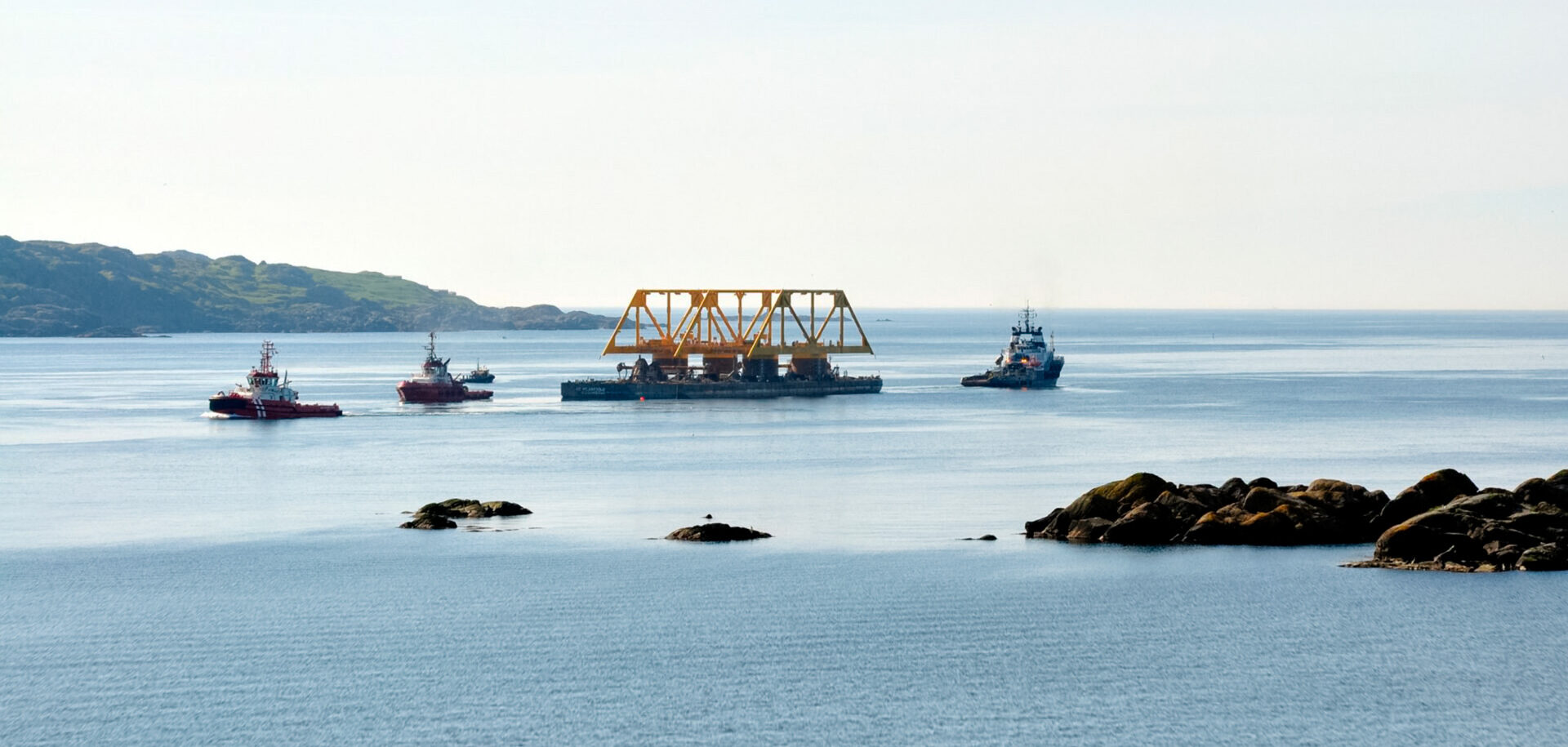
Des paliers magnétiques à toute épreuve
Exploiter des turboexpanders, des moteurs à haute vitesse et des compresseurs dans des environnements hostiles est un casse-tête. Il peut s’avérer difficile de déployer ces équipements pour qu'ils remplissent leur mission avec fiabilité sous l'eau, dans le désert et à des températures extrêmes, si on opte pour un modèle standard. Bien que les paliers magnétiques constituent une technologie robuste et éprouvée qui est tout à fait à la hauteur de la tâche, leur application n'est pas très répandue. Pourtant, ils ont démontré toute leur valeur dans l'une des applications les plus exigeantes au monde : les compresseurs du champ gazier sous-marin d'Åsgard, en mer de Norvège, où ils fonctionnent sans problème depuis plus de cinq ans, soit 90 000 heures.
