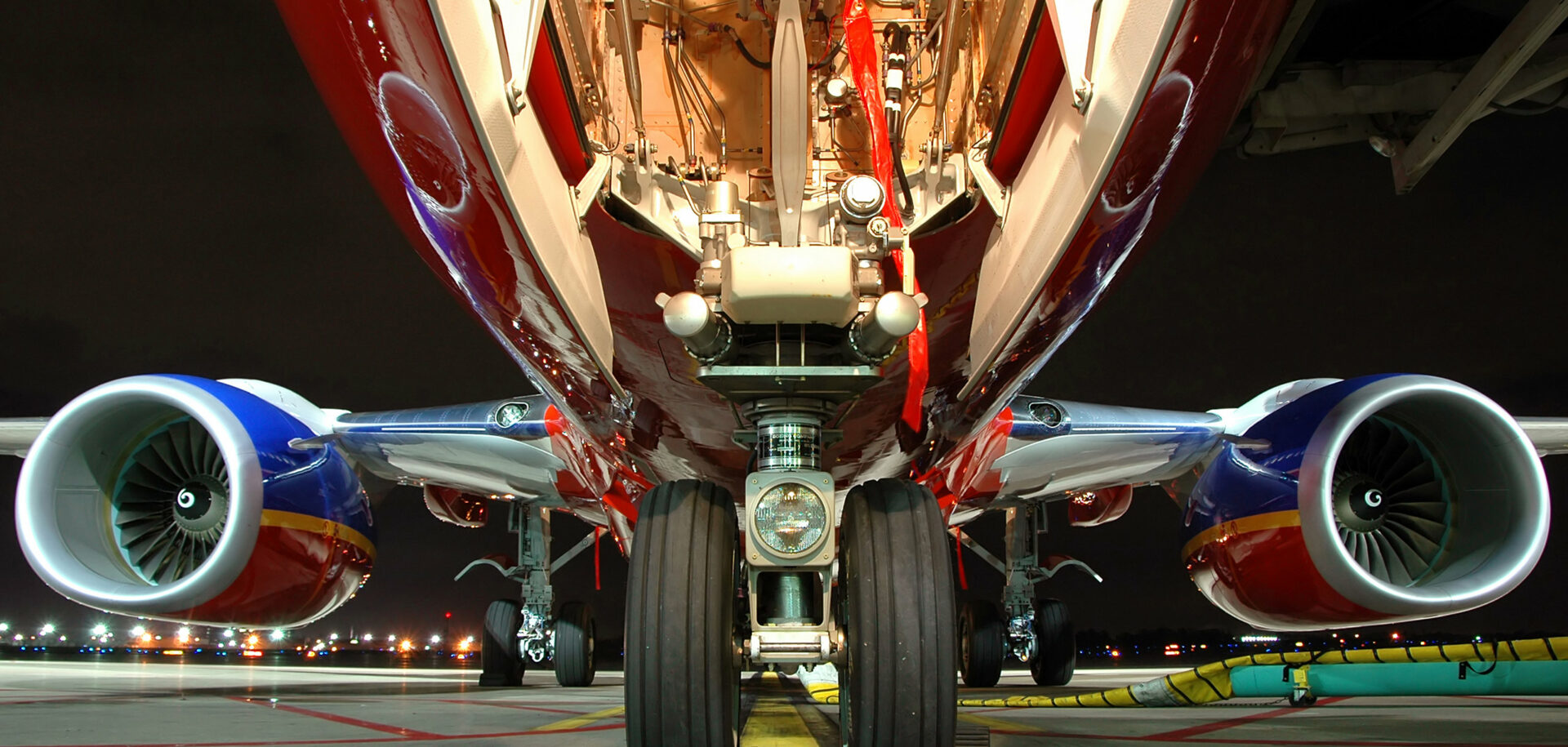
Willkommen an Bord!
Die Ingenieure von SKF Aerospace unterstützen ihre Kunden bei der Entwicklung von Innovationen.
