoff und seinem Additivpaket ab. Der Wert des Grenzreibungskoeffizienten kann aus den mit dem Kugel-Scheibe-Tribometer gemessenen Stribeckkurven ermittelt werden. Diese Versuche laufen normalerweise mit einem festen Nominalschlupf im Kontakt (2 – 5 %) bei stetiger Erhöhung der hydrodynamisch wirksamen Geschwindigkeit. Bei einem Kugel-Scheibe-Tribometer ist der Grenzkoeffizient für Reibung der erste Punkt auf der Stribeckkurve (Bild 3). Es sei angemerkt, dass die hier gemessenen Reibungskoeffizienten Durchschnittswerte innerhalb des Kontakts darstellen.
Bedeutung von Schmierung und Rauheit
Bei Wälzlagern spielt die Schmierung für das Lebensdauerverhalten eine bedeutende Rolle. Deshalb berücksichtigen die SKF Lebensdauermodelle den Einfluss des Schmierungsparameters к. Die Bedeutung der Schmierung und Rauheiten bei Oberflächenschäden ist sehr stark beeinflusst durch die lokalen Reibungskräfte und Spannungskonzentrationen (im Rauheitsbereich). Bei Grenz- oder Mischreibung bestimmen Unregelmäßigkeiten/Störgrößen in der Oberfläche (z. B. Rauheiten oder Eindrückungen, Bild 4) die Verteilung der sich kontaktierenden und geschmierten Stellen innerhalb des Kontakts. Außerdem müssen Traktionsdiskontinuitäten und Spannungsüberhöhungen (Bild 5) berücksichtigt werden. Hohe Rauheiten (oder hohe Profilsteigungen) führen zu hohen Kontaktdrücken, Zugkräften und fördern örtliche Zusammenbrüche des Schmierfilms, hohe Kontaktdrücke und Zugkräfte. Dies führt zu Spannungsüberhöhungen und Diskontinuitäten in diesen Bereichen.
Aus den Versuchsergebnissen und den theoretischen SKF Modellen geht hervor, dass die Oberflächenzerrüttung zunächst in den Bereichen hoher Druckdiskontinuitäten (Hochdruckgradienten) und erhöhten Rauheiten auftritt, unter anderem im Bereich von Rillen/Bearbeitungsstrukturen, Rauheitsspitzen/-täler oder Eindrückungen (Bild 4). Dabei stellt man eher unerwartet fest, dass der Oberflächenzerrüttungsprozess meistens auf der glatteren der beiden Gegenflächen beginnt.
Wechselwirkung zwischen Rauheitsorientierung und Reibungsrichtung
Versuche zeigen, dass bei Grenz- oder Mischreibung eine transversale (quer zur Roll-/Gleitrichtung verlaufende) Rauheitsausrichtung stärker zur Oberflächenzerrüttung neigt als eine longitudinale Rauheitsausrichtung (Bild 6); dieselbe Feststellung wird in [5] gemacht. Dies ist eine interessante Beobachtung, da unter vollelastohydrodynamischen (EHD) Schmierbedingungen tranversale Rauheiten einen besserenSchmierfilmaufbau erzeugen kann, jedoch auch zu Druckspitzen führt. Bei Grenz- oder Mischreibung sind die wirksamen Mechanismen jedoch unterschiedlich.
