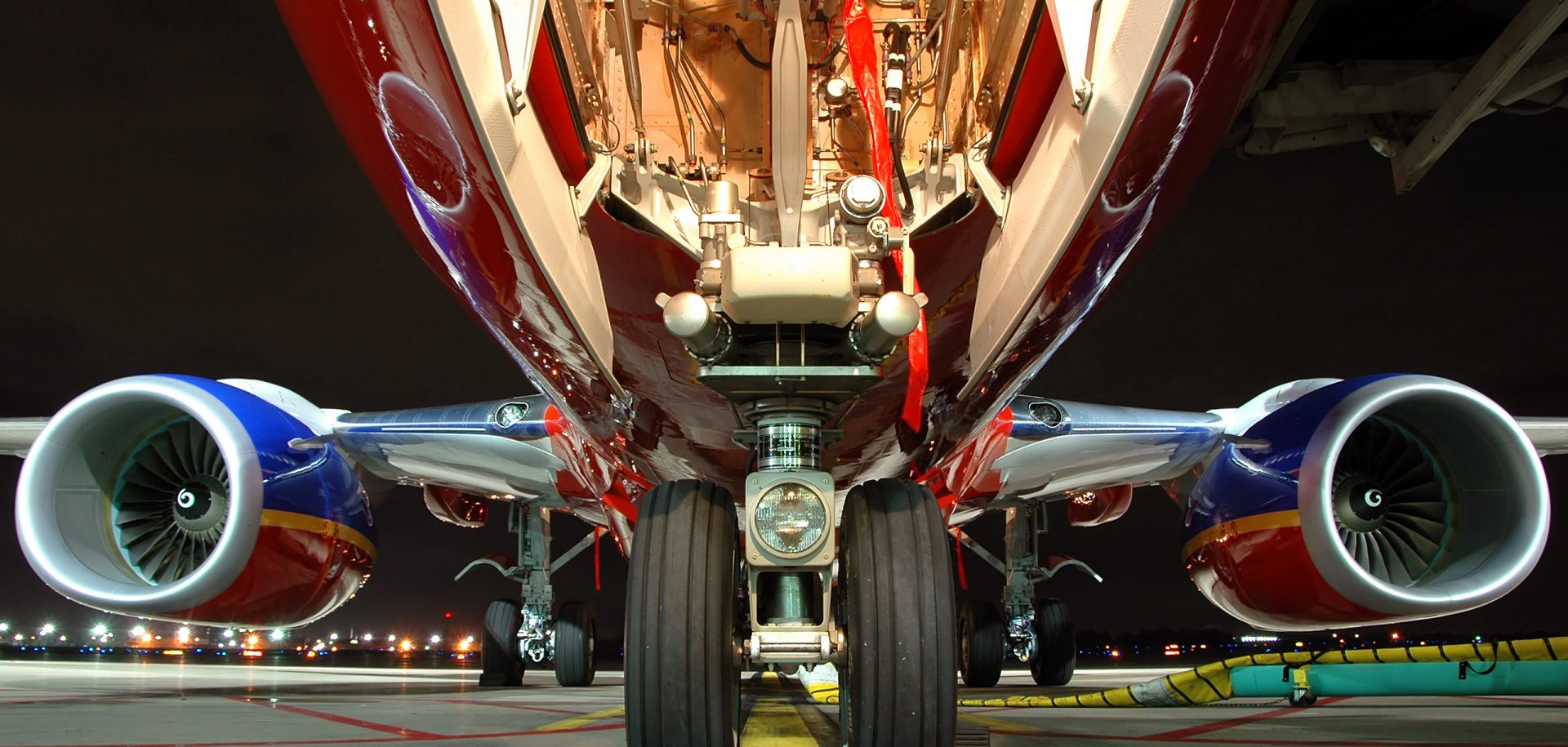
Bienvenue à bord !
Les ingénieurs de SKF Aerospace travaillent aux côtés des clients de SKF pour mettre au point les innovations d’aujourd’hui et de demain.