Zusammenfassung
Nachdem die Gebrüder Wright im Jahr 1903 ihren ersten motorisierten Flug mit einer Flugmaschine „schwerer als Luft“ durchgeführt hatten, entwickelte sich die Luft- und Raumfahrtindustrie rasant. Mit innovativer Technologie war SKF Aerospace stets führend und hat zum Fortschritt in dieser Branche beigetragen. SKF Aerospace wird auch weiterhin partnerschaftlich mit den Kunden zusammenarbeiten und sich den Herausforderungen der Zukunft stellen.
Das letzte Jahrzehnt war das spannendste, dynamischste und innovativste in der Geschichte der Luft- und Raumfahrtindustrie. Auftragseingänge in Rekordhöhe bei der kommerziellen Luftfahrt, neue gesetzliche Bestimmungen und Umweltauflagen, unberechenbare Treibstoffpreise und globale Konflikte sind nur einige der Faktoren, die zu einer noch nie dagewesenen Zahl neuer Plattformen und technologischer Umsetzungen geführt haben. Die Teams von SKF Aerospace unterstützen ihre Kunden weltweit in der Entwicklung von Lösungen für die Herausforderungen von heute und morgen.
Schneller und zuverlässiger
Die Geschichte der Luftfahrt umfasst mehr als 2000 Jahre von ersten Flügen mit Drachen über Springversuche von Türmen bis hin zu Flügen mit Schall- oder Überschallgeschwindigkeit in Düsenjets. Berühmte Erfinder wie Leonardo da Vinci, John Stringfellow und Otto Lilienthal brachten ungewöhnliche Maschinen zum Fliegen. Experimente mit Gleitapparaten waren die Basis für Luftfahrzeuge, die „schwerer als Luft“ sind. Fortschritte in der Antriebstechnik und Aerodynamik ermöglichten zu Beginn des 20. Jahrhunderts erstmals gesteuerte Motorflüge.
Der erste Flug dieser Art gelang den Gebrüdern Wright (mit Orville am Steuer) am 17. Dezember 1903 um 10:35 Uhr. Er dauerte 12 Sekunden bei einer Strecke von 36,5 Metern (Bild 1). 1909 etablierte sich dann die charakteristische Heckpartie moderner Flugzeuge. Von da an war die Geschichte des Flugzeugs an die Entwicklung immer leistungsfähigerer Triebwerke gekoppelt.
Zwischen 1940 und dem Ende der 1960er-Jahre erhöhte sich die Geschwindigkeit der Flugzeuge um den Faktor vier. Entwürfe für noch schnellere Flugzeuge lagen damals schon auf dem Zeichentisch und werden bei künftigen Überschallprojekten vielleicht noch einmal eine Rolle spielen. 1907 stellte der Luftfahrtpionier Glenn Curtiss mit 220km/h einen Geschwindigkeitsrekord auf. Zum „schnellsten Mann der Welt“ wurde der frühe „Speed Junkie“ allerdings nicht im Flieger, sondern auf einem Motorrad (Bild 2).
Noch sechs Jahre später erreichte der Franzose Louis Béchereau mit seinem hölzernen Flugzeug gerade mal ein Durchschnittstempo von 200 km/h. Dabei war seine Maschine schon mit einem der ersten speziell für Flugzeuge entworfenen Motoren ausgestattet: dem Umlaufmotor „Gnome“ mit 14 Zylindern und 117 kW (160 PS). Dafür erhielt Béchereau die „Gordon Bennett“-Trophäe, die der US-Verleger ursprünglich für die flotteste Ballonfahrt ausgelobt hatte.
Nach dem Ersten Weltkrieg wurde das „Geschwindigkeitswettrennen“ weltweit durch den Druck des Militärs vorangetrieben. Gleichzeitig legten die ersten Industrienormen für die aufkeimende kommerzielle Luftfahrt den Fokus auf Sicherheit.