SKF fand heraus, dass die normal zur Rauheitsausrichtung verlaufende Reibkraftkomponente die Spannungskonzentration im Materialbereich des Rauheitskontakts der raueren Oberfläche und an den Mikrokontakträndern der glatteren Oberfläche (Bild 5) wesentlich erhöhen kann. Durch diesen Effekt kann der Schaden und die Oberflächenzerrüttung verstärkt werden; ihre Schwere hängt aber von der tatsächlichen Mikrogeometrie der Rauheit ab. Es gibt aber einen weiteren Aspekt, der sich auf die Anzahl und Höhe der Spannungszyklen bezieht. Eine transversale Ausrichtung der Rauheiten führt im Kontakt zu einer höheren Anzahl von Mikrospannungszyklen im Gegenkontakt verglichen mit longitudinal ausgerichteten Rauheiten (mit oder ohne Anwesenheit von Schmierstoff). Da die Materialermüdung auch abhängig ist von der Anzahl der Spannungszyklen, ist an der gegenüberliegenden Kontaktfläche bei transversaler Rauheitsorientierung eine größere Schädigung zu erwarten. Neben numerischen Simulationen wurden Versuche durchgeführt, um diesen Effekt zu zeigen (Bild 6); hierbei wurden sehr ähnliche Oberflächen unter denselben Bedingungen getestet, wobei nur die Rauheitsausrichtung verändert wurde. In dem Modell wurde dieselbe gemessene Topographie sowohl bei 0° als auch 90° Ausrichtung verwendet. Es wurde zwischen den SKF Modellen und den experimentellen Ergebnissen eine gute Übereinstimmung festgestellt.
Kontakt zweier rauer Oberflächen
In Industrieanwendungen findet der Kontakt immer zwischen zwei realen Oberflächen mit einer bestimmten Rauheit statt. Dies trifft auch für die bei SKF durchgeführten Versuche unter Verwendung einer Oberflächenzerrüttungsprüfmaschine (Surface Distress Test Rig – SDTR) zu, die einen rotierenden Probekörper besitzt, der von drei Scheiben (alle aus gehärtetem Wälzlagerstahl) überrollt wird. Es wurde beobachtet, dass, wenn der Probekörper rauer als die belastenden Scheiben war, sich innerhalb eines relativ langen Zeitraums keine Oberflächenzerrüttung zeigte (Bild 7a). Wenn jedoch die Scheiben rauer waren als der Probekörper (Bild 7b), dann trat an der Probekörperoberfläche relativ schnell Oberflächenzerrüttung auf. Dies wurde auch in [9] beobachtet. Eine wahrscheinliche Erklärung hierfür ist im Lastverlauf, der Anzahl der Ermüdungsmikrozyklen aufgrund der Rauheiten, zu finden.
Da die Kontaktbedingungen im Allgemeinen mehr in Richtung Grenz- oder Mischreibung gehen, wird der zeitliche Spannungverlauf durch die Dominanz der raueren Oberfläche über die glattere bestimmt, solange ein gewisses Gleiten vorliegt. Bild 8 zeigt diese Situation schematisch (d. h. raue und glatte Kontaktflächen in relativer Gleitbewegung). Es kann festgestellt werden, dass die glatte Oberfläche Druckschwankungen (Belastungsmikrozyklen) „erfährt“, während alle Punkte auf der rauen Oberfläche immer dieselben Spannungen „erfahren“ (höhere in den Kontaktbereichen und niedrigere in den kontaktfreien Bereichen). Dieses Beispiel zeigt, dass es durch die raue Oberfläche auf der glatten Oberfläche zu Last-/Spannungsschwankungen kommt. In realen Kontakten sind beide Oberflächen rau und in Relativbewegung zueinander (mit einem gewissen Gleitanteil), aber sobald die Rauheitsunterschiede ein gewisses Maß überschreiten, wird die rauere Oberfläche auf der glatteren Oberfläche Belastungsmikrozyklen „auslösen“. Daher ist die glattere Oberfläche bei Anwesenheit von Gleitanteilen anfälliger für Oberflächenzerrüttung, vorausgesetzt, dass die mechanischen Eigenschaften beider Oberflächen gleich sind. Bei Vollschmierung (Flüssigkeitsreibung) und Anwesenheit hydrodynamischer Drücke (aufgrund des Schmierfilmaufbaus) kann dieser Effekt für den Lastverlauf jedoch sehr unterschiedlich sein. Beim Gleiten pflanzen sich hydrodynamische Druckwellen mit unterschiedlichen Geschwindigkeiten fort.
