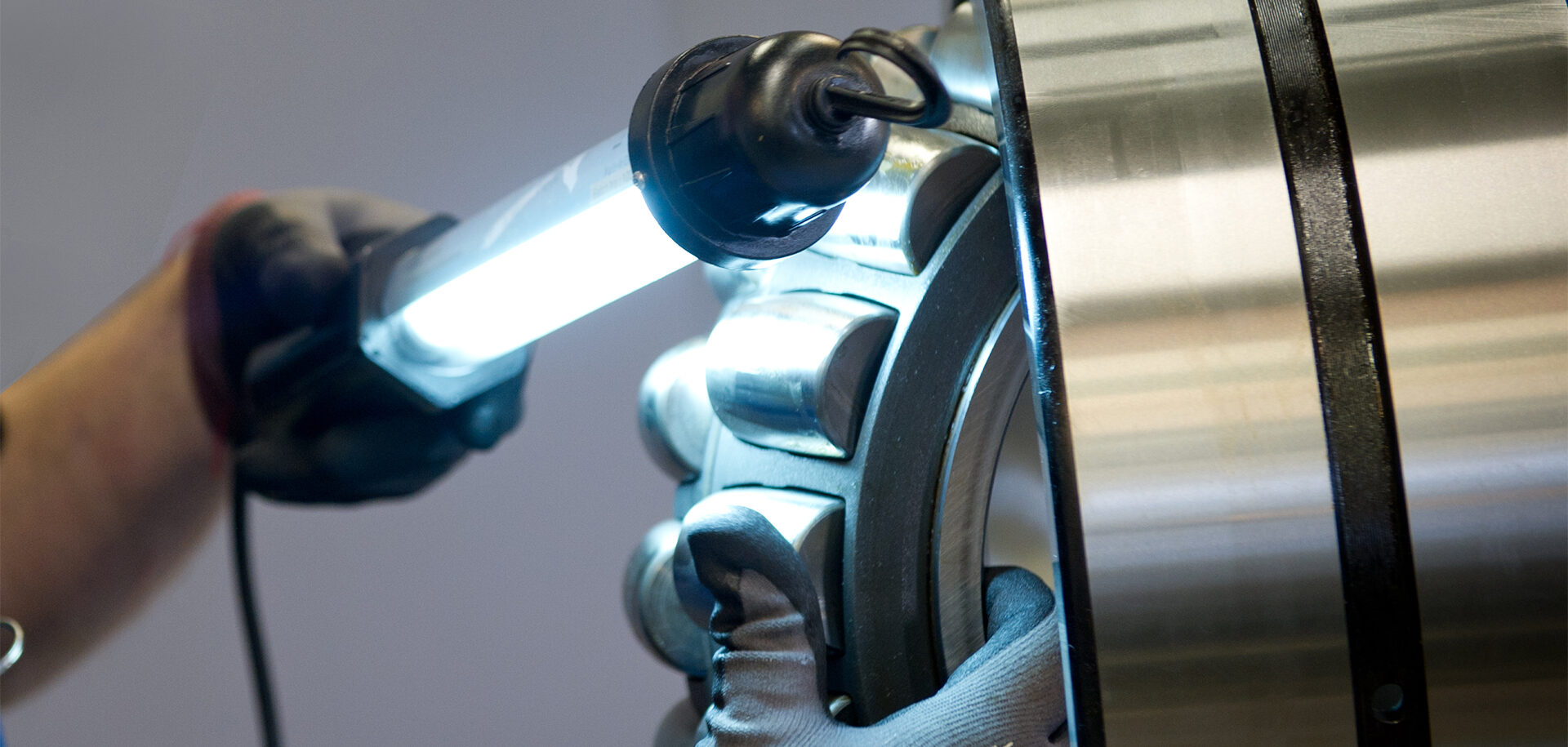
Análisis de daños en los rodamientos: ISO 15243 está aquí para ayudarle
Poder identificar los modos y causas de falla en los rodamientos es el primer paso para evitar que se repitan y mejorar la confiabilidad de la maquinaria.
Los rodamientos son uno de los elementos más comunes de la maquinaria industrial moderna. Conectan la pieza rotativa (eje) con la fija (soporte) con una fricción mínima. Facilitan un funcionamiento suave de la maquinaria, desde automóviles y aviones hasta generadores, cintas transportadoras, prensas de impresión y todo tipo de maquinaria o equipo rotativo.
