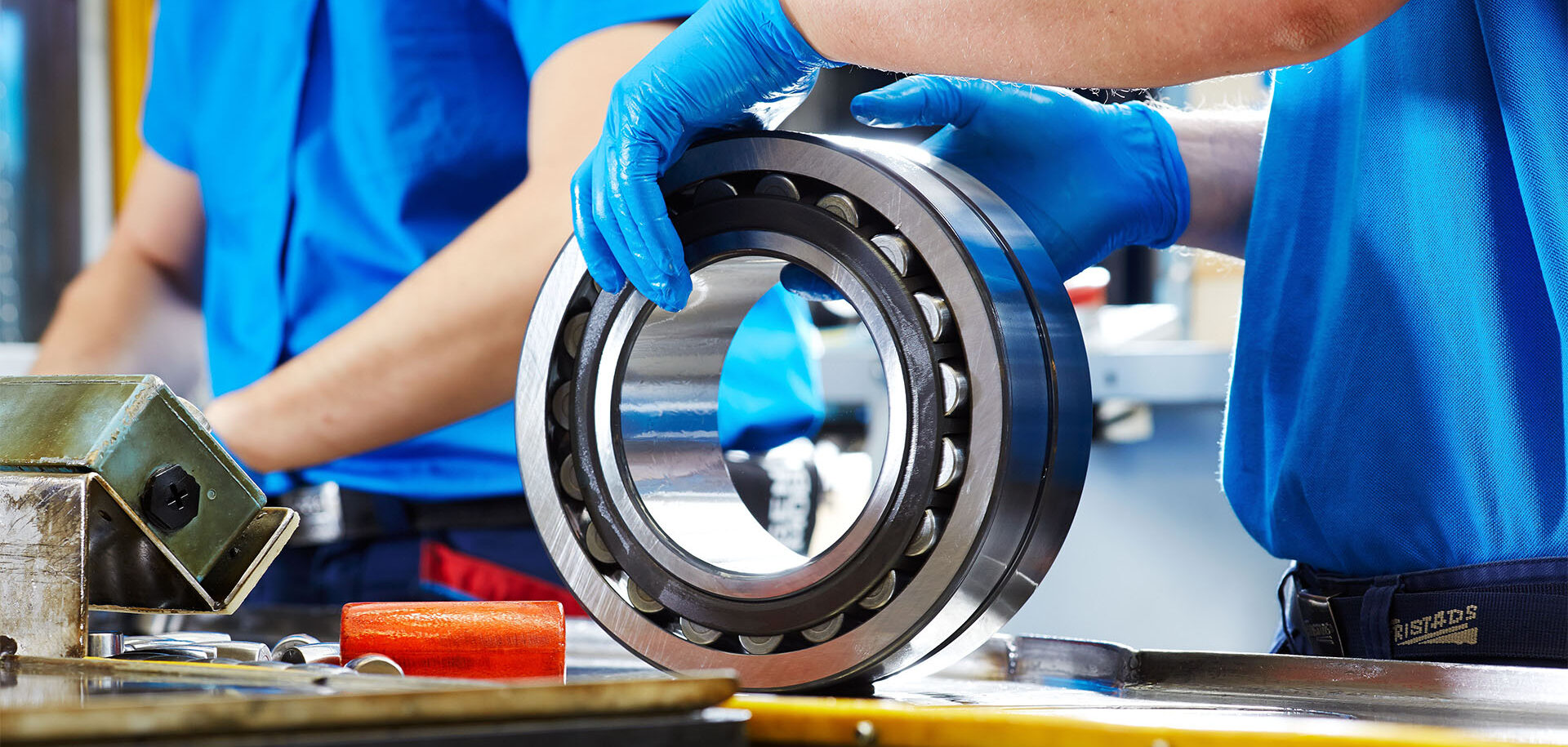
Lean e digital: il futuro dei processi produttivi SKF
Nel 2017, quando Ajay Naik si trasferì dall'India alla Svezia per dirigere lo stabilimento SKF di Göteborg, lo attendevano numerose sfide. Ma, insieme al suo team, le ha trasformate in successo.
