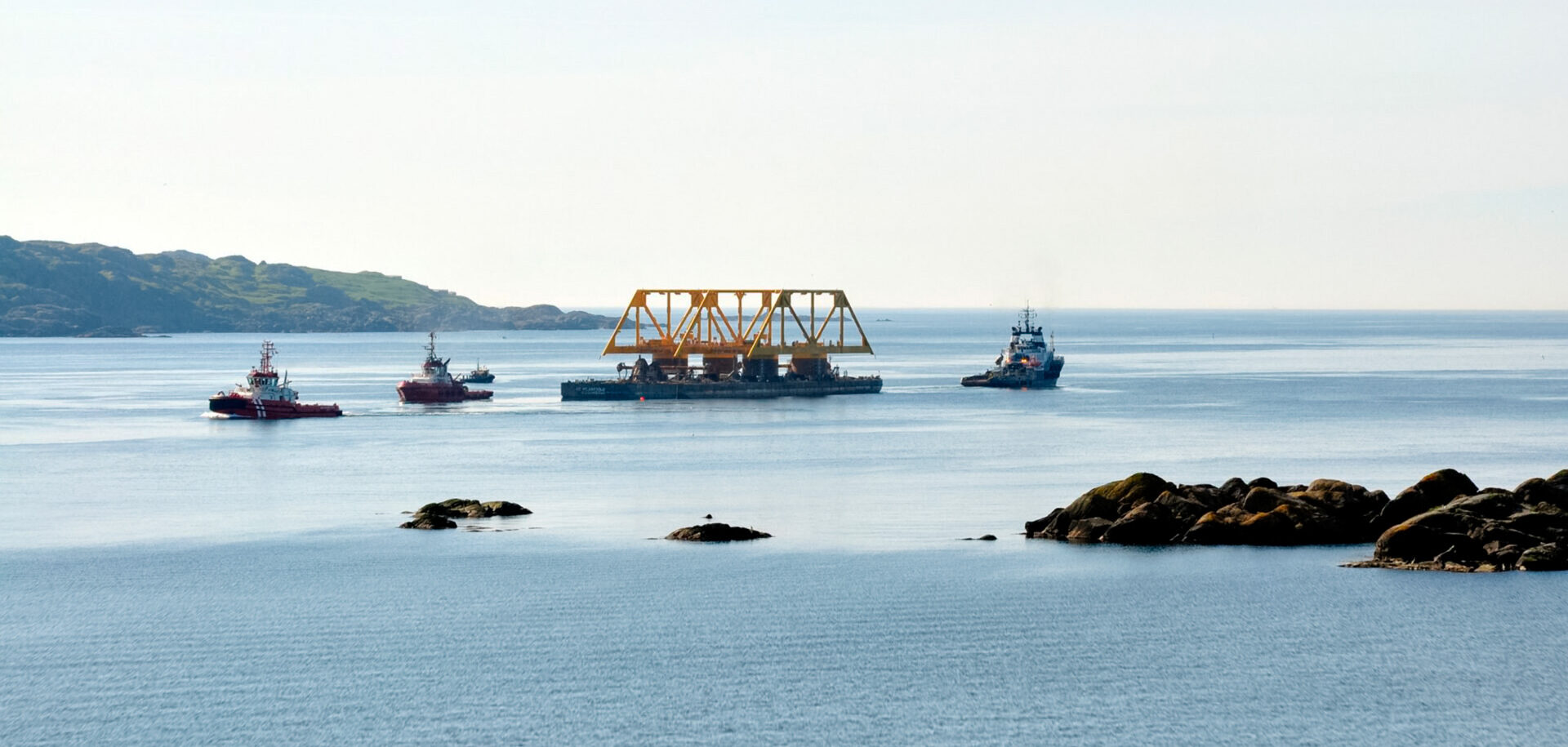
Rodamientos magnéticos, a toda prueba
Hacer funcionar turbomanorreductores, motores eléctricos de alta velocidad y compresores en entornos hostiles plantea múltiples desafíos. Puede ser difícil desarrollar estos equipos para que funcionen de forma confiable bajo el agua, en el desierto o a temperaturas extremas con diseños tradicionales. En cambio, con una tecnología sólida y probada, los rodamientos magnéticos son capaces de resistir condiciones adversas. Y a pesar de ello, su uso es menos extendido. Sus prestaciones han sido puestas a prueba en una de las aplicaciones más exigentes del mundo, el yacimiento de gas submarino de Åsgard, situado en el Mar de Noruega, donde funcionan sin problemas desde hace más de 5 años y acumulan 90 000 horas de uso.
