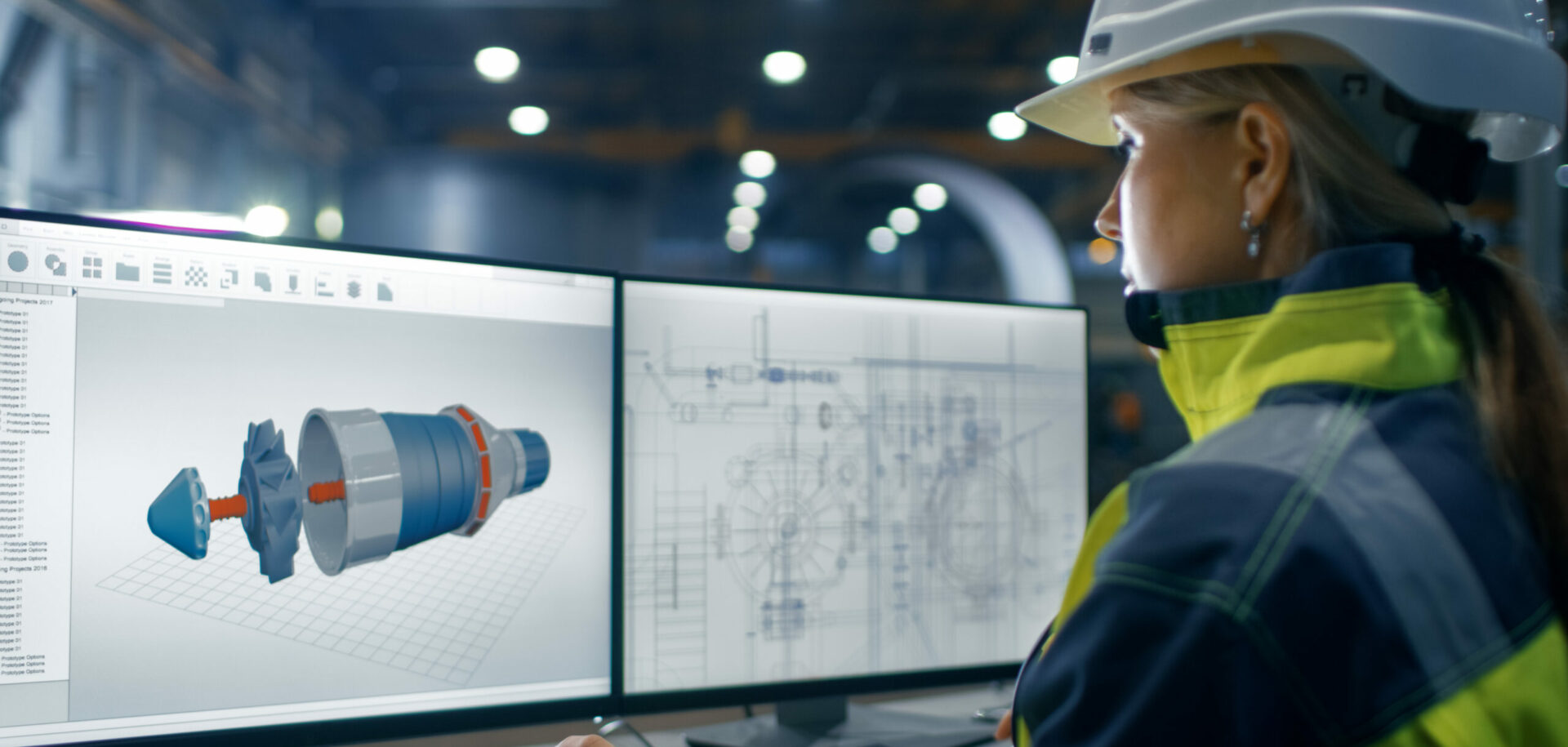
Food for thought
Food and beverage producers must take an uncompromizing approach to hygiene, health and safety. They need machine solutions that can match these expectations and at the same time support lower operating costs through lower need for maintenance. SKF’s food line Y-bearing units have been designed to do just that.
Food and beverage processing is a particularly challenging area for machinery suppliers. Production areas can be hot, cold or humid, or they can be chemically aggressive because of the nature of the food or drink (orange juice is acidic, for example, while biscuits are abrasive) or the consequence of strict cleaning regimes. Whatever the food or beverage, the machinery is often exposed to frequent high-pressure washdowns with caustic antibacterial cleansing agents.
The food line Y-bearing units from SKF have been developed to offer a complete assortment of bearings and bearing units for this demanding and varied environment. SKF Y-bearings for the food industry are hygienically designed, sealed and lubricated for life with NSF-approved SKF food-grade grease and offer maintenance-free operation.
The Y-bearing units
Y-bearings for the food industry are sealed deep groove ball bearing inserts with a convex sphered outer ring outside surface. These high-quality, corrosion-resistant bearings are available in stainless steel or with a zinc (ZYC) coating and are tested to a 10 MPa (100 bar) pressure. When coupled with tailored sealing and grease lubrication solutions (se bild . 1), these can be incorporated into versatile and cost-effective bearing unit designs.
The new SKF range comprises three distinct housing designs:
-
composite housings are strong, lightweight and chemical resistant (se bild . 2).
-
cast stainless steel housings are for heavy-duty applications (se bild . 3).
-
zinc-coated housings are strong and corrosion resistant (se bild . 4).
