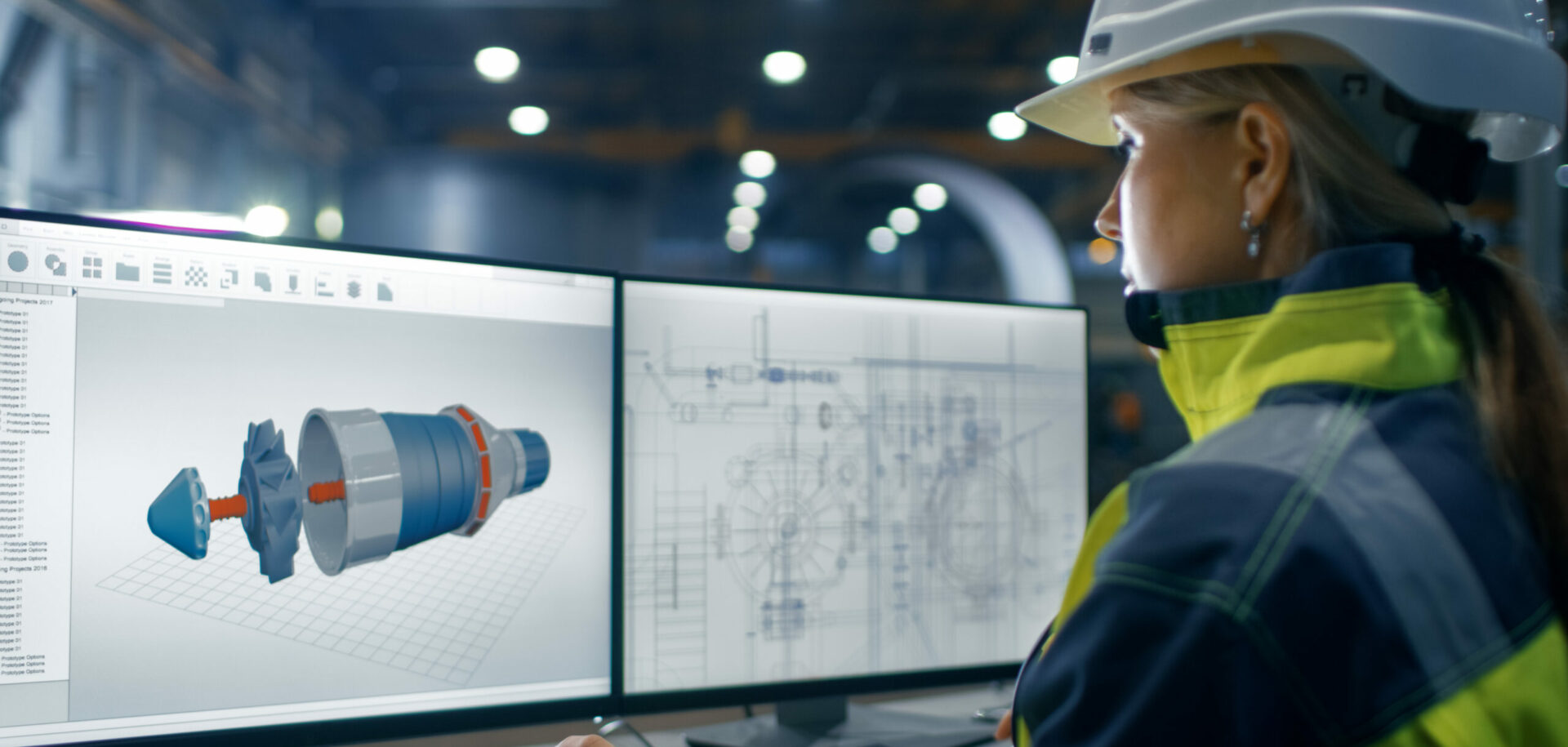
Good vibrations from the DV 90
The world’s northernmost airport and the world’s tallest bridge were challenging construction projects by anyone’s standards. Hamm’s DV tandem rollers lived up to the challenge.
The world’s northernmost airport and the world’s tallest bridge were challenging construction projects by anyone’s standards. Hamm’s DV tandem rollers lived up to the challenge.
“Don’t leave homewithout a rifle,” newcomers to Longyearbyen are warned. “Otherwise the polar bears will get you.” Longyearbyen is the capital of the Svalbard archipelago (population 2,500), between the northern tip of Norway and the North Pole. The world’s northernmost airport is near the town. To match a new terminal built in 2006, the airport’s operator, Avinor AS, decided to smooth some bumps out of the 2,480-metre runway and lengthen it by 160 metres.
The bitter arctic climate was a major difficulty. Work could be done only during the short summer of the “midnight sun,” as the ground is frozen solid for 10 months of the year. Other snags included the fact that the runway had to be cleared for take-offs and landings for four hours every day. In addition, all the equipment, fuel and operators had to be brought from mainland Norway.
Avinor picked four Hamm DV 90 OV tandem rollers to compact the runway’s polymer-modified asphalt. Hans-Peter Ackermann, product development manager at Hamm AG, explains why.
