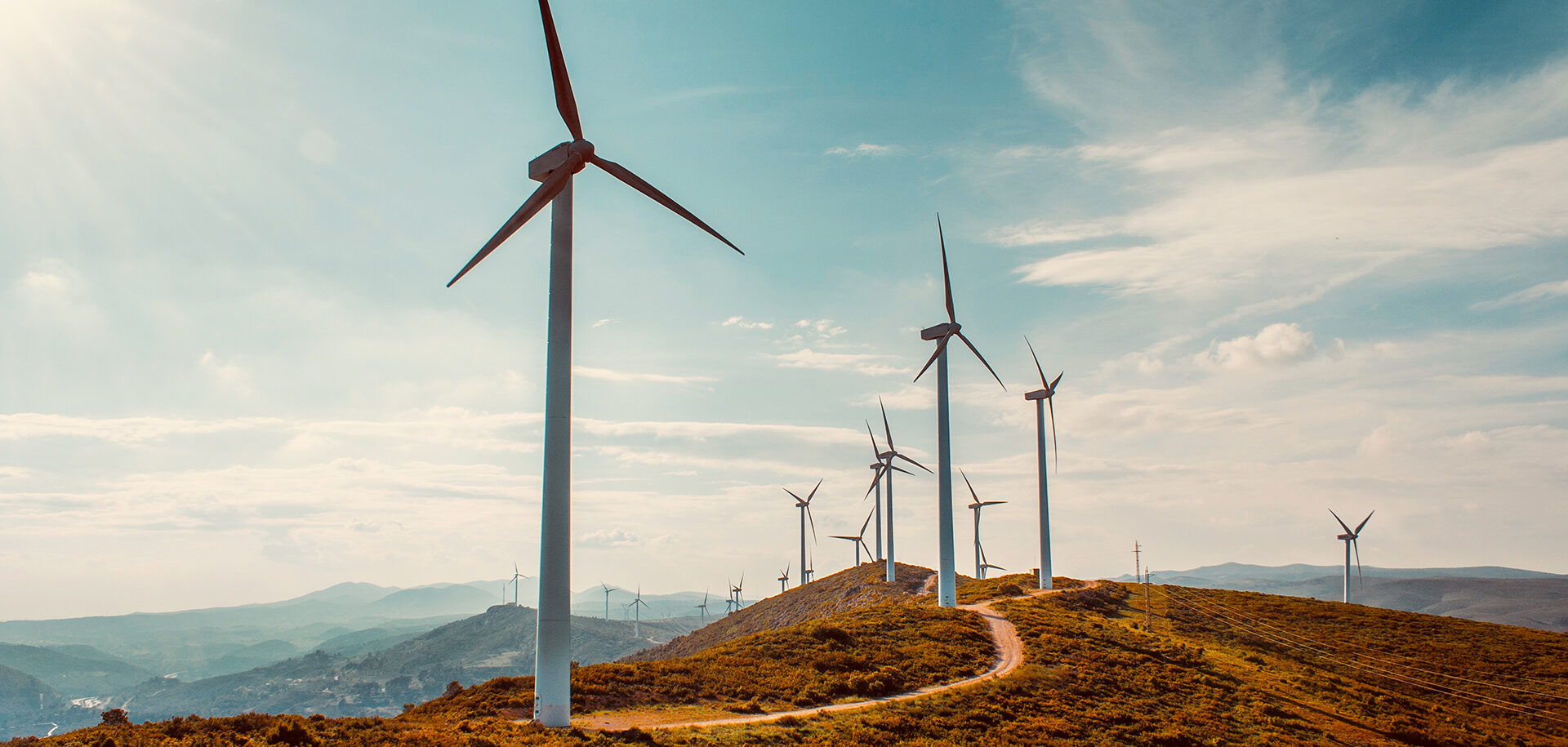
Mayor precisión en el monitoreo de las turbinas eólicas
Monitorear el funcionamiento de las turbinas eólicas es un gran reto. Cada turbina está sometida a cambios constantes debidos a los caprichos del tiempo. Por ello, circunstancias que pueden causar grandes tensiones en algunos componentes pueden identificarse erróneamente como defectos. SKF ha dado un considerable paso adelante con el desarrollo de una nueva herramienta de diagnóstico para reducir la posibilidad de falsas alarmas en el monitoreo del tren de transmisión de las turbinas.