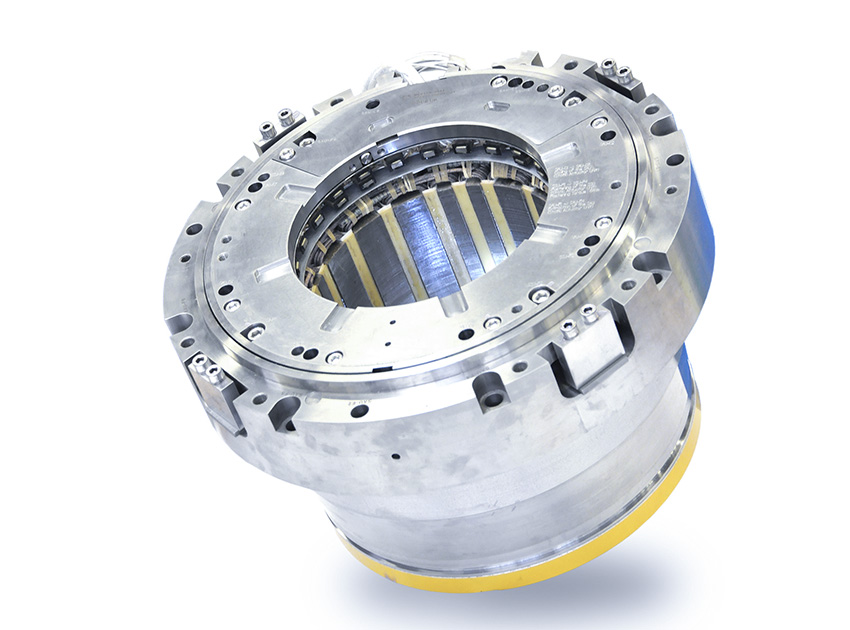
Ces caractéristiques les rendent particulièrement adaptés aux applications de production d’énergie, pétrolières et gazières dans des environnements hostiles. Nombre d’entre eux sont en service dans les environnements parmi les plus exigeants au monde, des déserts d’Arabie Saoudite aux plateformes de la mer du Nord, en passant par la taïga sibérienne au nord du cercle polaire.
« Nos paliers magnétiques sont montés dans plus de 750 turboexpanders, 200 compresseurs et 150 compresseurs hermétiques à travers le monde indique Alexandre Kral, du service développement commercial pétrole et gaz chez SKF. On les trouve également dans les turbines à gaz, les générateurs, la turbine à vapeur et bien d’autres machines. »
La seule solution réellement viable
S’agissant des compresseurs hermétiques, les paliers magnétiques sont la seule solution réellement viable car ils ne nécessitent pas de joints pour gaz sec. « Avec les paliers magnétiques, on crée un champ magnétique, de sorte qu’il n’y a ni contact entre les pièces, ni usure mécanique », explique Alexandre Kral.
L’absence d’usure mécanique élimine pratiquement tous les arrêts intempestifs. Dans les applications onshore/offshore, seul le contrôleur du palier magnétique doit être révisé, et comme il est composé essentiellement d’un système électronique, de ventilateurs et de filtres, il y a beaucoup moins de composants à entretenir. Autre avantage des paliers magnétiques, leur contrôleur est plus compact que le système de lubrification à huile standard. C’est un atout, notamment dans les endroits exigus comme les plateformes, les FLNG, les FPSO ou dans les zones reculées.

