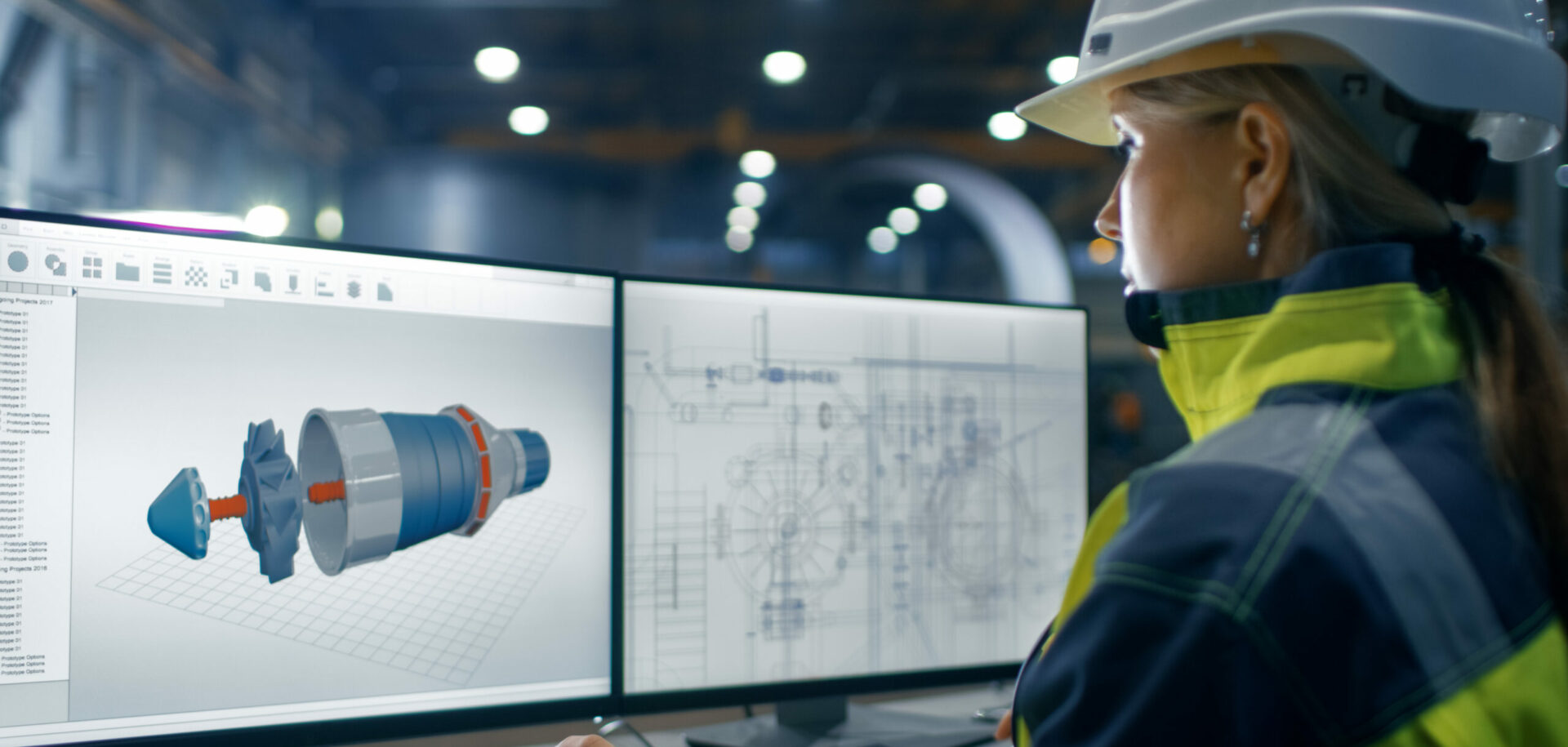
Green innovations at SKF supporting the automotive industry
With its commitment to sustainability throughout its own organization, SKF has a wealth of technical expertise in green solutions. This knowledge is being fully exploited for the automotive industry, where SKF is a strong partner, developing innovative products and services aimed at reducing carbon emissions.