Résumé
Depuis le premier vol d’un appareil aérodyne motorisé piloté par les frères Wright en 1903, l’industrie aéronautique n’a eu de cesse d’évoluer au fil des décennies, une innovation chassant l’autre. Leader depuis toujours des technologies innovantes qui font progresser l’industrie aéronautique, SKF Aerospace continue aujourd’hui de travailler main dans la main avec ses clients pour leur permettre de relever les défis de demain.
L’histoire de l’aviation s’étend sur plus de 2 000 ans, des premiers cerfs-volants, ébauches d’avions et tentatives de sauts depuis un promontoire, jusqu’au vol super- et hypersonique d’un aérodyne motorisé. Des inventeurs célèbres, tels Léonard de Vinci, John Stringfellow et Lawrence Hargrave, ont rivalisé d’idées pour faire voler les engins les plus étranges, bien avant le premier vol historique des frères Wright, à Kitty Hawk. Des expériences avec des planeurs avaient ouvert la voie au développement d’avions aérodynes et, au début du 20ème siècle, des progrès dans le domaine des moteurs et de l’aérodynamisme ont conduit au premier vol contrôlé et motorisé.
Ce vol a été réalisé le 17 décembre 1903, à 10h35, par Orville, l’un des deux frères Wright. Il a duré 12 secondes pour une distance parcourue de 36,5 mètres (Fig. 1). L’avion moderne avec sa queue caractéristique date de 1909 : à partir de là, l’histoire de l’aéronautique est étroitement liée au développement de moteurs toujours plus puissants.
Entre les années 1940 et 1960, les vitesses de vol ont été multipliées par quatre, et des concepts encore plus rapides étaient déjà dans les tuyaux ; concepts devenus aujourd’hui réalité avec le possible retour du vol supersonique. En 1907, le record du monde de vitesse (220 km/h) a été établi par le pionnier Glenn Curtiss, non pas à bord d’un avion mais sur une moto (Fig. 2).
Six ans plus tard, en 1913, l’un des tout premiers moteurs spécialement conçus pour l’aviation, le moteur rotatif Gnome, 14 cylindres et 160 ch (117 kW), installé sur l’avion en bois du Français Louis Béchereau a permis à ce dernier de remporter le trophée de l’aviation Gordon Bennett avec une vitesse moyenne de 200 km.
Après la Première Guerre mondiale, sous l’impulsion technologique donnée par l’industrie militaire, a démarré la course à la vitesse. Dans le même temps, les premières normes du secteur aéronautique ont commencé à s’intéresser à la sécurité, un élément essentiel pour l’évolution des vols commerciaux.
Le SR-71 Blackbird de l’entreprise Lockheed Martin (Fig. 3) a marqué les annales de l’aviation en termes de vitesse. En 1976, il a battu le record du monde de vitesse anémométrique et d’altitude en atteignant les 3 529,6 km/h à une altitude de 25 929 m, un record toujours inégalé à ce jour.
Le SR-71 a effectué régulièrement des missions de vol, à des vitesses au-delà de Mach 3, dans le cadre desquelles il pouvait surveiller plus de 250 000 km2 de surface terrestre par heure depuis une hauteur de 24 km. Ces vitesse et altitude vertigineuses lui permettaient d’éviter les chasseurs d’interception ou les missiles, mais contraignaient les deux personnes à bord à porter une combinaison semblable à celle des astronautes en prévention d’une dépressurisation de la cabine.
Gros plan sur les moteurs
Derrière chacun des avions mentionnés précédemment se trouve un groupe moteur. Une foule de méthodes uniques et variées ont été mises en œuvre par le passé pour la propulsion des avions, mais le turboréacteur « double flux » (Fig. 5), perfectionnement du turboréacteur, est aujourd’hui le type de moteur le plus courant pour les vols commerciaux.
Un turboréacteur est une turbine à gaz dont le fonctionnement repose sur les étapes suivantes : l’air admis est comprimé par un compresseur (axial, centrifuge ou mixte), puis mélangé à du carburant ; ce mélange est ensuite brûlé dans une chambre de combustion, et l’air chaud sous haute pression traverse une turbine avant d’être éjecté au niveau de la tuyère. Le compresseur est alors entraîné par cette turbine qui puise l’énergie dans l’expansion des gaz chauds qui la traversent. Le moteur convertit l’énergie provenant de la combustion en énergie cinétique au niveau de l’échappement pour produire la poussée. Selon le type de moteur, tout ou une partie de l’air admis à l’entrée traverse le compresseur, la chambre de combustion et la turbine. Le turboréacteur étant un moteur thermique, plus la température de combustion est élevée, plus l’expansion des gaz est importante.