“Under these conditions, both speed and quality were paramount,” Ackermann says. “Asphalt is poured at 160 degrees Celsius and can be compacted down to 100 degrees Celsius. In an arctic environment – where the temperatures are low even in summer and high winds are common – the temperature window is short, so the faster the compacting rollers work, the better. With the oscillatory compaction system, the DV 90 rollers, which we launched in 2004, are in a high-speed class of their own.”
Dynamic compactionincreases a roller’s efficiency. The traditional way is through vibration. A rotary vibrator generates powerful vertical impacts into the road surface as the roller moves along. These impacts greatly increase the compaction rate.
However, there are places where vibration is a concern, due to sensitive surroundings or other special circumstances. To replace vibration, Hamm developed an oscillatory system, which works with two synchron-ously rotating weights in the drum. These create shearing forces directed forwards and backwards on the road surface, rather than up and down. “The oscillatory system cuts out 90 percent of the vibration while enhancing the compaction rate and the quality of the work,” Ackermann explains. “You could say that Hamm puts ‘good vibes’ into compacting.”
The DV 90 rollers compacted 30,000 tonnes of asphalt on the runway in three weeks, working two 10-hour shifts each day. The other road-making equipment for the job – a cold-milling machine, a spreader and two pavers – was supplied by Wirtgen Norway, the Norwegian subsidiary of the Wirtgen Group, Hamm’s parent company.
Hamm’s oscillatory technology was also decisive in the choice of a Hamm DV 90 roller for compaction work on the world’s tallest bridge, the Millau viaduct over the Tarn Valley in France. Completed in 2004 at a cost of 400 million euros, this striking construction eliminates the holiday-season traffic jams for which the town of Millau used to be renowned. The bridge’s total length is 2,460 metres, the road surface is 270 metres above the valley floor, and the highest pillar is 343 metres tall. For comparison, the Eiffel Tower measures 300 metres, or 320 metres if you include the aerial on top.
At Millau, as at Longyearbyen, speed was important, because strong winds high above the valley cooled the asphalt faster than when building on solid ground. Compaction had to be of the highest quality, to ensure a leak-proof asphalt layer and prevent corrosion of the structural steel elements under it.
“The main contractor for the bridge initially speci-fied static compaction for the two 11-metre-wide roadways, fearing that vibrations would weaken the structure,” Ackermann says. “We suggested that they should nevertheless consider dynamic compaction, using non-aggressive oscillation technology, which is rapid yet gentle. Test runs with a DV roller in the neighbouring town of Montpellier convinced them that our system was safe, and the specifications were changed to allow oscillatory compaction.” The asphalt, a special grade with high polymer content, was laid in record time. In three days 25 trucks moved 9,500 tonnes from two mixing plants to the bridge. The DV 90 was the only machine at the site to use oscillatory technology to compact the surface.
Hamm’s DV seriesincludes the DV 90 (nine tonnes), the DV 70 (seven tonnes) and the DV 40 (four tonnes). Apart from their oscillatory technology, these rollers share a number of ultra-modern features that have won acclaim from construction industry professionals.
-
A steer-by-wire system, including SKF’s steering unit in the ADD series. This system provides greater operator comfort and better steering properties and affords the designer more freedom to develop optimum cabin ergonomics.
-
A swivelling operator’s seat. The seat automatically turns when the operator reverses the machine, so that he always faces forward, whichever direction the machine is moving.
-
A new concept in chassis design. The glass-sided, air-conditioned cabin can be laterally offset up to 30 centimetres to either side, and within the cabin the seat can shift sideways, to enable the operator a constant, unobstructed view of the drums, sprink-lers and edge work.
-
The Hammtronic electronic machine management system. This monitors and controls all important engine and vehicle functions, ensuring optimum compaction and maximum productivity, quality and service life. It also prevents drum spin, enables grading on steep inclines and lowers fuel consumption by 30 to 40 percent.
-
Individual frequency and amplitude control for vibration and oscillation of front and rear drums.
“Sophisticated” is not a term generally applied to road compactors. Yet with a guidance system modelled on that of the latest jet aircraft, Hamm’s DV rollers are set to accomplish further remarkable achievements in road construction.
Steamrollers without steam
Hamm AG’s founders, the Hamm brothers, started making agricultural machinery in Tirschenreuth, in northern Bavaria, Germany, in 1878. “Hamm’s reputation for innovation started in 1911, when they built their first road roller,” says Gottfried Beer, Hamm’s marketing director. “It had a diesel engine, a real novelty at that time, and we have used only diesel power ever since. We see ourselves as the technological leaders of our industry, and we intend to stay ahead.”
The company, part of the Wirtgen Group since 1999, launched several trend setting developments over the years, including the bogie-steered tandem roller in 1932, the first roller with pneumatic tyres in 1960 and oscillation technology in the 1980s. Today, Hamm offers a complete range of rollers, from 1.5 to 28 tonnes.
With a new 15-million-euro plant, the company boosted production from 1,250 units in 1999 to 2,450 units in 2004, 3,600 in 2005 and 5,000 in 2006. The Wirtgen Group’s network of offices in 60 countries opens many doors for Hamm equipment. With 600 employees, the company is the biggest employer in the Tirschenreuth area.