Technology
The automotive industry is experiencing dramatic changes, particularly in relation to the technology shifts towards more envir-onmentally friendly mobility concepts that include, for example, hybrid and full electric vehicles. Against the backdrop of general global market pressures and opportunities, the industry needs to adopt sustainable solutions while maintaining cost-competitiveness, to meet its environmental goals.
Currently, the average CO2 emissions are 153.5 g/km (8.7 oz/mi), with a target to reduce this to 130 g/km (7.4 oz/mile) by 2015 in Europe. China has implemented the Euro legislation and has put Euro 4 as target for 2015. The U.S., with Barack Obama as president, is increasing the pressure to reduce the carbon emission targets faster than set before. Automotive companies and their suppliers are expected to invest heavily in technologies aimed at reducing fuel consumption and CO2 emissions.
As a major supplier to the automotive industry, SKF has taken heed of the global automotive marketplace and its sustainability needs and has focused its product developments in a number of key areas. Now, SKF has new products and services that are available for use on current and new vehicle platforms. Product developments include the low-friction wheel hub bearing unit, called X-Tracker, the SKF Turbocharger Ball Bearing Unit, SKF Rotor Positioning Bearing and sensor-bearing units for electric motors.
LOW-FRICTION WHEEL BEARINGS
SKF has developed a complement to its range of wheel bearings to respond to the market trend for all car segments to reduce friction and weight. The aim of the development program was to offer better performances in wheel bearings at an affordable price. The result, SKF’s latest generation of wheel hub units, the X-Tracker, is a low-friction design that offers improved frictional behavior, obtained through optimized internal geometry, optimized grease quantity and superior raceway finishing/topography, coupled with a low-drag seal. The unit has a cassette seal with optimized seal lip contact forces and with normal and/or heavy-duty hub bearing unit application alternatives.
Simulation and thorough tests carried out at SKF indicate that this product may bring a 25% reduction in rolling resistance compared with SKF’s existing, already-efficient designs and could contribute up to 1.3 g/km (0.07 oz/mi) of CO2 emission reduction, coupled with a robust unit that offers long operational life.
TURBOCHARGERS
Turbochargers have become indispensable tools in the effort to cut fuel consumption and have an impact on overall engine performance. SKF has developed a new compact ball bearing unit that offers lower friction and higher engine efficiency for car and truck applications. The bearing unit design is a double row super-precision ball bearing, rather than a conventional plain bearing, thus lowering friction and in turn contributing to lower fuel consumption and emissions by up to 2%.This performance is achieved through lower friction and higher running accuracy than with conventional plain bearing units. At low speeds, turbo lag is also reduced.
The SKF Turbocharger Ball Bearing Unit for the turbocharger incorporates ceramic balls that can function at high temperatures and under poor lubrication conditions while generating lower centrifugal loads at high speeds. With the ball bearing units, less oil is required, offering optimum clean combustion. The unit uses advanced technologies and materials such as aerospace steel, ceramic balls, reinforced steel and polymer cage design. The low-weight ceramic balls also guard against engine oil contamination. The design offers low noise performance and improved running accuracy and both an integrated damper function and an anti-rotation feature.
SKF Turbocharger Ball Bearing Units also have few components, thus enabling easy assembly and high mounting precision and reducing assembly time and costs. The unit is an important development, as it offers SKF the ability to efficiently support a number of other emerging products and applications related to the next-generation internal combustion engines. These include flywheel technology for energy recovery systems, waste heat recovery systems for higher engine efficiency and turbo-compounding applications.
STOP-START SYSTEMS
In partnership with the Valeo Group in France, SKF has developed the SKF Rotor Positioning Bearing as a vital part in the new generation of StARS starter alternators and now their second generation i-StARS. The StARS was developed for use in small hybrid cars, such as Smart, Citroen C2 and C3 and Daimler Class A. Now the PSA Group has launched a new diesel engine family named e-HDi that will be equipped with i-StARS.
The StARS solutions have a dual function – as an alternator and as a starter motor.
