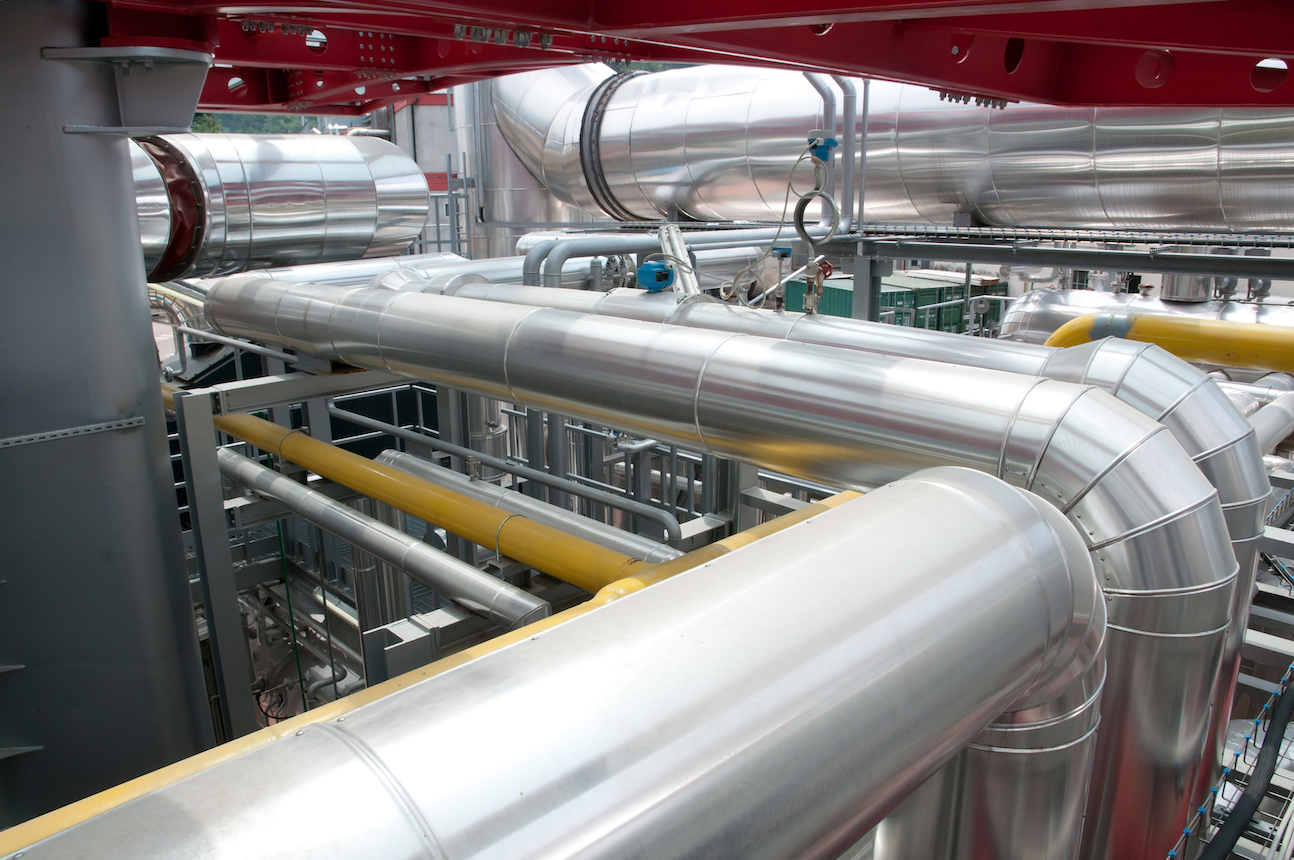
Homeward bound
Re-entry into the earth’s atmosphere is a dangerous phase of space flight. The European Space Agency’s IXV project is testing a new technological solution to reduce the risk.
One critical stage of space flight is when a spacecraft re-enters the earth’s atmosphere to land. Slowing down a vessel that is flying at some 27,000 kilometres per hour to a controlled landing speed is a challenge that requires the highest level of technological expertise, and it is a key issue for the European Space Agency’s new Intermediate eXperimental Vehicle (IXV), scheduled for launch in July 2014. The European Space Agency, or ESA, contracted Thales Alenia Space – Italy (TAS-I) to be the architect behind the IXV, and TAS-I has about 20 main subcontractors working on the project, including SABCA, Société Anonyme Belge de Constructions Aéronautiques. This Belgian aerospace company, a subsidiary of the Dassault Group, is producing the control systems for the IXV’s directional flaps in its factory in Haren, near Brussels. “In Europe, we have to acquire technological expertise regarding re-entry systems, so projects such as the IXV are essential in safeguarding our future European autonomy and independence in terms of space travel,” says SABCA Senior Project Manager Didier Verhoeven. “The experiments carried out during re-entry, and the expertise we will gain from these flights, will help consolidate our position as a major player in this strategic field.” The IXV, which is about the same size as a car (4.4x2x1.5 metres) and weighs about two tonnes, will be launched using a Vega rocket, the ESA’s small launcher. The IXV will perform a ballistic flight with a parabolic trajectory up to 415 kilometres in altitude; the critical phase will begin when the IXV returns to an altitude of 120 kilometres (at 7.7 kilometres per second). Re-entry will then be controlled to an altitude of 30 kilometres, at which time parachutes will open and the IXV will land in the Pacific Ocean. The flight will last a total of 100 minutes. The two flaps that steer the IXV during re-entry are individually controlled using two electro-mechanical actuators that can each deliver a force of 35 kilonewtons. During re-entry the flaps adjust the pitch and roll of the IXV by, respectively, symmetric and asymmetric deflection. The maximum temperature in the flap area is about 1,600 degrees Celsius. “The actuators we are supplying were originally an off-the-shelf system that we adapted for the IXV,” Verhoeven says. “Given the limited budget, we had to reuse as many existing components as possible, so we adapted the thrust vector control system we’d previously developed to drive the ZEFIRO nozzles on the Vega rocket for the IXV. In the past, when we worked on the Ariane 5 launcher, we used hydraulics for the actuators. But following the general trend in aerospace, we’ve moved to using electromechanical actuators for the VEGA and the IXV.” The IXV flaps move at a speed of 15 degrees per second. The onboard computer sends position information to SABCA’s electronics, and microprocessors inside drive the motor, determining the position and speed of the actuators. Two 60-volt battery modules in series supply 120 volts DC of power, with converters to make the electricity AC. One of the main challenges will be providing the reliability of the static braking system that holds the flaps steady until re-entry. The springs holding it must be able to withstand the huge vibration levels generated during launch. To release the brake, a 28-volt electromagnet compresses the springs to release it and enable the motor to run. “One concern is that there could be a cold-welding phenomenon caused by the vibrations in the vacuum that would prevent the brake from being released,” says Verhoeven. “But we’ve used a special vacuum-compatible Braycote grease to lubricate the brake. We are confident, having tested more than 1,000 cycles of brake engagement and release in vacuum conditions without a single incidence of cold welding. Moreover, additional tests will be performed during the qualification campaign.” SABCA is scheduled to deliver a prototype flight model by March 2013. Qualification tests in Italy began in October 2012, and in February 2014 the IXV will be shipped to the launch base in Kourou in French Guiana. “We are just one of about 20 main TAS-I subcontractors, and if any one of us fails to meet our deadline, the whole project will be held up,” says Verhoeven. “But we are confident and also excited to be part of the IXV, which is the first step on a very long road, with the long-term goal of a European space mission launching people into space and bringing them safely back home.”