El personal que trabaja con maquinaria industrial haría bien en profundizar sus conocimientos en cómo funcionan los rodamientos y, a veces, cómo fallan prematuramente.
Teniendo esto presente, la Organización Internacional de Normalización (ISO) ha publicado la norma ISO 15243, que ofrece una clasificación de los diferentes modos de falla que se producen en los rodamientos con elementos rodantes. En cada uno, la norma describe las características, el aspecto y sus posibles causas. La versión más reciente de la norma se publicó en 2017.
Además de conocer las características y el aspecto de un modo de falla, es importante comprender qué la provocó. Partiendo de ello, se dan recomendaciones de medidas correctivas para poder evitarlas en el futuro. Evidentemente, si el rodamiento funciona hasta que se produzca la falla y un agarrotamiento, entonces puede ser imposible identificarla y saber sus causas.
Aquí presentamos un resumen de los modos de falla según ISO en los rodamientos, así como sus causas. Pero, en primer lugar, un poco de información básica.
Conceptos básicos de los rodamientos
Los rodamientos son elementos de alta precisión en máquinas, fabricados de acero especial de gran dureza y, actualmente en muchos casos, con componentes rodantes de cerámica. Un rodamiento consta de aro interior y exterior, bolas o rodillos, una jaula y, opcionalmente, está tapado con sellos o una placa de protección. La figura 1 muestra las partes comunes de un rodamiento. El fabricante suministra los rodamientos tapados llenos de grasa. La lubricación, con grasa o aceite, es fundamental para el desarrollo del espesor de película lubricante necesario para separar elementos rodantes y caminos de rodadura. Un rodamiento debe seleccionarse específicamente para cada máquina, ajustarse e instalarse correctamente en ella, bien lubricado y exento de contaminación. Cuando se examinan los signos de daños, es importante conocer la geometría interna del rodamiento, y cómo se ha previsto que funcione.
Causas de las fallas
¿Qué impide que un rodamiento funcione correctamente y falle?
También es importante y, tal vez, aún más importante, comprender la causa de la falla que el modo de la falla en sí
Hay diferentes respuestas a esta pregunta, según a quién se haga. SKF realiza para sus clientes y como investigación propia muchas inspecciones y estudios de análisis de daños en rodamientos. SKF documenta los resultados en un software basado en la nube: Bearing Analysis Reporting Tool (BART). Se supervisan los motivos de la retirada de funcionamiento de los rodamientos y sus causas, junto con una clasificación de otros datos. Con ellos, SKF puede dar algunas respuestas a la pregunta: ¿por qué un rodamiento deja de funcionar?
Los datos muestran que la mayoría de los rodamientos se retiran de funcionamiento debido a vibración y ruido excesivos. También se retiran al realizar mantenimiento en la máquina o cuando se observa una temperatura excesiva (fig. 2).
Clasificación de modos de falla según ISO 15243 durante el funcionamiento de los rodamientos
ISO 15243: 2017 [Ref.1 ] clasifica los modos de falla que se producen mientras el rodamiento está instalado en el equipo/máquina y durante el funcionamiento, lo que significa que no incluye defectos referentes a la fabricación, como falta de piezas. Los modos de falla según ISO se dividen en seis categorías: fatiga por contacto rodante, desgaste, corrosión, erosión eléctrica, deformación plástica, y agrietamiento y fractura (fig.4). Cada falla se divide en subcategorías para una clasificación más específica de los modos de falla.
El manual Daño de rodamientos y análisis de fallas [Ref.2] puede ser útil para identificar los modos de falla y sus causas.
