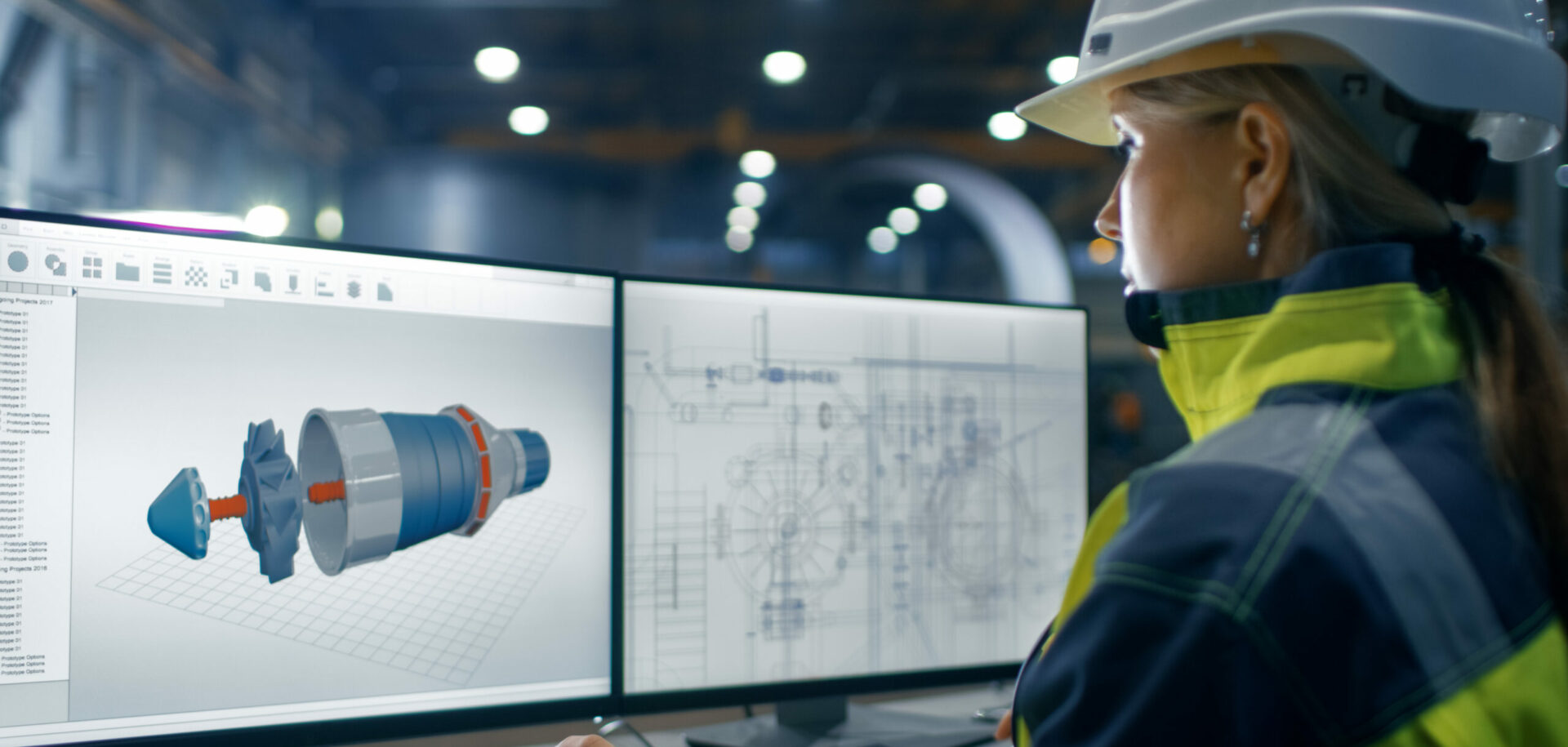
Vermeidung von Elektroerosion in Wälzlagern
Stromisolierte SKF Wälzlager INSOCOATTM können Schäden aufgrund von Stromdurchgang durch das Lager verhindern.Seit fast 70 Jahren ist bekannt, dass bei Wälzlagern Stromdurchgang auftritt und dass dieser Strom in der Kontaktzone zwischen den Wälzkörpern und der Innen- und Außenringlaufbahn Beschädigungen hervorrufen kann. Die Schäden sind nicht auf die metallischen Lagerbauteile beschränkt, auch der Schmierstoff wird im Lager bei Stromdurchgang verändert. Alle elektrischen Maschinen, Wechsel- und Gleichstrommotoren sowie Generatoren, können betroffen sein.
