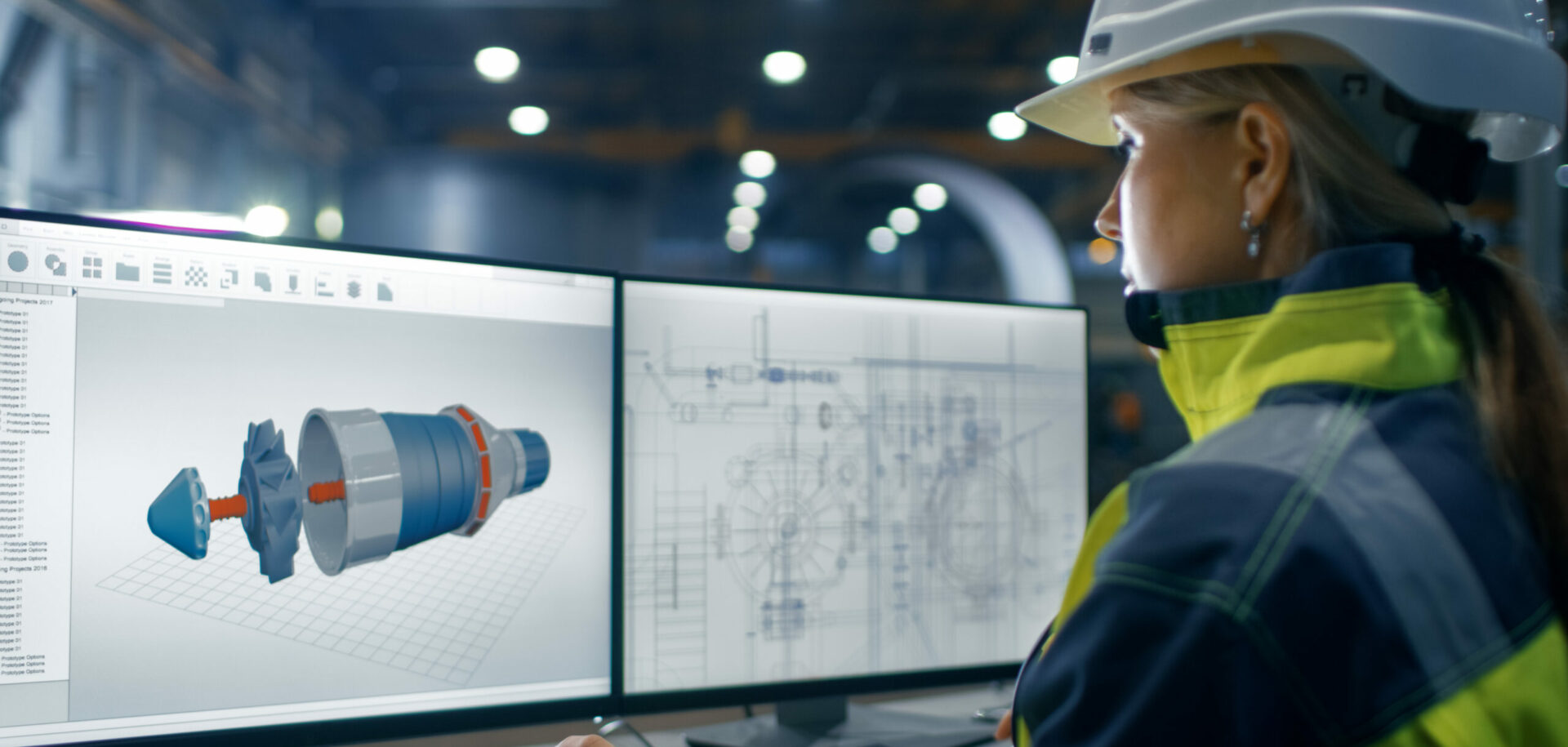
Improved grease-life model for Y-bearings
Improvements in bearing, seal and lubrication technology, combined with the latest grease-life calculation methods, result in a substantial improvement in grease life for SKF Y-bearings.When application engineers talk about a bearing being “sealed and greased for life” or “maintenance free,” there is still a calculated life of the bearing. That life is dependent on factors such as carrying capacity, axial and radial loads, speeds, contaminants, e.g., dirt and moisture, operating temperature and vibrations and, of course, grease life. Many of those factors are interrelated.
Improvements in bearing, seal and lubrication technology, combined with the latest grease-life calculation methods, result in a substantial improvement in grease life for SKF Y-bearings.When application engineers talk about a bearing being “sealed and greased for life” or “maintenance free,” there is still a calculated life of the bearing. That life is dependent on factors such as carrying capacity, axial and radial loads, speeds, contaminants, e.g., dirt and moisture, operating temperature and vibrations and, of course, grease life. Many of those factors are interrelated.
