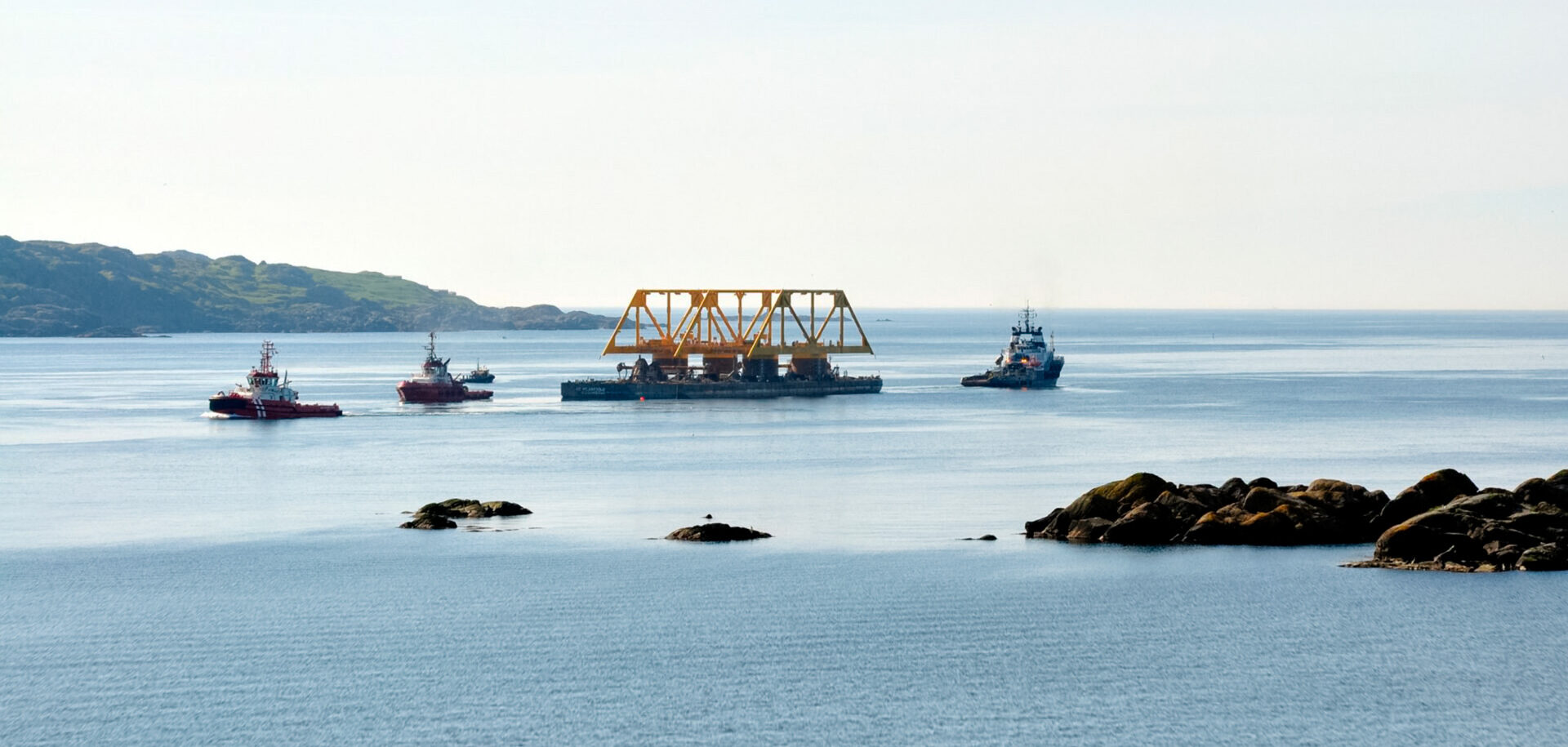
Magnetlager bestehen Härtetest
Der zuverlässige Betrieb von Turboexpander, Hochgeschwindigkeits-Elektromotoren und Kompressoranwendungen in einem rauen Umfeld ist eine echte Herausforderung. Mit herkömmlichen Lösungen lässt sich die Entwicklung von technischer Ausrüstung für den Einsatz unter Wasser, in der Wüste und bei extremen Temperaturen kaum bewerkstelligen. Aber Magnetlager sind als robuste und bewährte Technologie dieser Aufgabe gewachsen. Trotzdem werden sie bisher noch nicht oft eingesetzt. Was sie zu leisten im Stande sind, beweisen sie im Åsgard-Gasfeld im Europäischen Nordmeer, einer der weltweit anspruchsvollsten Anwendungen. Hier sind Magnetlager seit über fünf Jahren in 90.000 Betriebsstunden störungsfrei im Einsatz.
