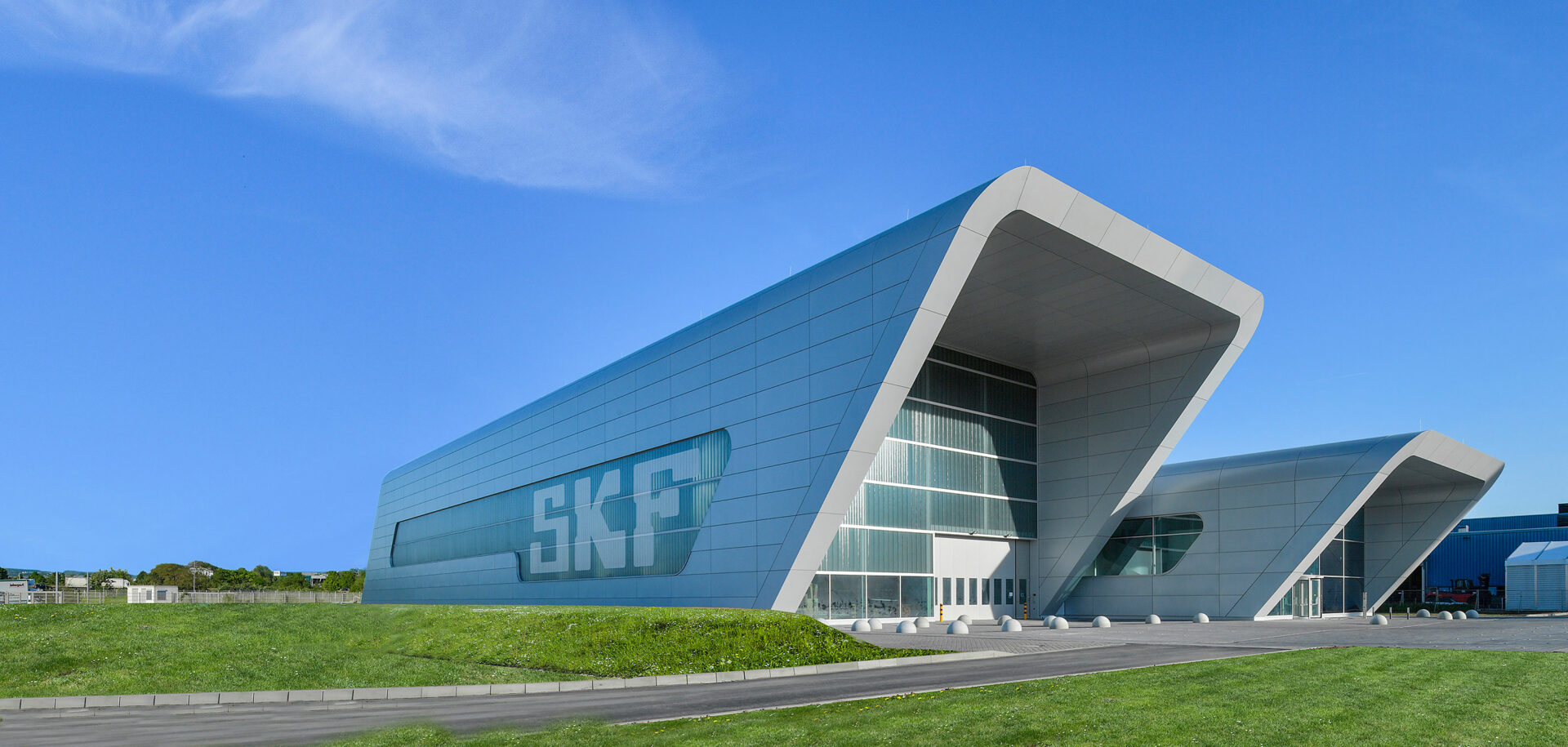
Aux limites du possible
Dédié aux roulements de grandes dimensions, le Centre d’essais Sven Wingquist offre une capacité inégalée. Situé en Allemagne, il est doté de deux bancs d’essais gigantesques pour tester les roulements dans des conditions extrêmes. Ces travaux préliminaires technologiques permettront d’optimiser encore la conception des roulements de grandes dimensions et d’améliorer l’efficacité de la fabrication. Au bout du compte, les clients bénéficieront de solutions optimisées.
