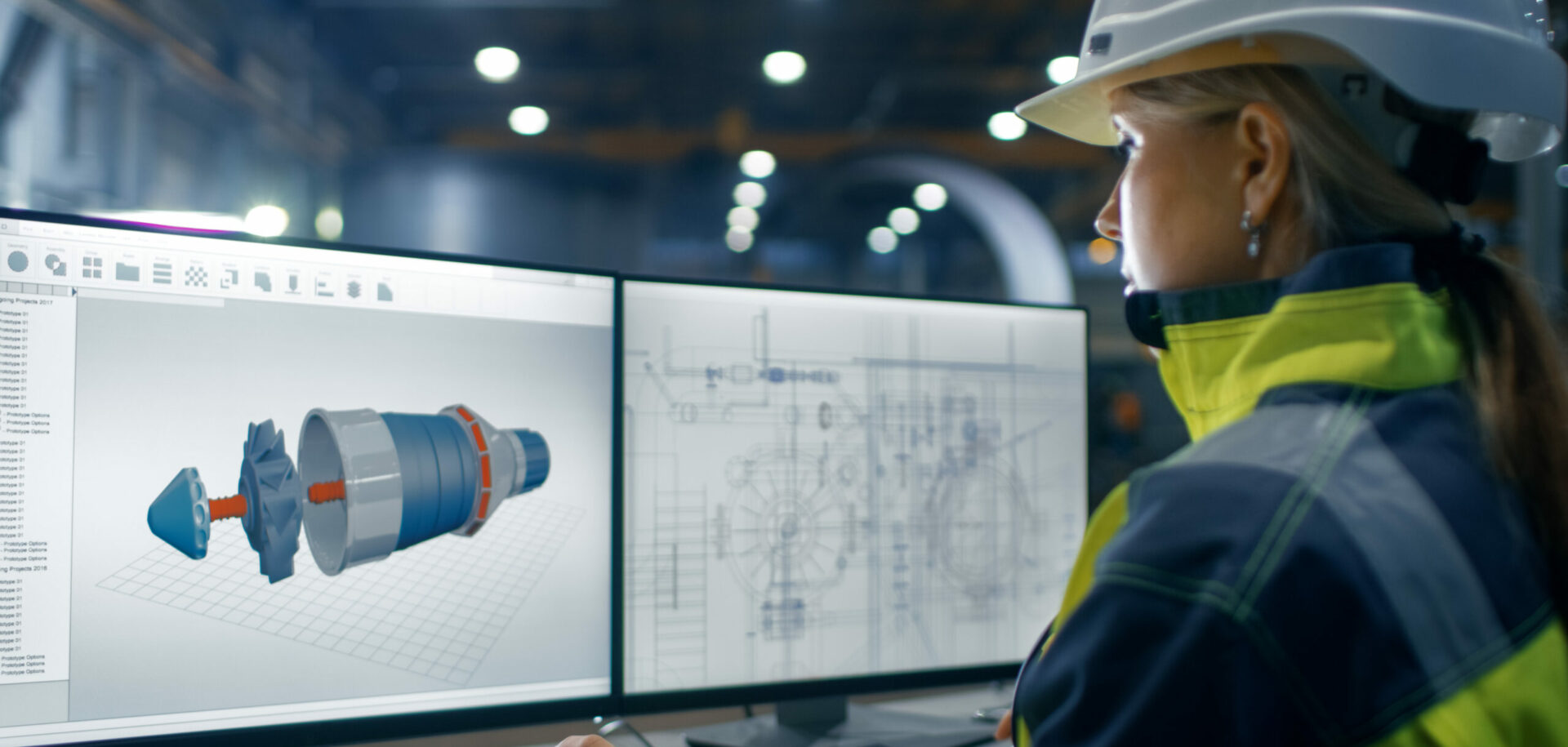
Helicopter application puts ceramic-coated spherical plain bearings through their paces
A spherical plain bearing that incorporates a ceramic-coated inner ring, used in helicopter main rotor applications, has undergone extensive testing to verify improvements in operating life and therefore lower maintenance costs.
A spherical plain bearing that incorporates a ceramic-coated inner ring, used in helicopter main rotor applications, has undergone extensive testing to verify improvements in operating life and therefore lower maintenance costs.
Ampep,a part of SKF Aero-space, is based at Clevedon, close to Bristol in the UK, and has been manufacturing self-lubricating plain bearings for more than 40 years. The Ampep XLNT ceramic-coated inner ring spherical plain bearing has been developed specifically to offer helicopter manufacturers and their customers a component with increased life that can reduce maintenance and downtime and offer lower life-cycle costs.
