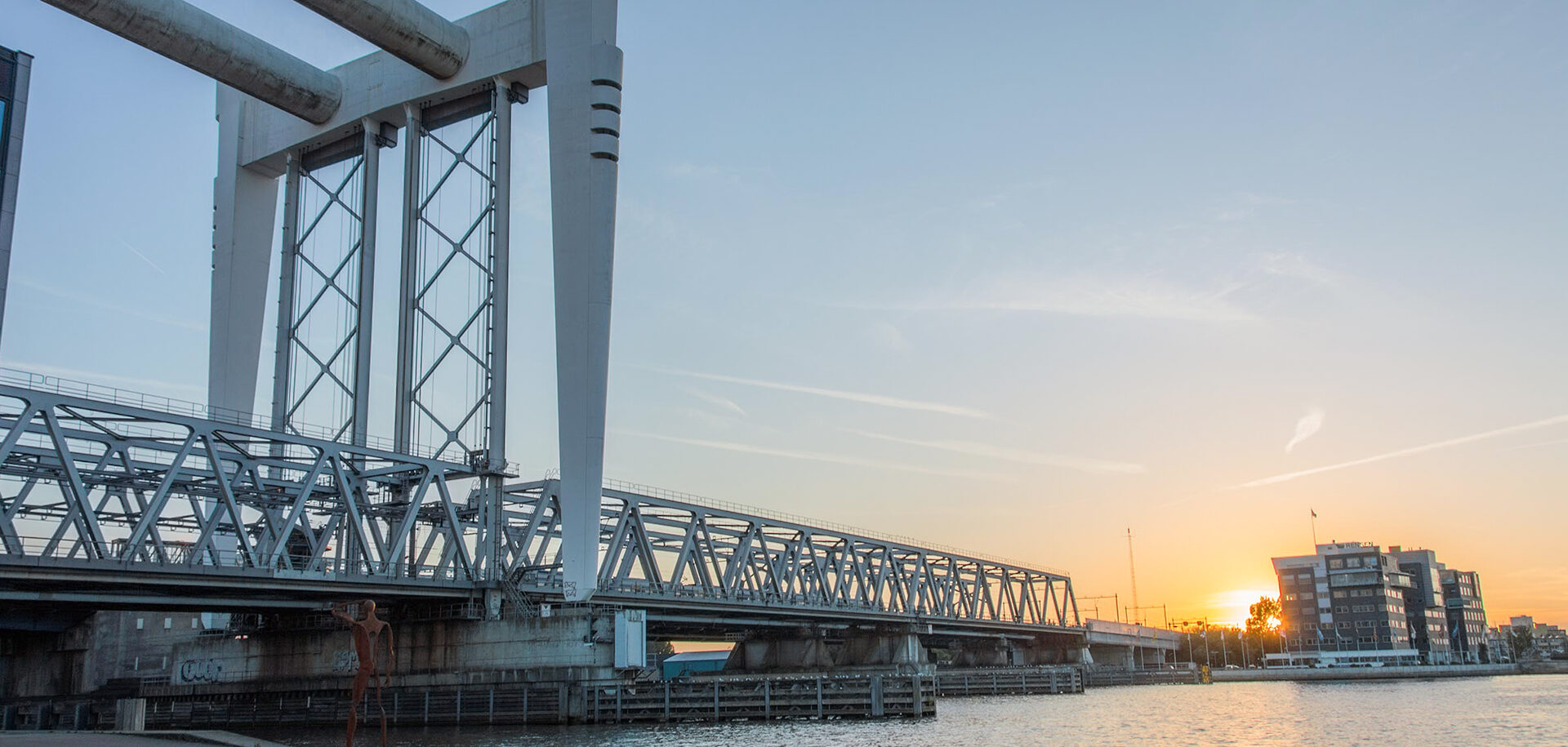
Dutch railway bridge gets a lift from new bearings
A railway bridge in the Netherlands needed new bearings on a number of wheels in the lifting mechanism in order to meet railway safety requirements. A bearing solution from SKF solved the problem, offering higher efficiency at a lower cost.