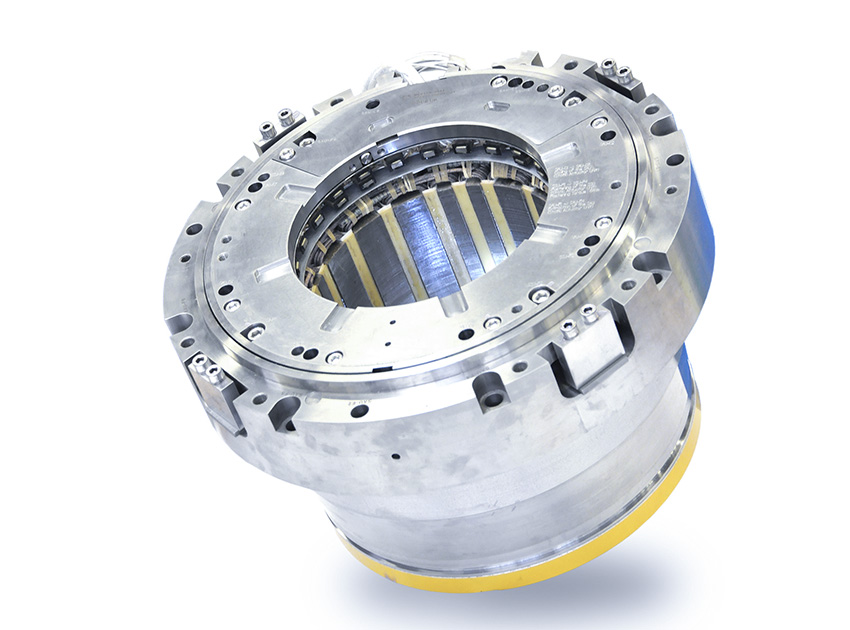
Con estas características, los rodamientos magnéticos están especialmente indicados para aplicaciones en entornos hostiles del sector energético, del petróleo y el gas. Muchos trabajan en los entornos más duros del mundo, desde los desiertos de Arabia Saudita hasta las plataformas del Mar del Norte y los yacimientos siberianos por encima del Círculo Polar Ártico.
“Nuestros rodamientos magnéticos están instalados en más de 750 turbomanorreductores, 200 compresores autónomos y 150 compresores herméticos en todo el mundo”, afirma Alexandre Kral, responsable de desarrollo de negocios de SKF en petróleo y gas. “También se pueden encontrar en turbinas de gas, grupos electrógenos y bombas, y mucho más”.
La única solución realmente viable
En el caso de los compresores herméticos, los rodamientos magnéticos son la única solución realmente viable porque no requieren sellos de gas seco. “Los rodamientos magnéticos crean un campo magnético de modo que no haya contacto entre las piezas y se elimine el desgaste mecánico”, explica Kral.
La ausencia de desgaste mecánico prácticamente elimina las paradas no planificadas. En aplicaciones tanto terrestres como marinas, solo el controlador de los rodamientos magnéticos necesita un mantenimiento que, al constituirse en gran parte de componentes electrónicos, ventiladores y filtros, es mucho menor. Por otra parte, el controlador es más compacto que el sistema estándar de lubricación con aceite. Esta es una cualidad muy valorada sobre todo en lugares con poco espacio como plataformas, unidades flotantes para la producción, almacenamiento y descarga (FPSO) o en zonas remotas.

Reducción sustancial del consumo energético
Además, los rodamientos magnéticos son más limpios que los de aceite. El resultado es una reducción sustancial del consumo energético, ya que los rodamientos magnéticos eliminan la necesidad de un sistema complejo de lubricación con aceite, que incluye los tubos al depósito de aceite, los filtros y el sistema de refrigeración. “El consumo energético de los rodamientos magnéticos es una décima parte del de los rodamientos de aceite”, explica Kral. “Además, al tener menos componentes, se generan menos datos para monitorear. Y con menos componentes, cabe en menos espacio”.
El consumo energético de los rodamientos magnéticos es una décima parte del de los rodamientos de aceiteAlexandre Kral, responsable de desarrollo de negocios de SKF en petróleo y gas
Sin embargo, a pesar de todas estas ventajas, muchos clientes dudan a la hora de dar el paso de cambiar a los rodamientos magnéticos. Una de las razones es su mayor costo de adquisición.