Dem Geschwindigkeitsrausch der Militärs leistete Hans Joachim Pabst von Ohain in den 1930er-Jahren mit der Entwicklung des Strahltriebwerks Vorschub. Einen echten Meilenstein mit dieser Technik setzte die SR-71 „Blackbird“ von Lockheed Martin (Bild 3): 1976 erreichte dieses Flugzeug 3.529,6 km/h bei einer Flughöhe von 25.929 m – beides Rekorde, die noch heute bestehen.
In derartigen Höhen flog die SR-71 regelmäßig Spionage-Einsätze mit Geschwindigkeiten über Mach 3 und konnte dabei pro Flugstunde ein Gebiet von über 250.000 km2 erfassen. Für Abfangjäger oder Raketen flog sie zu schnell und zu hoch. Die zwei Piloten der Besatzung mussten allerdings für den Fall eines Druckabfalls in der Kabine ähnliche Anzüge wie Astronauten tragen.
Blickpunkt Triebwerke
Bei jedem der vorgenannten Flugzeuge war der Antrieb von größter Bedeutung, und in der Vergangenheit gab es viele einzigartige und unterschiedliche Antriebsarten. In der heutigen Zeit ist das Turbofan-Triebwerk (Bild 5), eine Weiterentwicklung des Turbojet-Triebwerks, der gebräuchlichste Antrieb im kommerziellen Luftverkehr.
Ein Turbojet-Triebwerk besteht aus einer Gasturbine, die über einen Lufteinlass und einen Verdichter (axialer, radialer oder kombinierter Bauart) Luft verdichtet, Treibstoff mit der verdichteten Luft mischt und diese Mischung in einer Brennkammer verbrennt. Danach wird das unter hohem Druck stehende Heißgas durch eine Turbine und eine Düse geführt. Der Verdichter wird von der Turbine betrieben, die dem sich ausdehnenden Gas, das durch sie hindurchfließt, Energie entzieht. Das Triebwerk wandelt die im Treibstoff vorhandene Energie im Ausstoß in kinetische Energie um und erzeugt dabei den Schub. Die gesamte über den Einlass aufgenommene Luft wird durch den Verdichter, die Brennkammer und die Turbine geführt. Da es sich beim Turbojet-Triebwerk um eine Wärmekraftmaschine handelt, gilt: je höher die Verbrennungstemperatur, desto größer die Ausdehnung der Gase.
Ein Turbofan-Triebwerk besitzt darüber hinaus einen „Fan“ (Bild 5). Das ist ein Gebläse, das den Luftstrom aufteilt: in einen inneren, der ins Kerntriebwerk (die Gasturbine) gelangt, und einen äußeren, der außen vorbeigeführt wird. Das Verhältnis der Luftmenge, die außen vorbeiströmt, zu der Luftmenge, die durch die Gasturbine strömt, wird Nebenstromverhältnis genannt. Die Hauptvorteile von Turbofan-Triebwerken sind erhebliche Treibstoffeinsparungen und deutlich reduzierte Geräuschpegel. Einige der modernsten Turbofan-Triebwerke haben Nebenstromverhältnisse von bis zu 12:1.
SKF Aerospace
SKF Aerospace beschäftigt über 2.500 Mitarbeiter und ist weltweit einer der größten Lagerhersteller für Flugzeugtriebwerke. SKF ist führend bei Triebwerks-, Flugzeugzellen-, Elastomerlagern, Verbundlösungen, Dichtungen, Lagereinheiten und damit verbundener Technologie. Darüber hinaus unterstützt SKF die Flugzeugbauer mit innovativen Lösungen für individuelle Kundenanforderungen und trägt so zum Wandel in der Luft- und Raumfahrtindustrie bei.
