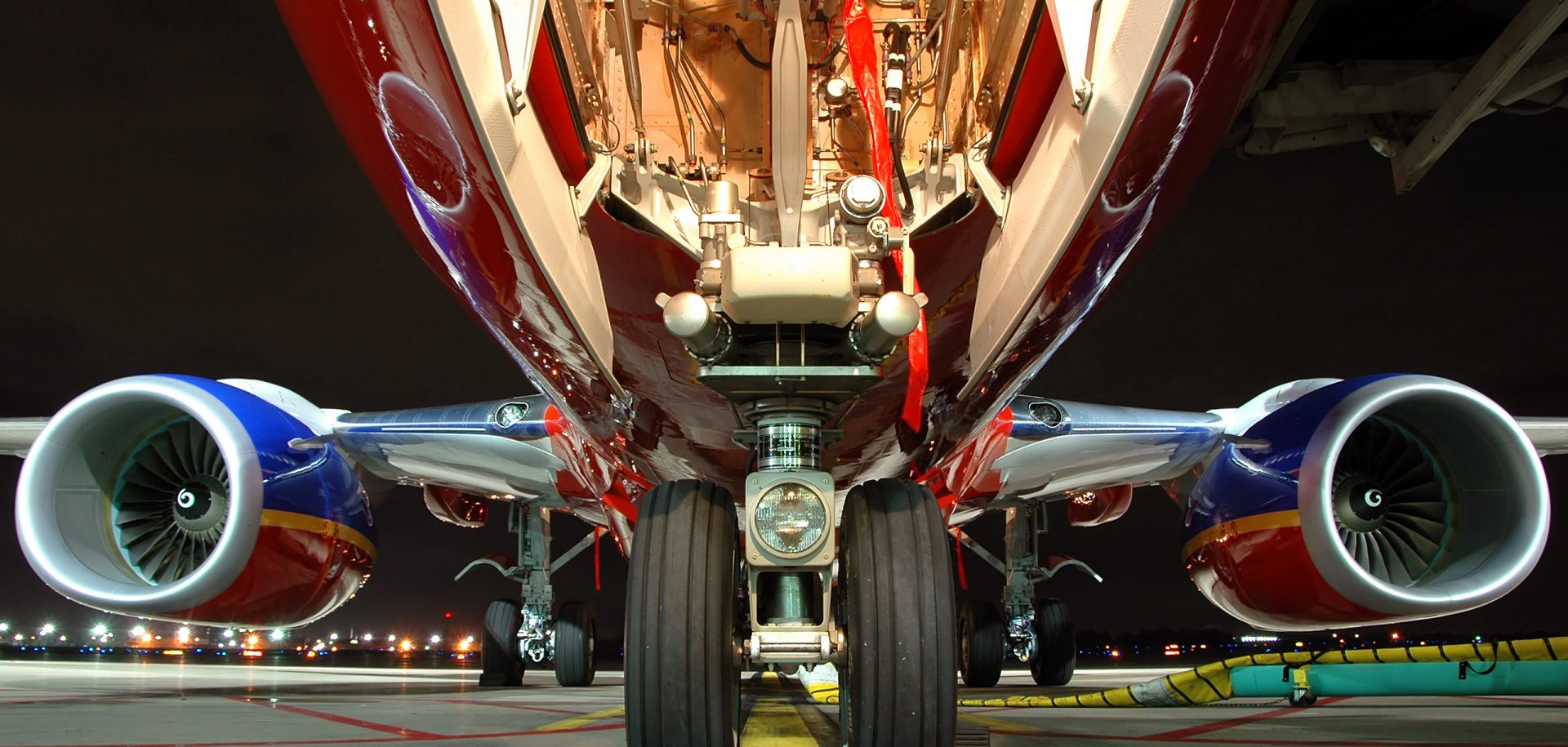
Benvenuti a bordo!
Gli ingegneri della SKF Aerospace partecipano con i loro clienti allo sviluppo delle innovazioni di oggi e di domani.
