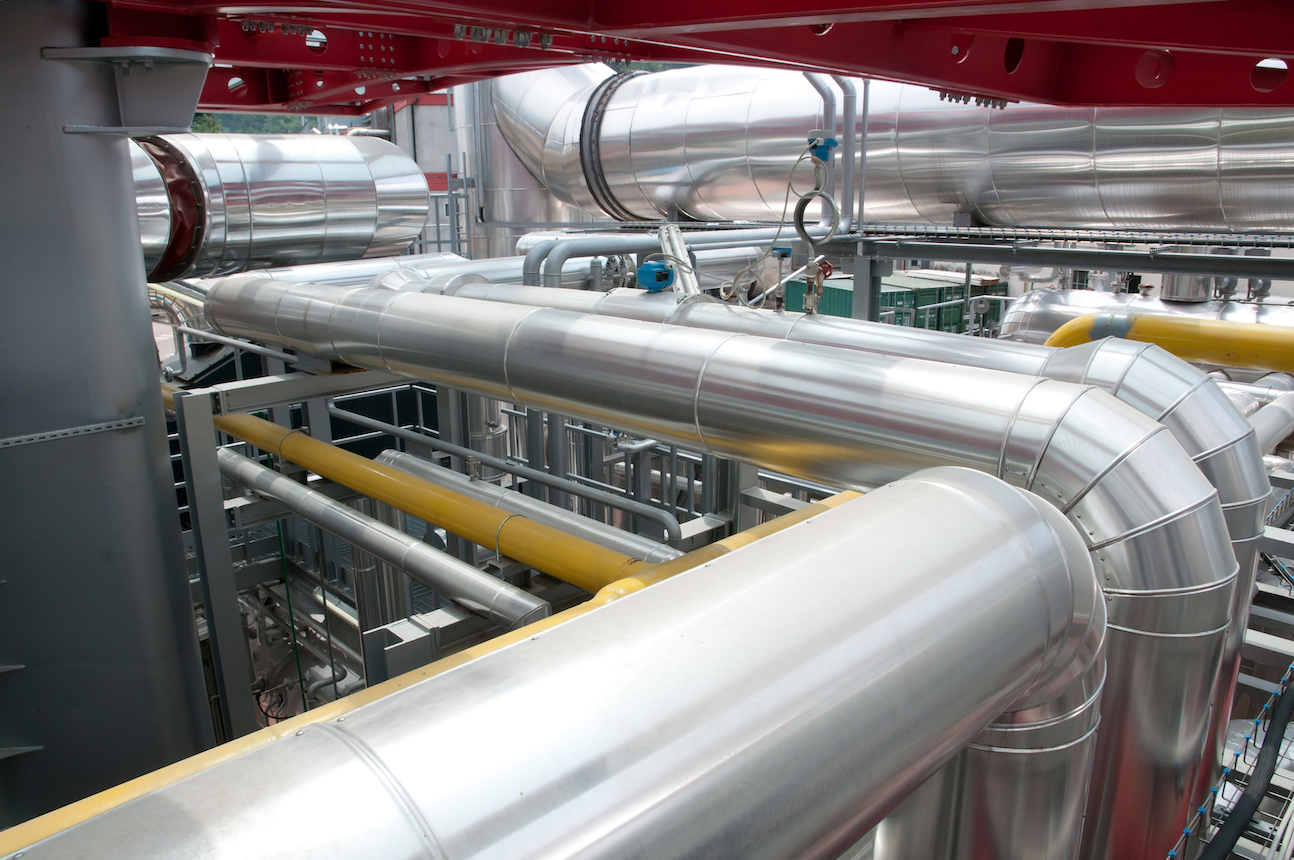
Pesos pesados
En la planta siderúrgica de SSAB en Luleå, Suecia, se cuida mucho el mantenimiento de las 15 grúas-puente que transportan y vuelcan las cubas de acero fundido al pasar de una fase de la producción de acero a otra. Sin las grúas, la producción se paralizaría.
En la planta siderúrgica de SSAB en Luleå, Suecia, se cuida mucho el mantenimiento de las 15 grúas-puente que transportan y vuelcan las cubas de acero fundido al pasar de una fase de la producción de acero a otra. Sin las grúas, la producción se paralizaría.
Industria
Fabricar acero no se trata solamente de procesos metalúrgicos y aleaciones. Es fundamental mantener en buen estado de funcionamiento equipos como las enormes grúas de la planta.
«El mantenimiento es barato; los paros son caros», dice Jan-Ola Wanhainen, responsable de las grúas de la planta siderúrgica de SSAB en Luleå. Su misión es que las grúas funcionen todo el tiempo.