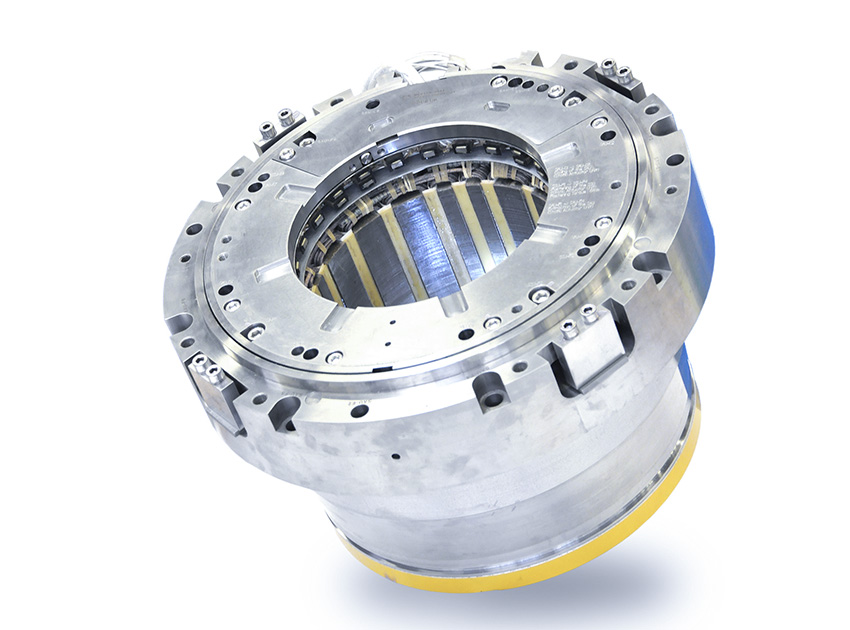
Diese Eigenschaften machen Magnetlager zu einer idealen Lösung für Anwendungen unter den harten Einsatzbedingungen des Energie-, Öl- und Gassektors. Viele Lager arbeiten in einem extrem rauen Umfeld – von saudi-arabischen Wüsten, Öl- und Gasplattformen in der Nordsee bis zu den sibirischen Gasfeldern nördlich des Polarkreises.
„Unsere Magnetlager laufen derzeit in mehr als 750 Turboexpandern, 200 Stand-alone-Kompressoren und 150 hermetisch abgedichteten Kompressoren auf der ganzen Welt. Sie sind auch in Gasturbinen, Generatoren, Pumpen und zahlreichen anderen Anwendungen eingebaut“, sagt Alexandre Kral, der im Bereich Geschäftsentwicklung Öl und Gas bei SKF tätig ist.
Die einzige realistische Lösung
In hermetisch abgedichteten Kompressoren sind Magnetlager die einzige realistische Lösung, weil sie keine Trockengasdichtung erfordern. „Magnetlager schaffen ein Magnetfeld; es gibt also keine Berührung von Teilen und keinen mechanischen Verschleiß“, erklärt Kral.
Da mechanischer Verschleiß ausbleibt, kommt es auch kaum zu Ausfällen. Bei Anwendungen im Onshore-/Offshore-Bereich benötigt lediglich die Steuerungseinheit des Magnetlagers Instandhaltung. Sie besteht jedoch hauptsächlich aus Elektronik, Lüftern und Filtern, der Wartungsaufwand hält sich also in Grenzen. Ein weiteres Plus von Magnetlagern ist, dass die Steuerungseinheit kompakter ist als das übliche Ölschmiersystem. Das ist insbesondere auf engem Raum, auf Plattformen, FPSO-Schiffen (FPSO = Floating Production Storage & Offloading) oder an entlegenen Einsatzorten von Vorteil.

Erheblich geringerer Energieverbrauch
Hinzu kommt, dass Magnetlager sauberer sind als ölgeschmierte Lager. Sie sind auch sparsamer im Energieverbrauch, da sie kein komplexes Ölschmiersystem und damit keine Leitungen zu Ölbehälter, Filter und Kühler benötigen. „Magnetlager verbrauchen rund zehnmal weniger Energie als ölgeschmierte Lager“, verdeutlicht Kral. „Dank der kleineren Anzahl von Bauteilen gibt es auch weniger Daten, die überwacht werden müssen, und der Platzbedarf ist ebenfalls geringer.“
Magnetlager verbrauchen rund zehnmal weniger Energie als ölgeschmierte LagerAlexandre Kral, Geschäftsentwicklung Öl und Gas bei SKF
Aber trotz aller Vorzüge beobachtet Kral eine gewisse Zögerlichkeit beim Umsteigen von herkömmlichen ölgeschmierten Lagern auf Magnetlager. Die höheren Initialkosten für Magnetlager seien ein häufiger Einwand.
