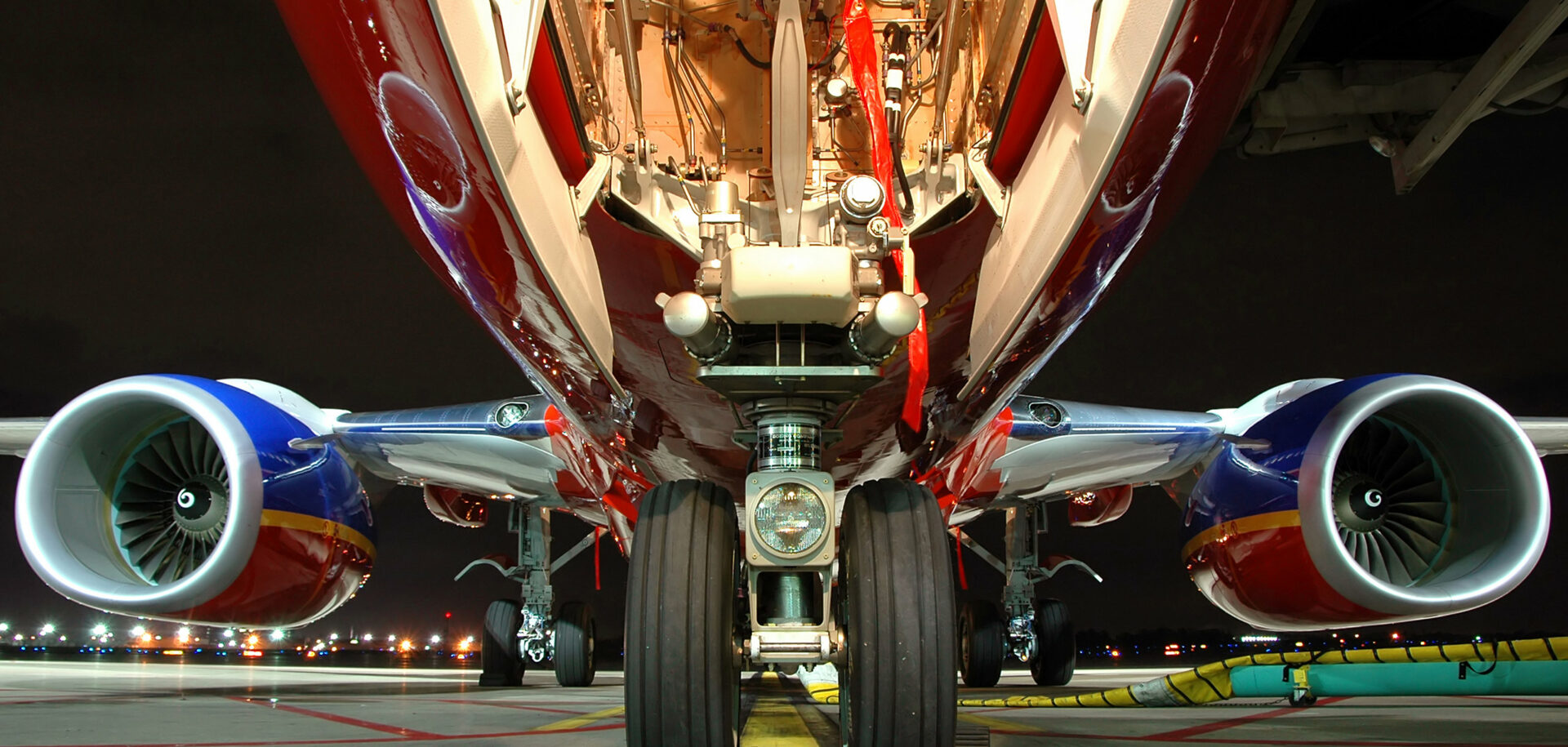
¡Bienvenido a bordo!
Los ingenieros de SKF Aerospace colaboran con los clientes en el desarrollo de innovaciones.
