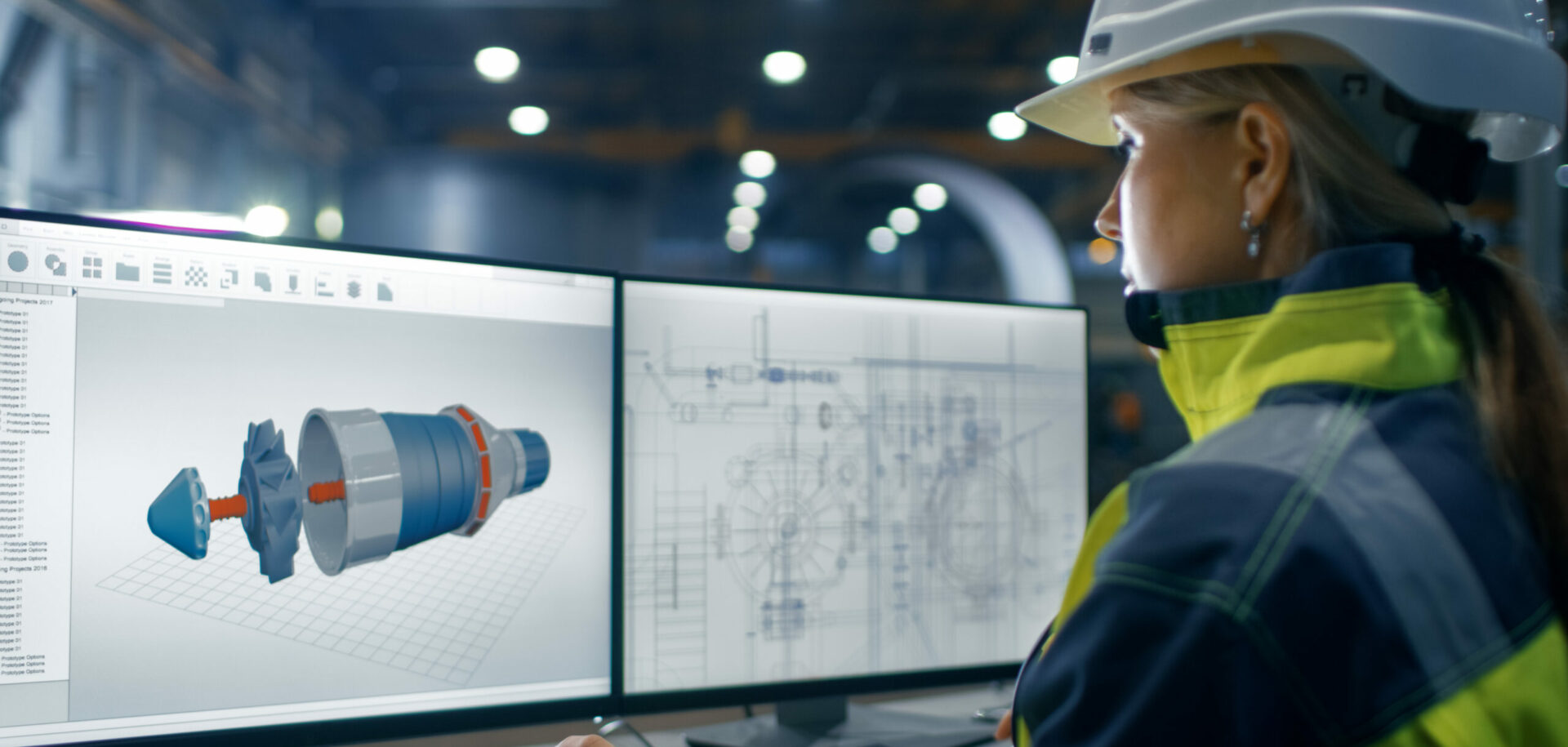
Documented care for the environment
There are five basic elements:
Summary
Environmental standards such as ISO 14001 and the Eco-Management and Audit Scheme (EMAS) are beginning to have an impact as industry increases its commitment to a culture of global environmental care. SKF has raised the profile of environmental management by being the first major bearing manufacturer to be certified for ISO 14001 for the group as a whole. This certification covers 63 manufacturing sites in 17 countries across five continents. SKF believes that this environmental standard will be adopted widely throughout industry. It will not only provide internal benefits such as cost savings through reduced waste and energy consumption, but will help realise the goal of creating a better environment for ourselves and our children.