Stromisolierte SKF Wälzlager INSOCOATTM können Schäden aufgrund von Stromdurchgang durch das Lager verhindern.Seit fast 70 Jahren ist bekannt, dass bei Wälzlagern Stromdurchgang auftritt und dass dieser Strom in der Kontaktzone zwischen den Wälzkörpern und der Innen- und Außenringlaufbahn Beschädigungen hervorrufen kann. Die Schäden sind nicht auf die metallischen Lagerbauteile beschränkt, auch der Schmierstoff wird im Lager bei Stromdurchgang verändert. Alle elektrischen Maschinen, Wechsel- und Gleichstrommotoren sowie Generatoren, können betroffen sein.
SKF hat stromisolierte Wälzlager entwickelt, die INSOCOATTM-Lager, die Schäden aufgrund von Stromdurchgang verhindern. Diese Lager haben eine Isolationsschicht aus Aluminiumoxid auf dem Außenring (Reihe VL0241). Sie ist nominell 100 µm dick und wird im Plasmaspritzverfahren aufgebracht. Die Abmessungen und Toleranzen der INSOCOAT-Lager entsprechen den ISO-Normen, sind also mit denen herkömmlicher Lager identisch( Abb. 1). Gegenüber Gleichstrom wirkt die Beschichtung wie ein ohmscher Widerstand und gewährleistet ausreichende Sicherheit vor Stromdurchgang. Der Gleichstromwiderstand liegt weit über 50 MW. Führende Hersteller von Elektromaschinen und Fahrmotoren setzen INSOCOAT-Lager ein. Auch in anderen Eisenbahn-Anwendungen, etwa in Radsatzlagern, werden sie verwendet.
Induktionsmotoren
In den letzten Jahrzehnten werden Wechselstrommotoren für Anwendungen in Schienenfahrzeugen und Industrie verstärkt eingesetzt. In industriellen Anwendungen werden meist Drehstrominduktionsmotoren verwendet, vom einfachen Lüfterantrieb bis hin zum komplexen und äußerst leistungsfähigen Antrieb für Papiermaschinen. Auch hier tritt das Problem des Stromdurchgangs durch das Lager auf, wobei es viele Ursachen für das Auftreten von Strömen im Lager und Wellenspannungen geben kann.
Bei einer sinusförmigen Netzspeisung kann ein Strom im Lager durch Asymmetrien im Magnetfeld des Motors fließen. Die asymmetrische Verteilung des magnetischen Flusses im Motor induziert eine Spannung in der Welle, die bewirkt, dass ein niederfrequenter Strom durch die Lager fließt. Auch durch asymmetrische, nicht geschirmte Motorverkabelung können Ströme im Lager entstehen. Diese „klassischen“ Lagerströme sind insbesondere in großen Motoren mit einer geringen Polpaarzahl problematisch (etwa Zweipolmotoren), weil hier stärkere Asymmetrien im Magnetfluss auftreten als bei kleinen Motoren oder bei Motoren mit einer größeren Polzahl. Mit einer besseren Isolierung oder mit einer verbesserten Motorenkonstruktion sowie Verkabelung kann weitgehend Abhilfe geschaffen werden.