Protean es una nueva herramienta de diagnóstico desarrollada para reducir la incidencia de falsas alarmas, y que distingue entre tensiones temporales y condiciones defectuosas. La función de diagnóstico de Protean se ha diseñado para funcionar con el software @ptitude Observer CMS, de SKF, para el monitoreo del tren de transmisión de las turbinas eólicas, usado ampliamente en el sector eólico. Ayuda a los técnicos de operación, mantenimiento y CMS a concentrarse en los aspectos de rendimiento potencial real, y así mitiga el riesgo de falsas alarmas. En grandes parques eólicos, puede proporcionar unos ahorros de tiempo considerables y hacer más eficaces y efectivos los sistemas de CMS.
Cómo funciona Protean
Fundamentalmente, Protean identifica las condiciones operativas del equipo y “aprende” su comportamiento normal respecto de diferentes indicadores de condición. Tras un período de aprendizaje de aproximadamente una semana, Protean establece automáticamente niveles umbral de los diferentes indicadores de condición, definidos por el operario. Los indicadores de condición se han diseñado para detectar defectos de diferentes tipos, como defectos en rodamientos y engranajes, desequilibrios, etc. Luego, esos indicadores se configuran para cada componente del equipo, lo que significa que, como mínimo, se usa un indicador para cada rodamiento. Si se presenta una alarma, Protean recalcula el nivel umbral según la nueva situación que ha conducido a una alarma. Por ello, solo se generarán nuevas alarmas si la condición empeora. Además, un valor de indicador de condición que viole el nivel umbral no accionará una alarma. Para activar la alarma, es preciso que “M de los N” últimos valores del indicador de condición superen el valor umbral (M y N se seleccionan siguiendo las mejores prácticas). Cuando se ha efectuado el mantenimiento, Protean detecta un descenso en el nivel del indicador de condición y recalcula automáticamente el nivel umbral para reflejar la nueva situación.
Para formarse una idea, crear una configuración de CMS de parque eólico para 20 turbinas significaría ajustar unos 1000 indicadores. Realizar esto manualmente es en realidad imposible. Por ello, un enfoque que aplique reglas de diagnóstico del software SKF @ptitude y se vincule con Protean y su enfoque de Inteligencia Artificial permite una configuración rápida y simple del CMS.
El software CMS de SKF permite automatizar el diagnóstico al permitir al usuario crear un modelo matemático del tren de transmisión de las turbinas eólicas con la biblioteca “arrastrar y soltar” de componentes, por ejemplo, rotor eléctrico, rodamientos, engranajes, etapa planetaria, impulsores, etc. (fig. 1). Las reglas de diagnóstico, o indicadores de condición, se han calculado tradicionalmente como un valor absoluto usando frecuencias que son significativas para que se detecte el defecto. Una regla de diagnóstico combina las amplitudes a frecuencias definidas en función de datos cinemáticos. Asimismo, en la medición, el valor del indicador de condición también puede calcularse como porcentaje del ruido de fondo. Entonces puede evitarse el ruido que anteriormente conducía a una detección positiva pero falsa. Los indicadores de condición se diseñan para reaccionar ante defectos definidos en un componente del equipo, como desalineación de eje, defecto de rodamiento o de engranaje, o desequilibrio de rotor.
