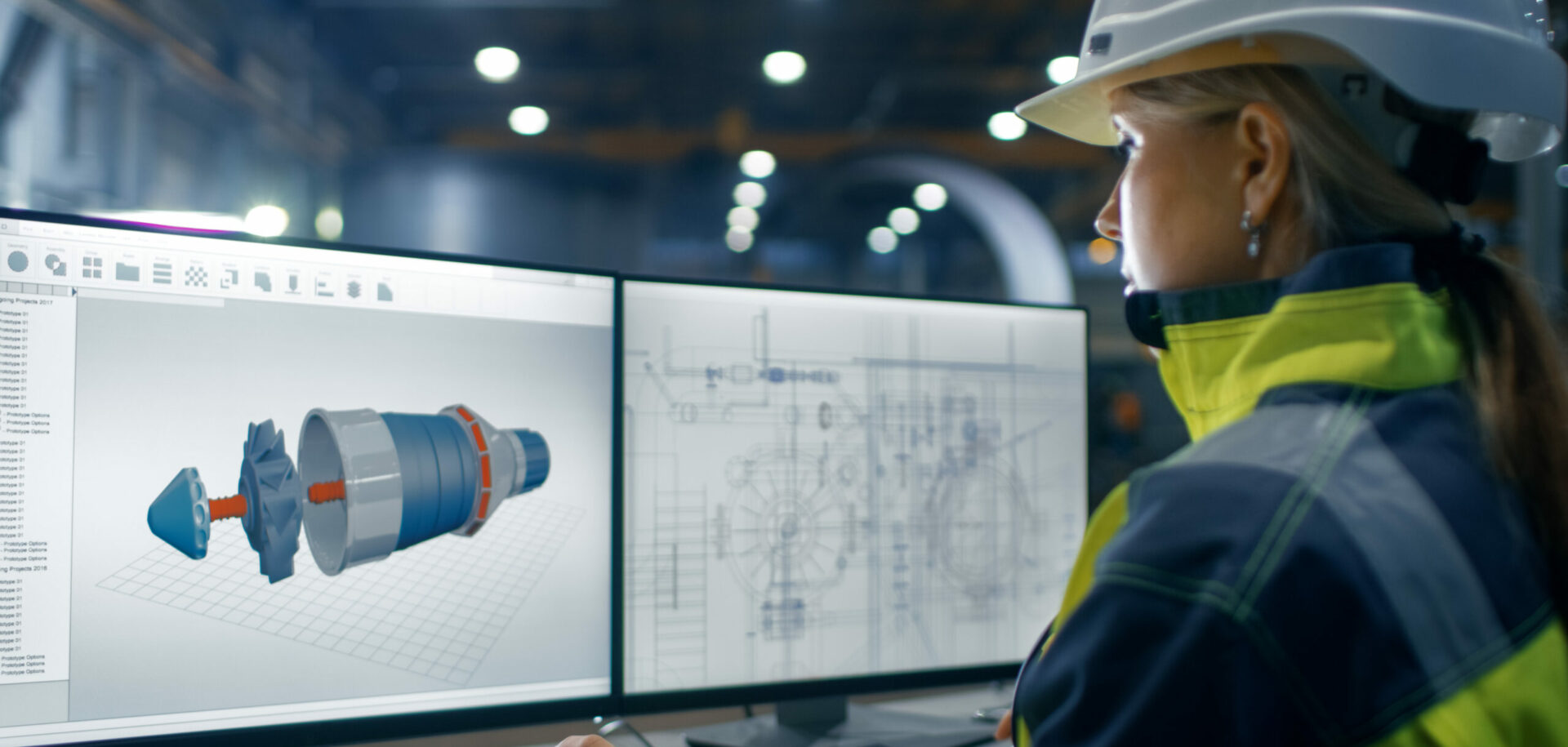
Drilling for productivity
SKF design engineering improves performance of mud bearings.
Mud motor bearings used for drilling in the oil and gas exploration industry operate under extreme conditions. They do their work deep below the earth’s surface under severe shock loads while being lubricated by mud and surrounded by abrasive materials and harsh chemical contaminants.
Downtime for mud motor replacement eats into productivity and profitability, with rig and crew costs as high as 200,000 euros a day. The inability to access the drill head during operation makes precise bearing load analysis close to impossible, but SKF has achieved an engineering clean sweep. By applying proprietary knowledge in bearing failure analysis, materials engineering, testing and bearing design, SKF has created a total bearing solution that provides dramatically enhanced performance with a 30 % increase in mean time between bearing failures.
Application
Oilfield equipment manufacturers that produce drill or moineau motors use the hydraulic force of the drilling mud to rotate the drill motor as an alternative to rotating the drill string to propel the drill bit. Pressurized to approximately 40 MPa (4 kg/mm²), the mud is pumped through the downhole drill string. The mud passes through the motor, lubricates the bearing stack, then passes through the drill bit and pushes outside the drill string, taking the drilling debris with it back to the surface. The mud and debris are then screened and filtered on the drill rig before being pumped back down the hole in a closed-loop operation.
The typical mud motor bearing stack contains eight to 12 rows of bearings, all exposed to harsh downhole conditions, including heavy and unpredictable forces, extreme shock loads and hard particle and chemical contaminants. Failures are frequent, with mean time between failures (MTBF) of just 15-20 hours in some cases, with a normal life expectancy of 100-200 hours.