In den 90er Jahren hat sich der verstärkte Einsatz von Antrieben mit veränderlicher Drehzahl auf die Anzahl der festgestellten Lagerausfälle ausgewirkt. Das liegt daran, dass in Frequenzumrichtern als Leistungsschalter nicht länger Thyristoren und GTO-Transistoren benutzt werden, sondern IGBTs, die heute den Markt der Regelantriebe beherrschen. Diese IGBTs erzeugen eine pulsbreitenmodulierte Ausgangsspannung und helfen so den Wirkungsgrad und die dynamische Leistungsfähigkeit der Antriebe zu verbessern. Leider hat jede neue Technik auch ihre Nachteile. Neben den herkömmlichen, im Motor erzeugten Spannungen und Strömen wurden bei der Versorgung des Motors durch einen Frequenzumrichter (Frequenzen zwischen
3 und 12 kHz, je nach Leistungsbereich) neue Phänomene beobachtet. So entstehen die Lagerschäden durch hochfrequente Ströme (5 kHz bis 10 MHz), die durch diese schnell schaltenden IGBT-Halbleiterelemente (100 ns) induziert werden. IGBTs rufen auch einen schnellen Spannungsanstieg (du/dt) von bis zu 5 bis 8 kV/µs oder sogar 10 kV/µs am Umrichterausgang hervor. Es wurde also eine neue Quelle von Strömen im Lager entdeckt, die allerdings noch nicht vollständig erforscht ist.
Lagerströme gehen im wesentlichen auf folgende Ursachen zurück:
- Asymmetrischer Magnetfluss im Motor
- Asymmetrische, nicht geschirmte Verkabelung
- Schnellschaltende Frequenzumrichter und ihre Gleichtaktspannung
Die ersten beiden Ursachen gelten für alle Elektromotoren, letztere jedoch nur für
frequenzumrichter-gespeiste Antriebe. Probleme ergeben sich durch drei unterschiedliche Ströme:
- Hochfrequente Erdungsströme der Welle
- Hochfrequente zirkulierende Ströme (Kreisströme)
- Kapazitive Ströme
Die ersten beiden Ströme werden durch die Gleichtaktspannung am Umrichterausgang hervorgerufen. Sie entsteht, da die Summe der Spannungen in den drei Phasen ungleich Null ist. Der Frequenzumrichter erzeugt eine sinusförmige Eingangswelle durch pulsbreitenmodulierte Signale, die eine hohe Schaltfrequenz und eine steile Flanke besitzen und kapazitive Ströme hervorrufen.
Hochfrequente Erdungsströme gehen in ähnlicher Weise auf Verkabelung zurück. Hier entsteht jedoch eine induzierte Spannung wesentlich höherer Frequenz in der Schutzerde, bedingt durch die Gleichtaktspannung des Umrichters. Wenn die Impedanz des Rückleitungskabels zu hoch und die Statorerdung unzureichend ist, sucht sich der Strom einen Weg vom Stator über die Lager und die Welle zur Erde und somit zurück zum Umrichter (Abb. 2).
Diese Gleichtaktspannung erzeugt eine Gleichtaktstörung, die eine Stromasymmetrie zwischen den drei Phasen in den Statorwicklungen hervorruft. Die Summe des Stroms über den Statorumfang ist ungleich Null. Eine hochfrequente Flussänderung umgibt die Welle und erzeugt eine hochfrequente Wellenspannung. Es besteht die Gefahr, dass hochfrequente zirkulierende Ströme axial entlang des Rotors, durch ein Lager und zurück durch das andere Lager laufen (Abb. 3). Hochfrequente zirkulierende Ströme haben bei jedem Lager ein anderes Vorzeichen.
In einem problemlos umlaufenden Wälzlager sind die Wälzkörper von den Laufbahnen durch einen dünnen Schmierfilm getrennt. Dieser Schmierfilm wirkt als Dielektrikum eines Kondensators, das von der Rotorspannung aufgeladen wird. Die Kapazität dieses Kondensators hängt von verschiedenen Parametern wie Schmierstoffsorte, Temperatur, Viskosität und auch der Dicke des Schmierfilms ab. Wenn die Spannung einen Schwellenwert – die Durchschlagspannung des Schmierstoffs – übersteigt, entlädt sich der Kondensator, und ein hochfrequenter kapazitiver Strom entsteht. In diesem Fall wird der Strom von den inneren Streukapazitäten des Motors begrenzt, tritt aber bei jedem Schaltvorgang des Umrichters auf.
Ein Induktionsmotor, der durch einen Frequenzumrichter gesteuert wird, ist also ein sehr komplexes Antriebssystem, auf das viele Parameter einwirken. Der gesamte Antrieb einschließlich Stromversorgung, Gleichstromzwischenkreis, Schaltelementen, Kabel und mechanischer Belastung muss als ein System aus Induktivitäten und Kapazitäten betrachtet werden.