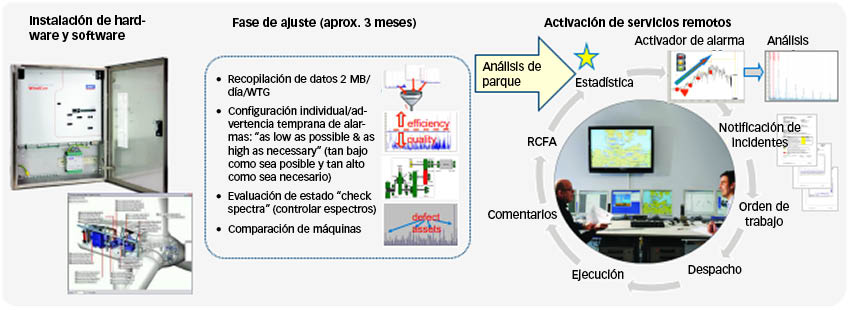
La diferencia con Protean
Para un posible defecto de holgura en un eje mecánico, se aplican en gran medida las reglas de diagnóstico, lo que permite la extracción de indicadores de condición predefinidos (fig. 3). La biblioteca facilita la configuración habitual y basta con que el usuario ajuste la alarma y el nivel de peligro, o seleccione “auto” para que el software calibre el nivel de alarma según el comportamiento de la maquinaria durante el primer funcionamiento. Sin Protean (fig. 4), el sistema reacciona al incremento en holgura mecánica pero se precisará la intervención manual para ajustar los niveles de alarma.
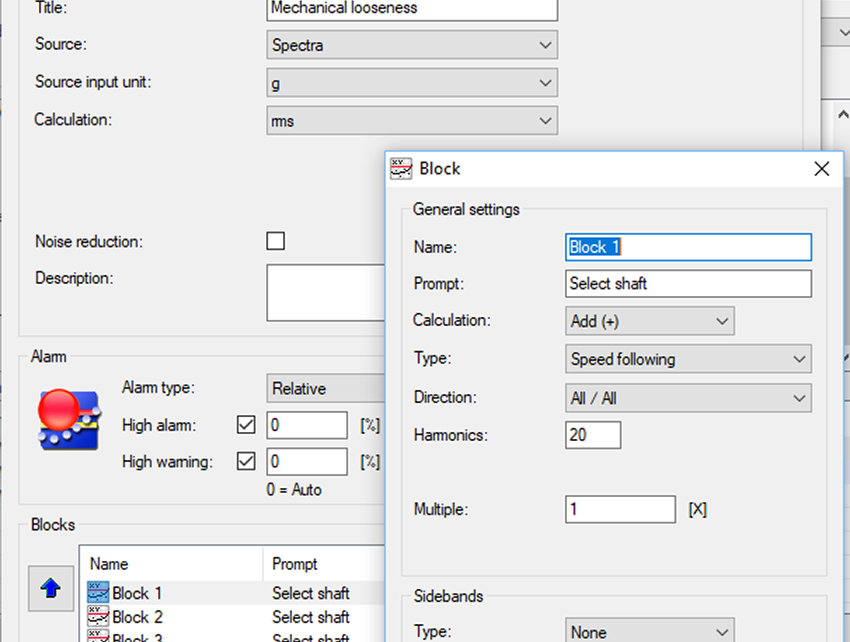

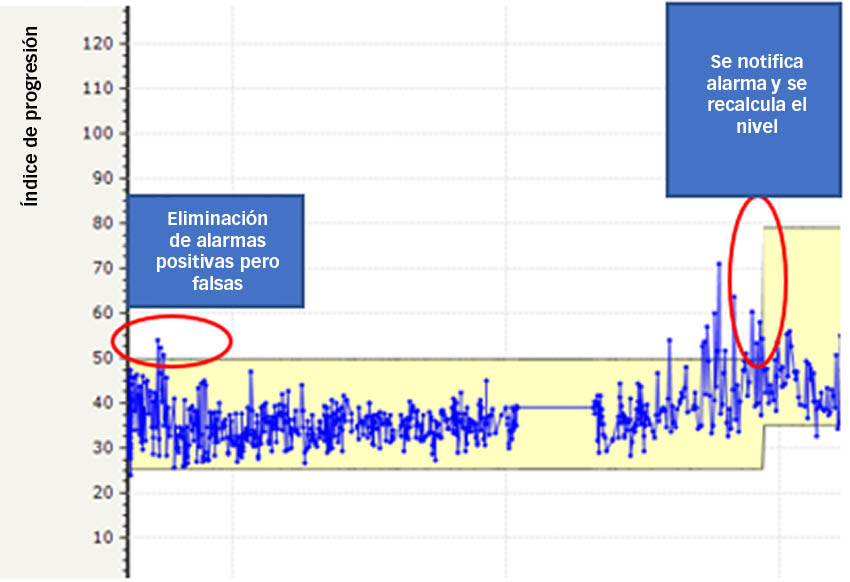
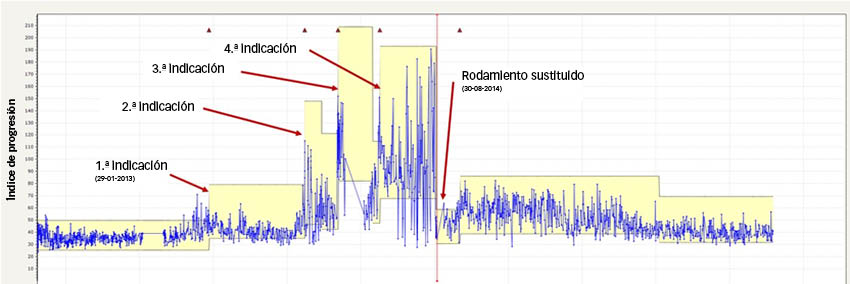

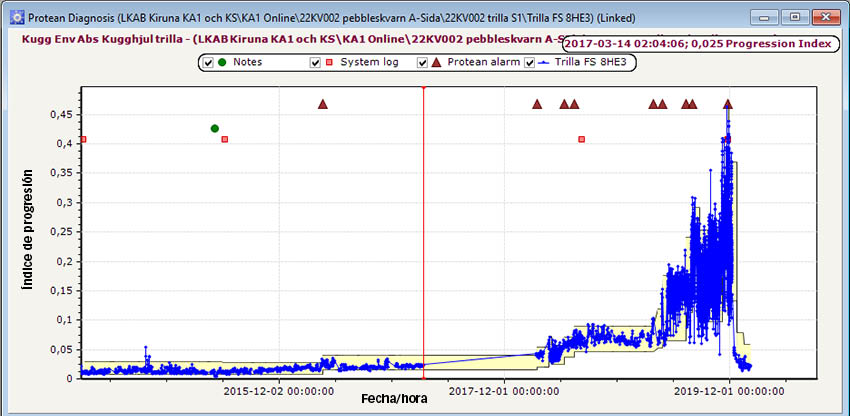
Protean es una solución de autodiagnóstico muy confiable que ofrece una reducción significativa de las falsas alarmas sin un mayor riesgo de pasar por alto defectos. Libera a los técnicos de CMS de pesadas tareas repetitivas y les permite concentrarse en casos más difíciles. Respalda y refuerza los beneficios de un CMS satisfactorio, que detecta fallas y otras condiciones no deseadas de manera temprana. Además permite planificar y realizar tareas correctivas oportunamente y con la calidad correcta, lo que evita daños posteriores en la maquinaria.
SKF considera a Protean como un importante paso adelante para mejorar la detectabilidad, precisión y eficacia del monitoreo de condición, no solo en turbinas eólicas, sino en todo tipo de maquinaria giratoria. El continuo desarrollo y las nuevas herramientas son fundamentales para convertir al CMS en una tecnología más inteligente que ayude a los clientes a gestionar sus procesos de operación y mantenimiento de una forma más efectiva.