SKF dispose d’un vaste portefeuille de logiciels de calcul et de simulation extrêmement puissants pour tous types de roulements. Des systèmes sophistiqués permettent notamment d’étudier le comportement des roulements au sein d’un environnement virtuel. Grâce à l’outil SimPro Expert, par exemple, des spécialistes hautement qualifiés peuvent calculer la fatigue des roulements en s’appuyant sur la théorie SKF de l’allongement de la durée de vie des roulements. Ce logiciel est le fruit non seulement d’années de recherche et développement, mais aussi de l’expérience opérationnelle accumulée pendant des décennies. Il en va de même pour l’outil, encore plus puissant, baptisé BEAST que les ingénieurs SKF utilisent pour simuler en détail les phénomènes dynamiques qui s’opèrent à l’intérieur d’un roulement. Il s’agit d’un banc d’essai virtuel qui permet d’étudier les charges, les moments, etc. qui s’exercent à l’intérieur d’un roulement, et ce dans pratiquement toutes les conditions de charge.
Des logiciels en deçà de la réalité
Cependant, ni ce dernier logiciel ni aucun autre programme de simulation n’était capable–jusqu’ici – de reproduire ce qui se passe à l’intérieur des roulements de grandes dimensions de manière véritablement réaliste. L’expérience a montré que, malgré les calculs les plus méticuleux, certains roulements de grandes dimensions, pourtant conçus en intégrant des marges de sécurité supplémentaires et fabriqués selon les normes les plus strictes, étaient sujets à des dommages et des défaillances précoces. Il est clair, par conséquent, que certains phénomènes se produisant au sein des applications réelles ne sont pas totalement pris en compte par les algorithmes des modèles de simulation actuels basés sur le lien de cause à effet.
Résumé
Jusqu’ici, aucun programme de simulation au monde n’était capable de reproduire de manière véritablement réaliste l’ensemble des phénomènes dynamiques qui s’opèrent à l’intérieur des roulements de grandes dimensions. Deux nouveaux bancs d’essais au sein du Centre d’essais de haute technologie Sven Wingquist de SKF à Schweinfurt, en Allemagne, peuvent fournir des connaissances encore plus pointues qui permettront d’améliorer les modèles de simulation actuels pour des calculs plus proches de la réalité. En outre, le savoir-faire acquis par ce biais sera intégré au développement de produits afin que les futures générations de roulements de grandes dimensions atteignent une durée de vie optimale au sein de leurs applications respectives avec un poids et un frottement minimisés. Tous ces avantages cumulés représentent des économies de ressources, non seulement pendant les essais et lors de la production, mais aussi au sein de l’application commerciale des futurs roulements de grandes dimensions SKF. Ce qui est bénéfique aussi bien pour l’environnement que pour les clients.
L’exploration des causes profondes, jusqu’ici indécelables, de ces dommages est l’une des motivations qui ont conduit SKF à investir environ 40 millions d’euros dans le Centre d’essais Sven Wingquist, à Schweinfurt, en Allemagne, et se doter ainsi du centre d’essais pour roulements de grandes dimensions le plus puissant au monde. Logés dans deux bâtiments jumeaux d’allure futuriste (Fig. 1), les deux nouveaux bancs d’essais gigantesques poussent les roulements de grandes dimensions jusqu’à leurs derniers retranchements.
Des charges énormes pour l’énergie éolienne
Le plus grand des deux (Fig. 2) est le premier banc d’essais au monde capable d’accueillir et de tester non seulement un roulement destiné à l’industrie éolienne (dont le diamètre extérieur peut atteindre jusqu’à 6 m), mais aussi l’ensemble complet, incluant les pièces adjacentes du client. Avec des dimensions d’encombrement gigantesques de 9 x 11 x 8 m, ce banc d’essais pèse environ 700 tonnes. Il est équipé de pas moins de 64 vérins disposés radialement et axialement et capables de développer plusieurs méganewtons de charges dynamiques.
Les vérins hydrauliques agissent dans un premier temps sur le disque en acier surdimensionné (Fig. 3) qui tourne à l’intérieur du banc. Ce disque gigantesque de 7 m de diamètre pèse 125 tonnes. Il transmet les charges produites par les vérins hydrauliques à la pièce par le biais d’un adaptateur auquel le roulement testé est fixé.