For example, excessive radial or axial loads will eventually lead to damage of the rolling elements and raceways, but in the meantime, those excessive loads will increase the heat generated in the bearing to substantially decrease grease life and therefore cause premature bearing failure. Grease life is one of the key parameters to long bearing service life.
Because grease life plays such an important role in bearing life calculations for “maintenance-free” applications, particularly for Y-bearings, SKF engineers conducted a study of the interrelated factors that have an effect on grease life for these bearings. In their study they looked at improvements in bearing design, surface finish of the balls and raceways, seal design and the composition of the grease and its additives.
To understand the results of their study, let’s take a look at a Y-bearing unit and its components.
About Y-bearings
Y-bearings are basically sealed 62 Series deep groove ball bearings with a convex sphered outside diameter and an extended inner ring on one or both sides ( .1). Instead of having an interference fit to the shaft as most bearings traditionally have, Y-bearings are fixed to the shaft with set screws, eccentric locking collars or the patented sleeve technology of SKF Concentra.
The bearings have a single-lip contact seal, “M-seal,” as standard. Bearings for air-handling applications also have a flinger in combination as standard ( .2). The seal is designed to keep grease in the bearing and contaminants out of the bearing cavity, while the flinger is designed to protect the seal lip by preventing debris particles from reaching the seal.
Within this well-sealed environment, the internal design of an SKF Y-bearing has been refined so that it generates a minimum amount of heat. In addition, the internal geometry and surface finish of all contact surfaces, including the molded
polyamide cage, have been designed to maximize the effectiveness of the lubricant.
As a result of these internal and external improvements, SKF Y-bearings are able to realize the advancements in grease technology and take advantage of the benefits that a factory grease fill can provide.
Because Y-bearing units are “greased and sealed for life,” they provide the following advantages:
- Bearings are filled with grease that has known performance characteristics;
- Grease is applied in a controlled environment to provide optimum cleanliness; and
- Grease fill is optimized, virtually eliminating the chance of overfilling.
Relubrication intervals
The grease relubrication interval diagrams created decades ago and based on then-current manufacturing capabilities remain unchanged today. As a result, these diagrams often promote very conservative practices – practices that can result in over-greasing, waste and premature bearing failure. While conservative practices are warranted in harsh environments, experience shows that bearings used in less demanding applications – from a speed, temperature and load point of view – can operate for extended periods without relubrication. Examples of this can be found in applications ranging from small electric motors in home appliances to the wheel-bearing units used in today’s cars and trucks.
Many Y-bearing applications are characterized by ambient temperatures, low to moderate shaft speeds, relatively low loads and, often, clean, filtered air. Furthermore, experience has shown that seal failure and high bearing-operating temperatures are common for Y-bearings, due to over-filling during relubrication. To take advantage of advancements in bearing, seal and grease technology and at the same time account for current maintenance practices, SKF developed a new grease-life calculation method for Y-bearings.
The new diagram
The new Y-bearing grease-life diagram represents an L10 life (90% survival) and is valid for Y-bearings with a bore diameter up to 100 mm, lubricated-for-life with a standard Y-bearing grease from SKF Y-bearing factories, equipped with seals and flingers, and operating conditions as explained above ( diagram 1).
Parameters such as operating temperatures and the factor n x dm, which comprises the rotational speed and the bearing mean diameter, were taken into account when developing the diagram. The diagram also considers the positive contribution of the polymeric cage and the superior seals with flingers. As a result, longer lives can be estimated, up to 100,000 hours, provided that the grease life is not affected by other external factors. Reduction factors must be applied for heavy Y-bearing loads (i.e., for C/P
Diagram constraints
The grease-life diagram is plotted for operating temperature against number of hours of operation for different n x dm values. The curves show the difference in grease response over various operating temperatures. Over the temperature range 55° C (131° F) to 100° C (212° F), the grease life for the selected Y-bearing grease shows an exponential adjustment with temperature.
In that range, the life is reduced by around a factor of two when the temperature is increased by 15° C (59° F). The grease-life expectancy is held constant for temperatures between 40° C (104° F) and 55° C (131° F), due to the rule of doubling grease life only once for operating temperatures more than 15° C (59° F) below the grease’s reference temperature (70° C [158° F]).
No extrapolation is permitted for temperatures below 40° C (104° F), due to reduced oil separation and subsequent oil starvation at these lower temperatures, which cannot be quantified.
The validity of the Y-bearing grease-life diagram has been confirmed through grease-life testing in SKF’s ROF test rig at its Engineering & Research Center in Nieuwegein, the Netherlands. In test rigs, conditions are chosen so that the failure types are representative of typical grease failure modes in the field.
Overall, the new diagram is a useful tool to indicate if maintenance free Y-bearings are suitable and feasible for a particular application.