Un turboréacteur « double flux » est un turboréacteur équipé d’une soufflante (Fig. 5). Celle-ci envoie autour du compresseur une partie de l’air qui lui est destiné. Le taux de dilution est le rapport entre la proportion d’air contournant le compresseur et celle qui y pénètre. Certains des derniers modèles de turboréacteur « double flux » peuvent annoncer des taux de dilution de 12:1. Parmi les avantages de ce type de turboréacteur : l’atténuation des nuisances sonores et la réduction de la consommation de carburant.
SKF Aerospace
SKF Aerospace regroupe plus de 2 500 collaborateurs et figure parmi les principaux fabricants mondiaux de roulements pour moteurs aéronautiques. L’entreprise est leader en matière de roulements pour moteurs, transmissions de puissance, structure et commandes de vol (palier et rotules métalliques et élastomériques), solutions composites structurales, joints et technologies associées. SKF contribue à faire évoluer l’industrie aéronautique en permettant aux constructeurs de ce secteur de répondre aux besoins variés de leurs clients grâce à un vaste panel de solutions innovantes. Cette innovation est le moteur de SKF.
Amérique du Nord
Aux États-Unis, SKF Aerospace a démarré ses activités en 1940 suite au rachat par SKF d’une usine de roulements pour l’aéronautique à Philadelphie, en Pennsylvanie. Pour faire face à la demande croissante en roulements de moteurs d’avions, SKF a également acheté, en 1986, MRC, une filiale de TRW Bearings Division basée à Falconer, dans l’État de New York (Fig. 6). Le rachat de MRC incluait également une usine de roulements à billes de précision à Winsted, dans le Connecticut. SKF a alors fermé l’usine de roulements aéronautiques de Philadelphie dont la production a été transférée en partie vers les sites MRC. En 1990, SKF a fait l’acquisition de Chicago Rawhide, devenu aujourd’hui SKF Sealing Solutions, à Elgin, dans l’Illinois. Les solutions d’étanchéité et produits de contrôle des mouvements pour l’aéronautique sont actuellement fabriqués sur ce site.
En 2000, SKF a créé Aero Bearing Service Center (ABSC) à Charleston, en Caroline du Sud. ABSC est spécialisé dans les services de révision et réparation de roulements de moteurs d’avions. En 2007, SKF a constitué une joint-venture avec General Electric Aircraft Engines pour ouvrir une usine de production à Ladson, en Caroline du Sud. En 2013, SKF a racheté Kaydon Corporation, qui fabrique des produits pour tous les segments, dont l’aéronautique. Le portefeuille de produits aéronautiques de Kaydon inclut des joints en carbone et des joints circonférentiels ; les modèles en carbone sont utilisés principalement comme solutions d’étanchéité des roulements d’arbre principal et dans des applications de moteurs d’avions. Les joints SKF Aerospace pour arbres de turboréacteurs sont conçus pour assurer l’étanchéité des compartiments roulements de l’arbre principal et du carter d’huile pour un fonctionnement plus efficace et plus respectueux de l’environnement.