Resumen
La industria aeroespacial ha saltado de innovación en innovación durante las décadas posteriores al primer vuelo de los hermanos Wright, en 1903, con un avión más pesado que el aire provisto de motor. SKF Aerospace es un potente líder en tecnología innovadora que ha contribuido al avance de la industria aeroespacial, y la empresa continúa trabajando codo a codo con los clientes para abordar los retos del futuro.
Para la industria aeroespacial, la última década ha demostrado ser la época más interesante, dinámica e innovadora de su historia. Pedidos comerciales récord, nuevas normas gubernamentales y medioambientales, precios de combustible impredecibles y conflictos globales son solo algunos factores clave que han impulsado una introducción sin precedentes de nuevas plataformas e implementaciones tecnológicas. Equipos técnicos de SKF Aerospace trabajan codo a codo por todo el mundo con clientes de SKF para superar los retos actuales y futuros.
La carrera por la velocidad y la confiabilidad
La aviación tiene más de 2 000 años de historia, desde sus formas más primitivas, con cometas e intentos de saltos desde torres, hasta vuelos supersónicos e hipersónicos con aviones más pesados que el aire provistos de motores a reacción. Inventores famosos como Leonardo da Vinci, John Stringfellow y Lawrence Hargrave concibieron extrañas máquinas para volar, mucho antes del famoso primer vuelo de los hermanos Wright en Kitty Hawk. Experimentos con planeadores proporcionaron los elementos básicos para crear aeroplanos más pesados que el aire y, a principios del siglo XX, los adelantos en la tecnología de los motores y la aerodinámica hicieron posible por primera vez el vuelo controlado a motor.
El 17 de diciembre de 1903, a las 10:35 a. m., los hermanos Wright, con Orville ante los mandos, hicieron el primer vuelo a motor con un aparato más pesado que el aire. Su duración fue de 12 segundos y alcanzó los 36,5 metros (fig. 1). El aeroplano moderno, con su característica cola, quedó establecido en 1909 y, desde entonces, la historia de la aviación ha estado vinculada al desarrollo de motores cada vez más potentes.
Entre las décadas del cuarenta y del sesenta, la velocidad de los aviones se cuadruplicó, con bocetos de aparatos incluso más rápidos ya en la mesa de dibujo, proyectos que hoy son una realidad gracias al posible retorno de los vuelos supersónicos. En 1907 el pionero de la aviación Glenn Curtiss estableció un récord mundial de velocidad (220 km/h), aunque no con un avión sino con una motocicleta (fig. 2).
Seis años más tarde, en 1913, uno de los primeros motores diseñados especialmente para uso en aviación, el motor giratorio Gnome –un dispositivo de 14 cilindros, 117 kW (160 CV) montado en el aeroplano de madera del francés Louis Béchereau–, ganó el Trofeo de aviación Gordon Bennett con una velocidad promedio de 200 km/h.
Después de la Primera Guerra Mundial, un impulso militar de alcance mundial en tecnología acentuó la carrera de la velocidad, al mismo tiempo que las primeras normas de la industria de la aviación se centraron en la seguridad, y se convirtieron en decisivas para la evolución del tráfico aéreo.
Un importante hito en los anales del vuelo y la velocidad es el SR-71 Blackbird de Lockheed Martin (fig. 3). En 1976 batió la marca mundial de velocidad aerodinámica y altitud, 3 529,6 km/h a una altitud de 25 929 m, un récord que todavía no ha sido superado.
El SR-71 realizó regularmente misiones a velocidades superiores a Mach 3 y podía reconocer por hora más de 250 000 km2 de superficie terrestre desde una altura de 24 km. Esas extremas condiciones de funcionamiento permitían evitar con seguridad aviones de caza o misiles, pero también obligaban a sus dos tripulantes a ir equipados con trajes tipo astronauta para el caso de pérdida de presión en la cabina.
Motores: aspectos generales
Detrás de cada uno de los aviones antes mencionados hay una unidad motriz. Anteriormente había una gran abundancia y variedad de formas de propulsar un avión. Sin embargo, hoy el sistema más comúnmente usado en los vuelos comerciales es el turbofan (fig. 5), un desarrollo del turborreactor.
