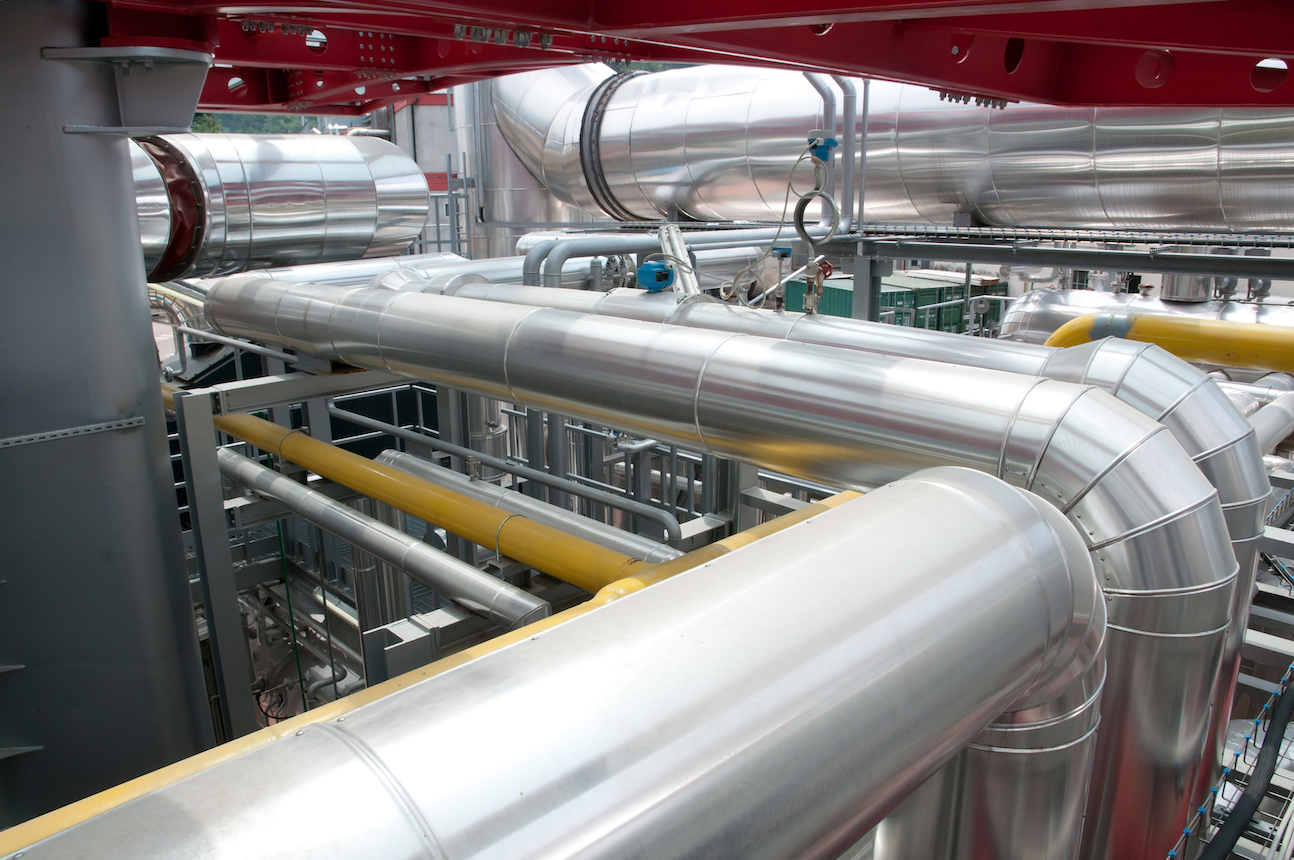
Sotto ferreo controllo
La tedesca ArcelorMittal Bremen GmbH, che fa capo al più grande gruppo siderurgico del mondo, produce ogni anno oltre tre milioni di tonnellate di acciaio. La SKF ha fornito un dispositivo per il condition monitoring che controlla il sistema centralizzato dell’aria compressa.