Las seis clasificaciones se describen a continuación:
Fatiga por contacto rodante (ISO 5.1)
La fatiga por contacto rodante está clasificada en dos subcategorías: fatiga iniciada debajo de la superficie e iniciada en la superficie. La fatiga iniciada debajo de la superficie (ISO 5.1.2) (fig. 5) la causa la carga cíclica sobre las superficies de contacto rodante que, con el tiempo, origina un cambio en la estructura del material, y se inician microgrietas. Las microgrietas se desarrollan debajo de la superficie, frecuentemente en una inclusión en el material, y se propagan hasta la superficie como desconchado. Sobre la fatiga, influye la calidad del rodamiento, las cargas aplicadas, la lubricación y la limpieza. Son factores vinculados con la vida nominal del rodamiento, L10mh. La fatiga debajo de la superficie puede acelerarse si el rodamiento está sometido a altas tensiones debidas, por ejemplo, a sobrecarga temporal o a otro factor que debilite el material. En estos casos, la vida a fatiga es breve (del 5 % al 10 % de L10mh). La fatiga iniciada en la superficie (ISO 5.1.3) (fig. 6) tiene lugar en la superficie de rodadura y generalmente está causada por deformación superficial debida a lubricación o limpieza deficientes. Una película lubricante inadecuada y el aplastamiento sobre contaminación sólida pueden ocasionar un contacto de metal con metal, y hacer que las asperezas en la superficie se corten entre sí. Luego pueden producirse microgrietas, seguidas de microdesconchado y finalmente fatiga iniciada en la superficie.
Desgaste (ISO 5.2)
La categoría siguiente es desgaste. ISO clasifica el desgaste en dos subcategorías: desgaste abrasivo y desgaste adhesivo. El desgaste abrasivo (ISO 5.2.2) (fig. 7) es el desprendimiento progresivo de material, generalmente en presencia de material abrasivo, tal como partículas contaminantes. El desgaste abrasivo también puede producirse debido a una lubricación inadecuada. En general se caracteriza por el aspecto opaco de las superficies. El desgaste abrasivo es un proceso degenerativo que eventualmente puede destruir la microgeometría de las superficies rodantes de un rodamiento. Las partículas abrasivas pueden desgastar rápidamente los caminos de rodadura de los aros y elementos rodantes, al igual que las cavidades de la jaula. La causa puede ser la penetración de material contaminante en el lubricante y rodamiento, y la falta de lubricante en el contacto rodante.
Corrosión (ISO 5.3)
La siguiente categoría, corrosión, se clasifica en tres categorías: corrosión por humedad, corrosión por fricción y vibrocorrosión. La corrosión por humedad (5.3.2) (fig. 9) es un problema clásico de penetración de humedad en el rodamiento. El material de elevada dureza de los rodamientos posee una baja resistencia a la corrosión. La humedad causará daños en los espacios de separación de los elementos rodantes cuando el rodamiento está parado. El deterioro de la superficie puede conducir a fatiga iniciada en ella posteriormente al funcionar. La humedad degrada considerablemente la capacidad del lubricante de desarrollar el espesor de una película en un rodamiento en funcionamiento. La corrosión por contacto (ISO 5.3.3.2) (fig. 10) se produce cuando hay micromovimientos en una interfaz entre superficies en contacto, como entre el aro interior del rodamiento y el eje, y el aro exterior del rodamiento y el soporte. Puede deberse a un montaje incorrecto del rodamiento en el eje o en el soporte, según la carga aplicada. Por ejemplo, para evitar la corrosión por contacto, un rodamiento con un aro interior giratorio y una carga constante aplicada precisa que su aro interior tenga en el eje un cierto ajuste de interferencia mínimo. De igual manera, para evitarla, un rodamiento con un aro interior giratorio y una carga rotativa aplicada en el aro interior requiere un cierto ajuste de interferencia del aro exterior en el soporte. La corrosión por contacto se presenta como una oxidación roja/negruzca en la interfaz. La vibrocorrosión (ISO 5.3.3.3) (fig. 11) surge en la zona de contacto entre los elementos rodantes y el camino de rodadura sujeto a un pequeño movimiento oscilante o de vibración. El desgaste se produce en los espacios de separación de los elementos rodantes. El desgaste elimina el acabado de fabricación original de las superficies y también puede producir una oxidación roja/negruzca en ellas, similar a la corrosión por contacto. La extensión del desgaste depende de la intensidad de la carga aplicada, la intensidad de la oscilación y vibraciones, y de las condiciones de lubricación.