Un turborreactor es un motor con turbina de gas, que funciona comprimiendo el aire, con una boca de entrada y compresor (axial, centrífugo o ambos sistemas), y mezcla el combustible con el aire comprimido, realiza la combustión de la mezcla en una cámara y hace circular el aire calentado a alta presión por una turbina y una boquilla. El compresor es accionado por la turbina, que obtiene energía del gas expandido que circula por ella. El motor convierte la energía interna del combustible en energía cinética en el punto de salida, con lo que genera empuje. Todo el aire que penetra por la boca de entrada pasa por el compresor, la cámara de combustión y la turbina. Debido a que el turborreactor es un motor térmico, cuanto más elevada es la temperatura de combustión, mayor es la expansión de los gases.
Además, un turbofan tiene un ventilador (fig. 5), para enviar una parte del aire alrededor del núcleo, en lugar de a través de este. El flujo másico de aire que rodea el núcleo en comparación con el flujo másico que pasa a través de él se conoce como “índice de derivación”. La ventaja principal de un turbofan es la reducción considerable en consumo de combustible y en nivel de ruido. Algunos de los más recientes turbofans tienen índices de derivación de hasta 12:1.
SKF Aerospace
SFK Aerospace tiene más de 2 500 empleados y es uno de los mayores fabricantes del mundo de rodamientos para el mercado de los motores aeronáuticos. SKF es líder en rodamientos de motores de aviación, de fuselaje y elastoméricos, en soluciones estructurales de materiales compuestos, sellos, unidades y tecnología afín. Con su oferta de una amplia gama de soluciones innovadoras, SKF contribuye a la transformación de la industria aeroespacial prestando asistencia a constructores de aviones para que puedan atender diversas demandas de los clientes. Esto es lo que continúa haciendo avanzar a SKF.
América del Norte
SKF Aerospace inició sus actividades en Estados Unidos en 1940 al adquirir SKF una fábrica de rodamientos para aviación en Filadelfia, Pensilvania. Para hacer frente a la creciente demanda de rodamientos de la industria aeronáutica, en 1986 SKF adquirió MRC, una empresa de la División de Rodamientos TRW, situada en Falconer, Nueva York (fig. 6). La adquisición de MRC incluía una planta de rodamientos de bolas de precisión en Winsted, Connecticut. Posteriormente, SKF abandonó las instalaciones de rodamientos aeroespaciales en Filadelfia, y transfirió parte de la producción a los talleres de MRC. En 1990 SKF adquirió Chicago Rawhide, hoy SKF Sealing Solutions, radicada en Elgin, Illinois. Los sellos y productos de control de movimiento para el sector aeroespacial se fabrican actualmente en esas instalaciones.
En el año 2000, SKF estableció su Aero Bearing Service Center (ABSC) en Charleston, Carolina del Sur. ABSC se especializa en servicios de supervisión y reparación de rodamientos de motores de aviación. En 2007 SKF participó en una empresa conjunta con General Electric Aircraft Engines para establecer una planta de fabricación en Ladson, Carolina del Sur. En 2013 SKF adquirió Kaydon Corporation, que fabrica productos para todos los segmentos, incluido el sector aeroespacial. La cartera de productos aeroespaciales de Kaydon abarca sellos de carbono y circunferenciales. Los sellos de carbono se utilizan principalmente en rodamientos del eje principal en aplicaciones de motores de avión y equipos aeroespaciales. Los sellos de los ejes de motores de turbinas en equipos aeroespaciales están concebidos para sellar la sección del rodamiento del eje principal y el cárter de aceite, a fin de obtener un funcionamiento más eficiente y sostenible desde el punto de vista medioambiental.