Failure analysis
SKF applied a broad set of technical capabilities to determine the root cause of mud motor bearing failures. The SKF methodology went beyond bearing analysis, encompassing a review of the total application and operating environment.
Initial analysis of bearing failure modes revealed extensive wear between the rings and balls as well as ring fractures and sheared balls resulting from heavy shock loads. SKF engineers also discovered that loads were not consistent from one bearing row to the next. Using those findings as a starting point, they went to work to investigate ways to resolve the problem of premature bearing failure.
Test rig studies
The first step in the development process was to build two test rigs that could simulate the operating conditions of an actual mud bearing stack. Using these test rigs, SKF was able to achieve actual failure modes, replicating wear patterns and cracking the rings in a manner consistent with the typical failure modes the engineers had seen during their initial study. To build the test rigs, loads were calculated using the dimensions of the drill string, the density of the material being drilled and the known working pressures.
There were factors that could not be calculated with certainty, such as shear losses within the drill string, sharpness and angle of the drill cutter. However, drawing on a wide knowledge base, the SKF team was able to make fairly accurate assumptions that seemed to prove true on the test rig.
An important benefit of the test rig study was the validation of findings in the initial bearing failure analysis, showing that there was an unequal load distribution between bearings in the stack. Tests showed that the loads shift with wear.
The first row, which is exposed to large particles, wears faster. This increases the clearance between the balls and the raceways until there is no contact. The load is then shifted to the next row until that row wears. That process continues until all rows are worn equally.
The test rig studies also identified what is commonly known, that forces are flowing through the side faces of the bearing. However, this factor was underestimated in its effect and had not been seriously taken into account. Recognizing that side face dimensions have a critical effect on the service life of the bearing stack, SKF worked to equalize the forces at play within the bearing. At this point, they also realized that they would need to use a tolerance simulation tool, developed for design for Six Sigma, to analyze tolerances for individual raceways. With this tool, combined with the team’s bearing design knowledge, they would eventually re-engineer the dimensions of the side faces and achieve the optimum tolerance stack.
Materials specifications
A unique SKF competency is its depth of knowledge of materials development, particularly steel. The initial root cause failure analysis done by SKF engineers showed that the base steel as well as post-production processes would have a significant impact on bearing service life. With this in mind, the engineering team looked at alternative materials as well as various steel compositions, taking hardness, wear resistance, impurities and other factors into consideration. This has resulted in a new steel formula, developed by SKF metallurgists, that provides a consistent, specific grain structure that maximizes the effects of the heat treatment process.
Finite element analysis
One of the outcomes of the initial root cause bearing failure analysis was that, because a mud motor bearing stack must accommodate extremely heavy loads and shock loads, there was a very fine line between optimum ball size and ring thickness. Larger balls would increase load-carrying capability, but the increase in ball size would probably have a negative impact on the ability of the rings to resist cracking. The objective was to find the optimal cross section with a ball size large enough to accommodate the extreme loads and a ring thickness that would resist cracking. Engineers used finite element analysis programs combined with SKF’s proprietary software and bearing knowledge to determine that optimum balance.
Osculation is a key factor in bearing service life. Osculation of the balls and raceways – that is, the ratio of the ball radius to the raceway radius – can affect how a bearing wears in a highly contaminated environment and how it responds to various loads.
Finding the optimum degree of osculation can be a daunting task. However, SKF engineers, having studied this phenomenon for years, were able to draw on the basic aSKF factor used in bearing life calculations. From that, they were able to extrapolate the data and determine the optimum degree of osculation.
Bearing redesign
Using the findings of this comprehensive analysis, SKF manufactured a limited number of bearings of the new design for the test rig. The bearings, which featured a special steel for improved wear-resistance, a full complement of balls for increased load-carrying capacity, matched rings for optimized load distribution and a unique internal geometry to support heavy axial drilling loads and contaminants, proved to last longer than previous designs.
Results
After the positive results on the SKF test rigs, the bearings were put into operation on a customer test rig in an application with an axial load of 310 kN. The customer’s previous best-case performance for the bearing was 63 hours MTBF. The SKF redesigned mud bearing test was stopped at 86 hours and examined for wear. The bearings were still in useable condition and sent back for additional runs.
Expectations are that the SKF mud motor bearing solution will perform in downhole conditions significantly longer than the industries current 100-200 service hours – in some cases up to 50 % longer.
This increased reliability will translate to extended MTBF, enhanced productivity and cost control. With a predicted surge in worldwide drilling activity over the next few years, this improved performance offers a critical advantage for oil producers looking to gain an edge in an increasingly competitive market.
The SKF Design Process
To significantly improve bearing performance and reliability, SKF engineers used proprietary SKF design and simulation tools to:
- Accurately define the behaviour of a bearing stack
- Redesign the bearing to minimize stresses and optimize load-carrying capacity
- Test new designs and materials.
With the SKF virtual test rig, engineers were able to identify and correct the problem of cracked rings and sheared balls – two common problems with the bearings in this application.
Product features
- Special steel for all bearing components
- Full complement bearing
- Precision matched rings
- Unique bearing design to support heavy axial drilling loads.
Customer benefits
- Improved wear resistance
- Increased load-carrying capacity
- Optimized load distribution
- Increased robustness
- Improved reliability
- Customized design.