Nordamerika
In den USA nahm SKF Aerospace den Betrieb im Jahr 1940 durch Übernahme einer Flugzeuglagerfabrik in Philadelphia (Pennsylvania) auf. Um die steigende Nachfrage nach Flugzeuglagern zu decken, erwarb SKF 1986 MRC, einen Teil der TRW Lagersparte, mit Sitz in Falconer (New York) (Bild 6). Zur MRC-Fabrik gehörte eine Präzisionskugellagerfertigung in Winsted (Connecticut). Später wurden Teile der Produktion in Philadelphia an die Standorte von MRC verlegt. Im Jahr 1990 integrierte SKF Chicago Rawhide in die heutige SKF Sealing Solutions (Elgin, Illinois). Dort werden Dichtungen und Motion-Control-Produkte für die Luft- und Raumfahrtindustrie gefertigt.
Im Jahr 2000 gründete SKF das „Aero Bearing Service Center“ (ABSC) in Charleston (South Carolina). ABSC ist auf die Rekonditionierung und Reparatur von Flugzeugtriebwerkslagern spezialisiert. 2007 ging SKF mit General Electric Aircraft Engines ein Joint Venture ein und richtete einen Fertigungsbetrieb in Ladson (South Carolina) ein. 2013 erwarb SKF dann die Kaydon Corporation, die Produkte für sämtliche Industriesegmente einschließlich Luft- und Raumfahrt herstellt. Das Produktportfolio von Kaydon für die Luft- und Raumfahrttechnik beinhaltet Karbondichtungen und Rundumdichtungen, wobei die Karbondichtungen insbesondere als Hauptwellenlagerdichtungen bei Triebwerken in der Luft- und Raumfahrtindustrie eingesetzt werden. Sie dichten die Hauptwellenlagerung gegen die Ölwanne ab und sorgen so für einen effizienteren und umweltverträglicheren Betrieb.
Europa
In Europa begann SKF Aerospace 1963 unter dem Namen AMPEP Aerospace in Clevedon, North Somerset (England). Über das SKF Unternehmen SARMA wurde AMPEP 2005 in SKF (U.K.) Limited, Aerospace umgewandelt. Der Standort Clevedon ist spezialisiert auf die Konstruktion und Fertigung von selbstschmierenden, mit PTFE/Glasfasern ausgekleideten Lagern für die Luft- und Raumfahrttechnik und andere industrielle Anwendungen. Diese Lager werden in großem Umfang bei Flugzeugen mit festen Tragflächen und bei Helikoptern vor allem zur Bewegung der Steuerflächen eingesetzt. Im Jahr 1966 kaufte SKF die RIV Lagerfabrik in Villar Perosa (Italien). An diesem Fertigungsstandort werden kundenspezifische Lager und Lösungen für Flugzeugtriebwerke, Antriebselemente und andere spezielle Hightech-Anwendungen hergestellt. 1971 baute SKF ein Werk in Lons-le-Saunier (Frankreich). Im Jahr 2005 übernahm SKF das Stonehouse-Werk in Gloucestershire (England) zu 100 Prozent. Als Lagerhersteller und bedeutender Zulieferer von Luft- und Raumfahrtunternehmen weltweit blickt Stonehouse auf eine 90-jährige Firmengeschichte zurück. 2006 erwarb SKF das 1952 gegründete, französische Unternehmen SNFA mit Sitz in Valenciennes. SNFA konstruiert und fertigt Hochgenauigkeitslager für die Luft- und Raumfahrttechnik und für Spezialanwendungen. 2013 wurde in Valence (Frankreich) das „Aerospace Technical Center Europe“ eröffnet. In diesem mit Prüfeinrichtungen auf Weltklasseniveau ausgestatteten Entwicklungszentrum arbeiten hochqualifizierte Techniker und Ingenieure an den Produktlösungen von morgen.
Fortschritte bei Lagerstählen
Bei der Weiterentwicklung der Luft- und Raumfahrtindustrie spielten Lager eine wichtige Rolle. Für die Triebwerkshauptwellenlager und Getriebelager waren vor allem die Entwicklungen in der Werkstofftechnik und der thermischen Verfahrenstechnologie von größter Bedeutung. Auch heute liegt der Schwerpunkt nach wie vor auf diesen Bereichen (Bild 7).
