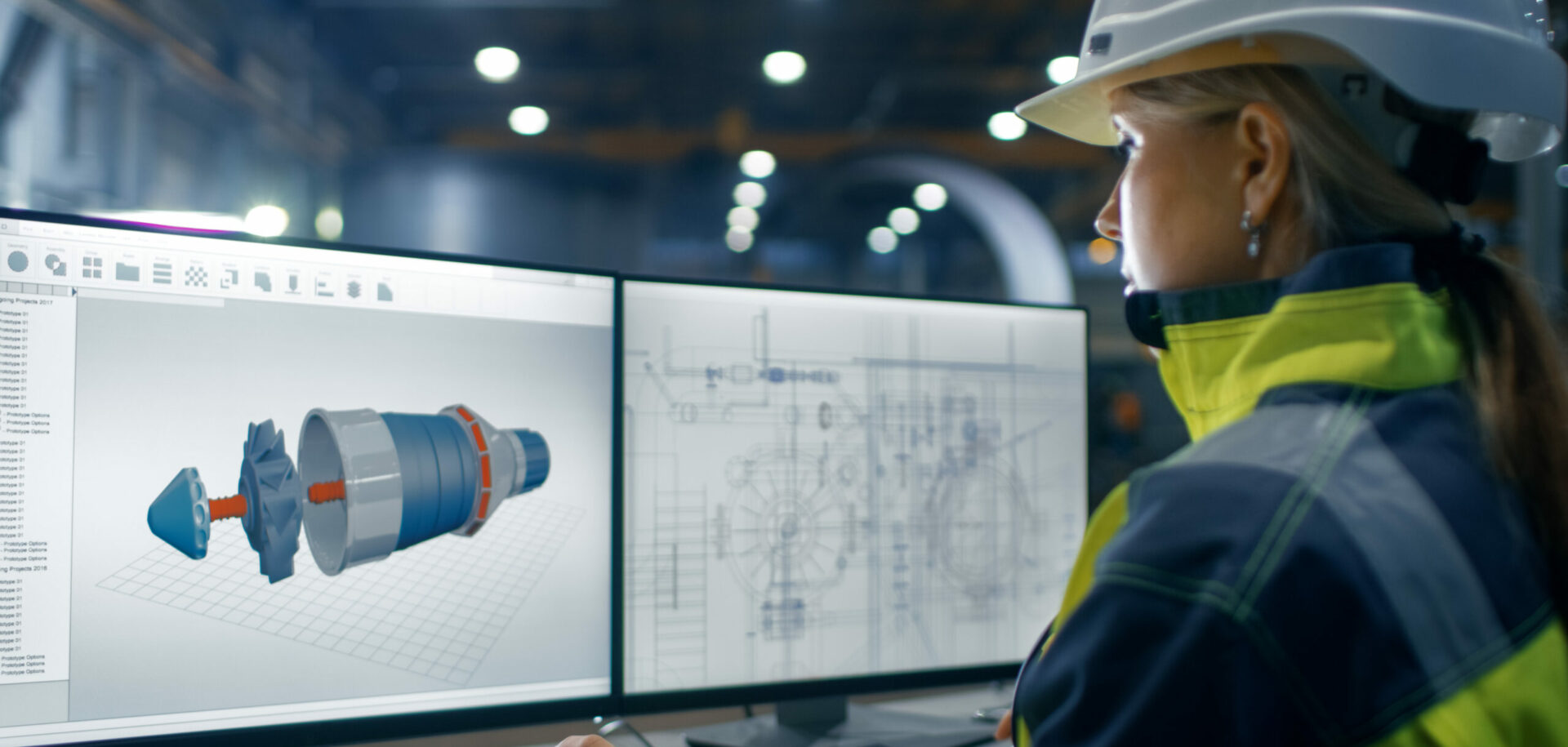
Front-page precision
Summary
Eccentric unit
In 1991, MAN Roland entered into an exclusive contract with SKF to develop a new bearing system for printing cylinders. The printing cylinder bearing unit, which was initially developed for the Geoman press and is also used in the presses made by MAN Plamag in Plauen, Germany, includes the functions of the various elements that were previously used, but brings them together into a single, more precise and cost-effective unit.
Effectively, the unit includes both the cylindrical roller bearing and the eccentric housing which can be turned to adjust the position of the printing cylinders. The whole unit can simply be REPLACEed directly into the frame of the press, and does not require a separate bushing. As a result of its construction as a single unit, it offers a high level of radial stiffness and a smoother, more precise eccentric adjustment, with low friction and long life.
SKF makes the units to a variety of specifications and sizes, from two-ring concentric to four-ring, two-eccentric.
Quality standards for printing machines are as demanding as those in the aerospace industry. Add speed, and you will understand what MAN Roland is all about.It all began back in 1845, when Carl August Reichenbach and Carl Buz delivered their new company’s first high-speed press from their factory in Augsburg, Germany, to a local printer by the name of Nikolaus Hartmann. With the flatbed press – whose production utilised a technique invented by Reichenbach’s uncle – 1,000 sheets could be printed in an hour rather than a day, a substantial development in the history of printing.