Sintesi
Dal primo volo compiuto nel 1903 dai fratelli Wright su un apparecchio a motore, l’industria aeronautica ha compiuto enormi progressi; grazie alle innovazioni tecnologiche, SKF Aerospace vi ha avuto un ruolo di primo piano e oggi continua a operare fianco a fianco con i propri clienti per affrontare le sfide del futuro.
Per l’industria aeronautica quello trascorso è stato il decennio più dinamico e innovativo della sua storia. Ordinazioni record, nuovi regolamenti governativi e ambientali, prezzi dei carburanti imprevedibili e conflitti globali ne hanno condizionato l’andamento e hanno promosso la diffusione di nuove piattaforme e nuove realizzazioni tecnologiche. I tecnici dell’SKF Aerospace di ogni parte del mondo lavorano fianco a fianco con i loro clienti per affrontare nel migliore dei modi le sfide di oggi e di domani.
La corsa alla velocità e all’affidabilità
La storia dell’aviazione copre un periodo di circa 2000 anni, dai primi tentativi di volo, con lanci giù dalle torri, fino ai voli supersonici e ipersonici effettuati con gli aviogetti. Prima che i fratelli Wright effettuassero il celebre primo volo a Kitty Hawk, famosi inventori come Leonardo, John Stringfellow e Lawrence Hargrave si erano cimentati nell’ideazione delle macchine volanti più strane. Gli esperimenti con gli alianti fornirono le basi di partenza per le macchine più pesanti dell’aria, mentre, a partire dai primi anni del XX secolo i progressi nella tecnologia dei motori e nell’aerodinamica resero possibile per la prima volta il volo controllato di velivoli dotati di motore.
Alle 10.35 del 17 Dicembre 1903, con un velivolo a motore, i fratelli Wright, con Orville ai comandi, compiono un volo della durata di 12 secondi, arrivando a 36,5 metri di altezza (fig. 1). Il moderno aeroplano con la caratteristica coda viene realizzato nel 1909 e da allora la storia dell’aviazione è costantemente legata allo sviluppo di motori sempre più potenti.
Tra gli anni quaranta e sessanta la velocità aumenta di quattro volte mentre sono già in progetto velocità ancora superiori, divenute in seguito una realtà consolidata con l’avvento del volo supersonico. Nel 1907, il record di velocità di 220 km/h viene raggiunto su una motocicletta, ma guidata da un pioniere dell’aviazione, Glenn Curtiss (fig. 2).
Ci vogliono ancora sei anni, nel 1913, per vedere all’opera un motore appositamente disegnato per l’impiego aeronautico, il motore radiale rotativo Gnome, un 14 cilindri da 117 kW (160 HP), montato sull’aereo in legno del francese Louis Béchereau, il quale in quell’anno vince il Gordon Bennett Aviation Trophy, alla velocità di 200 km/h.
Dopo la prima guerra mondiale le esigenze militari spingono la tecnologia verso maggiori velocità, mentre le prime normative industriali aeronautiche si concentrano sulla sicurezza, favorendo lo sviluppo dei viaggi di tipo commerciale.
Un’importante pietra miliare negli annali del volo e della velocità è rappresentata dall’SR-71 Blackbird della Lockheed Martin (fig. 3), che, nel 1976, supera il record mondiale di velocità e altitudine, volando a 3.529,6 km/h, ad un’altezza di 25.929 m – un record che resiste tuttora.
L’SR-71 compie varie missioni a velocità superiori a Mach 3 effettuando ricognizioni su più di 250.000 km2 di superficie ogni ora da un’altezza di 24 km. Tali condizioni operative estreme gli consentono di evitare di essere intercettato da aviogetti o missili, ma costringono i due piloti a indossare tute da astronauta per ovviare a eventuali perdite di pressione in cabina.