The spherical plain bearings are manufactured from stainless and corrosion-resistant steels and are self-lubricating and maintenance free. They are compact and have a very high load-carrying capacity to weight ratio and are used in primary and secondary flight-control systems. Typically these are a mono-ball type of construction. The inner ring is through-hardened and the spherical surface is ceramic-coated, which is applied using thermal spray technology. The outer ring is cold formed around the inner ring and has a woven PTFE/glass composite liner bonded to its inner spherical surface.
Wear of the PTFE liner surface is a function of pressure and sliding distance at the interface; each angular motion of operation under load causes a very small amount of wear in the liner. There are four different phases to the liner wear process.
1.Initially there is what is known as the bedding-in phase. This is where a PTFE transfer shear film (the lubricant) starts to be formed.
2.As the PTFE transfer film becomes more established, the wear rate is reduced.
3.Once fully established, the liner wears at a relatively uniform rate.
4.When the liner has worn significantly, the final phase of rapid wear takes place. The bearings should never be allowed to reach this condition on the aircraft, as flight safety is of paramount importance.
The Ampep XLNTis the latest in a line of developments in spherical plain bearings for aerospace applications aimed at giving extended operating life. The product had already undergone extensive in-house testing at Ampep’s Clevedon facility, which is recognized by all the major European helicopter manufacturers.
SKF believes that the Ampep XLNT can overcome the problem of the relative short operating life associated with existing products on the market.
One such applicationfor these bearings is to constantly change the pitch angle of helicopter main rotor blades as the main rotor rotates. The aerodynamics of the rotating blades and the articulation of the main rotor head provide the lift and manoeuvrability of the aircraft.
Some customers, interested in the potential of the Ampep XLNT ceramic-coated bearing, requested samples to perform their own bench tests and flight trials on prototype and existing helicopter models, which has since resulted in the Ampep XLNT bearing being equipped as standard.
Opportunities for this new bearing technology exist throughout the world, but initially North America has been identified as a potential market for the use of this product in helicopter flight-control systems.
After additional extensive bench testing, which returned promising results, one company, MD Helicopters Inc (MDHI), was interested in the possibility of using this product in the main rotor pitch control links on its Explorer helicopter. Currently the performance of the SKF solution is being monitored in the field.
The MD Exploreris a five-blade multipurpose, twin-engine helicopter. It features a fully articulated main rotor system, bearingless composite flexbeams and a rotor hub. Anti-torque control is provided by the patented NOTAR™ system that reduces pilot workload and external noise levels and significantly improves safety in confined areas. These helicopters are typically used for offshore/onshore passenger transport, emergency medical services and law enforcement missions.
The pitch control links continuously change the pitch angle of the main rotor blades with each revolution of the main rotor head. One end is connected to the swash plate, and the other end is connected to the blade pitch horn. This constant operation is a demanding application for spherical plain bearings; the typical operating life of the existing type of bearing used on the MD Explorer was quoted to be approximately 300 hours. With a number of these helicopters in service in the UK, SKF offered a service to monitor the performance of its products on some of these helicopters.
A number of companiesand organizations were involved in the monitoring project. Initially contact was made with Specialist Aviation Services, SAS, based at Staverton Airport in Gloucester. This company is a distributor for MDHI and also provides maintenance services for the helicopter operators. A presentation was made to SAS, and the possibility of a monitoring project was discussed. Following consultation with the operators SAS offered three of its aircraft for the programme. The proposal was made to the helicopter manufacturer, MD Helicopters Inc, which approved the project on the condition that one helicopter in particular, the Virgin HEMS London Air Ambulance, was included in the programme, as it was known to have a high attrition rate on the pitch control bearings.
With the project agreed,the bearings were manufactured and supplied to MDHI and then shipped to SAS for installation. In total four aircraft are being used for the monitoring programme. These are two high-utilization police helicopters that each fly approximately 100 hours/month, West Midlands Police and West Yorkshire Police, one combined role helicopter, Wiltshire Police and Air Ambulance and one high-cycle helicopter, Virgin HEMS London Air Ambulance, that accumulates approximately
40 hours/month, as it has an average flight time of only six minutes. These were to prove rigorous test environments for the bearings. By monitoring these four helicopters, the results would provide a good representation of bearing performance for the MD Explorer fleet.
The bearingsfor this application are classed as “on-condition” parts. That is to say there is no specific life imposed on the product, providing it is within the rejection criteria limits. SKF has recommended much tighter limits on its product in the interest of aircraft safety.