A large part of the Dutch railway system is located in the Rijn–Maas–Schelde delta, which means that trains often rely on bridges to cross the delta’s rivers. One of these bridges, on the railway line between Rotterdam and Breda, is the Dordrecht railway bridge, which crosses the Oude Maas river, a tributary of the Rhine situated near the city of Dordrecht in the province of South Holland.
The first incarnation of this railroad bridge was opened in 1872 to connect Dordrecht with Rotterdam, but the bridge in use today was built between 1990 and 1995. It comprises a fixed part with two double-track trussed bridges and a moveable part with two double-track lift bridges. Boats have 11.4 metres of clearance at the fixed part of the bridge and 46.5 metres at the lift bridge when opened.
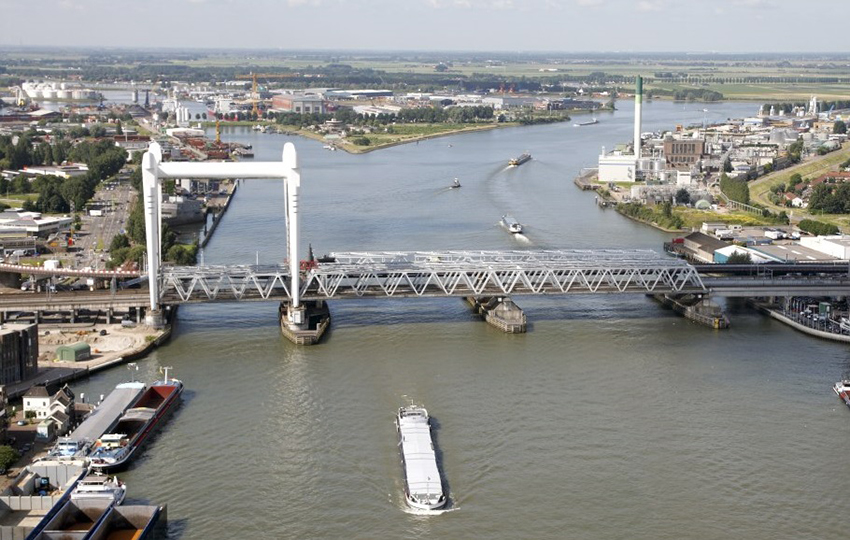
Difficulties in meeting safety requirements
The lifting mechanism is an open construction with constant exposure to wind, moisture and other possible contaminants. The corrosion and bearing failures that resulted made it difficult to meet the Netherlands’ railway safety requirements, which require that bearings have a 50-year operating life.
Dutch rail operator ProRail assigned SPIE, a technical service provider, to solve the problem. SPIE proposed exchanging the existing bearings for bearings with a larger outer diameter and other characteristics to help mitigate the situation. A third-party assessment report verified that the selected bearings were suitable, but standard procedure required a double-check, which in this case was done by SKF.
We were very pleased with SKF’s active contribution to this project.
Jaap Nieuwenhuijsen, technical manager, SPIE
“When I started looking into this application, I searched our systems to see if we already had some information about this lift bridge,” says Casper Duijndam, an application engineer at SKF. “It turned out that a colleague had carried out a bearing inspection previously. His conclusion at the time was that there was an increased risk of corrosion in the bearings. Further assessment showed that improvements in the bearing application were possible.”