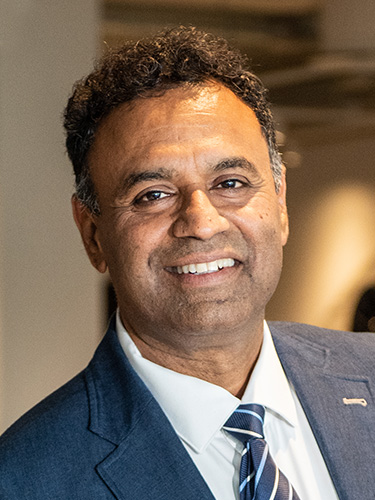
Nel 2017, nel bel mezzo di una riprogettazione dei sistemi informatici aziendali, lo stabilimento SKF di Göteborg registrava un’impennata senza precedenti della domanda globale. Nell’estate gli ordini si erano accumulati e le gravi carenze di personale imponevano la ricerca urgente di lavoratori temporanei.
“Non eravamo affatto preparati”, commenta Ajay Naik, managing director e country manager di SKF Sweden. “In condizioni normali riusciamo a far fronte a incrementi graduali della domanda, ma il mercato è cresciuto in modo vertiginoso proprio mentre stavamo affrontando problemi interni”.
Nei 30 anni passati a lavorare per SKF in India, Naik aveva maturato esperienza nel gestire le sfide legate ai processi di produzione. Al suo arrivo in Svezia questa gli è servita per nominare un crisis manager, un esperto di supply chain e istituire una “sala operativa” nel tentativo di stabilizzare la situazione. Alla fine del 2017, con il momento più critico ormai alle spalle, si apriva una fase di trasformazione che avrebbe consolidato lo stabilimento di Göteborg come leader globale in termini di prestazioni. Nel 2021 la European Organization for Quality (EOQ) ha conferito a Naik il premio European Quality Leader (EQL) per i risultati ottenuti.
Nel 2017, nel bel mezzo di una riprogettazione dei sistemi informatici aziendali, lo stabilimento SKF di Göteborg registrava un’impennata senza precedenti della domanda globale. Nell’estate gli ordini si erano accumulati e le gravi carenze di personale imponevano la ricerca urgente di lavoratori temporanei.
“Non eravamo affatto preparati”, commenta Ajay Naik, managing director e country manager di SKF Sweden. “In condizioni normali riusciamo a far fronte a incrementi graduali della domanda, ma il mercato è cresciuto in modo vertiginoso proprio mentre stavamo affrontando problemi interni”.
Nei 30 anni passati a lavorare per SKF in India, Naik aveva maturato esperienza nel gestire le sfide legate ai processi di produzione. Al suo arrivo in Svezia questa gli è servita per nominare un crisis manager, un esperto di supply chain e istituire una “sala operativa” nel tentativo di stabilizzare la situazione. Alla fine del 2017, con il momento più critico ormai alle spalle, si apriva una fase di trasformazione che avrebbe consolidato lo stabilimento di Göteborg come leader globale in termini di prestazioni. Nel 2021 la European Organization for Quality (EOQ) ha conferito a Naik il premio European Quality Leader (EQL) per i risultati ottenuti.
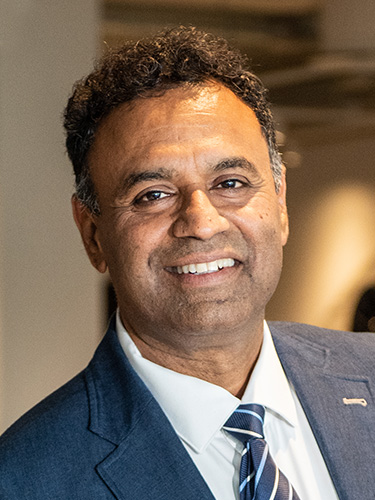
Le prime misure per la trasformazione
La prima fase della trasformazione è cominciata nel gennaio 2018 ed è proseguita fino all’estate del 2019, un periodo che Naik definisce “normalizzazione”. Mentre il sistema informatico era in fase di debug, nello stabilimento è stato introdotto un sistema manuale di supply chain. Sono state presentate iniziative per alleviare lo stress dei dipendenti. I manager hanno intensificato la loro presenza nelle linee di produzione. La comunicazione è stata migliorata ed è stato avviato un piano per ridurre in modo significativo gli sprechi.
Abbiamo detto che non useremo i colori per dipingere i nostri muri, ma che coloreremo il nostro mondo con il miglioramento
Ajay Naik, managing director e country manager di SKF Sweden.
“Volevamo diventare prevedibili e realmente affidabili”, dice Naik. “Avevamo inoltre capito che i nostri costi erano troppo elevati per permetterci di essere competitivi. Avremmo anche potuto superare la crisi, ma margini così esigui non avrebbero mai prodotto redditività”.