Als nicht nur Triebwerke, sondern auch Bauteile speziell für Flugzeuge entwickelt wurden, galt der damals verfügbare 52100-Stahl noch in den 1930er- bis 1950er-Jahren als beste Lösung. Angesichts der enormen Perspektiven der Luftfahrt griff jedoch so manche Regierung in die Lieferkette ein und definierte Industrienormen mit Mindestanforderungen für kritische Werkstoffe wie beispielsweise im ersten Übereinkommen über die internationale zivile Luftfahrt („Chicago Convention“) von 1944. So ebnete Militärtechnik den Weg für zwischenzeitlich auf Eis gelegte Verarbeitungspläne und Lagerkonstruktionen von Triebwerks- und Getriebeherstellern, die nun auf bessere Zuverlässigkeit und Verminderung des Risikos achteten. In den 1960er-Jahren war M50-Stahl der erste speziell für Flugzeugtriebwerkslager entwickelte Stahl. Seine Leistungsfähigkeit ließ höhere Betriebstemperaturen zu. So wurde die Schmierung zum maßgeblich begrenzenden Faktor (und ist es auch heute noch). Gegenüber dem „althergebrachten“ 52100-Stahl wurde unter anderem die Lebensdauer bei wesentlich höheren Temperaturgrenzen erheblich verbessert. Dank der Weiterentwicklung des M50NiL-Stahls war es möglich, neue Ausgestaltungsmerkmale in die Triebwerkslagerkonstruktionen aufzunehmen und dabei andere Hochleistungseigenschaften beizubehalten. Bei diesem einsatzgehärteten Stahl bilden sich höhere Druckeigenspannungen an der Kontaktfläche; daher besitzt er eine höhere Beständigkeit gegenüber der Wälzkontaktermüdung. Aufgrund der „weicheren“, elastischeren Kerneigenschaften kann der Konstrukteur festere Passungen vorsehen, die bei zunehmenden Betriebsdrehzahlen und bedingt durch die Auswirkungen des Ringwachstums im Verhältnis zur Welle erforderlich sind.
Diese Eigenschaften müssen bei Temperaturen von 200 °C und manchmal sogar mehr erhalten bleiben, wobei der Werkstoff eine Oberflächenhärte von mindestens ~58 HRC beibehalten muss, um einen zuverlässigen Betrieb sicherzustellen. Durch Nitrieren lässt sich die Oberflächenhärte von M50/M50NiL-Stahl erheblich erhöhen (bis auf ~70 HRC), was zu einer besseren Beständigkeit gegenüber Verschmutzungen führt. Beim Nitrieren wird Stickstoff mittels eines Diffusionsprozesses in die Oberfläche eingebracht, wobei ein Stickstoffprofil entsteht, das einen verbesserten Härteverlauf ergibt. Beim Nitrieren von Stählen in Luft- und Raumfahrtqualität haben umfangreiche Prüfungen gezeigt, wie wichtig die entstehende Mikrostruktur (z. B. keine weiße Schicht auf der Oberfläche und keine Ausscheidungen entlang der Korngrenzen) ist, damit alle Vorteile dieses Verfahrens genutzt werden können. Da Nitrieren zeitaufwändig und teuer ist, wird es heute vor allem bei großen Triebwerkshauptwellenlagern (Bohrung > 120 mm) (Bild 10) angewandt. Prognosen zufolge werden die Betriebsbedingungen der Flugzeugtriebwerkslager der nächsten Generation (2030+) die Leistungsfähigkeit der derzeit verwendeten Lagerstähle übersteigen (Bild 8).
