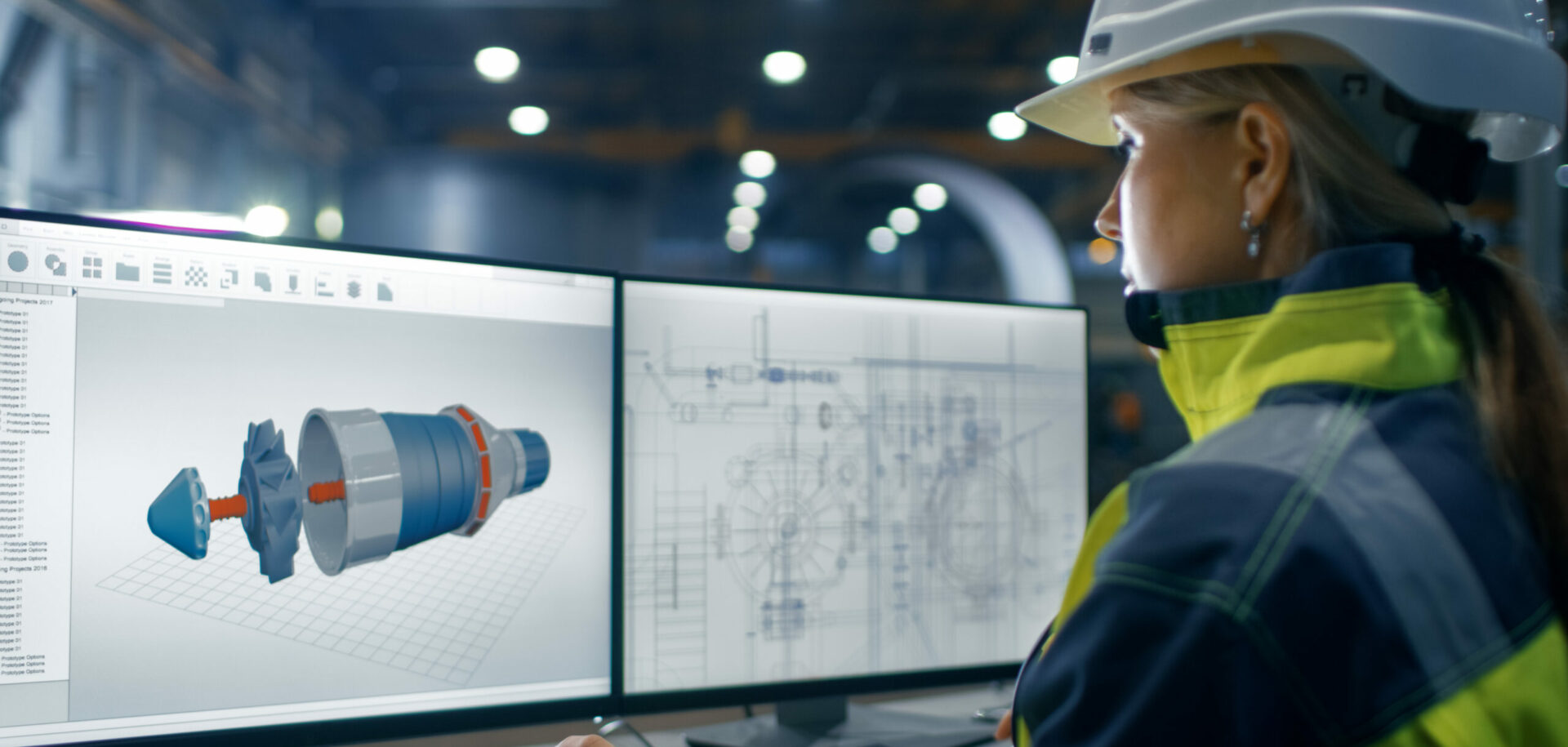
Decision-support system for selecting bearing lubricants
LubeSelect is a system that will allow SKF to further improve its support to customers when selecting appropriate bearing lubricants.
Summary
Selecting the correct lubrication for a particular bearing is a crucial step if a bearing is to live up to design expectations in its application. SKF engineers have considerable experience and knowledge of greases in association with bearing operation. This knowledge has been encapsulated into a computer program called LubeSelect, which can be accessed by SKF engineers through company intranet. Based on fuzzy logic, the program allows users to choose from a range of standard and non-standard greases depending on the particular operating conditions of the application.
Appropriate grease lubrication is crucial in bearing applications and of strategic importance for SKF. The company has developed deep knowledge of this topic through fundamental understanding of grease lubrication, from empirical test results and from application experience.
Its understanding of bearing lubrication has been condensed into a knowledge-based system called LubeSelect. The system, accessible via the SKF intranet, helps SKF engineers to support bearing customers by tapping into the combined experience of SKF engineers. As many as 300 SKF engineers use LubeSelect every week. LubeSelect ranks grease lubricants on the basis of their relevance to the particular application conditions.
In today’s knowledge economy, companies need to differentiate themselves not only by offering high-quality products but also by exploiting their unique knowledge. Knowledge management introduces ways to optimise the creation and flow of knowledge through the company.