“Algunos piensan que los rodamientos magnéticos son más costosos, y es cierto que las piezas mecánicas, el armario y tal vez el diseño de la máquina cuestan un poco más”, explica Kral. “Pero esta diferencia de costos se anula fácilmente con la simplificación de la instalación de la máquina in situ. También ocupará menos espacio y pesará menos. El resultado es un ahorro de costos al reducir la necesidad de construir estructuras adicionales, como sería el caso en una plataforma marina. Paralelamente, ofrece grandes ahorros en gastos de explotación porque hay menos mediciones, menos componentes, cero desgaste mecánico y más disponibilidad”.
Tras el proyecto submarino de Åsgard, SKF y sus socios vuelven a poner a prueba los rodamientos magnéticos. “Con cinco años de resultados positivos, el proyecto ha demostrado su efectividad”, concluye Kral.
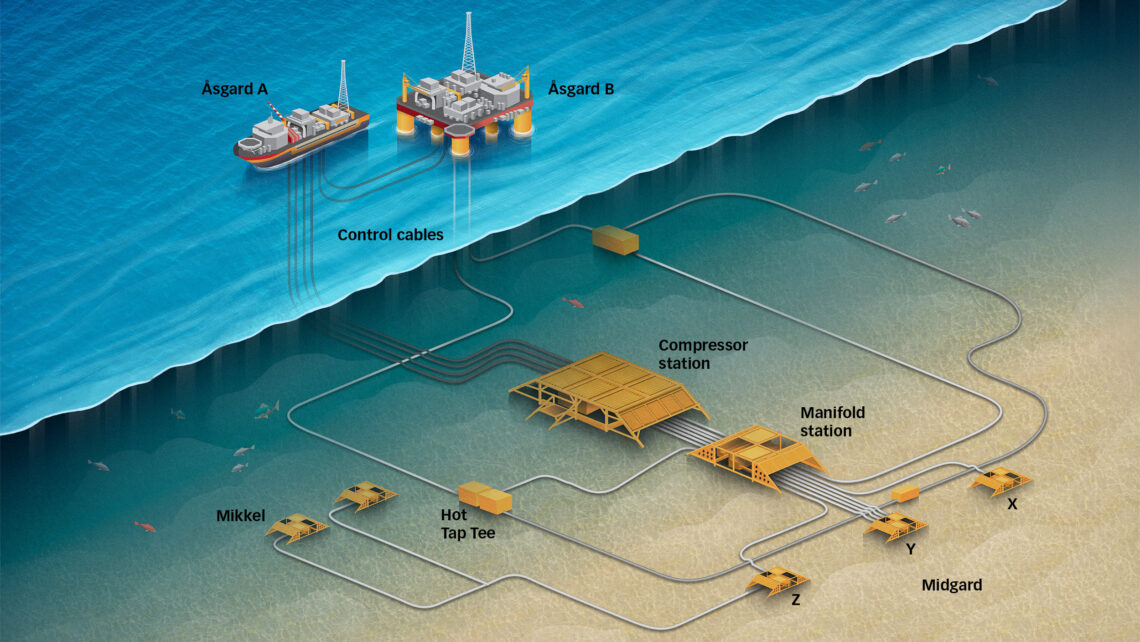
Maratón subacuático: cinco años y sigue
El primer sistema de compresión de gas submarino del mundo, equipado con rodamientos magnéticos de SKF, entró en servicio en el yacimiento de gas de Åsgard en el Mar de Noruega en septiembre de 2015. Más de cinco años y 90 000 horas después, sigue funcionando perfectamente, con una disponibilidad cercana al 100%.
Los rodamientos magnéticos de SKF son el núcleo del sistema de compresión, que consta de dos unidades de compresores herméticos instalados a 300 metros bajo la superficie. Estos motocompresores de alta velocidad (7000 r. p. m.) funcionan gracias a la tecnología de rodamientos magnéticos de SKF.
Los compresores normalmente se instalan en plataformas marinas por encima del nivel del mar. Sin embargo, instalarlos en el lecho marino en Åsgard ofrecía muchas ventajas; ha mejorado las tasas de recuperación de gas (del 50-60% a más del 80%), al tiempo que ha reducido los costos de explotación y producción. El sistema es más ecológico, con una huella más pequeña y menos emisiones de CO2.
El yacimiento de Åsgard, descubierto en 1981, es una parte importante de la infraestructura energética del Mar de Noruega. La producción empezó en 1999 y las exportaciones de gas comenzaron un año después. A lo largo de estos cinco años, SKF ha asignado al proyecto un equipo de dedicación exclusiva compuesto por hasta 20 ingenieros.