Deshalb werden bei der Konstruktion der nächsten Hochleistungstriebwerke bereits alternative Werkstoffkombinationen und Oberflächenbehandlungen vorgesehen, um die derzeitige Lebensdauer und Leistungsfähigkeit der Werkstoffe zu erhöhen. Hierzu zählen beispielsweise Hybridlager (Stahllaufbahnen und Siliziumnitrid-Kugeln) und nitrierte M50-/M50NiL-Stähle. Unter den zahlreichen potenziellen Werkstoffen, die man in den letzten 20 Jahren erforschte, hat sich Pyrowear®675 (P675) als der Werkstoff herausgestellt, der alle gewünschten Eigenschaften einer Lagerstahllegierung der nächsten Generation in sich vereint. Dazu zählen: Temperaturbeständigkeit bei einer anhaltenden Härte von 58 HRC bei 357 °C, zweifache Vakuumschmelze, Korrosionsfestigkeit, höhere Druckeigenspannung, niedriger Gehalt an Restaustenit, feinkörnige Struktur der aufgekohlten Einsatzschicht und ausgewogener Anteil an großen Karbiden, damit die Verschleißfestigkeit nicht zu Lasten der Ermüdungslebensdauer geht. P675 ist ein von der Carpenter Technology Corporation entwickelter hochfester, nicht rostender martensitischer Einsatzstahl.
Mit „LEAP“ in die Zukunft
Vor 50 Jahren erschien im Magazin „ Aviation Week“ eine Anzeige mit einer Beschreibung der „neuen“ Boeing 737, für die damals schon 124 Bestellungen von 15 Luftfahrtunternehmen vorlagen. Das war der Start der weltweit ersten Düsenjet-Familie. Diese Flugzeuge besaßen eine größere Reichweite als die Boeing 707 und 727 und – das war damals neu – sechs Sitze in einer Reihe. Der erste Flug der Boeing 737 fand am 9. April 1967 statt, die erste 737-100 wurde an die Lufthansa geliefert. Auch heute bricht dieser Düsenjet noch Rekorde mit einem aktuellen Auftragsbestand von über 13.000 Flugzeugen und fast 8.800 Auslieferungen seit Markteinführung. Derzeit befindet sich die 737-MAX-Modellreihe in der Testphase; sie wird ausschließlich mit LEAP-Triebwerken von CFM ausgestattet (Bild 9). CFM International ist ein Joint Venture, das zu gleichen Teilen GE Aviation (USA) und Snecma (Frankreich) gehört.
LEAP ist eine Triebwerksserie der nächsten Generation, bei deren Konstruktion und Entwicklung der Fokus auf einem niedrigeren Treibstoffverbrauch, geringeren CO2-Emissionen und einem reduzierten Geräuschpegel lag. Mit LEAP-Triebwerksvarianten werden die Boeing 737 MAX, der Airbus A320neo und die COMAC C919 ausgestattet.
Zur LEAP-Familie gehören die bevorzugten Triebwerke für die künftigen Flugzeuge mit nur einem Mittelgang („Next Generation Single Aisle“) (Bild 9): LEAP-1A ist eine Option beim Airbus A320neo; LEAP-1B dient als ausschließlicher Antrieb der Boeing 737 MAX; LEAP-1C ist das einzige westliche Triebwerk, mit dem die COMAC C919 ausgestattet wird. Für diese Triebwerke liegen Aufträge von über 50 Kunden weltweit vor.
Seit vielen Jahren unterhält SKF eine Geschäftsbeziehung mit CFM International und hat während der gesamten Entwicklungsdauer des LEAP-Programms Wissen in die Fertigung, Konstruktion und Prüfung der Hauptwellen- und Hilfsgetriebelager einfließen lassen. Aufgrund der speziell für das LEAP-Programm entwickelten keramischen Hybridhauptwellenlager wird das neue Triebwerk nicht nur leichter, leiser und treibstoffeffizienter sein, sondern auch 16 Prozent weniger CO2 ausstoßen als die Vorgängerserie CFM56.
Dazu Rutger Barrdahl, Chef von SKF Aerospace: „Für SKF ist die Mitarbeit an diesem prestigeträchtigen Entwicklungsprogramm eine großartige Chance, um zu beweisen, dass wir wirksam zur Reduktion von CO2-Emissionen beitragen können“.