Europa
SKF Aerospace Europe inició sus actividades con Clevedon, en North Somerset, Inglaterra. Formalmente era conocida como AMPEP, Aerospace. Esta sociedad se fundó en 1963 y fue adquirida por SARMA, una empresa de SKF. En 2005 se realizó otro cambio, al convertirse AMPEP en SKF (U.K.) Limited, Aerospace – Clevedon. Clevedon se especializa en el diseño y la fabricación de rodamientos autolubricantes revestidos de PTFE/fibra de vidrio para aplicaciones aeroespaciales e industriales. Estos componentes se usan ampliamente en aplicaciones de ala fija y helicópteros, principalmente en el movimiento de superficies de control de vuelo. En 1966 SKF adquirió la fábrica de rodamientos de RIV en Villar Perosa, Italia. La planta de Villar Perosa fabrica rodamientos y soluciones diseñados a medida para motores aeronáuticos, equipos de transmisión y otras aplicaciones especiales de alta tecnología. En 1971 SKF construyó una fábrica en Lons-le-Saunier, Francia. En 2005 SKF se hizo cargo del 100% del control de la fábrica de Stonehouse, en Gloucestershire, Inglaterra. Stonehouse tiene 90 años de historia como fabricante de rodamientos e importante proveedor de empresas aeroespaciales en todo el mundo. En 2006 SKF adquirió SNFA, un fabricante líder francés de rodamientos de alta precisión. Fundada en 1952, la SNFA tiene su sede en Valenciennes. La empresa diseña y fabrica rodamientos de alta precisión para aplicaciones aeroespaciales, espaciales y proyectos especiales. En 2013 abrió sus puertas en Valence, Francia, el Aerospace Technical Center Europe. En él trabajan ingenieros altamente calificados en el desarrollo de productos avanzados, y está equipado con instalaciones de clase mundial para pruebas de soluciones aeroespaciales.
Avances en aceros de rodamientos aeroespaciales
A medida que la industria aeroespacial iba ensanchando los límites de muchas tecnologías, los rodamientos seguían siendo un componente clave en estos logros. Para los rodamientos del motor del eje principal y de la caja de engranajes eran sumamente importantes los avances en materiales y el procesamiento térmico (forjado, tratamiento térmico, etc.). Era un aspecto primordial y sigue siéndolo en la actualidad (fig. 7).
A medida que los motores se iban diseñando específicamente para la aviación, lo mismo sucedió con los componentes y, a partir de la década del treinta hasta la del cincuenta, el mejor material para fabricarlos era el acero de rodamientos “sucio” (inicialmente el 52100). Aunque su composición era deficiente para los estándares actuales, tenía una confiabilidad aceptable. Cuando los gobiernos se convirtieron en una fuerza impulsora de las cadenas de suministro, las normas industriales establecieron requisitos mínimos en los materiales de importancia crítica, por ejemplo, en el Convenio de Chicago, de 1944, las primeras normas globales de la aviación. Esto condujo a que la aviación militar abriera el camino a que se aplicaran planes de procesamiento con congelación y diseños de rodamientos controlados por fabricantes de equipos originales de motores y cajas de engranajes, lo que mejoró la confiabilidad y redujo los riesgos. Durante la década del sesenta, el M50 fue el primer acero desarrollado especialmente para rodamientos de motores de aeronáutica. En ellos el M50 significó que las características del acero dejaban de ser el factor limitante para funcionamiento a altas temperaturas. La lubricación se convirtió en el factor restrictivo, y lo sigue siendo. En comparación con el 52100 inicial, se obtuvieron mejoras significativas en el ciclo de vida de los componentes, con límites de temperatura mucho más elevados. El progreso que significó el acero cementado en caja M50NiL permitió integrar características estructurales en los diseños de rodamientos para motores de aviación, al mismo tiempo que se mantenían las demás características de alto rendimiento. Debido a que el acero cementado en caja tiene más tensiones residuales de compresión en la superficie de contacto, aumenta su resistencia ante la fatiga por contacto rodante. La mayor elasticidad de su núcleo “más blando” permite al diseñador utilizar encajes más ajustados, lo cual es preciso con el incremento de las velocidades operativas y los efectos de la expansión del aro con respecto al eje.
Estas propiedades deben mantenerse a temperaturas que pueden alcanzar, y en algunos casos superar, los 200 °C, donde el material debe mantener una dureza superficial de ~58 HRC como mínimo para asegurar un funcionamiento confiable. La nitruración del M50/M50NiL puede incrementar significativamente la dureza superficial (hasta ~70 HRC), lo que da como resultado la importante característica de mayor resistencia a la contaminación. La nitruración es la adición de nitrógeno a la superficie mediante un proceso de difusión. El resultado es un perfil con contenido de nitrógeno que proporciona mayor dureza. Al nitrurar aceros de grado aeroespacial, extensas pruebas han mostrado la importancia de la microestructura resultante (p. ej., sin capa blanca superficial ni precipitados en los contornos de los granos) para lograr todos los beneficios del proceso. Debido a que la nitruración es lenta y costosa, hoy se usa principalmente en rodamientos grandes para motores de eje principal (agujero >120 mm) (fig. 10). Se prevé que las condiciones de funcionamiento de la próxima generación de rodamientos de motores de avión (2030+) superarán las características de los materiales de acero para rodamientos actualmente usados (fig. 8).