Europe
SKF Aerospace Europe est né avec Clevedon, basé dans le North Somerset, en Angleterre. L’entreprise était à l’époque connue sous le nom de AMPEP, Aerospace. Elle a été créée en 1963 et rachetée par SARMA, une entreprise de SKF. En 2005, nouveau changement, AMPEP est devenu SKF (U.K.). Limited, Aerospace – Clevedon. Clevedon est spécialisé dans la conception et la fabrication de bagues ou de rotules autolubrifiantes en PTFE renforcé de fibres de verre pour des applications aussi bien dans le secteur aéronautique que dans l’industrie générale. Ces bagues ou rotules sont couramment utilisées sur les aéronefs à voilure fixe et les hélicoptères, principalement dans les systèmes de commandes de vol. En 1966, SKF a acheté l’usine de roulements RIV à Villar Perosa, en Italie. Cette usine fabrique des roulements techniques sur mesure et des solutions pour moteurs d’avions, équipements de transmission et autres applications spécifiques de haute technologie. En 1971, SKF a construit une usine à Lons-le-Saunier, en France. Depuis 2005, SKF détient 100 % de l’usine de Stonehouse dans le Gloucestershire, en Angleterre. Ce fabricant de roulements, installé depuis 90 ans, dessert des entreprises aéronautiques du monde entier. En 2006, SKF a racheté SNFA, une société française qui figure parmi les principaux fabricants de roulements de précision. Fondée en 1952, l’entreprise SNFA est basée à Valenciennes. Elle conçoit et fabrique des roulements de précision pour l’aéronautique, l’aérospatiale et des applications spécifiques. En 2013, le Centre technique aéronautique européen a ouvert ses portes à Valence, en France. Ce centre, qui emploie un personnel d’ingénierie hautement qualifié, se consacre au développement de produits de pointe. Il est, pour ce faire, équipé d’installations d’essai de classe mondiale spécialement conçues pour tester les solutions aéronautiques.
Évolution des aciers pour roulements aéronautiques
L’industrie aéronautique n’a eu de cesse de repousser les limites de nombreuses technologies et les roulements ont joué un rôle clé à cet égard. Les évolutions majeures relatives aux roulements d’arbres principaux et de boîtes d’engrenages ont porté sur les matériaux (forgeage, traitement thermique, etc.). Les matériaux et traitements thermiques ont constitué et demeurent encore aujourd’hui le principal domaine d’intérêt (Fig. 7).
Comme pour les moteurs, la conception des pièces s’est progressivement spécialisée pour l’aéronautique. Des années 1930 aux années 1950, l’acier pour roulements de faible propreté (52100) – du fait de sa composition médiocre au regard des normes actuelles mais qui offrait toutefois une fiabilité acceptable – a fait figure de solution haut de gamme. Sous l’effet du rôle de plus en plus actif des États dans les chaînes d’approvisionnement, des normes industrielles ont été établies pour définir les exigences minimales relatives aux matériaux critiques, notamment lors de la Convention de Chicago de 1944 qui a instauré les premières normes mondiales de l’aviation. L’aviation militaire a alors ouvert la voie aux processus de fabrication figés et à la conception de roulements, tous deux contrôlés par les fabricants de moteurs et de boîtes d’engrenages, dans une perspective d’amélioration de la fiabilité et de réduction des risques. Dans les années 1960, l’acier M50 a été le premier acier spécialement mis au point pour les roulements de moteurs d’avions. Avec l’acier M50, la capacité de l’acier ne constituait plus le facteur limitant pour un fonctionnement à haute température. La lubrification est alors devenue le nouveau facteur limitant et le reste encore aujourd’hui. La hausse des limites supérieures de température s’est traduite par une augmentation significative de la durée de vie par rapport au précédent acier 52100. L’acier carburé et cémenté M50NiL a permis d’intégrer de nouvelles caractéristiques structurelles à la conception des roulements de moteurs d’avions, tout en conservant les autres caractéristiques de haute performance. Du fait de contraintes de compression résiduelles supérieures au niveau de la surface de contact, l’acier carburé et cémenté offre une résistance accrue à la fatigue de contact roulant. Le cœur plus élastique, plus « tendre », permet au concepteur d’utiliser des ajustements plus serrés, ce qui est nécessaire en présence de vitesses de fonctionnement supérieures et des effets de la dilatation de la bague par rapport à l’arbre.
