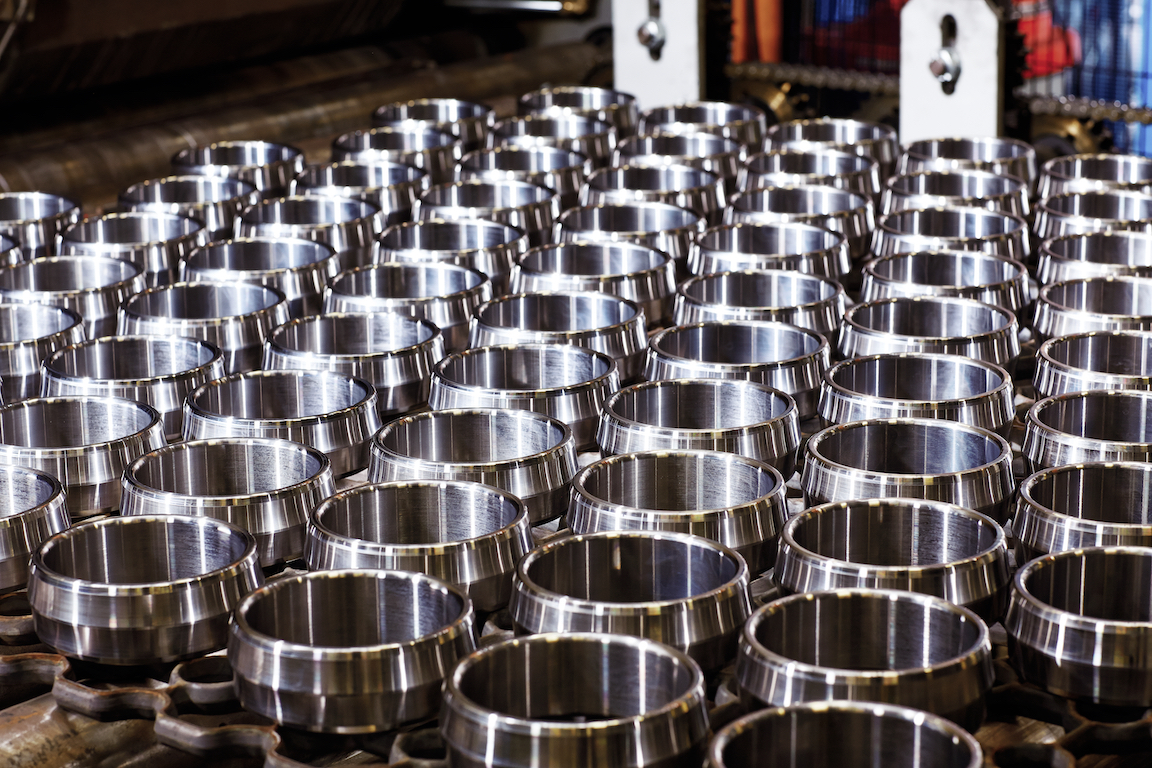
OBIETTIVO LIMPIDEZZA
Vino, acque reflue e olio sono tra i numerosi prodotti la cui lavorazione implica la separazione solido-liquido. Le centrifughe decanter dell’Alfa Laval assolvono efficacemente il compito, producendo forze fino a 3.500 volte superiori a quella di gravità.
Fatti
Alfa Laval
Scambio termico, separazione e movimentazione dei fluidi sono le tre tecnologie di specializzazione della Alfa Laval. Fondata nel 1883, l’azienda dà attualmente lavoro a 16.400 dipendenti e registra vendite nette per 3,4 miliardi di euro. La produzione di decanter, che risale agli anni cinquanta, ha garantito alla Alfa Laval una posizione di preminenza in questo settore, con una quota nel mercato globale pari al 20 percento. Stati Uniti e Canada sono i suoi principali mercati.
Link correlati
Contatto vendite
Frank Fiddelaers Peder Dalgaard
Molti processi industriali richiedono la separazione di particelle solide da un liquido nel quale si trovano in sospensione. Questo avviene, per esempio, nel trattamento delle acque reflue o nella produzione di olio e vino. Il prodotto finito è di norma costituito dal liquido chiarificato, ma può anche essere il residuo solido ottenuto dopo la separazione, come nel caso della soia.
Se il fattore tempo non è decisivo, per separare i vari elementi si può ricorrere semplicemente alla forza di gravità. Il processo consiste nel lasciare depositare sul fondo di un apposito recipiente le particelle solide contenute in sospensione. Tuttavia si può accelerare il processo facendo ruotare la sospensione all’interno del tamburo di cui sono dotate per esempio le centrifughe decanter prodotte dalla Alfa Laval.
“Il tamburo ruota a una velocità periferica di 100-110 metri al secondo”, informa Bent Madsen, Process and Technology Manager di Alfa Laval presso il centro di produzione decanter di Copenhagen, Danimarca. “Produciamo una forza centrifuga interna elevata, da 3.000 a 3.500 volte quella di gravità”.