Uno sguardo ai motori
Tutti gli aerei prima citati erano mossi da un motore di forma più o meno artigianale, ma oggi per gli usi commerciali prevale il turbofan (fig. 5), un ulteriore sviluppo del turbogetto.
Il motore a turbogetto è costituito da un compressore (assiale, centrifugo o misto), che serve a comprimere l’aria in ingresso e a convogliarla nella camera di combustione, dove si mescola con il carburante; i gas combusti muovono la turbina e fuoriescono da un ugello. Il compressore è azionato dalla turbina stessa, che estrae l’energia dai gas che si espandono mentre l’attraversano. Il motore converte l’energia interna del combustibile in energia cinetica all’uscita, producendo una spinta. Tutta l’aria che entra passa attraverso il compressore, la camera di combustione e la turbina. Tanto maggiore è la temperatura di combustione, più grande è l’espansione dei gas.
Il turbofan ha anche una ventola (fig. 5)che fa passare un certo flusso d’aria secondario attorno al nucleo centrale oltre che attraverso quest’ultimo. Il rapporto tra questo flusso e quello primario che attraversa il nucleo centrale è noto come rapporto di diluizione o di bypass. I vantaggi del motore turbofan sono minori consumi e minore rumorosità. Alcuni turbofan recenti hanno un rapporto di bypass 12:1.
SKF Aerospace
SKF Aerospace ha più di 2.500 dipendenti ed è uno dei maggiori costruttori di cuscinetti del mercato aeronautico. La produzione SKF spazia dai cuscinetti dei motori e della cellula ai cuscinetti in elastomero, dalle soluzioni strutturali in materiale composito alle tenute e alle relative tecnologie. Con un ampio pacchetto di soluzioni innovative, aiuta l’industria aeronautica a soddisfare le varie esigenze e continua a lanciare il suo sguardo verso il futuro.
Nord America
Negli Stati Uniti SKF Aerospace inizia a operare nel 1940, con l’acquisto di uno stabilimento di cuscinetti avio a Philadelphia. Per soddisfare la crescente richiesta di tali cuscinetti SKF acquista nel 1986 la MRC di Falconer, New York, facente parte della TRW Bearings Division (fig. 6). Nell’acquisizione è incluso lo stabilimento di cuscinetti di precisione a sfere di Winsted, Connecticut. Successivamente SKF chiude lo stabilimento di Philadelphia, trasferendo parte della produzione presso altri impianti MRC. Nel 1990, acquista la Chicago Rawhide, oggi SKF Sealing Solutions, situata a Elgin, Illinois, presso la quale si producono le tenute e i prodotti per i comandi di volo dell’industria aeronautica.
Nel 2000, SKF fonda l’Aero Bearing Service Center (ABSC) di Charleston, South Carolina. ABSC è specializzata in servizi di revisione e riparazione dei cuscinetti per i motori d’aereo. Nel 2007, SKF entra in una joint venture con la General Electric Aircraft Engines per fondare una fabbrica a Ladson, South Carolina. Nel 2013, acquista la Kaydon Corporation, che costruisce prodotti per tutti i settori industriali, incluso l’aerospace. L’assortimento prodotti aerospace della Kaydon comprende tenute al carbonio e tenute circonferenziali; le prime sono principalmente impiegate per i cuscinetti dell’albero principale dei motori d’aereo. Le tenute per gli alberi delle turbine sono studiate per sigillare il compartimento dei cuscinetti dell’albero principale e la coppa dell’olio per ottenere un funzionamento ambientalmente compatibile.