Réduction substantielle de la consommation d’énergie
En outre, les paliers magnétiques sont plus propres que les paliers à l’huile. Cette caractéristique contribue à réduire considérablement la consommation d’énergie car, avec les paliers magnétiques, nul besoin d’un système complexe de lubrification à l’huile, notamment la tuyauterie menant au réservoir d’huile ainsi que les systèmes de filtrage et de refroidissement. « Les paliers magnétiques consomment environ dix fois moins d’énergie que les paliers à l’huile, souligne Alexandre Kral. Il y a également moins de données à surveiller en raison du peu d’appareils nécessaires. Et quand il y en a moins, on n’a pas besoin d’autant d’espace. »
Les paliers magnétiques consomment environ dix fois moins d’énergie que les paliers à huile.Alexandre Kral, du service développement commercial pétrole et gaz chez SKF
Pourtant, malgré tous ces atouts, Alexandre Kral a constaté à maintes reprises une certaine réticence à sélectionner des paliers magnétiques plutôt que des paliers à l’huile plus habituels. L’une des objections habituellement formulées concerne l’investissement initial. « Certains pensent que les paliers magnétiques sont plus onéreux, et il est vrai que les composants mécaniques, l’armoire de contrôle et peut-être la conception de la machine coûtent un peu plus cher. Mais ce surcoût est facilement compensé par la simplification du processus d’installation sur place. Celle-ci aura également un encombrement plus réduit et sera moins lourde. Ceci permet de faire des économies car il est moins nécessaire de réaliser des structures dédiées comme, par exemple, sur une plateforme offshore. En parallèle, il y a des gains substantiels sur le plan des coûts d’exploitation car il y a moins de mesures, moins de matériel, pas d’usure mécanique et une plus grande disponibilité. »
Suite au projet sous-marin mené à Åsgard, SKF et ses partenaires vont remettent les paliers magnétiques à l’épreuve. « Avec des résultats positifs sur cinq ans, le projet Åsgard a prouvé son efficacité. »
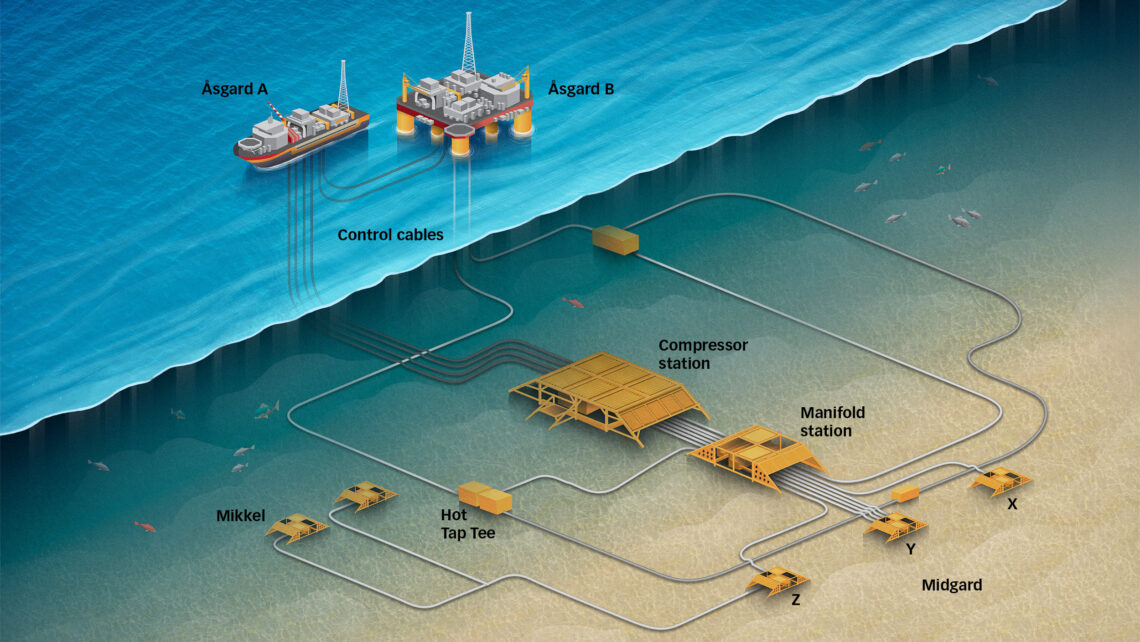
Un marathon sous-marin : cinq ans et ce n'est pas terminé
Équipé de paliers magnétiques SKF, le tout premier système sous-marin de compression de gaz au monde est en service sur le champ gazier d’Åsgard, en mer de Norvège, depuis septembre 2015. Plus de cinq ans et 90 000 heures plus tard, il fonctionne toujours parfaitement, avec une disponibilité proche de 100 %.
Les paliers magnétiques SKF sont au cœur du système de compression, lequel comprend deux compresseurs hermétiques immergés à 300 m de profondeur. Ces compresseurs à moteur haute vitesse (7 000 tr/min) ont pu être conçus grâce à la technologie des paliers magnétiques de SKF.
Les compresseurs sont généralement installés sur des plateformes offshores et au-dessus du niveau de la mer, mais une installation immergée sur le champ gazier d’Åsgard offrait de nombreux avantages, notamment une hausse du taux de récupération du gaz (de 50 ou 60 % à plus de 80 %) tout en réduisant les coûts d’exploitation et de production. Le système est également plus respectueux de l’environnement car son emprise est moindre et ses émissions de CO2 réduites.
Découvert en 1981, le champ d’Åsgard est un élément primordial de l’infrastructure énergétique de la mer de Norvège. Son exploitation a commencé en 1999, les exportations de gaz un an plus tard. SKF a mis en place une équipe dédiée, comptant jusqu’à 20 ingénieurs, qui ont travaillé sur le projet pendant cinq ans.