Bild 9 zeigt Simulationsergebnisse für einen Oberflächenkontakt „rau auf glatt“ und beschreibt die zerrüttete Fläche in Abhängigkeit vom maximalen Hertz’schen Kontaktdruck. Es zeigt sich, dass sowohl die Oberflächenzerrüttung auf der glatteren Oberfläche viel schneller fortschreitet als auch das Oberflächenzerrüttungsrisiko bei beiden Oberflächen mit der Belastung zunimmt.
Leichter Materialabtrag (milder Verschleiß)
Die auf der SDTR durchgeführten Versuche zeigen, dass bei zu geringer Schmierstoffviskosität (z. B. 1 cSt) eine Oberflächenzerrüttung nicht unbedingt auftreten muss, sondern eher ein leichter Materialabtrag (milder Verschleiß) an der Oberfläche stattfinden kann. Es wird daher angenommen, dass bei einer Verschlechterung der Schmierqualität, definiert durch den Parameter к bei Wälzlagern oder das Lambda-Verhältnis Λ (Λ = h/Rq) bei allgemeineren Schmierkontakten, der Materialabtrag zunimmt. Die Oberflächenzerrüttung und milder Verschleiß konkurrieren miteinander [8, 9], sowohl während der Einlaufphase als auch im stabilen Zustand. Daher ist das Modellieren der Oberflächenzerrüttung eine komplexe Aufgabe, da mehrere Phänomene zusammenwirken.
Es wird angenommen, dass in einigen Fällen milder Oberflächenverschleiß durch Veränderung der Oberflächentopografie oder durch Abtragen von geschädigten Materialschichten eine Oberflächenzerrüttung verringern oder verhindern kann, wodurch die Oberfläche gegenüber der Oberflächenzerrüttung weniger anfällig wird [8, 9]. Ein leichter Materialabtrag kann auch mit den Schmierbedingungen im Kontakt interagieren. Bild 10 zeigt ein Beispiel für den durch das SKF Modell prognostizierten Schmiereffekt: der prozentuale Anteil der zerrütteten Fläche in Abhängigkeit vom Schmierqualitätsparameter (Λ) in zwei Fällen – d. h. mit und ohne milden Verschleiß. Wie ersichtlich, nimmt die Oberflächenzerrüttung in dem Fall, in dem kein Materialabtrag erfolgt, mit steigenden Λ-Werten allmählich ab, da die Oberfläche durch den dickeren Schmierfilm besser geschützt wird. Im Fall der Kombination von Ermüdung und leichtem Materialabtrag ist das Verhalten komplexer. Das heißt, bei sehr niedrigen Λ-Werten wird die Oberflächenzerrüttung durch den Materialabtrag an der Oberfläche gänzlich unterdrückt. Der entgegenwirkende Effekt des Materialabtrags verschwindet jedoch mit zunehmenden Λ-Werten rasch, was eine vorübergehende Zunahme der Oberflächenzerrüttung verursacht, die ihr Maximum bei Λ≈ 1,1 erreicht. In diesem Beispiel wird der Einfluss des milden Verschleißes ab Λ > 1,1 vernachlässigbar und die beiden Kurven laufen ineinander.
Der Einfluss des Gleitens
Dies ist ein wichtiges Thema, da der Einfluss des Gleitens auf die Oberflächenzerrüttung bei Wälzlagern immer wieder auf Interesse stößt. In vielen Studien wird auf der Basis von Rissausbreitungskonzepten behauptet, dass zunehmendes Gleiten die Oberflächenzerrüttung fördert. Allerdings muss ein Riss zuerst einmal entstanden sein, damit er wachsen kann. Mit Hilfe der SKF Modellierungsmöglichkeiten und sorgfältig durchgeführter Laborversuche wird nachgewiesen, dass erhöhte Gleitanteile nicht unbedingt zu einer stärkeren Oberflächenzerrüttung führen müssen. Vielmehr tritt genau das Gegenteil ein. Bild 11 zeigt den Einfluss des Gleitens im SKF Modell (Kurve) unter Berücksichtigung von mildem Verschleiß. Im selben Bild werden Fotografien der Rollenlauffläche von Versuchen mit zunehmendem Gleiten gezeigt für S=0,01, S=0,02 und S= 0,1 (wobei S = Gleitgeschwindigkeit/hydrodynamisch wirksame Geschwindigkeit). Es zeigt sich deutlich, dass der Schaden durch Oberflächenzerrüttung bei niedrigen Gleitwerten (S≈0,01) am größten ist. Dabei handelt es sich um den Gleitwert, der typischerweise bei jedem Wälzlagertyp vorzufinden ist. Daher gibt es, wenn es um die Beständigkeit gegenüber der Oberflächenzerrüttung als Funktion des Gleitens geht, keinen Unterschied zwischen Rollenlagern, Pendelrollenlager oder sogar Kugellagern.