La méthode consistant à utiliser un disque pour le transfert des charges disponibles au roulement testé présente un avantage décisif : les charges à laquelle la pièce est soumise ne sont pas limitées par la stabilité inhérente d’un roulement exerçant la charge. Au lieu de cela, le système, constitué des vérins et du disque, peut appliquer des charges sur tous les axes ; ces charges cumulées représentent plusieurs fois les charges des installations d’essais les plus puissantes qui existaient jusqu’ici. Le nouveau banc d’essai SKF peut en outre atteindre des vitesses de rotation très élevées pour les dimensions du roulement testé.
20 ans simulés en quelques semaines
Cette combinaison unique de charges dynamiques et maximales, de contraintes de flexion et de vitesses de rotation se traduit pour le client par un avantage économique substantiel. En effet, pour garantir la rentabilité d’une éolienne, les gigantesques roulements, une fois installés, doivent fonctionner sans avarie pendant au moins 20 ans. Ces 20 années, et l’ensemble des charges qu’une telle période représente, sont simulées de manière très réaliste par le nouveau banc d’essais en l’espace de quelques semaines, grâce à une procédure accélérée. Il en résulte non seulement un gain de temps considérable, mais aussi des économies financières et d’énergie. Ces économies d’énergie peuvent encore être augmentées avec un système de récupération de la chaleur : la chaleur générée par le banc d’essais est réintroduite dans le réseau et utilisée pour le bâtiment du banc d’essai et l’usine voisine de fabrication de roulements de grandes dimensions. Ce rendement énergétique a valu à cette installation d’essais gigantesque de bénéficier d’un financement du ministère bavarois de l’Économie et des Médias, de l’Énergie et des Technologies, à hauteur d’environ 1,9 million d’euros.
Des charges sous contrôle
Pour garantir un contrôle optimal des charges énormes appliquées au roulement testé sur le banc, les segments inférieurs des paliers sont fixés sur leurs socles au moyen de 200 boulons filetés M80 avec une précharge de plusieurs méganewtons. Ces boulons sont insérés dans des bases qui font partie des fondations de 3 000 tonnes dissociées du reste du bâtiment ouvert et aéré afin d’éviter les perturbations pour le bâtiment proprement dit.
L’usinage de précision à l’interface entre les socles et le palier est d’autant plus remarquable que la sous-structure est extrêmement solide : les surfaces de contact présentent un défaut de planéité de seulement quelques dixièmes de millimètre sur une distance d’environ 10 m (Fig. 4).
Plus petit, plus flexible, plus rapide
En comparaison, le plus petit des deux nouveaux bancs d’essais SKF (Fig. 5) semble moins impressionnant – il n’en est pas moins puissant. Sa tête d’essais de 130 tonnes est équipée de quatre vérins axiaux et deux vérins radiaux qui peuvent agir sur une grande variété de roulements de grandes dimensions grâce à l’utilisation d’adaptateurs de bagues intérieures et extérieures.
Il est ainsi possible de tester des roulements destinés par exemple aux secteurs de la construction navale, de l’exploitation minière, de la sidérurgie et de la métallurgie, des pâtes et papiers et du ciment. Ce banc d’essais se caractérise ainsi par une grande polyvalence. Paradoxalement cette flexibilité est offerte par, une fois de plus, un chef d’œuvre de mécatronique des plus imposants. L’installation pèse environ 300 tonnes.
Cette installation génère des forces de plus de six méganewtons (ce qui correspond approximativement à la force générée par un moteur du lanceur aérospatial Saturn V) et peut atteindre des vitesses de rotation supérieures à 200 tr/min. Ces charges et vitesses combinées placent le plus petit de ces deux nouveaux bancs d’essais SKF à un niveau mondial inégalé. Sa capacité unique permet au banc d’essais de révéler des opportunités d’économies significatives d’énergie et de matériaux pour la production des roulements de grandes dimensions. C’est ce qui a valu au banc d’essais d’être retenu dans le cadre du Programme d’innovation environnementale du ministère fédéral allemand de l’Environnement, la Protection de la nature, la Construction et la Sûreté nucléaire et de bénéficier à ce titre d’un financement de 1,6 million d’euros.