Schäden durch Stromdurchgang
Bei Stromdurchgang durch ein Wälzlager findet eine elektrische Entladung durch den Schmierstoff zwischen der Innen- und Außenringlaufbahn über die Wälzkörper statt. Durch die entstehende Wärme wird die Oberfläche an manchen Stellen aufgeschmolzen. Es bilden sich Krater, und geschmolzener Werkstoff wird teilweise an andere Stellen übertragen. An der Krateroberfläche verfestigt sich der Werkstoff wieder, ist aber wesentlich spröder als das Ausgangsmaterial. Unter dieser umgehärteten Schicht liegt ausgeglühter Werkstoff, der weicher als das Grundmaterial ist. In Wälzlagern werden – je nach den Beschädigungen der Laufflächen – drei Arten von Stromschäden unterschieden.
Bei hohen Spannungen – normalerweise in Gleichstromanwendungen wie Fahrmotoren – tritt Kraterbildung auf. Die vereinzelten Krater haben einen Durchmesser von 0,1 bis 0,5 mm und sind damit mit dem bloßen Auge sichtbar (Abb. 4).
Riffelbildung („washboarding“) zeigt sich als Vielzahl verschiedenfarbiger grauer Linien quer zur Laufbahn (Abb. 5). Sie entstehen durch mechanische Schwingungen, wenn die Wälzkörper kleine Krater überrollen. Riffelbildung ist daher kein primärer Lagerschaden durch Stromdurchgang, sondern erscheint erst als Sekundärschaden, wenn das Lager durch Krater- oder Grübchenbildung bereits geschädigt war.
Frequenzumrichter werden heute häufig eingesetzt, und so sind auch Mikrokrater die häufigste Schadensform bei Stromdurchgang. Die geschädigte Oberfläche zeigt ein mattes Aussehen mit zahlreichen winzigen aufgeschmolzenen Grübchen. Die Wälzkörper und Lagerringe sind mit Mikrokratern übersät, deren Durchmesser im allgemeinen 5 bis 8 µm beträgt (Abb. 6). Nur bei starker Vergrößerung unter dem Mikroskop ist die Form dieser Krater zu erkennen.
Nicht nur die metallischen Lagerflächen leiden bei Stromdurchgang, sondern auch der Schmierstoff verändert seine Zusammensetzung und verliert an Schmierfähigkeit.
Aufgrund der hohen Temperaturen reagieren das Grundöl und die Additive miteinander, das Grundöl verbrennt oder verkokt, und die Additive zersetzen sich oftmals schnell. Schließlich ist der Schmierstoff schwarz verfärbt und verhärtet (Abb. 7).
Zerstörung des Schmierstoffs ist ein typischer Schaden bei Stromdurchgang durch das Lager.
Elektrische Eigenschaften
Ströme unterschieden sich in ihrer Wirkung. Auch INSOCOAT-Lager verhalten sich unterschiedlich bei Gleich- und Wechselstrom.
In Gleichstromanwendungen wirkt INSOCOAT wie ein ohmscher Widerstand. Die Beschichtung aus Aluminiumoxid ist ein Isolator, und der entscheidende Wert ist ihr Gleichstromwiderstand R. Die Durchschlagspannung beträgt 1.000 VDC, der Widerstand mehr als 50 MΩ, so dass das Lager wirksam isoliert ist.
In Wechselstromanwendungen, insbesondere bei den hohen Frequenzen von pulsbreitenmodulierenden Umrichtern, gilt dies nicht. Wir müssen hier ein „elektrisches Ersatzschaltbild“ des gesamten INSOCOAT-Lagers einschließlich Innen- und Außenring, Wälzkörper, Käfig, Schmierstoff, Kontaktfläche zwischen Wälzkörpern und Laufbahnen und Keramikbeschichtung erstellen. Ein mögliches elektrisches Modell des Lagers zeigt Abb. 8.