Erosión eléctrica (ISO 5.4)
Hay dos clasificaciones de erosión eléctrica: erosión por corriente excesiva y erosión por fugas de corriente. La erosión por corriente excesiva (ISO 5.4.2) (fig. 12) se produce cuando la corriente pasa por un aro del rodamiento, a través de los elementos rodantes y por el otro aro. En las superficies de contacto, el proceso es similar a la soldadura por arco eléctrico (gran densidad de corriente por una superficie de contacto pequeña). El material es calentado a temperaturas que oscilan entre los niveles de templado y de fusión. Esto hace que se presenten zonas descoloridas, de tamaño variado, en las que el material ha quedado templado, endurecido o fundido. Se forman cráteres donde se ha fundido el material y, como consecuencia, se fragmentan debido a la rotación del rodamiento. El material excedente desgastado se desprende. A la erosión por corriente excesiva puede causarla el impacto de rayos en la maquinaria, cuando reparaciones con soldadura en la maquinaria se efectúan con una conexión a tierra inadecuada del equipo de soldar, etc. La erosión por fugas de corriente (ISO 5.4.3) (fig. 13) tiene lugar cuando corriente de intensidad algo baja pasa por el rodamiento. Generalmente los daños se presentan en forma de pequeños cráteres próximos entre sí y la aparición de un aspecto gris/ondulado con el transcurso del tiempo. Los elementos rodantes pueden tener un aspecto gris, opaco, y el lubricante quedar descolorido. La extensión de los daños depende de la intensidad de la corriente, su duración, la carga sobre el rodamiento, la velocidad y el lubricante. La erosión por fugas de corriente es común en motores eléctricos que tengan corrientes parásitas, cuando el eje no está adecuadamente conectado a tierra y el motor está controlado por un variador de frecuencia.
Deformación plástica (5.5)
ISO clasifica la deformación plástica en dos categorías: deformación por sobrecarga y mellas por partículas. La deformación por sobrecarga (ISO 5.5.2) (fig. 14) es un daño mecánico causado por sobrecarga estática, como una manipulación inadecuada (caída desde altura del rodamiento), montaje incorrecto (golpes de martillo sobre el rodamiento), cargas máximas durante el funcionamiento de la maquinaria, etc. Puede manifestarse como mellas del camino de rodadura o muescas en los espacios de separación de los elementos rodantes, daños en las jaulas, sellos y placas de protección, etc. Las mellas por partículas (ISO 5.5.3) (fig. 15) se producen por el aplastamiento de partículas sólidas contaminantes o impurezas en la zona de contacto rodante del rodamiento, lo que provoca mellas (deformaciones) en los caminos de rodadura y elementos rodantes. El tamaño, tipo y dureza de las partículas influye en el alcance de los daños. El aplastamiento posterior de las mellas puede conducir a que se produzca fatiga iniciada en la superficie (ISO 5.1.3).
Agrietamiento y fractura (ISO 5.6)
La categoría final de ISO es agrietamiento y fractura. Se clasifica en tres categorías: fractura forzada, fractura por fatiga y agrietamiento térmico. La fractura forzada (ISO 5.6.2) (fig. 16) se produce cuando las tensiones superan la resistencia a la tracción del material. Las causas comunes de una fractura forzada son una tensión circunferencial demasiado alta del montaje de un rodamiento en un eje con un ajuste de interferencia excesivo, o el calado excesivo de un rodamiento con agujero cónico en un asiento de eje o manguito de montaje cónicos. La fractura por fatiga (ISO 5.6.3) (fig. 17) se presenta cuando la resistencia a la fatiga del material se excede durante flexiones cíclicas. Una flexión repetida origina una grieta que se propaga por el aro o la jaula. Esto puede suceder en un rodamiento si está sometido a cargas pesadas y el soporte que lo sostiene no proporciona una rigidez uniforme, lo que somete al aro exterior a tensiones cíclicas elevadas. El agrietamiento térmico (ISO 5.6.4) (fig. 18) se produce cuando dos superficies se deslizan entre sí, lo que genera calor por fricción. Si el deslizamiento es sustancial, el endurecimiento local de las superficies en combinación con el desarrollo de tensiones de tracción residuales altas causa grietas, que generalmente están orientadas en ángulo recto respecto del sentido del deslizamiento. El agrietamiento térmico puede producirse, por ejemplo, si un soporte fijo entra en contacto con el aro giratorio del rodamiento.
Se puede encontrar una descripción más detallada de los modos de falla de los rodamientos y sus causas en la Referencia 2.