Nel giugno 2019 ha avuto inizio la fase di esecuzione. Naik ha organizzato seminari per formare il personale sulla riduzione dei costi inutili. Il management ha collaborato con i sindacati per organizzare la turnazione con criteri di flessibilità funzionali alle fasi di crescita e decrescita del ciclo economico. E per i ruoli resi obsoleti dall’automazione si è provveduto a riqualificare e formare il personale per le nuove competenze.
Adozione del metodo Kaizen
Naik ha introdotto la strategia Kaizen, un approccio pionieristico nato in Giappone, che prevede il coinvolgimento dei dipendenti, a tutti i livelli, per il miglioramento continuo del processo produttivo. Ogni mese, sindacati e dipendenti della fabbrica scelgono il miglior risultato ottenuto e lo affiggono sulle pareti dello stabilimento SKF di Göteborg. Sono già più di 5.000 da quando il metodo è stato adottato.
“Abbiamo detto che non useremo i colori per dipingere i nostri muri, ma che coloreremo il nostro mondo con il miglioramento”, dichiara Naik. “Lo facciamo per ogni parete, così abbiamo modo di vedere e apprezzare i contributi delle persone”.
I primi risultati
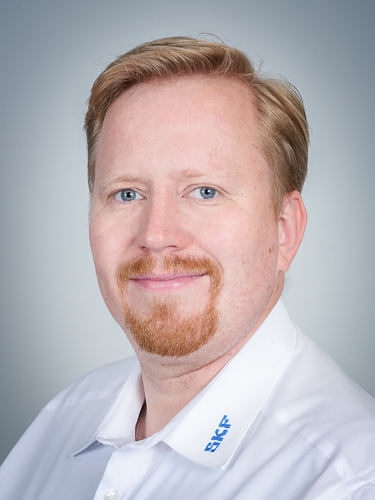
A dicembre 2020 i costi superflui erano stati tagliati e i margini operativi dell’impianto erano notevolmente migliorati. La European Organization for Quality ha conferito a Naik il premio EQL per “i risultati eccezionali ottenuti nel trasformare lo stabilimento SKF di Göteborg in uno dei tre più performanti d’Europa attraverso la sua leadership visibile e impegnata, unita a un team di lavoratori altamente coinvolti”.
Niki Homes, manager di SKF Future Factory, dice che il successo di Naik a Göteborg è ancora più ragguardevole se si pensa che lo stabilimento SKF è stato tra i primi a integrare una serie di nuove tecnologie.
“Naik ha fatto vari investimenti in canali world class manufacturing, uniti alle sfide di gestire le nuove tecnologie sia di digitalizzazione sia di automazione”, commenta. “La fabbrica di Göteborg ha imparato molto in fretta a padroneggiare le nuove tecnologie ed è aperta a ulteriori sviluppi, anche se a volte la strada è accidentata”.
I primi risultati
A dicembre 2020 i costi superflui erano stati tagliati e i margini operativi dell’impianto erano notevolmente migliorati. La European Organization for Quality ha conferito a Naik il premio EQL per “i risultati eccezionali ottenuti nel trasformare lo stabilimento SKF di Göteborg in uno dei tre più performanti d’Europa attraverso la sua leadership visibile e impegnata, unita a un team di lavoratori altamente coinvolti”.
Niki Homes, manager di SKF Future Factory, dice che il successo di Naik a Göteborg è ancora più ragguardevole se si pensa che lo stabilimento SKF è stato tra i primi a integrare una serie di nuove tecnologie.
“Naik ha fatto vari investimenti in canali world class manufacturing, uniti alle sfide di gestire le nuove tecnologie sia di digitalizzazione sia di automazione”, commenta. “La fabbrica di Göteborg ha imparato molto in fretta a padroneggiare le nuove tecnologie ed è aperta a ulteriori sviluppi, anche se a volte la strada è accidentata”.