The SKF Rotor Positioning Bearing in the Valeo StARS and i-StARS alternators allows the engine to function exclusively when the vehicle is in motion. StARS automatically stops the engine when the vehicle is traveling at less than 4 mph, 5 mph for i-StARS, and starts it again as soon as the car is put in gear (for manual cars) or when the brake pedal is released (in automatics). The result is a significant reduction in the amount of CO2 produced and fuel consumed.
The SKF Rotor Positioning Bearing consists of a deep groove ball bearing with a special sensor attached to the inner ring. The bearing provides a powerful, accurate, repeatable and durable magnetic field, able to function under severe running conditions, including high temperatures and speeds. The magnetic field makes it possible to receive data on the speed and positioning of the shaft, making the reversibility of the electric machine possible as well.
The StARS eliminates the consumption of fuel and the production of noise and exhaust fumes when the vehicle is stationary – which can be 30% of the time when driving in very dense urban areas. It provides a silent start for the car when the alternator is activated electronically. It is easy to install in conventional alternators. The system is compatible with the electrical systems of modern cars.
Designed to support other technical approaches to stop-start systems in micro hybrid and mild hybrid applications is the SKF Commutation Sensor-Bearing Unit. This unit has been developed to meet market requirements for an accurate and repeatable permanent magnet electric motor commutation position measurement. Its particular benefits are ease of integration and tuning to a customer’s application, in a robust and compact design that can sit close to the electric motor without being affected by the surrounding magnetic fields.
ELECTRIC POWER STEERING
In 2009, Electric Power Steering, EPS, represented 22% of the global steering systems market and is set to rise to 30% by 2014 as hybrid and electric vehicles markets increase. The prospect of eliminating many mechanical components such as the steering shaft, column, gear reduction mechanism, etc. holds several advantages, such as simplified interior design and better space utilization, modular and robust steering mechanisms and improved safety.
SKF has developed a range of plug and play mechatronics solutions, including sensing products that are safe, reliable, robust, maintenance-free and cost-effective.
For road vehicles, the SKF Rotor Positioning Sensor-Bearing Unit combines the bearing function with absolute angular position sensing technology. Developed as an alternative to inductive revolvers, this is a robust, compact design that offers highly accurate position information at a low function cost within the application. This product type can be used to determine the rotor’s absolute angle position over 360°. The unit has a low current consumption (40mA) under 5V and is easily integrated into existing electronic control systems.
Thanks to the precise bearing geometry, the unit generates highly accurate sine and cosine signals, based on advanced magnetic technology. The unit supports the optimization of electric motor efficiency so reducing fuel consumption and CO2 emissions. Plus, the compact axial design offers designers greater flexibility as well as being easy to mount, so offering assembly cost and design savings.
VALIDATION SOFTWARE
Along with these technical developments, SKF has also created a modeling software system called the SKF Vehicle Environmental Performance Simulator (VEPS). As its name implies, the VEPS is a software tool that can translate bearing friction into real-life savings and carbon dioxide reduction for a complete vehicle. It can accurately model the actual internal bearing geometry and thus indicate what would be the effect of even the smallest modification on the carbon dioxide balance.
Thus, the VEPS can help optimize the bearing arrangements at various positions within the vehicle, such as the gearbox, at the design phase. It can identify which bearing positions are the most promising in terms of their savings potential. It can analyze the loading conditions on any bearing position and the corresponding impact on bearing friction torque and power loss as a contribution to the carbon dioxide of a vehicle.
Consequently, the software allows a solid correlation between bearings to be built and savings in fuel consumption/CO2 emissions to be achieved. This software is unique to SKF and may become a useful tool for the automotive industry in objectively assessing the positive contribution of an energy-
efficient component to the overall efficiency of a vehicle.
CONCLUSION
SKF has set out a clear roadmap in which the latest developments are another step towards the vision to continue to reduce friction losses even more substantially and always at an affordable cost. With its emphasis on knowledge engineering, SKF is developing the tools, products and services to support the automotive industry in its efforts to build vehicles that make their contribution to a sustainable future for us all.