Hay que tener presente que el lubricante (aceite o grasa) del rodamiento dañado también puede proporcionar información al investigar el rodamiento. Debería tomarse una muestra de lubricante para compararla con una muestra de lubricante nuevo. Puede hacerse un análisis del lubricante para considerar el contenido de contaminación por partículas y humedad, los cambios en la viscosidad, el cambio en la consistencia de la grasa, etc.
También puede proporcionar datos el examen de los sellos o la placa de protección del rodamiento y otros componentes, como el manguito.
Las técnicas de mantenimiento predictivo o mantenimiento basado en la condición, como análisis de vibración, termografía, análisis del aceite, etc., pueden usarse para detectar fallas antes de que se produzcan daños graves en el rodamiento y también posibles daños en el equipo en el que funciona el rodamiento. Esto puede permitir una mejor identificación del modo de falla. La retirada del funcionamiento de rodamientos de gran tamaño (agujero > 200 mm) antes de que se produzcan daños extensos puede permitir su reacondicionamiento. Esto puede restituir el rodamiento a una condición de “como nuevo”, y reducir los costos de mantenimiento y el impacto medioambiental (fig. 19).
Modos de falla más comunes
Los datos1 de SKF identifican que los cinco modos de falla más comunes son el desgaste abrasivo (26 %), la fatiga iniciada en la superficie (16 %), la corrosión por humedad (14 %), el desgaste adhesivo (7 %) y la erosión por fugas de corriente (7 %) (fig. 20). Estos modos de falla representan aproximadamente el 70 % de todos los identificados en la investigación de rodamientos, aun cuando la corrosión por contacto se observa en la mayoría de los rodamientos, si bien es de escasa importancia. Se han observado los demás modos de falla según ISO, pero en menor medida.
SKF Bearing Analysis Reporting Tool (BART)
El software SKF BART utilizado por los ingenieros de SKF ahora está disponible para los clientes de SKF. El cliente recibe instrucción básica sobre rodamientos, técnicas para inspeccionarlos y uso del software SKF BART. Para rellenar el informe de inspección, el cliente trabaja estrechamente con un ingeniero o especialista de aplicaciones de SKF. El informe de inspección BART es aprobado por el experto de SKF. La inspección puede revelar si el rodamiento debiera sustituirse, puede reutilizarse, tiene posibilidades de reacondicionamiento o debe desecharse. También puede usarse para documentar la inspección de un rodamiento nuevo antes de ponerlo en servicio. Esto puede ser útil si un rodamiento ha estado almacenado durante largo tiempo.
Si fuera necesario, puede efectuarse un análisis de daños completo por un ingeniero de aplicaciones de SKF, a fin de obtener recomendaciones para mejorar la confiabilidad. Los ingenieros de SKF pueden usar inteligencia artificial (IA) [Ref. 3] para reforzar su análisis de daños. La IA utiliza un sistema de visión computarizada que evalúa los daños en rodamientos mediante fotografías digitales. El sistema usa inteligencia artificial en forma de un algoritmo de reconocimiento de imagen de red neuronal entrenado con miles de imágenes de rodamientos dañados de los archivos de SKF.
Resumen
En síntesis, la norma ISO 15243 es útil para clasificar los modos de falla de los rodamientos que funcionan en maquinaria, y puede ser útil para identificar las causas de las fallas. La familiarización con los modos de falla comunes y sus causas permite adoptar medidas correctivas para evitar que se repitan. Esto puede reducir considerablemente el riesgo de fallas no planificadas y de efectos catastróficos, y mejorar potencialmente la confiabilidad y disponibilidad de la maquinaria. Los rodamientos que se retiran para recibir mantenimiento pueden inspeccionarse para su reutilización o, tal vez, para su reacondicionamiento.
Los modos de falla de los rodamientos, los datos de su causa y otra información conexa se recopilan para comprender mejor cómo funcionan los rodamientos. SKF usa el software SKF BART, que también está disponible para los clientes a fin de realizar inspecciones de rodamientos e informes de análisis de daños.
1 SKF Bearing Analysis Reporting Tool
Referencias
[1.] Norma Internacional ISO 15243:2017 “Rolling bearings damage and failures – terms, characteristics and causes”
[2.] Folleto 14219 de SKF, “Daño de rodamientos y análisis de fallas”
[3.] Artículo en la revista Evolution de SKF, “El futuro del análisis de fallas en los rodamientos ya está aquí” (2022)