De hecho este fenómeno ya está haciendo que diseños emergentes de motores de alto rendimiento incorporen combinaciones de materiales y tratamientos de superficie alternativos para mejorar la vida útil actual y el rendimiento del material, incluidos los rodamientos híbridos (caminos de rodadura de acero y bolas de nitruro de silicio) y aceros nitrurados M50 y M50NiL. De los numerosos materiales investigados durante las dos últimas décadas y que podrían ser candidatos, el Pyrowear®675 (P675) parece destacarse como el que presenta todas las propiedades que se desean para una próxima generación de aleaciones para rodamientos, incluidos: resistencia a temperaturas altas, manteniendo ~58 HRC a 357 °C, fusión en doble vacío, resistencia a la corrosión, importante tensión residual de compresión en caja, poca austenita retenida, capa cementada de grano de tamaño fino y carburos grandes equilibrados para resistencia al desgaste sin reducción en la vida a fatiga por contacto rodante (RCF). El P675 es un acero inoxidable martensítico de grado cementado y alta resistencia desarrollado por la Carpenter Technology Corporation.
Salto al futuro
Hace cincuenta años, la revista Aviation Week publicó un anuncio en el que describía el “nuevo” Boeing 737, que ya tenía 124 pedidos de 15 compañías aéreas. Esto sería el punto de partida de la primera familia de turborreactores del mundo. Este avión se diseñó para incrementar el rango de alcance y con elementos comunes con los Boeing 707 y 727. Tenía como novedad asientos en filas de seis. Hizo su primer vuelo el 9 de abril de 1967, y se suministró el primer ejemplar del 737-100 a Lufthansa, Alemania. Hoy, el 737 continúa batiendo récords con una cartera de pedidos de más de 13 000 unidades y con más de 8 800 ejemplares entregados desde que empezó a fabricarse. Actualmente se está probando el 737 MAX, que incorporará el motor CFM LEAP como única unidad propulsora (fig. 9). CFM International es una empresa que tienen al 50% GE Aviation en EE.UU. y Sneema en Francia.
LEAP es la próxima generación de motores de avión diseñados y desarrollados para reducir el consumo de combustible, las emisiones y los niveles de ruido. Los aviones Boeing 737 MAX, Airbus A320neo y COMAC C919 irán equipados con variantes del motor LEAP.
Los CFM LEAP son los motores preferidos para la próxima generación de aviones de un solo pasillo (fig. 9). El LEAP-1A es una opción del Airbus A320neo; el LEAP-1B es el único equipo de propulsión del Boeing 737 MAX; y el LEAP-1C es el motor de procedencia occidental del COMAC C919. Estos equipos han conseguido pedidos de más de 50 clientes de todo el planeta.
SKF ha mantenido una larga relación comercial con CFM International, y aportó a lo largo de la labor de desarrollo del motor LEAP conocimientos en tecnología de fabricación, diseño y pruebas del eje principal, así como de los rodamientos de cajas de engranajes accesorias. Los rodamientos híbridos cerámicos del eje principal desarrollados para el programa de motores LEAP contribuirán a que el motor sea más liviano, silencioso y ahorrador de combustible, con un nivel de emisiones de carbono de hasta un 16% menor que su predecesor, el CFM56.
“Participar en uno de los programas de desarrollo de motores más prestigiosos de la industria es una gran oportunidad para SKF”, manifiesta Rutger Barrdahl, director de SKF Aerospace. También es un reconocimiento de que el enfoque de colaboración en el desarrollo tecnológico de SKF respalda el énfasis que pone la industria en reducir las emisiones.