Ces propriétés doivent rester stables à des températures atteignant parfois, voire dépassant dans certains cas, les 200 °C. Malgré ces températures, le matériau doit conserver une dureté en surface d’au moins ~58HRC pour garantir un fonctionnement fiable. La nitruration de l’acier M50/M50NiL peut accroître de manière significative la dureté de la surface (jusqu’à ~70 HRC), devenant ainsi le principal facteur d’amélioration de la résistance à la contamination. La nitruration permet d’obtenir un durcissement superficiel, et donc une modification du profil de dureté, par diffusion d’azote. Concernant la nitruration des aciers de qualité aéronautique, des essais intensifs ont montré l’importance de la microstructure obtenue (absence de couche blanche superficielle et de précipités le long des limites de grain) pour tirer pleinement profit des avantages de ce procédé. Coûteuse et chronophage, la nitruration est principalement réservée aux roulements de moteur d’arbre principal de grandes dimensions (alésage >120 mm) (Fig. 10). Les conditions de service des roulements de moteurs d’avions de prochaine génération (horizon 2030) devraient dépasser la capacité des matériaux pour roulements utilisés actuellement (Fig. 8).
Aujourd’hui, cette évolution annoncée se traduit déjà par l’émergence de modèles de moteurs haute performance mettant en œuvre des combinaisons de matériaux alternatives et des traitements de surface destinés à améliorer la durée de vie et les performances des matériaux actuels. On peut citer, par exemple, les roulements hybrides (pistes en acier et billes en nitrure de silicium) et les aciers nitrurés M50 et M50-NiL. Parmi les nombreux matériaux candidats potentiels étudiés ces deux dernières décennies, le Pyrowear®675 (P675) se démarque en offrant toutes les propriétés attendues d’un alliage pour roulements de prochaine génération : maintien d’une dureté de ~58 HRC à 357 °C, double fusion sous vide, résistance à la corrosion, contraintes résiduelles de compression, faible austénite résiduelle, cémentation carburée à grains fins et carbures de grande taille équilibrées conférant une bonne résistance à l’usure sans altérer la résistance à la fatigue de contact roulant. Le P675 est un acier inoxydable, martensitique de cémentation à forte capacité, mis au point par Carpenter Technology Corporation.
Le saut vers le futur
Il y a 50 ans, le magazine Aviation Week présentait le « nouveau » Boeing 737 qui faisait déjà l’objet de 124 commandes de la part de 15 compagnies aériennes. La première famille d’avions à réaction au monde était née. Cet avion a été conçu sur la base des Boeing 707 et 727 avec, toutefois, une distance franchissable supérieure et des rangées de six sièges de front, une nouveauté à l’époque. L’avion a effectué son premier vol le 9 avril 1967 suite à la première livraison du 737-100 à la compagnie allemande Lufthansa. Aujourd’hui, le 737 reste l’avion le plus vendu au monde, cumulant plus de 13 000 commandes et plus de 9 000 livraisons depuis ses débuts. Le 737 MAX est actuellement en phase de test. Il est équipé exclusivement du moteur LEAP de CFM (Fig. 9). CFM International est une co-entreprise détenue à parts égales par l’américain GE Aviation et le français Snecma.
Le moteur LEAP est un moteur de nouvelle génération qui a été conçu et développé en mettant l’accent sur l’amélioration du rendement énergétique et sur la réduction des émissions et du niveau sonore. Différentes versions équiperont les avions Boeing 737 MAX, Airbus A320neo et COMAC C919.
La gamme CFM LEAP est constituée de moteurs pour l’avion monocouloir de prochaine génération (Fig. 9). Le LEAP-1A fait partie des moteurs disponibles pour l’Airbus A320neo ; le LEAP-1B équipe en exclusivité le Boeing 737 MAX ; et le LEAP-1C est l’unique système propulsif occidental pour le COMAC C919.
SKF, partenaire de longue date de CFM International, a apporté, tout au long du développement du moteur LEAP, ses connaissances en matière de technologies de fabrication, de conception et d’essais des roulements d’arbres principaux et de boîtes d’accessoires. Grâce aux roulements hybrides céramiques pour arbre principal, spécialement mis au point pour le programme du moteur LEAP, celui-ci sera plus léger, plus silencieux et plus économe en énergie, avec des émissions de CO2 inférieures de 16 % à celles de son prédécesseur, le CFM56.
« La participation à l’un des programmes de développement de moteurs les plus prestigieux du secteur est une formidable opportunité pour SKF, a commenté Rutger Barrdhal, Directeur de SKF Aerospace. C’est également une reconnaissance de la contribution apportée par l’approche collaborative du développement technologique défendue par SKF aux efforts du secteur pour réduire les émissions. »