Auf der Grundlage der Rissbildungskonzepte gibt es zwei Erklärungen für diesen Mechanismus.
Reibung: Sie nimmt nicht unbedingt mit erhöhtem Gleitanteil zu, unabhängig davon, ob es sich um geschmierte oder trockene Kontakte handelt (=> Oberflächenreibung). Im trockenen Kontakt (Grenzschmierung) folgt die Reibung in etwa dem Coulomb’schen Gesetz; daher ist zum Aktivieren dieses Mechanismus nur ein winziger Gleitbetrag nötig, um beinahe den Höchstwert zu erreichen. Bei weiterer Zunahme des Gleitens wird die Reibkraft an der Oberfläche nicht größer (nachdem die Nachgiebigkeit der Oberfläche überwunden ist). Im geschmierten Kontakt folgt die Reibung dem rheologischen Gesetz des Schmierstoffs; unter EHD-Bedingungen verhält sich der Schmierstoff wie ein nicht-newton’sches Fluid und ist nahe den Schubspannungsgrenzbedingungen. Daher erhöht ein zunehmender Gleitanteil die Oberflächenreibung nicht wesentlich.
Milder Verschleiß: Er nimmt mit dem Gleiten zu. Die beschädigten Materialschichten werden von der Oberfläche entfernt und dadurch werden Ermüdungsschäden hinausgezögert.
Schlussfolgerungen
Es können verschiedene Schlussfolgerungen in Bezug auf die Oberflächenzerrüttung gezogen werden. Zunächst ist die Qualität der Schmierung (und der Rauheit) im Hinblick auf die Entstehung (und Kontrolle) der Oberflächenzerrüttung extrem wichtig. Grenz- und Mischreibbedingungen führen zu einem hohen Anteil von Rauheitskontakten. Dies führt zu einem lokalen Anstieg von Scherkräften, Spannungskonzentrationen (geschmierte Bereiche haben eine geringere Reibung als Festkörperkontakte) und Mikrospannungszyklen, die eine Ermüdung begünstigen können. Die Oberflächenreibung spielt bei der Entstehung der Oberflächenzerrüttung eine große Rolle. Selbst unter „anscheinend idealen“ reinen Abrollbedingungen kann eine Oberflächenzerrüttung hervorgerufen werden, da in realen Anwendungen immer gewisse Gleitanteile vorliegen. Aufgrund der Bedeutung der Oberflächenreibung bei der Entstehung der Oberflächenzerrüttung ist das Vorhandensein eines gewissen Gleitens für das Entstehen von Oberflächenzugkräften und Oberflächenschäden nötig. Ein Anstieg des Gleitanteils auf mehr als 1 bis 2 % (typisch für jeden Wälzlagertyp) erhöht jedoch nicht das Risiko einer Oberflächenzerrüttung, da die Reibung nicht unbegrenzt zunimmt und milder Verschleiß bei der Vermeidung von Oberflächenermüdung hilfreich sein kann.