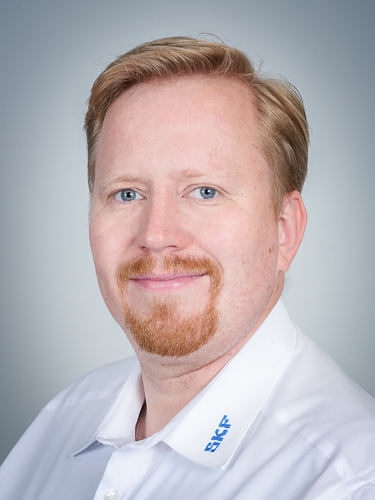
La trasformazione digitale di SKF nel mondo
Homes è responsabile di guidare la trasformazione digitale ispirata ai principi lean delle quasi 100 fabbriche SKF in tutto il mondo. I cambiamenti comportano l’integrazione di molte delle nuove tecnologie e dei processi sperimentati per la prima volta a Göteborg e in altre fabbriche leader nel mondo, al fine di ottenere risultati simili.
Al centro della trasformazione digitale c’è la spinta a trovare il giusto equilibrio tra tecnologia, processo e persone. Solo questo equilibrio permetterà a SKF di liberare il pieno potenziale dei dati per migliorare i suoi processi, come sostiene Homes. Ciò comporta una maggiore consapevolezza da parte di tutta l’azienda affinché tutti siano pronti ad accogliere il cambiamento, ottimizzando e standardizzando i processi e scegliendo la tecnologia più idonea a soddisfare le esigenze di SKF.
“Dopo aver definito le esigenze del business, il primo passo è individuare la tecnologia più adatta a noi”, precisa. “Fatto ciò, occorre implementarla per supportare i nostri processi e le persone che li eseguono”.
Componente chiave della tecnologia che sta rapidamente migliorando i processi SKF è l’infrastruttura iperconvergente o HCI, la quale permette ai team di far leva sui vantaggi sia della tecnologia cloud sia della potenza computazionale senza cloud (onsite). I calcoli necessari in tempo reale all’interno della fabbrica possono essere eseguiti immediatamente sul posto, permettendo allo stesso tempo l’esecuzione di compiti più complessi tramite il cloud, dove una maggiore potenza di calcolo è disponibile su richiesta.
Processo di rettifica migliorato
A titolo esemplificativo Homes cita la rettifica di precisione. Una macchina di misura calcola i risultati del processo di rettifica utilizzando un algoritmo. Rileva il potenziale di miglioramento e fornisce un feedback alla macchina per effettuare una registrazione che migliora ulteriormente la qualità del prodotto.
“Per molti anni abbiamo avuto la possibilità di misurare e reagire utilizzando algoritmi statici”, dice. “Oggi l’HCI ci permette di fornire continuamente i dati del processo di produzione in tempo reale al cloud e di addestrare in modo continuo e dinamico i nostri algoritmi di apprendimento automatico per regolazioni più precise”.
La digitalizzazione è uno dei fattori abilitanti nel percorso verso la world class manufacturing. Tuttavia, dice Homes, la trasformazione lean delle fabbriche SKF è il fondamento su cui costruire la trasformazione digitale. Il suo team sta guidando e supportando le fabbriche fino a quando non saranno certificate e soddisfatte le giuste condizioni.
“Dobbiamo prima migliorare e standardizzare i nostri processi”, spiega Homes. “Poi si parte con la digitalizzazione. Altrimenti c’è il rischio di digitalizzare un processo che contiene ancora sprechi, il che rende le soluzioni più complesse e meno efficaci.
La trasformazione è un processo continuo
“Ajay e il suo team di Göteborg hanno seguito questo metodo strutturato, ottenendo la certificazione di tutte le parti della fabbrica nel sistema di produzione SKF e lavorando a stretto contatto con tutti i dipendenti della produzione per far sì che la trasformazione avesse luogo. Tutto ciò ha prodotto gli ottimi risultati ottenuti a Göteborg negli ultimi anni”.
Per Naik non c’è tempo per riposarsi ed è già alla ricerca di nuovi miglioramenti con cui decorare le pareti in ottica Kaizen. Preparare la fabbrica al cambiamento, in particolare da una prospettiva digitale, è un processo continuo che deve evolvere con il progredire della tecnologia.
“Vogliamo costruire un’organizzazione realmente incentrata sul cliente, per questo dobbiamo seguire la nostra tabella di marcia, non solo per ridurre i costi ma anche per creare valore”, sottolinea Naik. “Questo comporta una maggiore attenzione alla gestione degli approvvigionamenti e un ulteriore sviluppo delle nostre future competenze verso la digitalizzazione. Comporta altresì più change leader e un maggiore investimento nella cultura di responsabilità del nostro operato. Questo è il nostro cammino”.