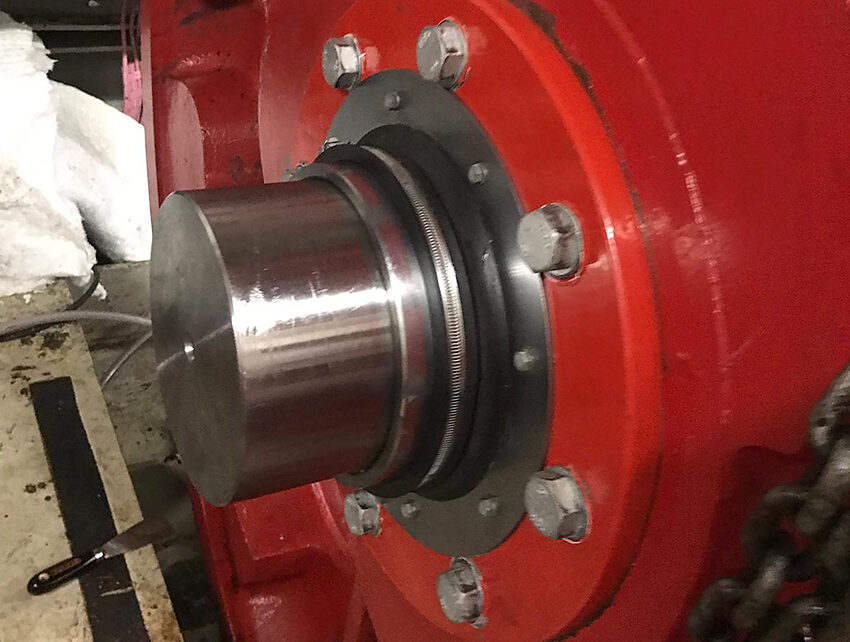
Cost-effective bearings
“We eventually worked out two options and submitted them to SPIE,” Duijndam continues. “The first option was based on the proposed construction, using sealed spherical roller bearings. The second option was to work with an open bearing and use additional customized external seals that hold the lubricant more effectively than the current labyrinth seal. This required an adjustment to the covers. In the end, the second option was chosen, partly because these bearings are more cost-effective and have better availability.”
Jaap Nieuwenhuijsen, a technical manager at SPIE, checked to see whether this option met all of ProRail’s requirements and specifications. “We verified whether the covers and sleeves supplied by SKF had a special coating and tested the exact hardness of the materials,” he says. “In addition to ensuring an optimally functioning lift bridge, the risk of corrosion in the bearings has been minimized. We were very pleased with SKF’s active contribution to this project.”
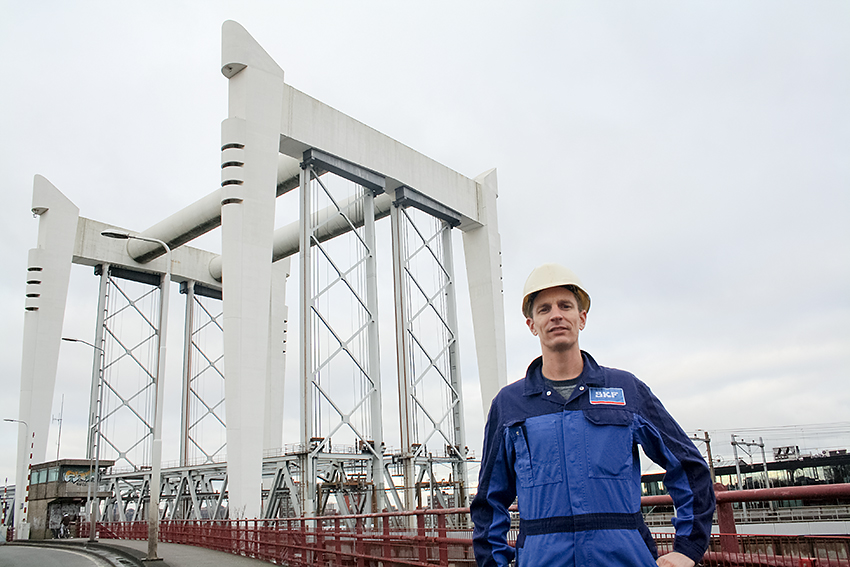
The best solutions for the customer
Duijndam explains that SKF always aims to provide the best solutions for the customer. “Partly due to technological advances and product improvements, our customers can expect us, as a supplier, to take a discerning approach to challenges in the field and give them our expert advice,” he says. “The adjustments made in this pilot project will be evaluated. Hopefully the remaining balance wheels can also be upgraded in this way.”