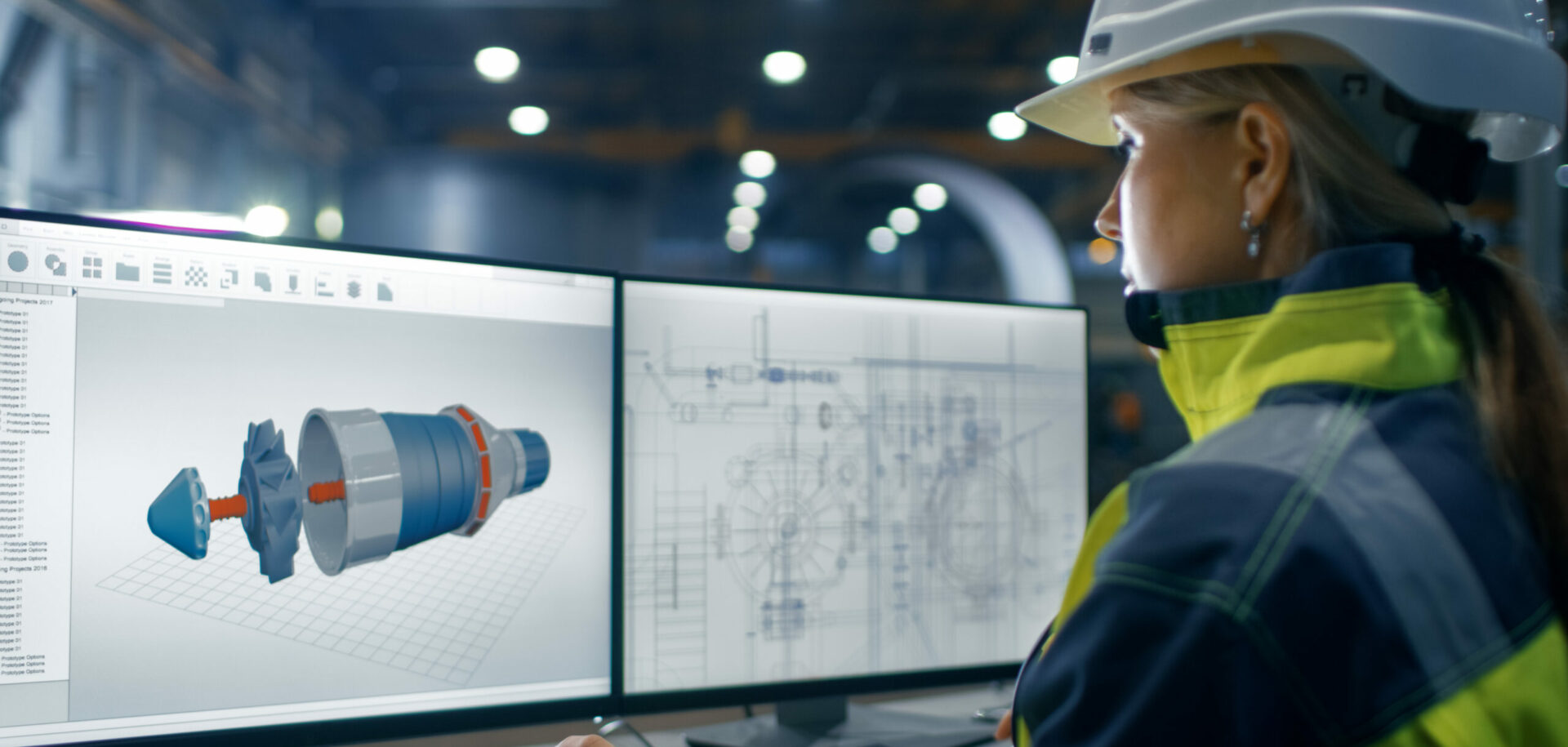
Cuscinetti per il risparmio energetico
Alla SKF, un’intensa attività di sviluppo ha dato vita a una nuova famiglia di cuscinetti, capaci di consumare molta meno energia dei tipi tradizionali. La produzione di questi nuovi cuscinetti ad alta efficienza energetica è iniziata nel 2007.
Alla SKF, un’intensa attività di sviluppo ha dato vita a una nuova famiglia di cuscinetti, capaci di consumare molta meno energia dei tipi tradizionali. La produzione di questi nuovi cuscinetti ad alta efficienza energetica è iniziata nel 2007.