Tra le ultime nate in casa Alfa Laval c’è la centrifuga decanter Lynx 1000, una delle più grandi, con una portata di 540 metri cubi all’ora. Mentre visitiamo la linea di montaggio, osserviamo l’unità che svetta nella sezione di collaudo prima della consegna. La Lynx 1000 è lunga quasi nove metri, alta due, e pesa 18,5 tonnellate. Al suo azionamento provvedono due motori elettrici, uno dei quali ha una potenza di 330 kilowatt.
Più indietro, lungo la linea di montaggio, si trovano i componenti di altri modelli in vari stadi di completamento. Tutto è organizzato alla perfezione. Ogni stadio viene contrassegnato mediante strisce gialle disegnate sul pavimento.
In un reparto troviamo un tamburo sedimentatore. Realizzato in acciaio duplex a elevata resistenza, si presenta come una grossa struttura tubolare cilindrico-conica. A un’estremità è munito di una serie di bocche di scarico; l’altra estremità, di sezione conica, è dotata di un’apertura. Questi tipi di tamburo hanno un diametro interno che va da 0,2 a 1 metro, con una lunghezza fino a quattro volte superiore. È il tipo di applicazione a determinarne la dimensione.
Il tamburo è internamente corredato di una coclea. Entrambi ruotano a velocità molto elevate, in alcuni casi fino a 5.000 giri/min, ma la coclea ruota un po’ più lentamente. La differenza di rotazione è compresa tra 1 e 50 giri/min, in funzione del mezzo che deve essere separato.
Con la rotazione combinata tamburo-coclea, la sospensione viene alimentata attraverso un canale centrale. Le forze centrifughe la spingono verso l’interno del tamburo, separando così i solidi dal liquido. Man mano che la fase solida cresce, la coclea provvede al suo trasporto verso la camera conica da dove viene espulsa. Il liquido chiarificato, invece, viene fatto uscire all’estremità opposta attraverso le bocche di scarico.
Questi apparecchi sono a funzionamento continuo e consentono di trattare maggiori volumi in tempi più brevi rispetto ai normali processi di sedimentazione. I risultati dipendono da una combinazione di fattori, come la velocità di rotazione, la rotazione differenziale e la geometria del sedimentatore.
Grasso per alte velocità
Si chiama Lynx 1000 l’ultima nata in casa Alfa Laval ed è una centrifuga decanter di ultima generazione, che gestisce portate di 540 metri cubi all’ora. Progettata in particolare per i solidi abrasivi nell’industria del petrolio e del gas, questa macchina offre una durata di esercizio maggiore rispetto ai modelli precedenti. Per impedire l’ingresso di sostanze contaminanti all’interno dei cuscinetti principali, i progettisti della Alfa Laval intendevano ricorrere alla lubrificazione con grasso. Scelta che si rivelò essere una sfida.
“Stando al Catalogo Generale SKF, la velocità e i carichi ai quali erano sottoposti i cuscinetti in quell’applicazione non permettevano la lubrificazione a grasso”, dice Lauge Svarrer, specialista dei sistemi d’ingranaggi.
Questo portò a una serie di esperimenti condotti in cinque anni, durante i quali si arrivò, in stretta collaborazione con la SKF, all’ottimizzazione del sistema di cuscinetti. Alfa Laval costruì uno speciale banco prova con il quale valutare parametri operativi diversi, oltre che i cuscinetti e i grassi.
“Dovevamo trovare un modo per lubrificare questi cuscinetti ad alta velocità di rotazione in condizioni stabili di temperatura”, commenta l’ingegnere dello sviluppo Kristoffer Sjögreen, che ha monitorato i test.
Il Dr. Jan Cederkvist, responsabile validazione dei prodotti, dice: “Quando si introduce il grasso, è normale che si verifichi un lieve picco di temperatura. Tuttavia, picchi eccessivi possono danneggiare i cuscinetti. L’esecuzione deve sempre garantire affidabilità e robustezza”.
La soluzione consisteva nel trovare il giusto equilibrio.
Peder Dalgaard, ingegnere dell’applicazione SKF, sostiene: “È possibile farlo, se si considerano tutti i fattori: tolleranze, corretto tipo di grasso e la sua quantità, configurazione del sistema di cuscinetti, precisione di rotazione dei cuscinetti. In questo caso abbiamo adottato il grasso SKF LGHP 2 e un sistema formato da un cuscinetto radiale a sfere e da un cuscinetto a rulli cilindrici con alloggiamenti separati”.
Il risultato ha prodotto un elevato livello di ottimizzazione del sistema di cuscinetti.
Frank Fiddelaers, ingegnere senior dello sviluppo, afferma: “Con questo progetto, i cuscinetti a rulli e quelli radiali a sfere lubrificati con grasso hanno raggiunto un’alta stabilità prestazionale in presenza di carichi gravosi, una varietà di temperature e con fattori di velocità superiori a 500.000 n x dm”.