Fatti
ArcelorMittal
– Oltre a essere il maggiore produttore di acciaio del mondo, la ArcelorMittal è anche un’importante società mineraria, con una presenza in oltre 60 paesi.
– In Germania la produzione di acciaio grezzo ammonta a circa 7 milioni di tonnellate, il che la rende il principale produttore del paese. I suoi clienti operano nei settori automobilistico, delle costruzioni, dell’imballaggio e degli elettrodomestici.
– L’impresa ha quattro importanti stabilimenti in Germania, due per la produzione di lamiere piane integrate a Brema e Eisenhüttenstadt, e due dedicati ai prodotti lunghi in acciaio, rispettivamente ad Amburgo e Duisburg.
Link correlati
Contatto vendite
Jorerg Lange Stephan Sondermannkf
Con il quartier generale e lo stabilimento di produzione situati sulle sponde del fiume Weser, la ArcelorMittal Bremen occupa una superficie di sette chilometri quadrati alla periferia di Brema. Con i suoi circa 3.500 dipendenti, l’acciaieria è una delle principali imprese industriali della regione.
In questo stabilimento l’azienda produce dal 1957 lamiere di acciaio laminate a caldo e a freddo, con speciali trattamenti superficiali, destinate a numerosi settori industriali, compreso quello automobilistico.
Grazie a un elevato grado di automazione, la ArcelorMittal Bremen produce ogni anno 3,2 milioni di tonnellate di acciaio. Tutti gli impianti, da quello di produzione della ghisa a quello di lavorazione della lamiera, si trovano all’interno di questo stabilimento.
I macchinari impiegati sono sottoposti a condizioni estreme, sia quelli utilizzati nelle applicazioni ad alte temperature dell’area a caldo sia quelli delle unità periferiche, come le apparecchiature per la distribuzione.
Ralf Suhling, responsabile metrologia dell’ArcelorMittal Bremen, sostiene che per ottimizzare la produzione e ridurre i costi di manutenzione occorre garantire l’affidabilità degli impianti. Un obiettivo per il quale il condition monitoring svolge un ruolo chiave.
Fa riferimento, a titolo esemplificativo, al sistema centralizzato dell’aria compressa, che attraverso l’apposita rete, serve le varie unità di produzion. Il sistema è composto da quattro turbocompressori, ciascuno dei quali opera a una pressione di 0,65 Mpa.
“Di norma, in funzione ci sono sempre tre compressori. Se si riscontra un danneggiamento grave ad uno di questi, di solito si tratta di problemi correlati ai cuscinetti del motore che lo comanda”.
Nel motore esiste sempre uno spazio tra il rotore e lo statore e non dovrebbe esserci usura. Col tempo, tuttavia, a causa proprio dell’usura, nei cuscinetti aumenta il gioco interno e, di conseguenza, questo spazio si riduce.
Stephan Sondermann, responsabile vendite ai principali clienti del settore siderurgico della SKF Germania, conferma che un aumento del gioco nei cuscinetti può provocare il contatto tra il rotore e lo statore, con conseguenti gravi danneggiamenti. “Quando succede, occorre rimuovere immediatamente il motore danneggiato e farlo riparare, sebbene questo comporti costi elevati”.
Per evitare questi inconvenienti, per il sistema centralizzato dell’aria compressa, la ArcelorMittal Bremen ha da anni adottato l’SKF Multilog Online System IMx-S. Si tratta di un dispositivo di monitoraggio on line, che permette di identificare le variazioni delle condizioni di lavoro e programmare in modo più efficace gli interventi di manutenzione e sostituzione dei motori.
Il principio di funzionamento è semplice: i danneggiamenti dei cuscinetti producono un aumento dei livelli di vibrazione a frequenze definite, le quali possono essere rilevate dai sensori. “Nel complesso, il monitoraggio continuo offre un flusso costante di informazioni che ci informa sullo stato di efficienza del macchinario”, aggiunge Sondermann.