No son grúas corrientes. Como un alto horno o una máquina de colada continua, estas enormes grúas-puente forman parte de la infraestructura necesaria para el funcionamiento correcto de la planta.
«En una planta siderúrgica, cada equipo es importante», dice Wanhainen. «El miembro más débil del equipo determina nuestra fuerza.».
En SSAB Tunnplåt (chapas de acero) en Luleå, el proceso siderúrgico empieza con el horneado de carbón importado en la planta de coque, un proceso que produce mucho gas, que se recicla para calentar la planta siderúrgica y la mitad de la ciudad de Luleå, de 45.000 habitantes.
El coque se utiliza como combustible, combinado con oxígeno, en el alto horno donde se funde el mineral de hierro que llega cada día a Luleå por ferrocarril, desde LKAB en Malmberget, a unos 200 kilómetros de distancia.
A continuación, el metal fundido se traslada a la acería en lotes de 300 toneladas y se transporta una distancia corta por ferrocarril en una vagoneta de forma alargada llamada «torpedo». En una cuba del tamaño de una casa, el metal fundido se inyecta con carburo u óxido de magnesio para eliminar el azufre.
En otra cuba, se sopla oxígeno a presión para eliminar el carbono del hierro líquido. El hierro se convierte en acero cuando el contenido de carbono es inferior al 1,7 por ciento.
A continuación, se realizan pequeños ajustes de la temperatura y composición del acero antes de transportarlo a una máquina de colada continua donde el metal fundido se solidifica en tochos de 11 metros de largo y 25 toneladas de peso. Cada día se fabrican 300 tochos en Luleå, equivalente a una producción anual de 2,7 millones de toneladas.
Luego los tochos se transportan por ferrocarril al molino laminador de SSAB en Borlänge, donde se conforman en distintos grosores y se pueden templar, endurecer, revenir y someter a otros tratamientos, en función de las preferencias del cliente.
Las naves, tan grandes como hangares, con sus gigantescos hornos, enormes grúas y cubas de metal fundido dan un ambiente de película de ciencia-ficción a la planta de Luleå. Pero las apariencias engañan. Detrás de la suciedad, el ruido y el humo, hay una infraestructura informática muy sofisticada que controla todos los parámetros de la producción de acero.
Por ejemplo, el operador de grúa Stefan Näslund maneja a distancia las cubas de 100 toneladas llenas de acero fundido. En una sala de mando, mediante pantallas de ordenador, controla las imágenes recibidas desde 300 cámaras maniobrables instaladas en puntos estratégicos de la planta para darle la visión más completa posible de lo que está pasando en las naves.
«Hasta hace un par de años, yo trabajaba sentado en la grúa, cerca del techo, y guiaba las cubas hablando por walkie-talkie con otra persona en el suelo», dice.
Algunos de los puentes-grúa de la planta de SSAB en Luleå se pueden guiar por control remoto, de modo parecido a los mandos usados por los aficionados al aeromodelismo.
Incluso la locomotora que lleva las vagonetas del alto horno a la acería es controlada a distancia.
A finales de 2009, SSAB Tunnplåt en Luleå se convirtió en la primera planta siderúrgica del mundo en instalar equipos de SKF de monitorización de estado en línea en los motores y transmisiones de sus grúas nuevas (ver recuadro).
A Wanhainen le gusta mostrar a los visitantes una grúa de los años 40 que todavía se encuentra en la planta, guardada en un rincón. Para hacer funcionar la grúa, dos hombres tenían que tirar de cadenas mediante un sistema de poleas, y los pesos que podía levantar la grúa eran una fracción de los volúmenes de acero suspendidos hoy.
«Hemos avanzado mucho desde entonces», dice Wanhainen.
Primera aplicación en grúas
SSAB Tunnplåt en Luleå, Suecia, es el primer gran grupo industrial del mundo en instalar los sistemas de monitorización de estado en línea de SKF en los motores y transmisiones de cinco grúas-puente compradas recientemente por la empresa.
SSAB utiliza el Sistema en línea SKF Multilog IMx-S para obtener información en tiempo real sobre el estado de los rodamientos en ambos lados de los motores y transmisiones a través de sensores para monitorizar continuamente la fiabilidad de las máquinas cuando las grúas están funcionando. Los datos son monitorizados por SKF.
«Un paro no previsto en una planta siderúrgica es catastrófico, por los volúmenes que se producen», dice Jan-Ola Wanhainen, responsable de todas las grúas de la planta de Luleå. «Por eso necesitamos disponer de la máxima cantidad posible de información antes de realizar un paro programado de mantenimiento de una grúa. La monitorización de estado en línea nos muestra cuándo y dónde se producen los fallos».