SKF introduced an environmental management system across the group that meets the new international voluntary standard, ISO 14001.SKF set itself a tough schedule for the global introduction of ISO14001. At the beginning of 1998, only six sites had been audited and approved to the environmental standard. On December 7, 1998, SKF’s certification was granted by Lloyd’s Register Quality Assurance (LRQA), an international certification body for management systems. The certificate covers all the company’s established manufacturing units – 63 locations in 17 countries across five continents. The only factories not included were a few recently acquired companies in Canada, Asia and the Ukraine. These units are already working towards certification.
ISO 14001 is a voluntary international environmental standard that was officially launched in September 1996. It provides guidelines related to the definition and implementation of an environmental management system (EMS). The standard was developed as a response to growing legislation, government and public pressure for greater environmental control. The standard takes into account legislative differences between countries.
The challenge for SKF was to meet not only a tight schedule but also the varying needs of each unit and diverse legal requirements. This is highlighted by the fact that certification covers sites in countries such as India, South Africa and Poland, where environmental awareness has traditionally been lower. SKF factories in these countries have met the high standards required for certification and the factory at Poznan in Poland has become one of the first organisations in that country to receive environmental certification.
Basics of ISO 14001
An EMS is a method of managing an organisation’s environmental performance, which can be assessed and measured by an external audit. It must contain an environmental policy and an evaluation of environmental aspects. Objectives and responsibilities must be established, resources allocated, performance monitored and action taken where required.
There are five basic elements:
- Development of an environmental policy.
- Evaluation of environmental effects.
- Set-up of overall goals and specific measurable targets.
- Establishment of a management control system.
- Continual review of the system.
To qualify for group certification, SKF had to implement a single EMS for all operations globally. Also, the group had to demonstrate a corporate auditing programme throughout its factories. LRQA then used two sets of evidence of compliance before giving approval: from their own audits at a sample of sites, and from SKF audits on all sites.
The standard commits an organisation to continuous improvement of all aspects of its environmental management.
Actions taken
Each plant has looked at its individual circumstances and the opportunity to reduce its overall environmental impact. The SKF bearing factory at Luton, for example, was able to overcome the problem of grinding waste, which is traditionally expensive to dispose of because of U.K. landfill taxes, by working with a recycling company. Now all of this waste is recycled, providing annual savings at this plant of 15,000 British pounds (US$25,000) a year and transforming waste into a raw material.
In the U.S., the SKF factory at Hanover, Pennsylvania, has reduced its generation of hazardous waste from 230 tones to almost zero, thanks to changes in the use of materials.
Saint Cyr in France, another SKF site, has introduced a seven-point plan for the reduction of its environmental impact that covers a range of initiatives, including specific steps such as:
- Development of a substitute for white spirit to reduce air emissions.
- Separation of waste products that can represent an environmental risk when combined.
- Improvements to the atmospheric extractor system to reduce external noise.
- Installation of an automatic control system for water treatment.
- Reduction of the risk of fire and explosion through employee training in the use of extinguisher equipment.
The basic steel used in the manufacture of SKF bearings has long been made from a secondary steel-making process using scrap. Recently, SKF has introduced a new technology that involves compressing grinding waste into briquettes, which can be used in steel furnaces.
Other measures within the group include the introduction of solar power systems, heat exchanger for energy recovery and water-treatment systems for recycling water.
Benefits of certification
In addition to the obvious benefits of protecting the environment, environmental improvement can have positive effects within an organisation in terms of cost savings from reduced energy consumption and waste. In the U.S. for example, a study of 500 companies found that those organisations that introduced clean production processes cut waste and emissions by up to 80 %.
There are, however, additional advantages for an organisation in seeking ISO 14001 certification. Certification can improve customer value. It provides assurance to customers, shareholders and other parties that SKF is serious about its commitment to the environment and is helping its customers to meet their obligations.
Continual development of the skills of employees is an important issue for a company competing in international markets. More than 20,000 SKF staff members have been trained so far. Eventually, the entire workforce will be involved in the education programme on environmental awareness, which supports the operation of the management system. It also gives more responsibility to employees through delegation of authority in all levels of the organisation. This can ensure that the EMS operates efficiently and contributes real benefits to the group as a whole.
Presence of an EMS can play a key role in minimising the risk of environmental accidents. As has been demonstrated in the past, the cost of rectifying such accidents is high and very damaging to a company’s reputation. ISO 14001 will improve the long-term stability of the SKF group and thus maintain share value. Indeed the pioneering work carried out by SKF in developing an EMS that can be applied groupwide across the diverse activities of the company’s individual operating units, also provides other organisations with a template on how to establish an EMS within other businesses.
Those who wait to introduce an EMS may find themselves losing competitive ground. As in the case of the quality management standard ISO 9000, which is now adopted throughout business and industry, it is forecast that ISO 14001 will evolve into a de facto standard for major companies and their suppliers.
Elaine Williams
Evolution technology editor, U.K.