Grazie all’impiego di questo sistema, la ArcelorMittal Bremen ha ridotto notevolmente il numero di sostituzioni dei motori e i costi correlati.
Nel campo del condition monitoring, l’azienda tedesca è sempre stata innovativa. A metà degli anni novanta aveva infatti introdotto il monitoraggio sistematico degli impianti, secondo il quale il personale preposto doveva acquisire regolarmente i dati relativi alle unità del sistema centralizzato tramite strumenti di misura portatili. Questi dati venivano poi registrati e utilizzati come base per le analisi successive, oltre che come elementi di valutazione per l’eventuale sostituzione dei componenti esaminati.
“Era già un grande passo avanti rispetto al metodo tradizionale che prevedeva la sostituzione di un componente al primo rumore sospetto”, osserva Suhling. “Con la successiva introduzione del monitoraggio offline basato su ronde, la ArcelorMittal Bremen aveva potuto pianificare più efficacemente la sostituzione dei cuscinetti, così come quella dei motori e dei componenti dei compressori.
Per ottimizzare ulteriormente le attività di condition monitoring, la ArcelorMittal Bremen si è rivolta alla SKF.
È apparso subito evidente che occorreva prevedere un sistema online capace di monitorare continuamente le condizioni delle apparecchiature presenti nell’impianto.
L’ingegnere SKF Jörg Lange è il project manager che ha seguito il progetto fin dall’inizio, nel 2008. Come spiega, il vecchio metodo di rilevazione dei dati basati su ronde presentava un evidente svantaggio, poiché “i dati misurati fornivano solo un’istantanea”.
Suhling fa presente che i dati rilevati con il metodo basato su ronde riportavano ripetute variazioni. “Quando un valore risultava estremamente alto, provvedevamo immediatamente a sostituire il componente interessato, ma nutrivamo dei dubbi che fosse realmente necessario farlo”.
L’SKF Multilog On-line System IMx-S, che è stato installato e messo in funzione in sole due settimane, fornisce indicazioni sulle prestazioni e la disponibilità delle macchine. Il sistema tiene costantemente sotto controllo i sensori, i cablaggi e l’elettronica, generando messaggi in modo automatico.
Suhling sottolinea che da quando è stato adottato il dispositivo, i costi di riparazione si sono sensibilmente ridotti. Contrariamente alle acquisizioni di dati basati su ronde, il monitoraggio continuo online permette di distinguere le variazioni temporanee dai segnali di reale continuo deterioramento delle condizioni.
La precisione delle informazioni consente a Suhling e ai suoi colleghi di agire in modo più appropriato. Invece di sostituire i componenti al minimo sospetto, come avveniva in passato, la ArcelorMittal Bremen oggi sa con maggiore precisione quando l’intervento è davvero necessario. Per Lange i vantaggi sono “una più efficace programmazione delle riparazioni, una maggiore efficienza delle macchine e, naturalmente, una maggiore sicurezza per gli operatori, i quali hanno accesso permanente ai dati direttamente dalla loro scrivania”.
Dall’introduzione delle unità SKF IMx-S, cinque anni fa, la ArcelorMittal Bremen ha dovuto sostituire un solo motore.
SKF Multilog On-line System IMx-S
L’SKF Multilog Online System IMx-S è disponibile nelle versioni con 16 o 32 segnali analogici di input, ciascuno dei quali può essere configurato. I dati rilevati sulle macchine vengono trasferiti in modo automatico e preciso a un computer host che gestisce il software SKF @ptitude Observer attraverso sensori di vibrazione fissi. Questo permette di acquisire, memorizzare ed elaborare in modo rapido, affidabile ed efficace numerose informazioni di carattere complesso su macchine e impianti. Grazie al fatto che il sistema fornisce in automatico indicazioni utili a risolvere i problemi esistenti o incipienti, gli operatori possono identificare tempestivamente le anomalie e intraprendere le opportune azioni correttive.
@ptitude è un marchio registrato del Gruppo SKF