Die Spannungsüberhöhungen und die Lastverläufe (Mikrozyklen) unter Misch- und Grenzschmierungsbedingungen, bedingt durch Kontakttopographien/Rauheiten, sind die wichtigsten Ursachen der Oberflächenzerrüttung. Wenn jedoch ein vollständig trennender Schmierfilm vorhanden ist, kann der Einfluss der Rauheit außer Acht gelassen werden. In den Versuchen hat der „Kontakt“ zwischen einer raueren und einer glatteren Oberfläche gezeigt, dass der letztere immer stärker zur Oberflächenzerrüttung neigt. Schließlich kann milder Verschleiß im Allgemeinen durch Reduzierung starker Oberflächenunebenheiten während der Einlaufphase und durch Entfernen der oberflächennahen Ermüdungsschichten die Entstehung von Mikrorissen verhindern oder verzögern. Ausgiebiger oder lokaler Verschleiß kann jedoch zu einer Änderung der Makrogeometrie der sich kontaktierenden Komponenten führen, was wiederum die Lebensdauer negativ beeinflussen kann.
Möglichkeiten der Prävention
Aus diesen Studien ergeben sich eine Reihe praktischer Schritte zur Reduzierung des Oberflächenzerrüttungsrisikos. Diese sind im Einzelnen:
-
Gute Schmierbedingungen (Voll-EHL) je nach Anwendung, z. B. durch eine höhere Schmierstoffviskosität, höhere Drehzahlen, niedrigere Temperaturen etc.
-
Verringerung der Reibung-/ Grenzreibung (via Schmierstoff, Verdicker, reibungsarme Beschichtungen etc.).
-
Reduzierung von Störgrößen, die zu Spannungsüberhöhungen führen (Verunreinigungen, Schmutzteilchen, Kratzer aufgrund der Montage etc.). Verwendung einer optimierten Topografie.
-
Verringerung von dynamischen Bewegungen unter Belastung (z. B. durch Vorspannung oder Minimieren des Lagerspiels).
-
Vermeidung ungleicher Rauheitswerte bei sich berührenden Elementen (z. B. durch Einlaufen).
-
In bestimmten Fällen kann ein kontrollierter leichter Materialabtrag an der Oberfläche (Wechselwirkung zwischen Additiv und Schmierstoff) zur Reduzierung des Oberflächenzerrüttungsgrads gerechtfertigt sein.
-
Verwendung von SKF Explorer Lagern, deren ausgewogene Oberflächentopografie das Risiko einer Oberflächenzerrüttung vermeidet.
Literatur
[1] ISO Standard 15243, „Rolling Bearings – Damage and Failures – Terms, Characteristics and Causes“, 2004.
[2] Way, S., „Pitting due to Rolling Contact“, J. of Appl. Mech., vol. 57, pp. A49-A58, 1935.
[3] Dawson, P.H., „Effect of Metallic Contact on the Pitting of Lubricated Rolling Surfaces“, J. Mech. Eng. Sc., vol. 4(1), pp. 16-21, 1962.
[4] Olver, A.V., „The Mechanism of Rolling Contact Fatigue – an Update“, Proc. Instn. Mech. Engrs., Part J, J. of Eng. Trib., Vol. 219, pp. 313-330, 2005.
[5] Oila, A., Bull, S.J., „Assessment of the Factors Influencing Micropitting in Rolling/Sliding Contacts“, Wear, Vol. 258, pp. 1510-1524, 2005.
[6] Brandão, J.A., Seabra, J.H.O., Castro, J. „Surface Initiated Tooth Flank Damage Part I: Numerical Model“, Wear, Vol. 268, pp. 1-12, 2010.
[7] Brandão, J.A., Seabra, J.H.O., Castro, J. „Surface Initiated Tooth Flank Damage Part II: Prediction of Micropitting Initiation and Mass Loss“, Wear, Vol. 268, pp. 13-22, 2010.
[8] Lainé, E., Olver, A.V., „The effect of Anti-wear additives on fatigue damage“, Extended abstract, 62nd STLE Annual Meeting, 2007.
[9] Lainé, E., Olver, A.V., Beveridge, T.A., „Effect of lubricants on micropitting and wear“, Tribology International, 41, pp. 1049-1055, 2008.
[10] Morales-Espejel, G.E., Brizmer, V., „Micropitting Modelling in Rolling-Sliding Contacts: Application to Rolling Bearings“, Tribology Transactions, im Druck.