Among the ways to exploit knowledge are expert systems for decision support. Knowledge can be represented in best practice examples, generalised rules or physical relations with empirical parameters. Different knowledge-based solutions are available, depending on the nature and maturity of the knowledge. In line with the technology revolution, expert systems can be accessed on the Web.
Within the SKF Engineering and Research Centre, a system has been developed for decision support in lubrication. The knowledge resides in fundamental understanding of grease lubrication, in empirical test results and in application experience. This knowledge is used through LubeSelect, which is available globally, round the clock, via SKF intranet.
Background
The selection of a lubricant has traditionally been based on the ratio between the desired and the actual base-oil viscosity, the goal being to build up a thin film of lubricant to prevent direct metallic contact between rolling elements, raceways and cages.
A rudimentary expert system, based on viscosity ratio calculations, was developed for grease selection in 1988. The system served as a base for developing recommendations that further differentiated between greases by adding selection criteria other than viscosity ratio.
More recently, a database – called LuBase – has been developed, containing product information on a wide range of greases. The system allows simple searches – for example, searches based on viscosity or consistency. Other bearing suppliers have introduced similar databases and a search facility based on consistency, thickener type, base-oil type and viscosity ratio.
The viscosity ratio still is a useful parameter, especially for oil lubrication. But because of the complexity of modern grease lubricants, with their special additives, solids, thickeners, base-oil types and other factors, the viscosity ratio does not completely represent the performance of a grease lubricant today. Instead, all the performance characteristics of the grease lubricant must be considered carefully in light of the bearing application.
Searching by consistency, thickener type and other values is a step in the right direction. But the most important translation from application conditions to the desired grease properties is missing. LuBase and other systems operate by allowing users to search through a grease database. In contrast, LubeSelect provides lubricant suggestions based on application conditions.
Working principles
LubeSelect can be consulted in two ways:
1. via application conditions. The conditions describe the bearing environment as completely as possible, and are mapped onto the performance characteristics of individual greases. Best-scoring greases are ranked first.
2. via application profiles. For a range of typical bearing applications, grease advice is formulated based on proven-practice examples.
Selection via application conditions:
The first step in selecting a grease is to get basic information about the bearing application. The user supplies about 30 application parameters. For particular requirements, the user can differentiate according to their importance. Example requirements are high rust protection, low noise and biodegradability. Given the conditions, standard greases are checked by generalised rules and when applicable recommended first.
If the application conditions are outside the standard range or special conditions apply, a wider range of SKF-tested greases are considered. These preferred greases are differentiated according to their individual performance on bearing-specific criteria. Assuming a range of criteria, specific performance tests are applied, for example, a test-rig for noise level measurements. After considering the application conditions, the total score of a grease is determined as a fuzzy number between 0 and 1 (no fit = 0, full fit = 1) out of the individual scorings of the required criteria.
The relevant fuzzy logic calculations are selected from fuzzy decision theory, a computational intelligence methodology. In essence this means that:
- the scoring on the different performance criteria is (weighed) averaged;
- the user can select “importance factors” to weigh the criteria, and
- a zero score on a specific criterion cannot be compensated for by other criteria.
Therefore, the geometric mean operator is chosen, given by:
Score j = P np ( m i,j ) n i,
for i = 1,…, n p and j = 1,…., ng
where
n i = normalised weight factor
m i,j = performance of the jth grease
for the i thcriterion
ng = number of greases
n p = number of performance criteria
Score j = total score for the jth grease
After assessment, the greases are ranked according to their individual scores. The final scores are expressed in percentages by multiplying by 100 percent. A rank of the greases, including their scoring, is the key outcome of the grease selection advice.
The system is further extended by various rules for exception handling and ranking – for example, for specific greased-for-life bearing variants. The recommended greases are accompanied by calculated grease life (or re-lubrication interval), viscosity ratio, grease quantity and other grease information.
Selection via application profiles:
A completely different approach of selecting a grease is to consider proven-practice application profiles. In cooperation with SKF business segments, lubrication experts and application engineers, about 50 application profiles (for example, pulp & paper applications) with recommended greases are offered. The profiles can be selected straightforwardly.
Implementation and rollout
LubeSelect is specified according to CommonKADS and System Development Framework (SDF) methods – formal knowledge engineering standards for designing knowledge-based systems. The core of LubeSelect is in a rule-based expert system shell written in Java. The system has the following components:
- the LubeSelect kernel, running online on a Windows-NT Web server;
- a Lotus Notes database for content maintenance by lubrication experts;
- a bearing data servlet (a parallel application that retrieves bearing data online from the SKF catalogue), and
- the user’s browser.
The components are all connected via SKF Intranet.
Since its rollout in September 2000, 250 to 300 SKF engineers use LubeSelect regularly every week. The system is also used in SKF internal courses for application engineers. Both minor and major extensions have been suggested since the system’s introduction. Major extensions are oil lubrication and several special bearing types. Most requests are being accommodated and will be added during an update of LubeSelect this autumn. In the near future, the system likely will be made accessible externally via the Internet as well.
The introduction of a knowledge-based system such as LubeSelect is an effective way to apply key company knowledge to daily decisions anywhere in the company. Similar systems in other knowledge areas are in progress and can be expected soon.
Gerard Schram,
SKF Engineering & Research Centre B.V. Nieuwegein,
the Netherlands