Europa
SKF Aerospace Europe nasce come Clevedon, situata nel North Somerset, UK, formalmente conosciuta come AMPEP, Aerospace. L’attività viene fondata nel 1963 per essere poi acquistata dalla SARMA, una consociata SKF. Nel 2005 si ha un altro cambiamento, quando l’AMPEP diviene SKF (U.K.) Limited, Aerospace – Clevedon. Clevedon è specializzata nella progettazione e fabbricazione di cuscinetti radenti autolubrificanti con rivestimento di PTFE e fibre di vetro per applicazioni industriali e aeronautiche. Tali cuscinetti trovano vasto impiego negli elicotteri e negli aerei, principalmente per il movimento delle superfici dei controlli di volo. Nel 1966, SKF acquista lo stabilimento RIV di Villar Perosa, che oggi produce cuscinetti speciali e soluzioni per i motori d’aereo, trasmissioni e altre applicazioni high-tech. Nel 1971, SKF costruisce uno stabilimento a Lons-le-Saunier, in Francia. Nel 2005 assume il controllo del 100% dello stabilimento di Stonehouse nel Gloucestershire, UK. Stonehouse vanta 90 anni di storia come costruttore di cuscinetti e importante fornitore delle aziende aeronautiche del mondo. Nel 2006, SKF acquista la SNFA, un’azienda francese leader di cuscinetti di alta precisione. Fondata nel 1952, SNFA è situata a Valenciennes e produce cuscinetti di alta precisione per applicazioni aeronautiche, spaziali e speciali. Nel 2013, viene inaugurato a Valence, in Francia, l’Aerospace Technical Center Europe, che impiega personale tecnico altamente qualificato per lo sviluppo di prodotti avanzati e vanta impianti di prima classe utilizzati per i test sulle soluzioni aerospaziali.
Progressi negli acciai per i cuscinetti
I cuscinetti hanno un ruolo molto importante nell’industria aerospaziale per il raggiungimento di ambiziosi obiettivi tecnologici, soprattutto dal punto di vista dei materiali, delle operazioni di fucinatura, dei trattamenti termici, ecc. A questi fattori si è sempre dedicata la massima attenzione (fig. 7).
Dal momento che i motori diventano sempre più specificamente progettati per gli aerei, occorre che lo siano anche i singoli componenti. Tra gli anni ’30 e ’50 l’acciaio per cuscinetti (il vecchio 52100) ha una composizione che è ritenuta sufficiente per i bisogni del tempo, ma che, secondo le norme attuali, non lo è più. Sotto lo stimolo da parte dei governi, le norme industriali impongono requisiti minimi per i materiali più critici, per esempio tramite le First Global Aviation Standards 1944 – Chicago Convention. Dal canto suo l’aviazione militare comincia a imporre ai costruttori di motori e rotismi procedure di lavorazione e cuscinetti ben definiti, in grado di assicurare maggiore affidabilità e minori rischi. Negli anni ’60 viene realizzato l’M50, il primo acciaio appositamente sviluppato per i cuscinetti avio; con esso l’acciaio non rappresenta più il fattore limitante per le operazioni ad alta temperatura, come oggi lo è invece la lubrificazione. Con limiti di temperatura molto maggiori rispetto all’acciaio 52100 si ottengono aumenti di durata significativi. I progressi ottenuti con l’acciaio da cementazione M50NiL hanno consentito l’integrazione nei cuscinetti di elementi strutturali, mantenendo inalterate le altre elevate prestazioni. L’acciaio da cementazione, presentando maggiori sollecitazioni residue a compressione nelle superfici di contatto, conferisce maggiore resistenza alla fatica da contatto volvente. Il fatto di avere un materiale dal cuore “più dolce” ed elastico consente di ottenere accoppiamenti più stretti, indispensabili con l’aumentare delle velocità di funzionamento e per contrastare la tendenza degli anelli a dilatarsi rispetto all’albero.