Con il contributo di LIFE, lo strumento finanziario per l’ambiente nell’Unione Europea.
Nell’intento di crearenuove soluzioni tecniche per l’industria in grado di dare un contributo positivo alla riduzione dei consumi di energia, è stato deciso di perfezionare due delle tipologie più comuni di cuscinetti, quelli radiali a sfere e quelli a rulli conici. Nella loro nuova esecuzione tali cuscinetti consentono in molte applicazioni risparmi di energia dell’ordine di quasi un terzo (fig. 1). Nello stesso tempo gli ingegneri SKF si erano imposti l’obiettivo di non compromettere la durata di esercizio e la capacità di carico offerta dai tipi tradizionali.
La realizzazione dei nuovi cuscinetti è stata possibile grazie all’eccezionale esperienza della SKF nella progettazione e nelle tecniche di modellazione e alle profonde conoscenze dei suoi ingegneri nell’applicazione della metodologia FEM, delle simulazioni dinamiche dei cuscinetti (SKF BEAST) e delle simulazioni del momento d’attrito (SKF BFree). I risultati ottenuti sono stati ripetutamente verificati tramite numerose prove in vari laboratori in Francia, Germania e Italia, come pure presso l’Engineering Research Centre di Nieuwegein, in Olanda.
Cuscinetti a rulli conici ad alta efficienza energetica
Nel caso del moltiplicatore di una turbina eolica i nuovi cuscinetti a rulli conici SKF consumano un 30 % in meno di energia rispetto ai tipi normali (fig. 2). L’industria eolica è infatti uno dei settori sensibili ai consumi energetici verso i quali questi tipi di cuscinetti sono indirizzati, unitamente ai settori dei riduttori industriali pesanti, delle applicazioni ferroviarie, delle unità a ingranaggi per la movimentazione dei materiali, degli estrusori e delle navi. Normalmente in tutti questi settori si devono trasmettere carichi elevati e spesso i cuscinetti hanno un diametro esterno che va da 200 a 600 mm. Come regola generale, maggiore è il diametro maggiori sono i possibili risparmi di energia, che possono arrivare al 50 %.
Aspetti della progettazione
I miglioramenti apportati ai cuscinetti riguardano la geometria delle flange, la riduzione degli scarichi e l’allargamento della pista dell’anello interno. Sono stati previsti una topografia speciale per i rulli e un profilo speciale per le piste; la rugosità superficiale delle piste e delle flange è stata ridotta. Caratteristica è l’adozione di una gabbia speciale, che si presenta con un diametro del foro ridotto e che è costruita in PEEK (poli-eter-eter-chetone) o per esigenze speciali, in lamiera d’acciaio.
Il PEEK è un materiale eccezionale, in quanto è facilmente stampabile e ha un’eccellente stabilità dimensionale e di forma. La sua stabilità termica è particolarmente buona e consente alla gabbia di operare in modo continuativo da temperature sotto zero fino a 160 °C, con picchi fino a 200 °C.
Un ulteriore contributo al risparmio di energia è dato dalla riduzione del numero dei rulli. Nel caso del tipo 32230, con meno rulli e con una gabbia in PEEK anziché in lamiera, si riduce la massa rotante di circa il 10 %, il che comporta una minore richiesta di energia per il movimento (fig. 3). Alla maggiore leggerezza del cuscinetto si aggiunge la minore energia necessaria per spostare i corpi volventi. Dato che le parti in movimento presentano un’inerzia minore, si riduce l’eventualità di slittamenti e strisciamenti, a tutto vantaggio delle prestazioni e della durata.
Vantaggi applicativi
Ai progettisti viene offerta la possibilità o di scegliere motori e riduttori con meno esigenze energetiche oppure di farli funzionare a velocità più elevate a pari prestazioni, incrementando così il rendimento di macchine e impianti. Un minore attrito comporta minori temperature di lavoro, il che a sua volta migliora la separazione delle superfici nei contatti volventi attraverso una migliore formazione del film lubrificante e inoltre prolunga la durata del lubrificante stesso.