Y-bearing units with a composite housing
The SKF Y-bearing composite housings (se bild . 2) resist citric acids, cooking fats and most chemicals used in food and beverage processing. They are made of a thermoplastic composite material that can be up to 61 % lighter than same size cast iron housings. The spherical bore accommodates the insert bearing’s spherical outer ring outside surface, enabling the units to accommodate initial bearing misalignment.
Steel coils embedded in the housing contribute to the housing’s fracture strength. The radial breaking load is far greater than the static load rating of the bearing. The SKF Y-bearing housings have possibly the highest fracture strength of any composite unit available.
A polyurethane-filled housing base enables the unit to meet flush with its mounting surface. Flush surface-to-surface mounting eliminates gaps, which otherwise are potential areas for bacteria to harbour and grow. Stainless steel bolthole inserts provide added strength to each housing foot.
Y-bearing units with an extreme-duty cast stainless steel housing
Where extremely challenging applications demand additional dur-ability, SKF offers AISI 300 series cast stainless steel housings (se bild . 3). These are suitable for any application where loads are very heavy or where shock loads are possible and the extra strength and toughness of the stainless steel housings are a benefit.
Exposure to extremely aggressive washdown chemicals is another reason to choose these stainless units. While composite and plated housings are resistant to most of the chemicals in use today, they can be susceptible to some strong concentrations of chlorine, hydrogen peroxide and other chemicals. Cast stainless steel housings, made of an AISI 300 series stainless steel, are not affected by these chemicals.
The bases are cast flat with no recesses to avoid trapping debris and bacteria, and the exposed surfaces of the housings have no unnecessary crevices or pockets. Consideration has been given to surface roughness as well. The smooth cast surfaces minimize the material trapped on the surface, enabling a more thorough cleaning.
Y-bearing units with a coated cast iron housing
The newest solution for the food processing industry is a corrosion resistant, heavy-duty cast iron series of bearing units (se bild . 4). The cast iron housings are protected with a unique and proprietary ZMaRC® coating, which is part of the metal surface and therefore does not have the flaking problems associated with nickel-plated products. The housings are matched with ZMaRC-plated, lubricated-for-life, high-quality insert bearings.
Housings and bearings are resistant to the majority of common washdown solutions. These units require no relubrication, even in a washdown environment, thus saving time and money while providing a cleaner-running bearing unit. The added strength and durability of these housings make them particularly well suited for applications in red meat, pork and poultry processing facilities where both housing strength and corrosion resistance are a concern.
To comply with health and safety regulations, the composite and stainless steel housed Y-bearing units can be supplied with effective end covers (se bild . 5). Closed end covers are tested to withstand a 10 MPa (100 bar) pressure wash for complete security and operator safety. An optional drain hole is part of the end cover design.
Sealing and lubrication
SKF uses its unique “2 RF” sealing solution for the bearings (se bild . 1). It consists of a multi-lip labyrinth seal, supported by a stainless steel insert, a stainless steel flinger and a food-compatible rubber-backed seal gasket. The SKF seal design is industry proven to be very effective during washdowns. The flinger and seal rubber lips with optimized axial contact form a double barrier against contaminants and washdowns. The seal gasket prevents contaminants from migrating around the seal insert’s outside diameter. The flinger adds mechanical and centrifugal protection to prevent contamin-ants from entering into the bearing cavity. The space between the insert seal and flinger is filled with grease (see below) for an even greater sealing efficiency. This unique sealing arrangement truly prevents detergent creep and water entry, so it is not necessary to re-grease to secure water absence. This makes the Y-bearing unit range maintenance-free.
The SKF Y-bearing is factory lubricated for life with an NSF approved SKF food-grade grease. This high-quality synthetic grease is odourless and tasteless, leaving foods unaffected. It resists washouts even during frequent high-pressure washdowns with hot or cold water containing disinfectant solutions. This grease can be used in applications where operating temperatures range from –15 °C to +120 °C.
Other grease benefits include excellent internal and external bearing corrosion protection, high ageing resistance for extended lubricant life plus high load-carrying capacity, which helps prevent premature bearing wear.
The most sustainable aspect of the SKF Y-bearing units is centred on the ability of these units to perform in a wet, abrasive or washdown environment without requiring any relubrication for the life of the bearing unit. There are several environmental benefits related to this feature.
Less grease is used because it avoids the common practice in washdown environments of relubricating bearing units frequently (often daily). This practice is deemed necessary to purge water and contaminants that can enter units past the seals during the washdown cycle. This frequent re-greasing practice can consume considerable grease quantities per year.
There is no grease purged into the environment with the SKF sealed system. When standard bearing units are relubricated frequently to purge water and contaminants, excess grease is often discharged past the bearing seals. During the next washdown cycle, this grease is washed away and ends up in the plant’s wastewater. With large amounts of grease often running through a single unit that is re-greased daily, this amounts to substantial quantities of waste grease entering the environment.
Since SKF Y-bearing units require no re-greasing, they do not discharge used grease from the seals. This eliminates a major source of wastewater contamin-ation, resulting in a cleaner plant environment and lower disposal costs for users. For example, if 20 g of lubricant is used per bearing purge during each weekly mainten-ance cycle that adds up to 1 kg per bearing per year. Multiply that by the number of bearings in a particular application, and you can see that the resulting se bild ure is significant in terms of cost of lubricant, staff time and disposal.