As part of the monitoring project, an SKF engineer witnessed the installation of the bearings into the main rotor pitch control links of these aircraft in June and July 2004. With the helicopters being subjected to routine periodic maintenance, the SKF engineer attended every 50-hour maintenance inspection of each aircraft. During these inspections the main rotor pitch control links are removed from the aircraft to enable the SKF engineer to measure and record the radial and axial play of the bearings in fixtures designed and manufactured by SKF.
For the West Midlands Policehelicopter, only the bearings located at the pitch horn end of the pitch control links were changed. However, as the pitch links are removed from the aircraft to perform the measurements, the play of the existing bearings installed in the swash plate end of the pitch control link are also measured and recorded, although the TSN (time since new) for these bearings is not precisely known.
For the West Yorkshire Police Helicopter and the Virgin HEMS London Air Ambulance, all five pitch control links (top and bottom) were fitted with the Ampep XLNT bearings.
The Wiltshire Police and Air Ambulance helicopter was equipped with a reference link.
The pitch control link of blade 1 was fitted with new bearings from the existing supplier at the same time as the Ampep XLNT bearings were installed in the pitch control links of blades 2, 3, 4 and 5. This enabled a direct comparison between the two bearing types to be made on this aircraft.
Since the startof the monitoring programme, a considerable number of flying hours have been accumulated:
-
West Midlands 627 hours
-
West Yorkshire 632 hours
-
Wiltshire 429 hours
-
Virgin HEMS 243 hours
With the excellent results gained to date and with very little play in the Ampep XLNT bearings, SKF has demonstrated that significant improvements are possible. In addition, it has also been possible to reduce the measurement frequency from every 50-hour maintenance inspection to every 100-hour maintenance inspection to minimize downtime of the aircraft.
The Ampep XLNTbearings will comfortably exceed 1,000 hours. Even with the recommended rejection criterion (tighter limits) the results indicate a 5x to 10x improvement in life when compared with the existing product. For any helicopter where life is an issue, the goal is to achieve a bearing life greater than the standard time between overhaul when the rotor head would need to be disassembled from the aircraft for other lifed components to be replaced.
The monitoring of these bearings will continue until the true service life has been established and the true life-cycle cost benefit to the operator can be quantified. (i.e., reduced downtime, reduced maintenance and bearing costs). The immediate benefits of using the Ampep XLNT bearing are already apparent from the results to date.
The participants
MDHI manufactures and sells a line of high-performance light twin- and single-engine helicopters, including the MD Explorer®, MD 600N®, MD 520N®, MD 530F® and MD 500E®. The company, which is based in Mesa, Arizona, has positioned itself as a niche provider, specializing in the law enforcement, air medical and corporate markets for which its products are particularly well suited.
Specialist Aviation Services is a company that offers integrated services related to equipping, maintaining and flying aircraft. Two of its subsidiaries are aimed at supporting medical and police emergency services.
Based in Devizes, the Wiltshire Constabulary has been operating a helicopter on a full-time basis since March 1990. The force works in conjunction with the Wiltshire Ambulance Service, and the MD 902 helicopter is staffed by a member of the force, a paramedic and a pilot supplied by Police Aviation Services. Wiltshire was the first UK operator of an MD 902.
Air support involves all aspects of emergency service work on a day-to-day basis. It currently flies approximately 900 hours a year and completes about 1,200 tasks annually. A reliable helicopter is crucial to the operation, and anything that can be done to increase the reliability, such as increasing the life of bearings, is welcomed.
Based at the Royal London Hospital, Whitechapel is the Virgin HEMS London Air Ambulance. It is the helicopter emergency medical service for London and covers some 1,800 square kilometres within London’s orbital motorway, the M25. It provides pre-hospital trauma care to more than 17.5 % of the UK population, and since its launch in 1989 the team has flown more than 14,500 missions. The service operates 365 days a year and is the only air ambulance in the UK that always carries a senior doctor and a paramedic trained specifically to treat patients who have suffered major injury as the result of an accident. Normally the helicopter can be airborne within two minutes of receiving a call and can reach anywhere within its area in 12 minutes. The service is partly funded by Britain’s National Health Service and Virgin, though it needs additional funds raised from the public to continue operation.
Based at Birmingham International Airport, the West Midlands Air Operations Unit provides a specialist support service 24 hours a day, 365 days a year. In 2000 it introduced its MD 902 Explorer into service. The MD 902 Explorer is fitted with some of the most sophisticated equipment and communications systems available.