Lubrification limite
Le plus petit banc d’essais du centre présente une autre particularité inhabituelle : il intègre un équipement de lubrification spécial issu des systèmes de lubrification SKF (Fig. 6). Généralement, les solutions de l’entreprise sont utilisées dans des applications diverses pour garantir une lubrification optimale des roulements dans des quantités adaptées et en temps opportun. Cependant, le système spécialement mis au point pour le centre d’essais offre exactement l’inverse : lors des essais, il pousse le roulement testé jusqu’à ses limites en termes de déficit de lubrification. Les résultats des essais peuvent être très instructifs pour améliorer encore la robustesse des roulements de grandes dimensions.
L’ensemble du système de 6 m de large par 1,6 m de profondeur pour un poids total de 7,2 tonnes peut contenir 3 000 litres d’huile lubrifiante. Il résulte d’un transfert de technologie en provenance de l’industrie des pâtes et papiers et de modifications profondes apportées par des experts SKF en systèmes de lubrification pour répondre aux exigences spécifiques du centre d’essais. Il convient également de souligner la conception optique exceptionnelle du dispositif et les mesures de protection anti-bruit hors du commun mises en œuvre.
Le paramètre crucial de la température
Afin d’exposer le roulement testé à des conditions de charge extrêmes, mais aussi à des conditions de lubrification tout aussi extrêmes, SKF a conçu son système pour des températures d’huile deux fois supérieures à celles relevées dans des solutions classiques. Il est ainsi possible d’utiliser toute la plage de température pour soumettre le roulement testé à d’énormes contraintes tribologiques.
Pour éviter tout dommage causé au système de lubrification en cas de « chaude lutte » avec le roulement testé, un système de refroidissement basé sur des échangeurs de chaleur à plaques a été installé.
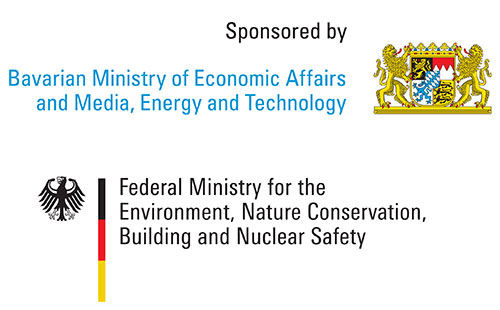
Sponsored by
Le ministère bavarois de l’Économie et des Médias, de l’Énergie et des Technologies a accordé au plus grand des bancs d’essais un financement de près de 1,9 million d’euros, tandis que le plus petit a été retenu dans le cadre du Programme d’innovation environnementale du ministère fédéral allemand de l’Environnement, la Protection de la nature, la Construction et la Sûreté nucléaire et a bénéficié d’un financement de 1,6 million d’euros.
Des mesures précises
Depuis le poste d’alimentation, l’huile lubrifiante est acheminée par pompage jusqu’au roulement testé via une douzaine de lignes. Une console de distribution connectée permet un dosage précis de l’huile par ligne et par point de lubrification. Un système de lubrification unique permet d’exposer des roulements de grandes dimensions destinés à l’industrie lourde aux conditions de lubrification les plus difficiles sous une variété de charges. De plus, le dosage variable combiné à la multitude de points de lubrification garantit un suivi extrêmement localisé de la distribution du lubrifiant ou du débit à l’intérieur de la pièce testée. Pour ce faire, le support qui maintient le roulement testé est pourvu d’un arsenal de capteurs supplémentaires. Ces capteurs non seulement mesurent les températures locales et leurs tendances mais détectent également les vibrations, charges et positions des éléments critiques. Enfin, les experts SKF peuvent savoir exactement quels phénomènes dynamiques s’opèrent à l’intérieur du roulement, où et dans quelles conditions.
Actuellement, les ingénieurs SKF mettent tout en œuvre pour que les travaux préliminaires relatifs aux essais répondent aux attentes élevées et lèvent le voile sur les secrets des roulements de grandes dimensions. Ils travaillent en ce moment même à la validation de l’imposant matériel et au calibrage des capteurs de mesure sensibles.