That first press was still in operation with the same printing company 110 years later, in 1955, but by then the rest of the printing industry had progressed substantially. For one thing, Reichenbach and Buz’s enterprise had become one of the world’s leading industrial companies, making commercial vehicles, machinery and plants under the name by which it is still known: MAN, for Maschinenfabrik Augsburg Nürnberg.
Jump ahead another 44 years, to the present, and Nikolaus Hartmann would be wondering what on earth they’re producing in the MAN Roland factories these days. (The printing machine division is now called MAN Roland, after a merger with Roland Offset of Offenbach, Germany, in 1979.)
Nowadays, panels hide thousands of switches and connectors. A single printing unit, together with its paper feed and folding equipment, can stretch over three storeys of a building. The largest printing press produced by MAN Roland, the Colorman, manages up to 86,000 16-page four-colour copies an hour. Its cylinders are up to two metres long, and turn at speeds higher than 1,000 rpm. The paper whips along from its huge rolls, and rushes between four printing cylinders, providing four colours in one pass. Several of these “towers” run in parallel, the paper from all of them will be directed to a folding machine to make a single newspaper of up to 160 pages, and all of it can be operated from a single control computer.
MAN Roland boasts that quality standards and control in the construction of these large printing machines is matched only by that of the aerospace industry. This claim was confirmed a few years ago by Det Norske Veritas, the independent certification organisation. Moreover, in 1995 MAN Roland was awarded the quality management certificate showing that it fulfils the requirements of the standard ISO 9001.
It’s easy to believe, when you think about your daily newspaper: that small, easy-to-read clear type is produced in a microsecond as the paper dashes past the roller carrying the image. The slightest imprecision in the process will lead to a blur; the slightest inaccurate movement at that speed in the machinery that folds, cuts and sorts the paper will result in damage to the finished product.
MAN Roland is one of the world leaders in the production of such large newspaper presses. Rupert Murdoch’s News International, the Axel Springer publishing house and many other prominent publishers throughout the world print on machines made in Augsburg. Bernd Egert, MAN Roland’s marketing director, says 330 million people read newspapers printed on their presses. In 1987, Murdoch placed the biggest-ever order for printing presses. It was for 42 Colorman presses worth a billion marks (US$610 million) for printing locations in Britain and Australia. With such a large order, it’s no surprise that Murdoch decided to give the presses a name of his own: the Newsman.
Full-service printing
MAN Roland describes itself as a “systems provider for the printers and publishers of the world” and emphasises that it can fulfil any request. A subsidiary, Eurografica, can build the necessary buildings, and MAN Roland can coordinate everything it doesn’t do itself. As Egert says, “We can organise everything from financing to staff training to the supply of ink.”
The company is not affiliated with any specific suppliers, and can thus fulfil a customer’s special needs. A worldwide distribution and maintenance network means that full service can be provided globally. The company offers a complete range of offset presses, sheet-fed and rotary (or web-fed) machines in all sizes, for books, magazines, newspapers, packaging and advertising brochures.
Offenbach, originally home of Roland Offset and now headquarters for MAN Roland, makes sheet-fed presses, for example the Roland 700. These presses are popular machines because of their flexibility. In less than 10 minutes, a new job can be set up with automated printing plate changeover.
MAN Plamag in Plauen, Germany, makes small and medium-sized web-fed offset presses for medium and short-run newspapers. The Coroman, Cromoman and Uniset are designed to provide small newspapers and other printers with the advantages of high flexibility and actuality.
In Augsburg, the original home of MAN, their giants are made. The Rotoman and Lithoman presses are designed for illustrated magazines, catalogues, brochures and directories, while Ecoman, Geoman and Colorman are directed at medium- and large-sized newspapers.
The presses are of a modular design so that customers can get exactly what they need. And the modular design makes it possible to upgrade presses, so that a decision to run, say, a configuration of four one-colour units, two two-colour units and a four-colour unit would not be irreversible if the market changed.
Research for future
MAN Roland is continually involved in research to improve its products. The development of a printing cylinder bearing unit for the Geoman heavy-duty offset press in close cooperation with SKF is one example (see box), and the development of digital “computer to press” technology is another.
The company faces a demand for ever-larger printing machines and, at the same time, the demand for more precise marketing of print products. For example, newspapers want to print local editions or special pages on relatively short runs. Currently, every time the original has to be changed, a new printing plate has to be prepared and fitted to the printing cylinder. If the original can be set up on a computer as usual, and transferred directly to the cylinder, then this would save time and money.
MAN Roland has come up with solutions to these problems using what it calls DICO (digital changeover) technology, by which a laser creates the image directly on the cylinder, both in offset and gravure printing. What is more, the image can be erased from the cylinder, allowing immediate re-imaging.
If Nikolaus Hartmann were to visit the factories of MAN Roland today, he might not recognise much, except in the company museum. But, as when Reichenbach and Buz sold him their first press, he would likely still have the feeling of buying a top-quality, up-to-the-minute piece of printing equipment.
Michael Lawton
a business journalist based in Cologne
photos MAN Roland
and Alexander Farnsworth