Nelle turbine eoliche, che sono il principale settore di applicazione, l’utilizzo di cuscinetti a rulli conici ad alta efficienza energetica nei moltiplicatori e nei generatori è interessante dal punto di vista della potenza sviluppabile. Se in tutto il mondo i cuscinetti dei moltiplicatori delle turbine fossero sostituiti con tipi a rulli ad alta efficienza energetica, si potrebbero generare 770 milioni di kWh in più all’anno, il che equivarrebbe al consumo di energia di circa un milione di abitazioni in Europa in un mese. Dato che hanno le normali dimensioni ISO, i nuovi cuscinetti a rulli conici si possono facilmente installare sulle applicazioni esistenti. La loro introduzione può far risparmiare consistenti quantità di energia anche in tutti gli altri settori industriali, nelle cartiere, in siderurgia, nelle miniere, nella lavorazione del greggio, nell’industria alimentare e tessile e negli impianti di trattamento delle acque.
Cuscinetti radiali a sfere ad alta efficienza energetica
I cuscinetti radiali a una corona di sfere possono reggere carichi radiali e assiali a varie velocità di rotazione e sono i più comunemente usati.
Nel caso cuscinetti radiali a sfere di nuova esecuzione, l’attenzione è stata posta nello sviluppo di prodotti destinati ad applicazioni medio-leggere, quali i motori elettrici per azionare pompe, compressori, ventilatori e convogliatori. Per il momento sono stati presentati i tipi con schermi metallici e diametro esterno da 52 a 130 mm.
Aspetti della progettazione
Per ottenere risparmi di energia non inferiori al 30 %, gli ingegneri SKF hanno ottimizzato la geometria interna, utilizzato una nuova gabbia in polimero e scelto un grasso con basso attrito (fig. 6). Con questi interventi combinati, finalizzati alle particolari condizioni di lavoro, hanno ridotto le perdite per attrito del 30 % come minimo e hanno migliorato la durata di esercizio (fig. 4).
Vantaggi applicativi
I vantaggi per gli utilizzatori finali sono minori consumi di energia, minori costi di utilizzo e più lunghe durate di esercizio; in più si possono progettare macchine caratterizzate da un maggiore rendimento.
I vantaggi applicativi si possono vedere su due livelli.
Ai costruttori di motori l’impiego di cuscinetti radiali a sfere più efficienti consente la realizzazione di motori con più alto rendimento, tenendo presente che in Europa e negli USA i regolamenti in proposito stanno diventando sempre più restrittivi.
Per gli utilizzatori di motori, i vantaggi diretti sono naturalmente un minore consumo di energia e quindi un minore costo totale di gestione e utilizzo. In un periodo di 10-15 anni, a seconda delle dimensioni del motore, il costo totale di gestione è costituito per il 95-99 % dalla bolletta energetica (il rimanente sono i costi di acquisto e di manutenzione, fig. 5). Inoltre lo sviluppo dei cuscinetti radiali a sfere ad alta efficienza energetica dimostra che, con un migliore uso del lubrificante e con minori temperature di lavoro, si possono ottenere maggiori durate. Tutto ciò rende i nuovi cuscinetti radiali a sfere ancora più interessanti in quanto conferiscono a loro volta maggiore durata alle macchine stesse.
Le macchine azionate da motori, quali le pompe, i compressori e i ventilatori, sono responsabili di circa il 16 % dell’energia consumata nelle applicazioni industriali nei soli Stati Uniti; in molti dei paesi più industrializzati la situazione è analoga. Con i costi dell’energia in continuo aumento ogni risparmio è il benvenuto. Anche se in un motore elettrico i cuscinetti rappresentano solo lo 0,6 % del consumo di energia stimato, il miglioramento delle loro prestazioni può pur sempre dare un significativo contributo ai risparmi di energia, (figg. 7e 8).
Se negli USA e in Europa si usassero i nuovi cuscinetti radiali a sfere SKF ad alta efficienza energetica in tutti i motori elettrici industriali, supponendo una riduzione minima del 30 % dei consumi di energia, il risparmio potenziale di energia sarebbe pari a 2,46 miliardi di kWh all’anno. Questo equivarrebbe a 420.000 barili di petrolio, senza tenere conto dei milioni di altri motori in uso altrove ne mondo.
Grazie ai propri sforzi, la SKF ha adeguato i due principali tipi di cuscinetti alle moderne esigenze, con il vantaggio di offrire significative riduzioni nei consumi energetici e maggiori durate.