Aus zwei Gründen lässt sich ein genaues Ersatzschaltbild nur mit Schwierigkeiten erstellen:
- Massive Metallteile in hochfrequenten elektrischen Feldern haben eine sehr komplizierte dreidimensionale Struktur. Es muss berücksichtigt werden, dass möglicherweise Wirbelströme entstehen.
- Die Kontaktstellen zwischen Außenring und Wälzkörpern und Wälzkörpern und Innenring stellen einen kapazitiven Widerstand dar. Der Wert dieses Widerstands ändert sich stochastisch aufgrund der Dynamik im Lager, etwa bei Schwingungen.
Eine stromisolierende Schicht wie die Beschichtung aus Aluminiumoxid Al2O3muss als Parallelschaltung eines Widerstands und eines Kondensators dargestellt werden. Wichtig ist die Impedanz Z, die sich folgendermaßen berechnet:
mit
Es handelt sich um eine komplexe Größe mit R [W] gleich dem Gleichstromwiderstand des Systems, C [F] der Kapazität und f [Hz] gleich der Frequenz.
Der Betrag der Impedanz errechnet sich als:
Aus dieser Gleichung wird folgendes deutlich: Mit steigender Frequenz wird der Term, der die Kapazität enthält, größer und damit die Impedanz kleiner. Um die Impedanz des Lagers zu steigern, muss die Kapazität der Beschichtung möglichst gering sein. Die Kapazität eines INSOCOAT-Lagers hängt von der Lagergröße (beschichtete Fläche), der Dicke der Isolationsschicht und dem Werkstoff der Beschichtung ab:
mit: A gleich der beschichteten Berührungsfläche,s gleich der Dicke der Keramikschicht, εr gleich der relativen dielektrischen Konstante der Keramikschicht und ε0gleich der dielektrischen Konstante im Vakuum.
Ausblick
Um die Wünsche der Kunden zu erfüllen und auf die Bedürfnisse des Marktes zu reagieren, hat SKF das Verhalten von INSOCOAT-Lagern bei hochfrequenten Strömen und Spannungen detailliert untersucht. SKF kann Aussagen über das Impedanzverhalten von INSOCOAT-Lagern in Abhängigkeit von der Frequenz für verschiedene Schichtdicken treffen. In Abb. 9 und Abb. 10 sind typische Verläufe der Impedanz und Kapazität eines beschichteten Rillenkugellager-Außenrings dargestellt.
Eine geringere Kapazität und damit größeren Kundennutzen erreicht SKF bei INSOCOAT-Lagern durch die stromisolierende Beschichtung der Innenringbohrung (Reihe VL207). Im Gegensatz zur Beschichtung des Außenrings ist hier die Fläche wesentlich kleiner, was eine erheblich geringere Kapazität bedeutet.
Für Sonderanwendungen sind beschichtete Außenringe mit dickerer Keramikbeschichtung (bis 300 µm) und Hybridlager erhältlich.
Das Problem der Lagerströme in einem frequenzumrichtergetriebenen Induktionsmotor ist außerordentlich komplex, denn viele Parameter wirken auf das ganze System ein. In Zukunft werden Antriebe mit veränderlicher Drehzahl vor allem in industriellen Anwendungen verstärkt verwendet. Höhere Schaltfrequenzen und schnellerer Spannungsanstieg (du/dt) bei pulsbreitenmodulierenden Umrichtern gewinnen an Bedeutung.
SKF ist bestrebt, durch INSOCOAT-Lager mit verbessertem elektrischen Verhalten die steigenden Ansprüche des Marktes zu befriedigen. In Zusammenarbeit mit mehreren Kunden untersucht SKF das Phänomen der Lagerströme in der Praxis. Bisher steht eines fest: Lagerströme können nur dann auf ein ungefährliches Niveau gesenkt werden, wenn alle Komponenten optimiert sind, insbesondere die Frequenzumrichter, die die Hauptursache für Lagerströme darstellen. SKF ist bemüht, praxistaugliche und kostengünstige Lösungen zu entwickeln.
Gerwin Preisinger und Martin Gröschl,
Institut für Allgemeine Physik, Technische Universität Wien,
und Hubert Köttritsch, Industrial Division, Development Centre Steyr, SKF Österreich AG