Per un funzionamento affidabile le proprietà sopra descritte devono rimanere inalterate a temperature che in taluni casi possono superare i 200 °C, mentre la durezza in superficie del materiale stesso deve rimanere di almeno ~58 HRC; ricorrendo alla nitrurazione del M50/M50NiL la si può aumentare significativamente fino a ~70 HRC, a tutto vantaggio della maggiore resistenza alla contaminazione. Con la nitrurazione si aggiunge azoto alla superficie mediante un procedimento di diffusione. Dai test sulle operazioni di nitrurazione degli acciai avio appare in tutta evidenza l’importanza di una microstruttura tale che consenta di sfruttare tutti i benefici del procedimento (assenza di strati bianchi e di precipitati lungo i bordi dei grani). Dato l’elevato costo e i tempi di realizzazione, la nitrurazione è prevalentemente utilizzata sui cuscinetti di grandi dimensioni per l’albero principale del motore (diam. foro > 120 mm, fig. 10). Si prevede che verso il 2030 le condizioni di lavoro dei cuscinetti per i motori avio di prossima generazione superino le capacità operative dei materiali attualmente in uso (fig. 8).
In effetti si sta già assistendo alla comparsa di progetti di motori per alte prestazioni che prevedono combinazioni di materiali alternativi e di trattamenti superficiali atti a incrementare durate e prestazioni con l’impiego di cuscinetti ibridi (piste in acciaio e sfere di nitruro di silicio) e di acciai M50 e M50NiL nitrurati. Tra i materiali potenziali candidati studiati negli scorsi due decenni, il Pyrowear®675 (P675) appare avere tutte le caratteristiche desiderabili per i materiali di nuova generazione destinati ai cuscinetti, in particolare: capacità di mantenere una durezza di ~58 HRC a 357 °C, fusione in doppio vuoto, resistenza alla corrosione, significative sollecitazioni residue alla compressione, basso tenore di austenite residua, dimensioni fini dei grani, cementazione e grossi carburi ben bilanciati per ottenere la resistenza all’usura senza influire sulla durata RCF. Il P675 è un acciaio inossidabile martensitico da cementazione ad alta resistenza sviluppato dalla Carpenter Technology Corporation.
Un salto nel futuro
Cinquant’anni fa la rivista Aviation Week pubblica un annuncio relativo al “nuovo” Boeing 737, che aveva già ottenuto 124 ordini da 15 compagnie aeree. Esso è il capostipite della prima famiglia di aerei del mondo, progettato con intenti di standardizzazione e per operazioni a più lungo raggio rispetto ai Boeing 707 e 727. Novità per quel tempo erano le file da sei poltrone. L’aereo, il primo 737-100 fornito alla Lufthansa, compie il volo inaugurale il 9 aprile 1967. Oggi il 737 continua a battere record vantando in totale un order book di più di 13.000 aeromobili e oltre 9.000 consegne. Il 737 MAX è attualmente sottoposto a test di volo e monterà il motore LEAP della CFM International, una joint-venture fifty-fifty tra l’americana GE Aviation e la francese Snecma (fig. 9).
Il LEAP è un motore di nuova generazione progettato con l’obiettivo di migliorare i consumi e ridurre emissioni e rumorosità. Il LEAP-1A è l’opzione per l’Airbus A320neo e il LEAP-1B per il Boeing 737 MAX, mentre il LEAP-1C è l’opzione occidentale per il COMAC C919. Questi motori hanno generato ordini da parte di più di 50 clienti in tutto il mondo.
SKF ha con la CFM International una lunga storia di relazioni tecnico-commerciali e contribuisce all’intero ciclo di sviluppo del motore LEAP con le proprie conoscenze nelle tecniche di fabbricazione, con la progettazione e con l’esecuzione dei test dei cuscinetti destinati ai rotismi e all’albero principale. In particolare i cuscinetti ibridi ceramici studiati appositamente per quest’ultimo contribuiranno a rendere il motore più leggero, più silenzioso e più efficiente in termini di consumi; le emissioni di questo motore saranno inferiori del 16 % rispetto a quelle del suo predecessore CFM56.
“Partecipare a uno dei più prestigiosi programmi di sviluppo di motori è una grande opportunità per la SKF,” ha dichiarato con entusiasmo Rutger Barrdahl, direttore di SKF Aerospace. “Questo è anche il riconoscimento dell’apporto decisivo della SKF allo sforzo che compiono le industrie per ridurre le emissioni”.