„Einige glauben, Magnetlager seien teurer, und ja, es stimmt, die mechanischen Teile, das Gehäuse und vielleicht das Maschinendesign kosten etwas mehr“, so Kral. „Dieser Kostenunterschied gleicht sich jedoch durch den einfacheren Einbau der Maschine vor Ort wieder aus. Die Maschine hat zudem eine kleinere Standfläche und ein geringeres Gewicht. Weniger Aufwand für den Bau von Tragkonstruktionen, wie sie auf Offshore-Plattformen erforderlich sind, bedeutet Kostenersparnisse. Auch die operativen Kosten sinken drastisch, wenn weniger gemessen werden muss, weniger Ausrüstung benötigt wird, Verschleiß praktisch nicht vorkommt und eine höhere Verfügbarkeit gewährleistet ist.“
Nach dem Åsgard-Projekt sucht SKF zusammen mit seinen Partnern neue Herausforderungen für seine Magnetlager. „Fünf Jahre mit positivem Ergebnis im Åsgard-Projekt haben die Wirksamkeit der Magnetlager bewiesen“, schließt Kral.
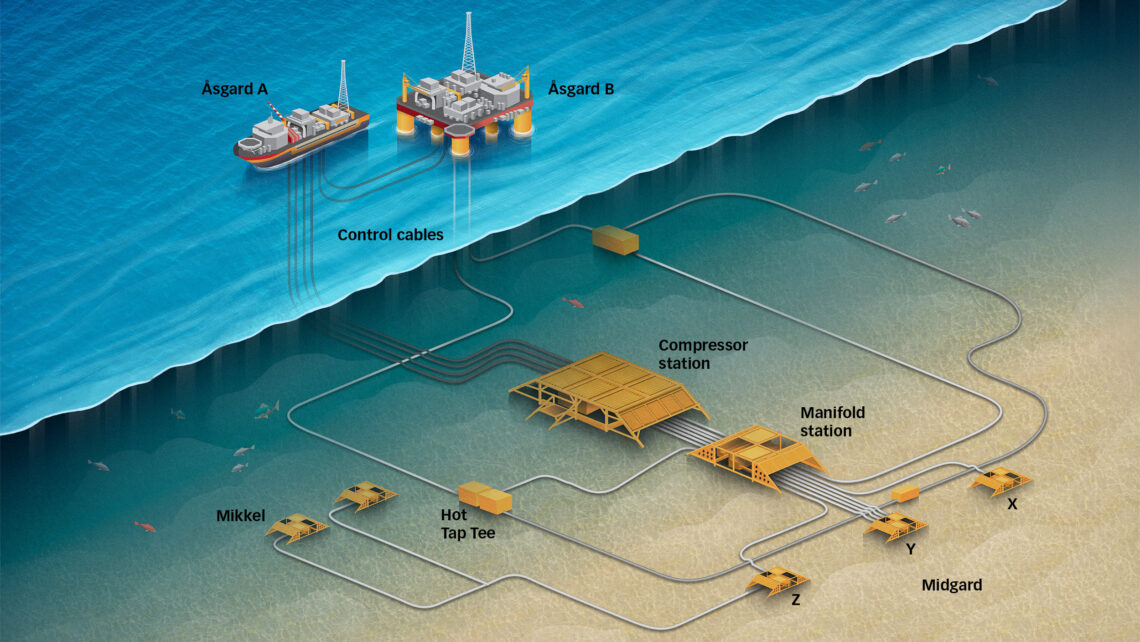
Unterwasser-Marathon – fünf Jahre und immer noch im Einsatz
Die weltweit erste Unterwasser-Gaskompressoranlage, ausgestattet mit Magnetlagern von SKF, ist seit September 2015 im Åsgard-Gasfeld im Europäischen Nordmeer in Betrieb. Nach mehr als fünf Jahren und 90.0000 Betriebsstunden läuft die Anlage immer noch reibungslos und mit nahezu hundertprozentiger Verfügbarkeit.
SKF Magnetlager sind das Herzstück des Kompressorsystems. Es besteht aus zwei hermetisch abgedichteten Kompressoreinheiten, die in 300 m Wassertiefe installiert sind. Eine Voraussetzung für diese Motorkompressoren mit hoher Drehzahl (7.000 U/min) war die Magnetlagertechnik von SKF.
Normalerweise werden Kompressoren auf Offshore-Plattformen und über Wasser installiert. Im Åsgard-Feld bot jedoch die Installation am Meeresboden viele Vorteile, darunter höhere Gasverwertungsraten (statt 50 oder 60 Prozent über 80 Prozent) bei niedrigeren Betriebs- und Produktionskosten. Die Lösung ist zudem umweltschonender und verursacht weniger CO2-Emissionen.
Das 1981 entdeckte Åsgard-Feld ist ein wichtiger Teil der Energieinfrastruktur des Europäischen Nordmeers. Die Produktion begann 1999 und der Gasexport ein Jahr später. SKF hatte während der fünf Jahre ein spezielles Team mit 20 Ingenieuren, die sich diesem Projekt widmeten.